I. Introduction
Cylindrical gears are widely used in power transmission mechanisms, and the meshing characteristics of gear pairs directly affect the transmission performance of mechanical equipment. The geometry of gear teeth has a significant impact on the performance of gear pairs. Currently, common types of cylindrical gears include spur gears, helical gears, herringbone gears, and circular-arc-tooth cylindrical gears.
Existing hobbing and shaping methods, despite continuous improvements, cannot achieve continuous gear processing across the full tooth width, limiting the processing efficiency of gears. The emergence of high-speed dry hobbing has improved the production efficiency and tooth surface integrity to some extent, but its process parameters need further optimization and the tool is prone to wear. Additionally, due to processing, installation errors, and elastic deformation, meshing transmission of gear pairs is prone to partial load, affecting the service life of gears.
In recent years, many scholars have conducted extensive research on circular-arc-tooth cylindrical gears and their processing methods. However, these processing methods often require single-tooth cutting, resulting in low processing efficiency and limiting the application of circular-arc-tooth cylindrical gears.
To enhance the processing efficiency and bearing capacity of cylindrical gears, this paper proposes a new type of plane spiral cylindrical gear and a rapid forming method for this gear.
II. Machining Principle of Plane Spiral Cylindrical Gear
- Formation Principle of Plane Spiral Tooth Line
- Traditional machining methods for cylindrical gears, such as hobbing and shaping, cannot achieve continuous processing across the full tooth width. To improve the cutting efficiency, a new method is proposed. By installing a single tool on a large cutter head and rotating the cutter head at a high speed, if the rack is stationary in the radial direction of the cutter head and continuously feeds in the axial direction, the machined tooth groove is arc-shaped. This method requires tool retraction and radial indexing of the rack for each tooth groove, severely limiting the processing efficiency.
- To improve this, the processing method is modified. While the cutter head rotates, the rack moves along the radial direction of the cutter head at a certain speed. The spiral tooth line is formed by the trajectory of the tool on the rack. When the speed relationship satisfies that the cutter head rotates one circle and the rack moves one tooth pitch, continuous full-tooth-width processing can be achieved, effectively improving the gear processing efficiency.
- There are several differences between the processing of cylindrical gear blanks and rack processing. In cylindrical gear blank processing, cutting depth processing and generating processing are involved. During cutting depth processing, the speed of the rack is converted into the angular velocity of the cylindrical workpiece, and the workpiece needs to feed in the axial direction of the cutter head simultaneously. During generating processing, an additional rotation and radial linear motion are applied to the workpiece to form an involute tooth profile.
- Gear Machining Cutter Head
- To ensure processing efficiency and accuracy, multiple tools are uniformly arranged on the large cutter head according to a plane spiral line, with the pitch of the spiral line being the same as the tooth pitch of the gear.
- The installation height of the tools is determined, with the main cutting tool having the highest installation radius, and the other tools serving as auxiliary cutting tools to reduce the cutting load and force of the main cutting tool.
- The polar coordinate equation of the tool arrangement spiral line is given, and the cross-sectional diagram of the main cutting tool shows the roles of the outer and inner cutting edges in generating the concave and convex surfaces of the gear tooth.
- Generating Motion Principle
- During processing, the cutter head rotates at an angular velocity ωD around the YD axis as the main motion, while the gear blank rotates at an angular velocity ωC around the ZC axis.
- To ensure accurate processing of the tooth grooves, the angular velocity of the gear blank ωC and the angular velocity of the cutter head ωD must satisfy a specific relationship.
- For the cutting depth processing, the gear blank needs to feed continuously in the YC direction while rotating. To generate the involute tooth profile, the gear blank performs a generating motion relative to the machining tool, rotating at an angular velocity (ωC – ωS) around the ZC axis and moving in the positive XC direction. The processing principle for the left tooth surface is similar, but with different rotation and movement directions.
III. Processing and Simulation of Plane Spiral Cylindrical Gear
- Machining Cutter Head Model
- Parameters of the gear and machining tool are provided, and based on these parameters, the tooth blank and machining cutter head models are established using SOLIDWORKS software.
- The cutter head and tool are imported into the VERICUT tool management library, and the model of the gear machining tool is shown.
- Processing Simulation
- After setting the milling processing parameters appropriately, the gear is simulated for processing in the VERICUT software.
- The simulation process shows that the cutter head rapidly rotates to machine the plane spiral cylindrical gear, achieving continuous full-tooth-width cutting. The machined tooth surface of the plane spiral cylindrical gear is divided into concave and convex surfaces, and the radius of the concave tooth line is slightly larger than that of the convex tooth line, forming slightly drum-shaped teeth.
- Actual Processing
- Based on the processing method and simulation results, a special machining machine tool for plane spiral cylindrical gears is developed.
- The machining cutter head is equipped with through slots for installing the tools, and the tools are fixed and positioned in the radial direction. The machining machine tool can achieve continuous full-tooth-width cutting of the gears, and its processing efficiency is significantly higher than that of the existing hobbing process for cylindrical gears.
IV. Main Geometric Parameters and Meshing Analysis of Plane Spiral Cylindrical Gear
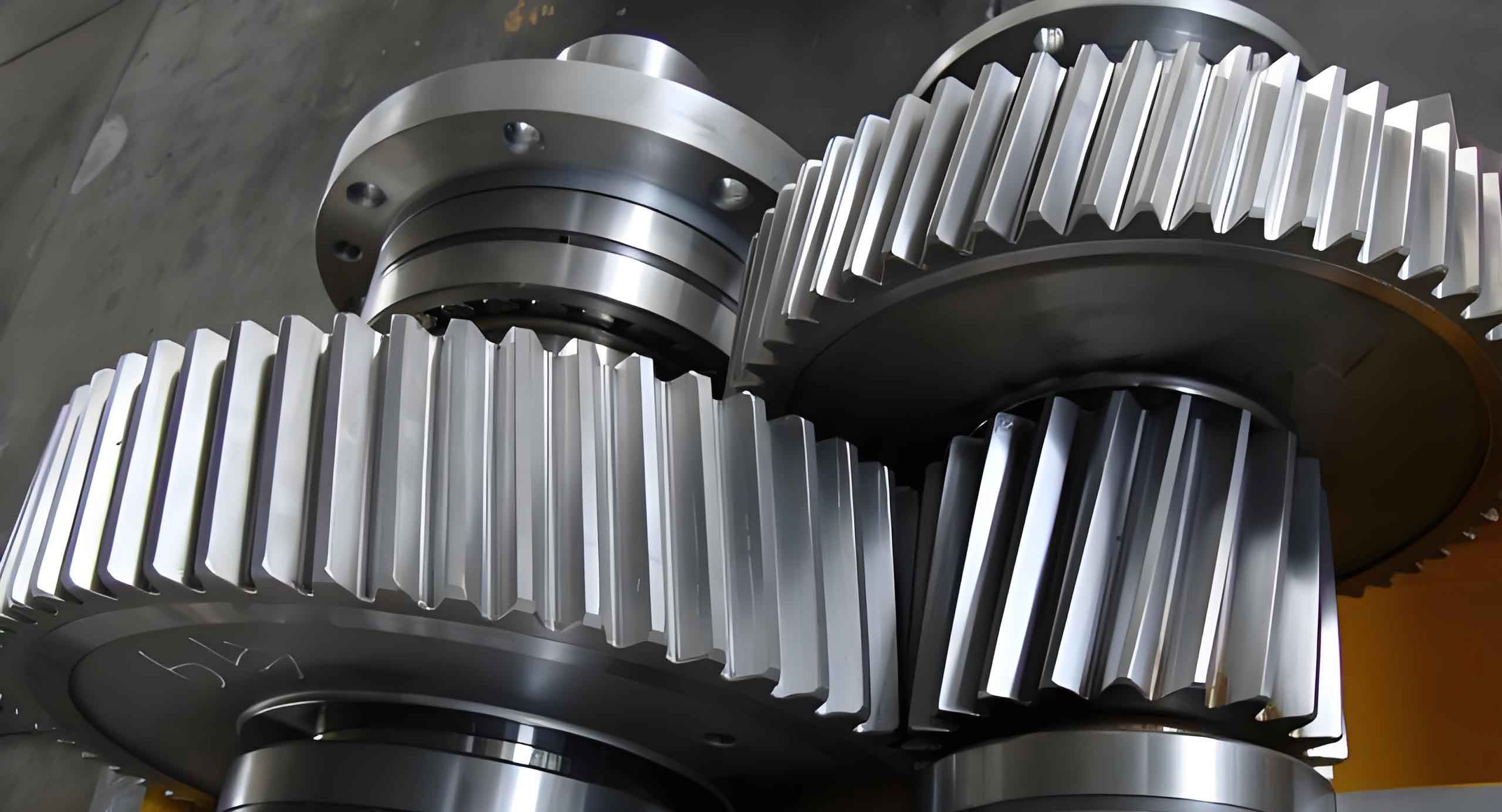
- Main Geometric Parameters and Characteristics of Plane Spiral Cylindrical Gear
- The tooth surface of the plane spiral cylindrical gear is divided into concave and convex surfaces, and the curvature radius of the concave tooth line is slightly larger than that of the convex tooth line. The difference between the tooth line radii at the same spiral line expansion angle is given by a specific equation.
- The main parameters of the plane spiral cylindrical gear include the module, number of teeth, pressure angle, tooth width, and the curvature radius at the centerline of the tooth width.
- By analyzing the meshing relationship between the gear and the rack, the characteristics of the plane spiral cylindrical gear are clarified. The tooth thickness at the centerline of the tooth width is slightly larger than that at the end faces, which can reduce stress concentration at the tooth roots and minimize meshing partial load caused by processing and installation errors.
