The measurement of non-circular gear with joint wall scanner is to obtain the three-dimensional point cloud model of non-circular gear by laser scanning. The measured three-dimensional point cloud model is compared with the theoretical model, and the deviation value of non-circular gear error items is obtained through calculation. The non-circular gear is clamped on the workbench, and the non-circular gear is scanned by laser scanning probe Tracing measurement.
Firstly, the tooth profile of the measured noncircular gear and the first order elliptic gear is drawn in the 2D drawing software CAXA by using the converted tooth profile method, which is imported into CAXA 3D entity design software to establish the theoretical model, which lays the foundation for the comparison and analysis of the measurement model and the theoretical model. The mathematical model of non-circular gear is established by the normal tooth profile method and the converted tooth profile method The equivalent coefficient K is used to represent the relationship between the two methods, so as to further improve the theoretical modeling accuracy of non-circular gears.
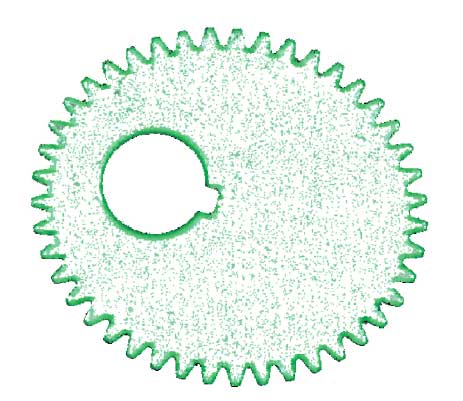
Secondly, the non-circular gear is measured. The robot articulated arm scanner can record the 3D coordinate information of the measured object with high speed and accuracy A series of points on the first-order elliptic gear were collected orderly and evenly to obtain the point cloud data. The point cloud data obtained by scanning were processed by Geomagic qualify reverse software, and the complete and accurate 3D point cloud model was obtained. The point cloud model of the first order non-circular gear was measured as shown in the figure. The iterative close point (ICP) method was used The tooth pitch error, tooth profile error and tooth alignment error of non-circular gear are obtained by analyzing the alignment of the two models based on feature alignment and best fit alignment.
Finally, the accuracy index of non-circular gear error items is studied by analogy with the establishment standard of cylindrical gear accuracy index, and the accuracy grade of non-circular gear error item is obtained. Through analysis and calculation, the tolerance calculation formula of non-circular gear compulsory inspection items is obtained.
The geometric deviation, motion eccentricity, transmission chain error, hob installation eccentricity and other errors in the process of machining will make the ideal position of cutter and workpiece relatively offset, and then affect the pitch deviation, tooth thickness deviation and total profile deviation of non-circular gear.