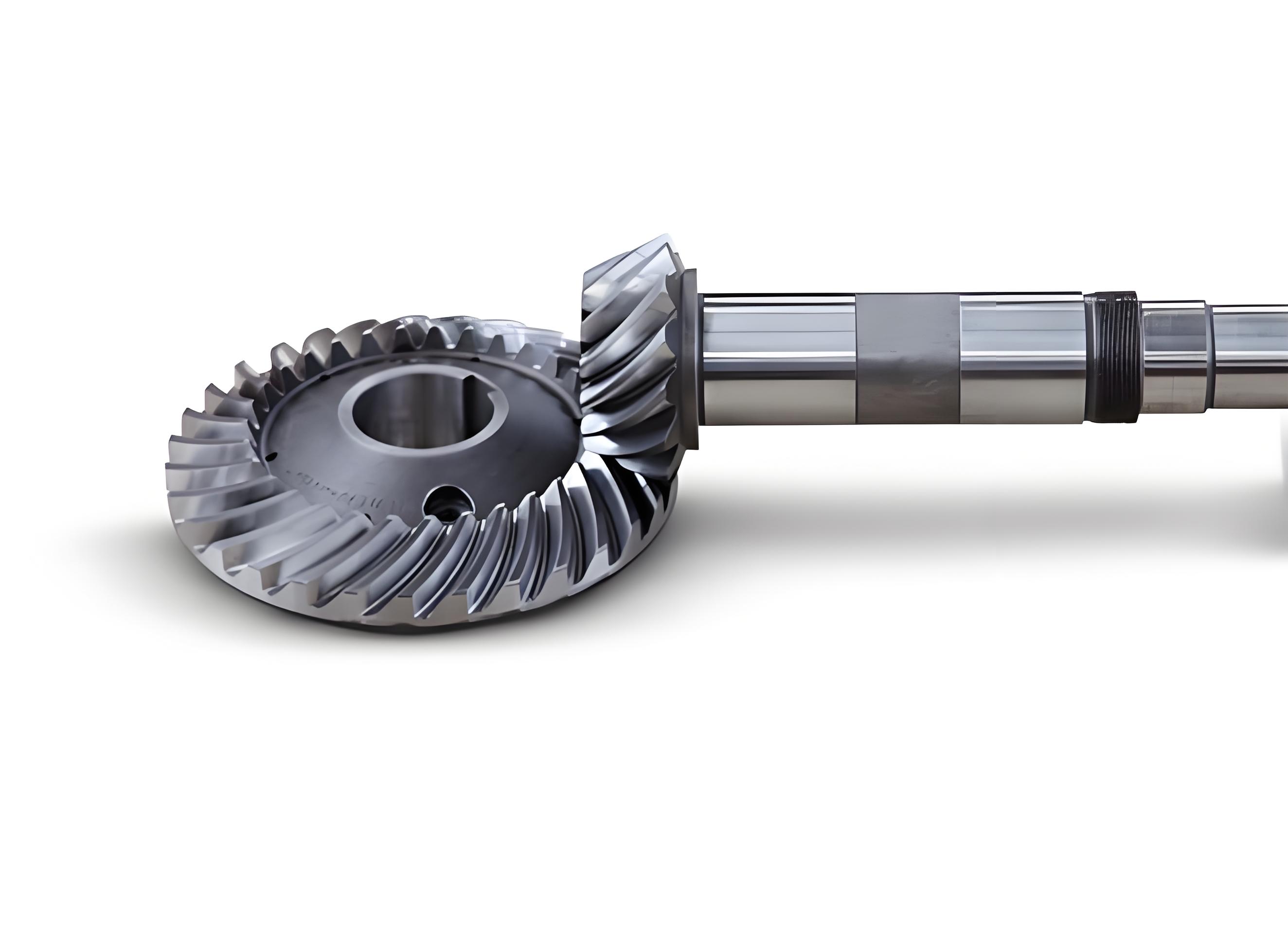
Abstract
The durability of spiral bevel gear is significantly influenced by the material properties used in their construction. This study compares various materials to understand their impact on the performance and lifespan of spiral bevel gear. Key material properties such as hardness, toughness, wear resistance, and fatigue strength are analyzed to determine the optimal materials for high-stress applications.
Introduction
Spiral bevel gear is critical components in many high-performance mechanical systems, requiring materials that can withstand significant loads, stresses, and wear. The selection of appropriate materials is essential for ensuring the durability and reliability of these gear. This study examines different materials commonly used in the manufacture of spiral bevel gear and evaluates their performance under various operational conditions.
Materials Analyzed
- Alloy Steels
- Case-Hardened Steels: 8620, 9310
- Through-Hardened Steels: 4140, 4340
- Stainless Steels
- Martensitic Grades: 17-4 PH, 410
- Tool Steels
- Cold-Work Steels: D2, A2
- Non-Ferrous Alloys
- Titanium Alloys: Ti-6Al-4V
- Aluminum Alloys: 7075-T6
- Composite Materials
- Carbon Fiber Reinforced Polymers (CFRP)
Material Properties and Their Impact
- Hardness
- Importance: Higher hardness improves wear resistance, reducing surface wear and extending spiral bevel gear life.
- Materials: Tool steels (e.g., D2, A2) exhibit high hardness due to their carbon and alloy content, making them ideal for high-wear applications.
- Toughness
- Importance: Toughness is critical for resisting impact loads and preventing brittle fracture.
- Materials: Alloy steels like 4140 and 4340 offer a good balance of toughness and strength, making them suitable for dynamic loading conditions.
- Wear Resistance
- Importance: Wear resistance is essential for maintaining spiral bevel gear accuracy and efficiency over time.
- Materials: Case-hardened steels (e.g., 8620, 9310) provide excellent wear resistance due to their hardened surface layers.
- Fatigue Strength
- Importance: High fatigue strength ensures spiral bevel gear can withstand repeated loading cycles without failure.
- Materials: Titanium alloys (e.g., Ti-6Al-4V) and certain high-strength steels (e.g., 4340) are known for their superior fatigue strength.
- Corrosion Resistance
- Importance: Corrosion resistance is important for spiral bevel gear operating in harsh environments.
- Materials: Stainless steels (e.g., 17-4 PH, 410) offer excellent corrosion resistance, making them ideal for marine and chemical applications.
Comparative Analysis
- Alloy Steels
- Pros: Excellent toughness, good wear resistance, cost-effective.
- Cons: Moderate corrosion resistance, may require surface treatments for enhanced performance.
- Applications: Automotive spiral bevel gear, industrial machinery.
- Stainless Steels
- Pros: High corrosion resistance, good toughness.
- Cons: Lower hardness compared to tool steels, higher cost.
- Applications: Marine applications, chemical processing equipment.
- Tool Steels
- Pros: High hardness and wear resistance, good fatigue strength.
- Cons: Limited toughness, higher cost.
- Applications: High-precision tools, heavy-duty gear.
- Non-Ferrous Alloys
- Titanium Alloys:
- Pros: Excellent fatigue strength, good corrosion resistance, lightweight.
- Cons: High cost, challenging to machine.
- Applications: Aerospace spiral bevel gear, high-performance racing applications.
- Aluminum Alloys:
- Pros: Lightweight, good machinability.
- Cons: Lower strength and wear resistance, not suitable for high-stress applications.
- Applications: Low-load applications, where weight reduction is crucial.
- Titanium Alloys:
- Composite Materials
- Pros: High strength-to-weight ratio, good corrosion resistance.
- Cons: Limited wear resistance, complex manufacturing processes.
- Applications: Specialized applications where weight reduction and corrosion resistance are critical.
Case Studies
- Automotive Industry
- Material Used: 8620 case-hardened steel.
- Findings: Excellent balance of wear resistance and toughness, cost-effective for mass production.
- Aerospace Industry
- Material Used: Ti-6Al-4V titanium alloy.
- Findings: Superior fatigue strength and corrosion resistance, ideal for high-performance applications despite higher costs.
- Marine Industry
- Material Used: 17-4 PH stainless steel.
- Findings: High corrosion resistance and adequate toughness, suitable for harsh marine environments.
Conclusion
The choice of material significantly impacts the durability and performance of spiral bevel gear. Alloy steels, particularly case-hardened variants, provide a good balance of properties for general applications. For high-stress and specialized environments, materials like titanium alloys and stainless steels offer superior performance. Understanding the specific requirements of the application is essential for selecting the optimal material, ensuring reliability, and extending the lifespan of spiral bevel gear.
References
- Materials Science and Engineering A: Research on the mechanical properties and applications of different spiral bevel gear materials.
- Journal of Tribology: Studies on wear resistance and lubrication effects on spiral bevel gear materials.
- International Journal of Fatigue: Papers on fatigue performance and failure analysis of spiral bevel gear materials.
- Metallurgical and Materials Transactions A: Articles on the effects of heat treatment and surface engineering on spiral bevel gear materials.
This comparative study provides a detailed understanding of the material properties that influence the durability of spiral bevel gear, offering valuable insights for material selection and gear design optimization.