1. Introduction
Helical cylindrical gears play a crucial role in various mechanical systems, especially in agricultural machinery. Their unique characteristics such as high transmission efficiency, smooth operation, strong load – carrying capacity, and low noise make them ideal for applications in tractors, harvesters, seeders, and mixers. The X62W milling machine is a commonly used equipment for machining helical cylindrical gears, offering advantages like high precision, high efficiency, controllable accuracy, wide processing range, and cost – reduction. This article aims to provide a detailed and comprehensive guide on the milling process of helical cylindrical gears using the X62W milling machine, covering everything from gear parameters and processing methods to potential problems and solutions.
2. Gear Parameters and Their Significance
2.1 Basic Gear Parameters
Helical cylindrical gears are defined by several key parameters. The following table summarizes these parameters and their significance:
Parameter | Symbol | Explanation |
---|---|---|
Number of Teeth | z | Determines the gear ratio and affects the speed and torque transmission. A larger number of teeth generally leads to a smoother transmission but may increase the size and weight of the gear. |
Normal Module | \(m_{n}\) | Controls the size of the gear teeth. It is a fundamental parameter for gear design and manufacturing, and gears with the same normal module can mesh properly. |
Normal Pressure Angle | \(\alpha_{n}\) | Influences the force distribution during gear meshing. A standard normal pressure angle of \(20^{\circ}\) is commonly used in many applications for its balanced performance in terms of strength and smooth operation. |
Helix Angle | \(\beta\) | Determines the direction and angle of the helical teeth. It affects the load – carrying capacity, noise level, and axial force in the gear system. Different helix angles are chosen based on specific application requirements. |
Hand of Helix | – | Specifies whether the gear has a left – hand or right – hand helix. This is important for proper gear meshing and determining the direction of rotation and axial forces. |
Precision Grade | – | Indicates the manufacturing accuracy of the gear. Lower precision grades are suitable for less demanding applications, while higher precision grades are required for high – performance machinery. |
Material | – | Affects the mechanical properties of the gear, such as strength, hardness, and wear resistance. Common materials for gears include 45 steel, which offers a good balance of properties and cost – effectiveness. |
2.2 Example Gear Parameters
For the purpose of illustration, we will use a set of sample gear parameters throughout this article:
Parameter | Value |
---|---|
Number of Teeth (z) | 21 |
Normal Module (\(m_{n}\)) | 2.5 |
Normal Pressure Angle (\(\alpha_{n}\)) | \(20^{\circ}\) |
Helix Angle (\(\beta\)) | \(9^{\circ}\) |
Hand of Helix | Left – hand |
Precision Grade | 9 (low – precision grade according to GB10095) |
Material | 45 steel |
3. Processing Method Selection
3.1 Comparison of Gear Processing Methods
There are several methods for manufacturing gears, with the two main ones being the generating method and the form – milling method. The generating method, often used in CNC machines or dedicated gear – manufacturing equipment, offers high precision but is more complex and expensive. The form – milling method, on the other hand, is more suitable for small – batch production and low – precision gears. The following table compares these two methods:
Processing Method | Precision | Applicability | Cost | Equipment Requirements |
---|---|---|---|---|
Generating Method | High | High – precision gears in large – scale production | High | CNC machines or dedicated gear – hobbing machines |
Form – Milling Method | Moderate | