Figure 1 shows the influence curve of helical gear tooth surface friction coefficient on dominant frequency resonance. It can be seen from the figure that with the increase of friction coefficient, the resonance amplitude decreases obviously. When the friction coefficient is 0.2, the vibration response amplitude decreases by nearly 8% compared with that when the friction coefficient is 0.1, and the resonance frequency increases slightly.
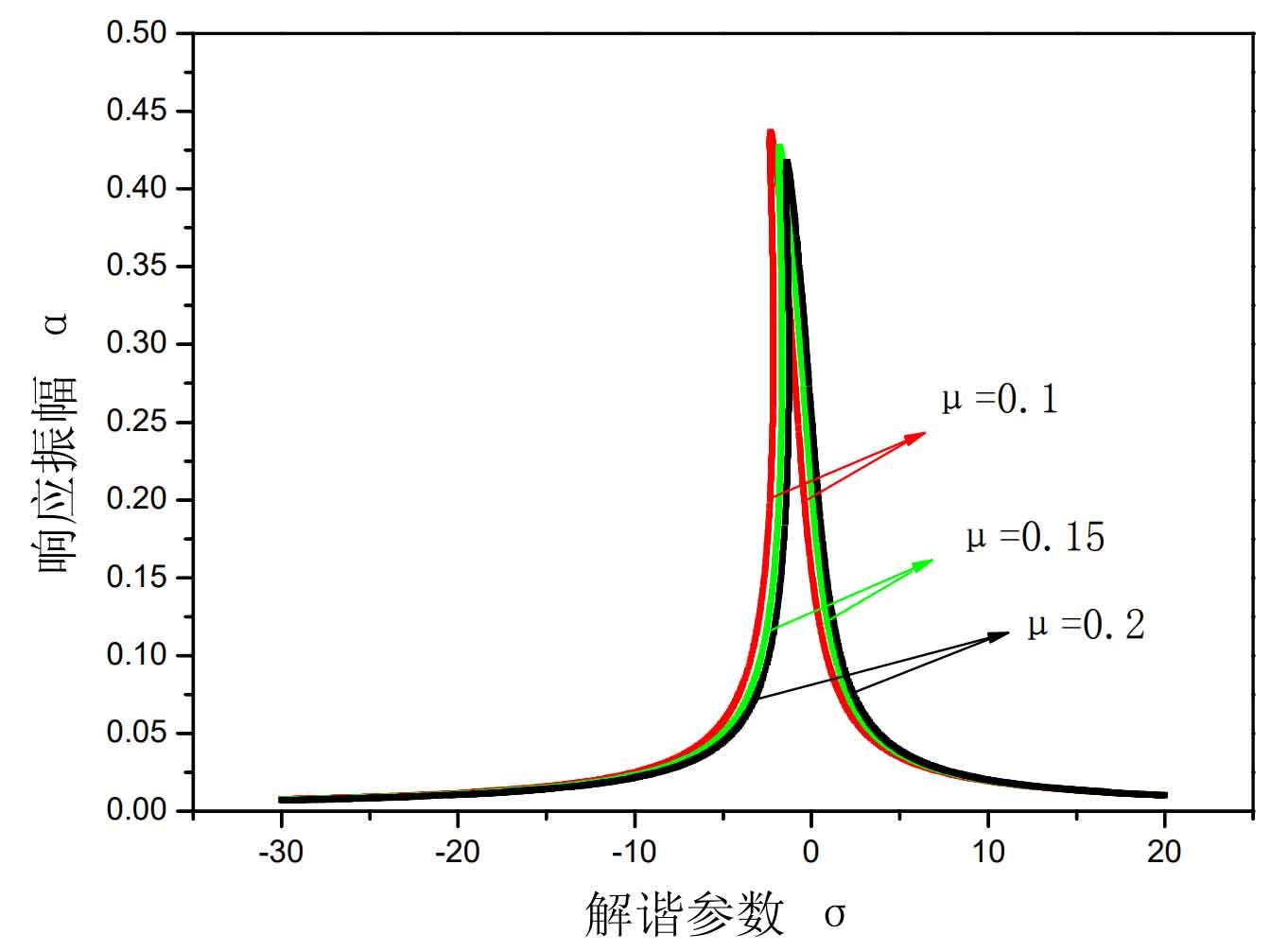
In order to further study the influence of helical gear tooth surface friction on resonance, and considering the large friction coefficient in boundary lubrication and spatial solid lubrication of heavy helical gear transmission, this paper selects the response law when the larger friction coefficient is 0.2 to compare with that when friction is not considered. Figure 2 shows the influence curve of static load on dominant frequency resonance. It can be seen from figure a) and figure b) that under the same parameters, the amplitude caused by static load when considering helical gear tooth surface friction is significantly lower than that without friction. Taking FM = 0.8 as an example, the amplitude of vibration response when considering friction is nearly 9% lower than that when not considering friction, but when considering helical gear tooth surface friction, the resonance frequency changes greatly, The curve of the graph decreases slightly, and it decreases in the case of multiple values.
