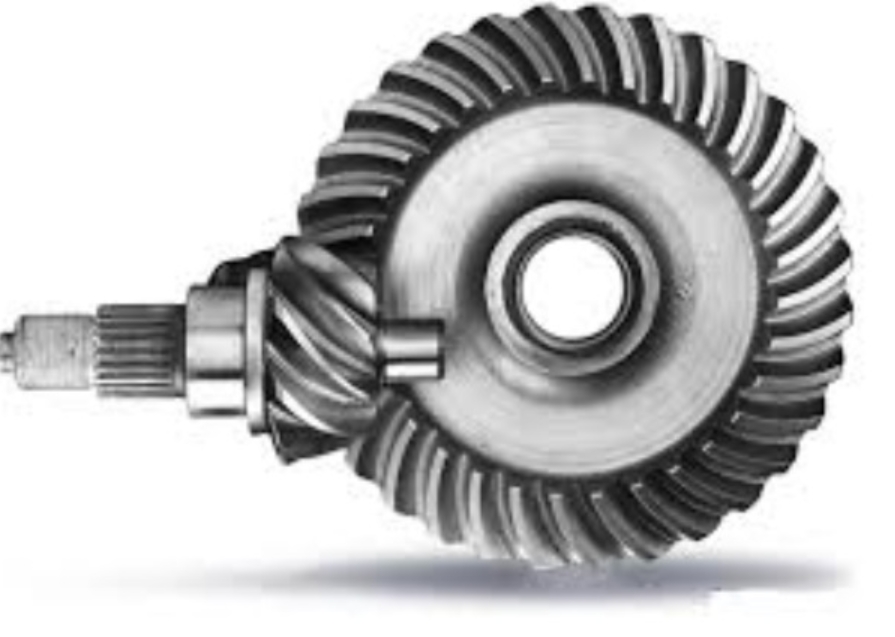
Maximizing the durability and efficiency of hypoid gear systems involves a strategic approach to their design, material selection, manufacturing processes, and maintenance. Hypoid gear, with their unique characteristics, offer significant advantages in various applications, but optimizing these benefits requires a careful balance of several factors:
1. Design Optimization
- Customized Gear Geometry: Designing the gear teeth profile and the offset angle specifically for the intended application can significantly enhance both durability and efficiency.
- Finite Element Analysis (FEA): Using advanced simulation tools like FEA to predict stress distribution and potential failure points helps in refining the design for maximum durability.
2. Material Selection
- High-Strength Materials: Using high-quality materials like advanced steel alloys, which can withstand high stress and wear, is crucial for the durability of hypoid gear.
- Heat Treatment Processes: Implementing processes like case hardening or tempering can greatly increase the toughness and longevity of hypoid gear.
3. Precision Manufacturing
- Advanced Machining Techniques: Employing precision manufacturing technologies like CNC machining ensures that hypoid gear meet the exact design specifications.
- Quality Control: Rigorous quality control throughout the manufacturing process helps in detecting any flaws or inconsistencies that could affect performance.
4. Efficient Lubrication
- High-Quality Lubricants: Using premium lubricants reduces friction, minimizes wear, and helps in heat dissipation, crucial for maintaining efficiency and prolonging hypoid gear life.
- Lubrication System Design: Designing an effective lubrication system that ensures consistent and adequate lubrication across hypoid gear surfaces is vital.
5. Heat Management
- Thermal Analysis: Conducting thermal analysis can inform design changes or the selection of materials that better dissipate heat.
- Cooling Systems: In high-performance applications, integrating cooling systems can prevent overheating and reduce thermal degradation.
6. Maintenance and Monitoring
- Regular Inspections: Routine checks for wear, alignment, and lubrication help in early detection of issues.
- Predictive Maintenance Technologies: Implementing sensors and monitoring technologies can predict wear or failure, allowing for timely maintenance interventions.
7. Research and Development
- Innovative Coatings: Exploring advanced coatings that reduce wear and friction can extend hypoid gear life.
- Alternative Materials: Research into materials like composites or ceramics might offer benefits in specific applications.
8. Sustainability Considerations
- Eco-friendly Lubricants: Using biodegradable or less environmentally harmful lubricants can be considered.
- Recycling and Reusability: Designing hypoid gear with recyclability in mind can enhance the overall sustainability of the system.
Conclusion
Maximizing the durability and efficiency of hypoid gear systems is a multi-faceted process that requires attention to detail in design, materials, manufacturing, and maintenance. By addressing these aspects, the full potential of hypoid gear can be harnessed, leading to systems that offer high performance, longevity, and efficiency. As technology evolves, further advancements in these areas are likely to continue enhancing the capabilities of hypoid gear systems.