Material innovations aimed at extending the lifespan and performance of spiral bevel gear, crucial components in various mechanical systems, involve advancements in metallurgy, coating technologies, and manufacturing processes. These innovations are geared towards achieving greater durability, efficiency, and reliability in operation, especially under high-stress conditions. Let’s delve into some of the cutting-edge material innovations:
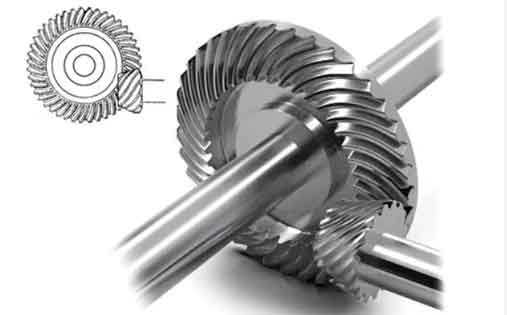
- Advanced Steel Alloys: Modern alloying techniques have led to the development of high-performance steels with enhanced properties for gear manufacturing. These steels are formulated with a mix of elements such as nickel, chromium, molybdenum, and vanadium to improve hardness, toughness, and resistance to wear and fatigue. Ultra-clean steels, produced with minimal impurities, further contribute to the strength and longevity of spiral bevel gear by minimizing potential sites for crack initiation and propagation.
- Case-Hardened Steels: Through processes like carburizing, carbonitriding, and nitriding, the surface of the spiral bevel gear is hardened to withstand wear and fatigue, while the core remains tough and ductile. This differential in properties ensures spiral bevel gear can absorb significant impact loads without failure, extending its operational life.
- Powder Metallurgy and Metal Injection Molding (MIM): These manufacturing techniques allow for the creation of spiral bevel gear from powdered materials, offering superior material properties due to high purity and uniform microstructures. Spiral bevel gear produced through powder metallurgy and MIM can achieve near-net shape precision, reducing the need for extensive machining and thereby preserving the integrity of the material structure.
- Composite Materials: The incorporation of fiber-reinforced polymers and composites into spiral bevel gear manufacturing presents opportunities for weight reduction and enhanced performance, especially in terms of wear resistance and noise reduction. While traditionally not as strong as metal gears, advancements in composite materials technology are making them increasingly competitive for certain applications.
- Surface Engineering and Coatings: Surface modification techniques, including advanced coatings such as diamond-like carbon (DLC), titanium nitride (TiN), and other physical vapor deposition (PVD) coatings, significantly enhance the wear resistance and frictional properties of spiral bevel gear. These coatings can protect the spiral bevel gear surface from abrasive wear, pitting, and scoring, thereby extending the gear’s service life.
- Ceramics and Ceramic Composites: In applications where extreme temperatures, corrosion, and wear are of concern, ceramics and ceramic-metal composites (cermets) offer outstanding performance. Although their use in spiral bevel gear is less common, these materials provide exceptional hardness, wear resistance, and thermal stability.
- Additive Manufacturing (3D Printing): The advent of additive manufacturing allows for the design and fabrication of spiral bevel gear with complex geometries and tailored material properties that were previously unachievable. This technology enables the optimization of spiral bevel gear design for specific applications, potentially leading to spiral bevel gear with improved performance and longer life spans.
These material innovations, coupled with advancements in manufacturing and design techniques, are pivotal in meeting the increasing demands placed on spiral bevel gear across various industries, from automotive to aerospace and beyond. The ongoing development in these areas signifies a promising future for the durability and efficiency of these essential mechanical components.