- The tooth profile at the middle section of the plane spiral cylindrical gear is an involute, while the tooth profiles at other sections are similar to but slightly deviated from the standard involute. Meshing requires a pair of left-handed and right-handed plane spiral cylindrical gears with the same module, pressure angle, and curvature radius at the centerline of the tooth width.
- Meshing Characteristics Analysis of Plane Spiral Cylindrical Gear
- To verify the contact line of the gear transmission, two plane spiral cylindrical gear models with the same parameters but opposite rotation directions are used for meshing characteristics analysis.
- The gear pair is precisely assembled in the SOLIDWORKS software, and interference analysis is performed on the tooth surfaces of the gear pair.
- The analysis results show that the theoretical contact area is mainly distributed in the middle 80% – 90% region of the contact tooth surface, reducing the bending stress at the tooth roots and improving the bearing capacity of the gear pair.
V. Conclusion
- The method of full-tooth-width continuous cutting of cylindrical gears using a large cutter head is proposed, and its feasibility is verified through VERICUT software simulation.
- The geometric characteristics of the plane spiral cylindrical gear are summarized, including the relationship between the arc-tooth radii of the concave and convex tooth surfaces and the tooth line being a plane spiral line.
- The theoretical tooth surface contact characteristics of the plane spiral cylindrical gear pair are that the contact area is mainly distributed in the middle of the contact tooth surface, reducing the bending stress at the tooth roots and improving the bearing capacity of the gear pair.
- Future research directions include calculating the tooth surface equation of the gear, analyzing the distribution of tooth surface contact stress and tooth root bending stress, and building a gear transmission experimental device to study the transmission characteristics of the plane spiral cylindrical gear.
In this paper, the “Spiral Bevel Gear” is not directly related to the content of the plane spiral cylindrical gear. The focus is on the new type of plane spiral cylindrical gear and its processing and meshing characteristics. Further research and development in this area can lead to improvements in gear processing efficiency and performance.