1. Maximum circumferential stress of ring gear in design specification
Considering the influence of tooth parameters, load distortion of flexible wheel on load stress and dynamic load coefficient, as well as the influence of different wave generators, the design specification of harmonic gear estimates the maximum load stress of flexible gear ring by correction factor:
Phi=KrtKMKdCu0Eh/rm2
Where: Krt is the stress increase factor for increasing the bending rigidity of the ring gear to the teeth, Krt=(1+h)/h, where: h*=h/m, m is the modulus; KM is the stress increase factor caused by the deformation of the flexible wheel under load; Kd is the dynamic load factor; C is the positive stress factor. For the assembly stress of the plane ring gear, KM=1, Kd=1. It can be obtained from formula (3), when beta=25 degrees, the maximum C=1.43 at the roller, short shaft.Minimum C= -1.52 at location.
Effective stress concentration factor of gear teeth against circumferential stress:
K=(1.6h+0.8)/(1+h)
Considering the influence of gear teeth on the increase of ring stiffness and stress concentration, the influence coefficient of gear teeth on ring stress is as follows:
KrtK=(1.6h+0.8)/h
Get the maximum circumferential stress at the roller of the no-load flexible ring gear
Phi=1.144(2+m/h)u0Eh/rm2(4)
2. Conversion of Maximum Circumferential Stress by Tooth Impact Factor
Replacing the actual teeth with rectangular equivalent teeth, the influence of tooth stress on ring gear is converted. The equivalent tooth thickness is taken as the tooth thickness SF of the actual teeth on the root circle, and the tooth height is calculated as the tooth height h p, s2p=h+h P. P is the pitch at the root (figure). However, the H P needs to be obtained by experiment according to the condition of equal stiffness, which is a problem that has not yet been solved.
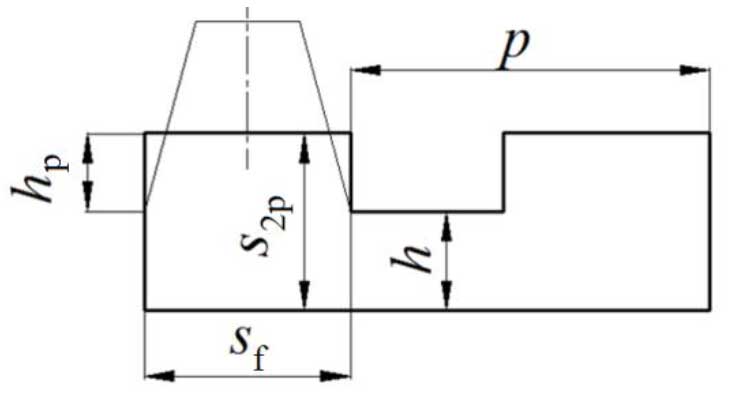
Based on aperture stress, the influence coefficient of gear teeth is introduced to calculate the maximum circumferential bending stress of gear ring.
Phi=Yz(_) (5)
Among them, the influence coefficient of gear teeth
Yz=1/{1_Ks [1(h/s2p)3]} (6)
Where_(_) is the circumferential bending stress of an aperture with wall thickness h, and Ks is the influence factor of tooth thickness, Ks=sf/p;
3. Maximum circumferential stress of toothed ring in photoelastic experiment
Based on the Photoelastic Measurements of 190 smooth shells and 148 true flexible wheel shells, it is recommended that the effective stress concentration coefficient of the gear teeth to the positive stress of the ring gear be 2.2-2.5. In structural analysis, the assembly deformation of the ring gear is pure bending deformation, and the positive stress is the circumferential stress. That is, the maximum circumferential stress of the ring gear is 2.2-2.5 times of the equation (3).