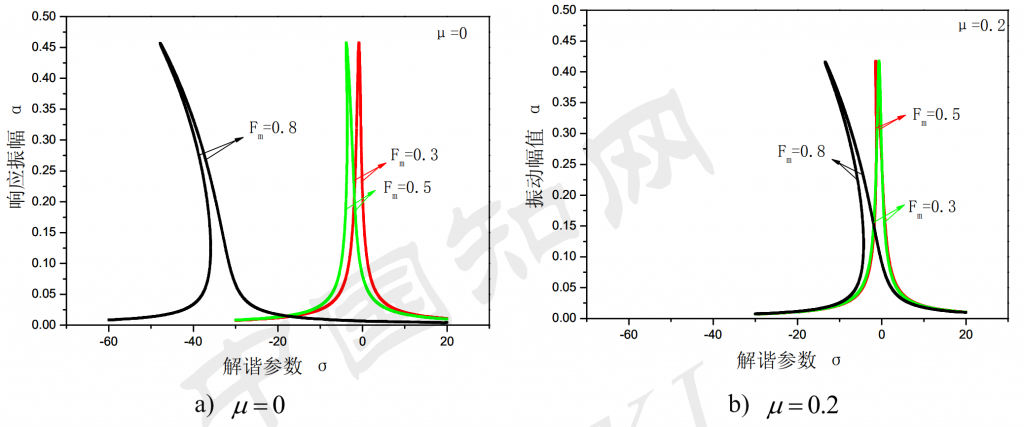
The vibration response caused by dynamic load when friction is considered has an obvious inhibitory effect on the amplitude than when friction is not considered, as shown in Figure 3. When the dynamic load is 0.3, 0.5 and 0.8, the amplitude of vibration response decreases by 7.4%, 8.6% and 9.5% respectively, and the curve bending becomes smaller when the dynamic load is large, indicating that the multi value vibration is reduced.
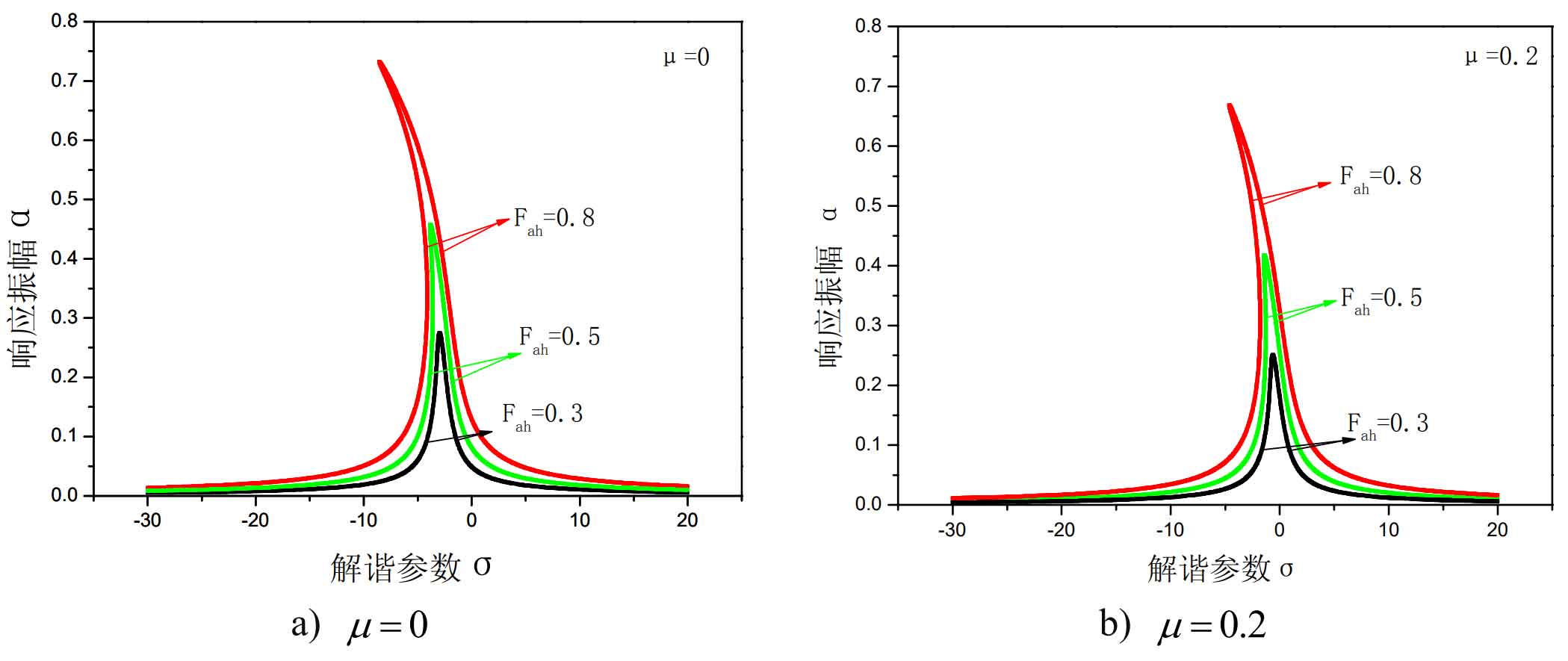
When the friction of helical gear tooth surface is considered, the amplitude of dominant frequency resonance caused by damping is obviously reduced compared with that without friction. As shown in Figure 4, when the damping coefficient is 0.3, 0.5 and 0.8, the reduction range is 7.9%, 10.9% and 12% respectively., The larger the damping coefficient is, the more obvious the reduction of the amplitude of helical gear tooth friction is. However, the resonance frequency tends to increase under the condition of considering friction, but the trend is small.
