Abstract
This paper focuses on investigating the meshing behavior and dynamic response of spur gear pairs under the combined effects of assembly errors and tooth surface friction. A method integrating geometric analysis and the energy approach is employed to model the mesh stiffness of spur gears. Furthermore, a six-degree-of-freedom bending-torsional coupling vibration model is developed based on the lumped mass method. The numerical solutions are obtained using the Runge-Kutta method to analyze the system’s meshing behavior and dynamic response. The analysis reveals that the mesh stiffness amplitude of the spur gear pair decreases with the increase of the tooth surface friction coefficient. Simulation results indicate that appropriate adjustment of installation conditions and reasonable tooth surface friction coefficients can improve the transmission accuracy and vibration characteristics of the spur gear pairs. The findings of this study provide valuable references for the dynamic analysis and optimization of spur gear transmission systems under the influence of systematic errors.
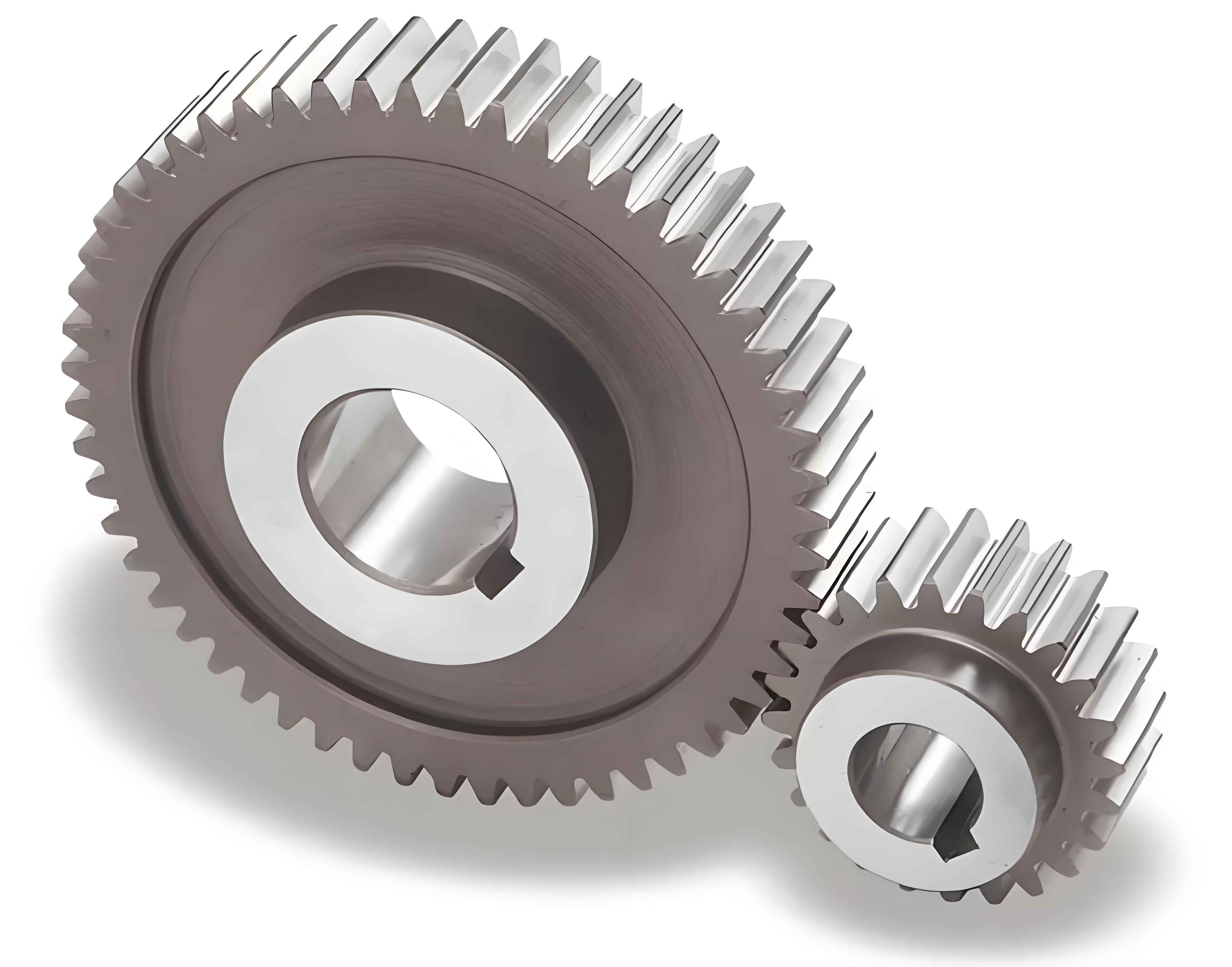
Keywords: Spur gear, mesh stiffness, assembly error, tooth surface friction, dynamic response
1. Introduction
As the gear transmission system evolves towards higher speeds and power densities, reducing vibration and noise levels has emerged as a critical challenge in developing high-performance and high-reliability gear transmission systems. The time-varying nature of mesh stiffness, arising from the varying number of teeth in mesh during the engagement process, significantly impacts the dynamic behavior and vibration characteristics of gear transmission systems. Consequently, the study of gear mesh stiffness and the dynamic modeling of gear transmission systems are crucial for vibration analysis and optimization design, holding immense engineering and scientific significance.
