From the point of view of meshing mechanism and gear characteristics, due to the change of pressure angle of gear teeth, the machining cutter parameters of asymmetric gear with double pressure angle change correspondingly, so it is necessary to analyze and calculate the cutter parameters.
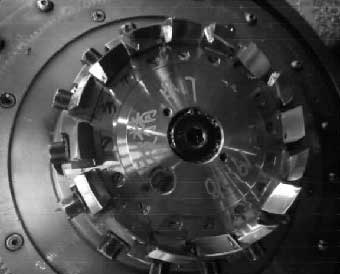
Two kinds of cutter heads, double cutter head and single cutter head, are used in the machining of unsymmetrical spiral bevel gears. On the double-sided cutter head, there are two kinds of blades, the external cutting blade and the internal cutting blade, arranged alternately. The external edge of the external cutting blade is the working surface, cutting the concave side of the asymmetric gear; the internal edge of the internal cutting blade is the working surface, cutting the convex side of the asymmetric gear. The blades installed on the single-sided milling cutter head are all external cutting blades. The single-sided external cutting cutter head is used to cut the concave side of the asymmetric tooth slot, and the single-sided internal cutting cutter head is used to cut the convex side of the asymmetric tooth slot. The finish milling cutter head used to process the passive wheel of the asymmetric spiral bevel gear is shown in Figure 8. In order to improve the production efficiency, the single-sided cutter head is only used to precisely cut asymmetric gears.
The machining of the unsymmetrical spiral bevel gear adopts the double-sided cutting method. When cutting the passive wheel of the unsymmetrical spiral bevel gear, the two sides of the tooth slot are precisely cut by a cutter head at the same time; when cutting the two sides of the tooth side of the unsymmetrical driving wheel, the inner and outer fine cutting cutter heads are used for machining, and different machine tools are used for adjustment, respectively finishing the two sides of the tooth.
The fixed installation method is adopted in the installation, that is, each process is carried out on a fixed machine tool, and a total of 5 machine tools and 5 cutter heads are required. The passive gear of asymmetric spiral bevel gear needs two processes of rough cutting and fine cutting, and the driving gear needs three processes of rough cutting, outer fine cutting and inner fine cutting.
The fixed installation double-sided method is adopted in the processing, which can control the contact area of the convex and concave sides of the tooth profile of the unsymmetrical spiral bevel gear independently, and the processing site is as shown in the figure.
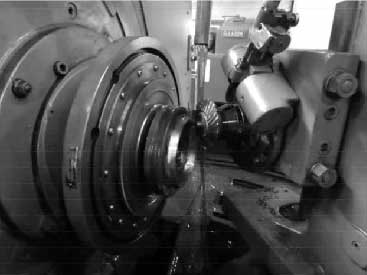
The processed double pressure angle asymmetric spiral bevel gear and the original reducer symmetric gear driven wheel are as shown in the figure. The left is the asymmetric spiral bevel gear driven wheel, with a mass of 1.15 kg, and the right is the original symmetric gear driven wheel, with a mass of 1.7 kg, with a reduction of about 37%.
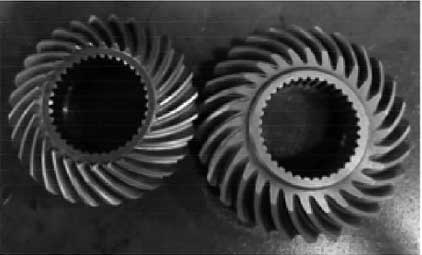
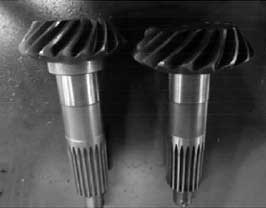
The processed double pressure angle asymmetric spiral bevel gear and the original symmetric gear driving wheel are shown in the figure. The left is the asymmetric spiral bevel gear driving wheel, with a mass of 1.8kg, and the right is the original symmetric gear driving wheel, with a mass of 2.0kg, with a reduction of about 10%. Because the driving wheel has a gear shaft, the lightweight value is small. At the same time, when the volume of unsymmetrical spiral bevel gear becomes smaller, the volume of other parts such as bearing seat, case and so on also decreases, so the total lightweight value is very considerable.