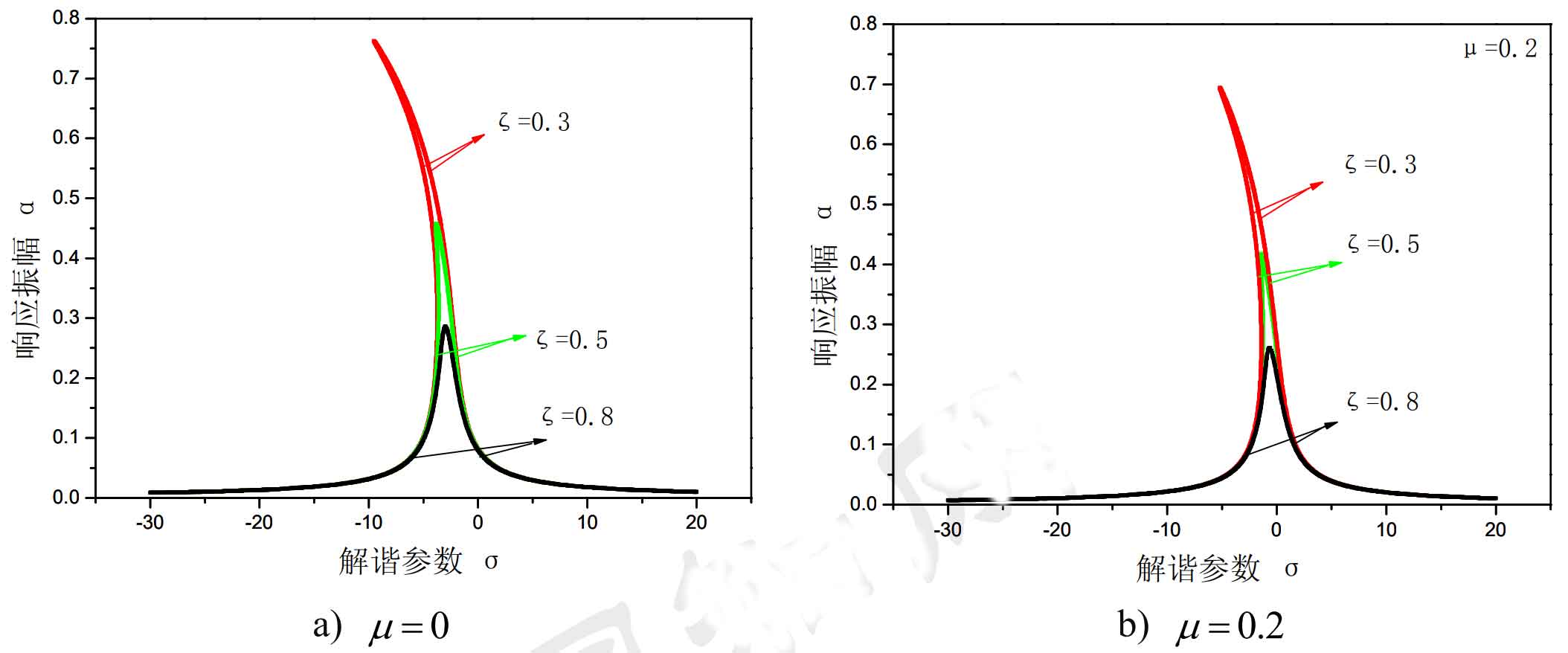