In recent years, various methods have been proposed for mesh stiffness calculation, including the material mechanics method, energy method, finite element method, and experimental method. Among these, the energy method, known for its low cost and high accuracy, is widely used in mesh stiffness modelling. However, the existing literature primarily focuses on the impact of tooth surface friction on mesh stiffness, neglecting the combined effects of assembly errors.
This paper aims to address this gap by investigating the influence of both assembly errors and tooth surface friction on the mesh stiffness and dynamic response of spur gear pairs. By integrating geometric analysis and the energy approach, we develop a comprehensive model for spur gear pairs considering both factors. Furthermore, we analyze the system’s dynamic response through simulations and provide recommendations for optimizing spur gear transmission systems.
2. Literature Review
2.1 Mesh Stiffness Calculation Methods
Several mesh stiffness calculation methods have been proposed, each with its unique advantages and limitations. The material mechanics method, while straightforward, often provides rough estimates due to its simplifications. In contrast, the finite element method and experimental method offer high accuracy but come at a higher computational or experimental cost. The energy method, as a compromise, balances cost and accuracy, making it a popular choice for mesh stiffness modelling.
Previous research has improved the energy method by incorporating factors such as gear base circle radius deviation, tooth root relief, and adjacent tooth interactions [1-6]. Additionally, studies have considered the influence of tooth surface friction and gear faults on mesh stiffness [7-8]. However, the combined effects of assembly errors and tooth surface friction remain understudied.
2.2 Effects of Assembly Errors
Assembly errors, including eccentric errors and installation deviations, can significantly affect gear meshing and dynamic performance. Luo et al. [9] studied the influence of center distance variations on mesh stiffness, while Cao et al. [10] and Xu et al. [11] explored the effects of eccentric errors on planetary gear systems. These studies highlighted the need to consider assembly errors in mesh stiffness modelling to accurately predict gear system behavior.
2.3 Effects of Tooth Surface Friction
Tooth surface friction, governed by factors such as lubricant type and operating conditions, plays a vital role in gear meshing. Jiang et al. [8] and Luo et al. [7] investigated the effects of sliding friction on the mesh stiffness of helical and planetary gears, respectively. Their findings emphasized the need to account for tooth surface friction in dynamic analysis to ensure accurate predictions.
3. Mesh Stiffness Modelling of Spur Gears with Assembly Error and Tooth Surface Friction
3.1 Geometric Analysis of Spur Gear Pairs with Assembly Error
The geometric relationship between spur gear pairs under assembly error conditions. The deviation from the ideal installation position (O_p and O_g) to the actual position (O’_p and O’_g) is represented by the eccentricities e_xp, e_yp, e_xg, and e_yg in the x and y directions for the driving and driven gears, respectively.
Based on this geometric model, the actual meshing line A’B’ and the node point C can be determined, enabling the calculation of key geometric parameters such as the actual center distance and meshing angle.
3.2 Mesh Stiffness Calculation Incorporating Tooth Surface Friction
The mesh stiffness of spur gears is calculated using the energy method, which considers the potential energy stored in the meshing teeth. The total potential energy U comprises bending, axial compression, shear, Hertz contact, and foundation deformation energies (U_b, U_a, U_s, U_h, and U_f, respectively).
The bending deformation energy U_b, for instance, can be expressed as:
Ub=2kbF2=∫0d2EIxM2dx
where F is the meshing force, M is the bending moment, E is the elastic modulus, I_x is the polar moment of inertia, and d is the distance from the tooth root.
The meshing force F can be decomposed into vertical (F_b) and horizontal (F_a) components considering the tooth surface friction coefficient f:
Fa=Fsinα1∓fcosα1
Fb=Fcosα1∓fsinα1
where α_1 is the pressure angle at the meshing point.
The Hertz contact deformation energy U_h and foundation deformation energy U_f are also calculated similarly, incorporating the effects of tooth surface friction on the contact geometry and stiffness.
3.3 Integration of Assembly Error and Tooth Surface Friction
The assembly errors modify the geometric relationship between the spur gears, affecting the meshing line and actual contact points. Consequently, the geometric parameters used in the energy method, such as contact angles and meshing positions, are recalculated to reflect the assembly error conditions.
The tooth surface friction coefficient f, determined by the lubricant properties and operating conditions, directly influences the decomposition of the meshing force into its vertical and horizontal components. This, in turn, affects the potential energies involved in mesh stiffness calculation.
