Effective lubrication is crucial for maximizing the lifespan of worm gear. Proper lubrication reduces friction, wear, and heat generation, ensuring smooth operation and prolonged service life. Here are key lubrication strategies for worm gear:
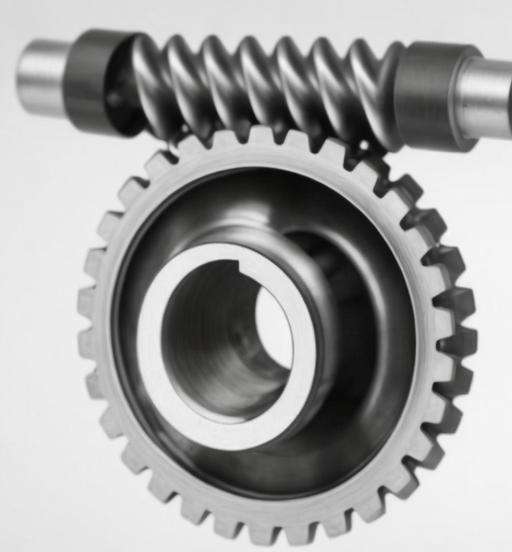
Types of Lubricants
- Oils:
- Mineral Oils: Traditional choice, suitable for general-purpose applications.
- Synthetic Oils: Provide better thermal stability, oxidation resistance, and longer service life. Common types include polyalphaolefins (PAO) and polyglycols (PAG).
- Greases:
- Calcium-Complex Grease: Offers good water resistance and mechanical stability.
- Lithium-Complex Grease: Provides excellent thermal stability and load-carrying capacity.
- Polyurea Grease: Suitable for high-temperature applications and provides good oxidation stability.
Lubrication Techniques
- Splash Lubrication:
- Involves partially submerging worm gear in an oil bath, where the rotating worm splashes oil onto the meshing gears.
- Suitable for moderate-speed applications.
- Ensures continuous lubrication and cooling.
- Forced Circulation Lubrication:
- Uses a pump to circulate oil continuously over worm gear.
- Ideal for high-speed or high-load applications where splash lubrication is insufficient.
- Provides effective cooling and filtration of contaminants.
- Grease Lubrication:
- Applied to worm gear with low to moderate speeds and where oil lubrication is impractical.
- Requires periodic replenishment and monitoring to ensure adequate coverage.
- Mist Lubrication:
- Sprays a fine mist of oil onto worm gear.
- Used in high-speed applications where precise lubrication is needed.
- Ensures minimal lubricant usage and effective cooling.
Best Practices for Lubrication
- Proper Lubricant Selection:
- Choose the right lubricant based on operating conditions such as load, speed, temperature, and environment.
- Refer to manufacturer recommendations and compatibility with worm gear materials.
- Regular Lubricant Maintenance:
- Monitor and maintain lubricant levels to ensure consistent lubrication.
- Regularly check for contamination, degradation, and viscosity changes.
- Optimal Lubricant Viscosity:
- Select lubricants with appropriate viscosity to balance film strength and flowability.
- Higher viscosity oils are better for heavy loads, while lower viscosity oils suit high-speed applications.
- Temperature Control:
- Ensure the operating temperature is within the lubricant’s optimal range.
- Implement cooling systems or use high-temperature lubricants if necessary.
- Contamination Control:
- Keep lubricants clean by using filtration systems to remove particles and moisture.
- Regularly inspect and replace filters and seals to prevent contamination ingress.
- Lubricant Application:
- Apply lubricants evenly and adequately cover all contact surfaces.
- Use automatic lubrication systems for consistent and precise application.
Advanced Lubrication Strategies
- Condition Monitoring:
- Use sensors and monitoring systems to track lubricant condition in real-time.
- Analyze data to predict maintenance needs and prevent failures.
- Synthetic Lubricants:
- Utilize synthetic lubricants for better performance in extreme conditions and longer intervals between changes.
- Special Additives:
- Use lubricants with anti-wear, extreme pressure (EP), and anti-oxidation additives to enhance performance.
- Consider additives that improve load-carrying capacity and reduce friction.
Specific Applications
- Heavy-Duty Applications:
- Use high-viscosity synthetic oils with EP additives for enhanced protection under heavy loads.
- Implement forced circulation systems to maintain optimal temperature and lubrication.
- High-Speed Applications:
- Select low-viscosity oils to reduce friction and heat generation.
- Use mist or spray lubrication to ensure precise and effective lubrication.
- Environmentally Sensitive Areas:
- Opt for biodegradable or environmentally friendly lubricants.
- Implement stringent contamination control measures.
By following these lubrication strategies, worm gear systems can achieve enhanced performance, reduced wear, and extended service life, ensuring reliable operation in various demanding applications.