4. Dynamic Response Analysis of Spur Gear Pair
4.1 Six-Degree-of-Freedom Bending-Torsional Coupling Vibration Model
A six-degree-of-freedom bending-torsional coupling vibration model is developed based on the lumped mass method. The model considers the displacement of the driving and driven gears in the x, y, and θ directions.
The dynamic equations of motion for the system are derived using Newton’s second law of motion and the Euler-Lagrange equations:
mpx¨p+kxpxp+cxpx˙p=−Fm
mpy¨p+kypyp+cypy˙p=0
Ipθ¨p+FmRbp=Tp
mgx¨g+kxgxg+cxgx˙g=Fm
mgy¨g+kygyg+cygy˙g=0
Igθ¨g+FmRbg=−Tg
where m_p and m_g are the masses of the driving and driven gears, I_p and I_g are their moments of inertia, k and c are the stiffness and damping coefficients of the support bearings, R_bp and R_bg are the base circle radii, and F_m is the dynamic meshing force.
The dynamic meshing force F_m is related to the mesh stiffness k_m(t) and dynamic transmission error δ_pg:
Fm=km(t)δpg+cmδ˙pg
where c_m is the meshing damping and δ_pg is the dynamic transmission error given by:
δpg=xp−xg+Rbpθp−Rbgθg
4.2 Numerical Solution Using the Runge-Kutta Method
The Runge-Kutta method is employed to numerically solve the system’s equations of motion. This approach provides stable and accurate solutions for dynamic systems, making it suitable for analyzing the complex vibrations of spur gear pairs.
5. Simulation Results and Discussion
5.1 System Parameters and Conditions
The main parameters of the spur gear transmission system used in the simulations are summarized in Table 1. Three different installation conditions with varying eccentricities are considered, as listed in Table 2.
Table 1: Main Parameters of the Spur Gear Transmission System
Parameter | Value |
---|---|
Number of teeth (driving) | 50 |
Number of teeth (driven) | 50 |
Module (m) | 3 mm |
Face width (b) | 20 mm |
Mass of each gear | 2.5274 kg |
Moment of inertia (driving) | 340 kg·m^2 |
Moment of inertia (driven) | 340 kg·m^2 |
Pressure angle (α) | 20° |
Elastic modulus (E) | 2×10^5 MPa |
Poisson’s ratio (ν) | 0.3 |
Bearing stiffness (k_x, k_y) | 10^8 N/m |
Meshing damping ratio (ζ) | 0.07 |
Bearing damping (c_x, c_y) | 10^5 N/(m/s) |
Input torque (T_p) | 340 N·m |
Gear speed (ω) | 340 rpm |
Table 2: Installation Conditions with Varying Eccentricities
Condition | e_xp (μm) | e_yp (μm) | e_xg (μm) | e_yg (μm) |
---|---|---|---|---|
1 | 0 | 0 | 0 | 0 |
2 | 0 | 0 | 10 | 10 |
3 | 0 | 0 | 100 | 100 |
5.2 Effect of Tooth Surface Friction
The variation in mesh stiffness with different tooth surface friction coefficients. As the friction coefficient increases, the mesh stiffness amplitude decreases, particularly in the single-double tooth meshing transition region
The dynamic transmission error (DTE) for different friction coefficients. A friction coefficient of f = 0.05 results in the smallest DTE amplitude, indicating that an optimal friction coefficient can improve transmission performance.
5.3 Effect of Assembly Error
The influence of assembly errors on mesh stiffness and DTE is analyzed, respectively. Assembly error conditions significantly alter the double-tooth meshing region width, affecting the actual contact ratio and meshing state.
Condition 3 exhibits the smallest DTE amplitude, while Condition 2 shows the largest, indicating that adjusting the installation conditions can enhance transmission accuracy and reduce vibrations.
6. Conclusion
This paper presents a comprehensive analysis of the mesh stiffness and dynamic response of spur gear pairs under the combined effects of assembly errors and tooth surface friction. By integrating geometric analysis and the energy method, a mesh stiffness model considering both factors is developed. The model is validated through numerical simulations using the Runge-Kutta method.
The key findings include:
- Mesh Stiffness Variation: The mesh stiffness amplitude decreases with increasing tooth surface friction coefficient, particularly in the single-double tooth meshing transition region.
- Optimal Friction Coefficient: An optimal tooth surface friction coefficient (f = 0.05 in this study) minimizes the dynamic transmission error amplitude, improving the transmission performance.
- Assembly Error Effects: Assembly errors significantly affect the mesh stiffness and dynamic response of spur gears. Adjusting installation conditions can enhance transmission accuracy and reduce vibrations.
The proposed model and findings provide valuable insights into the dynamic behavior of spur gear pairs under systematic errors, offering guidance for the design and optimization of high-performance gear transmission systems.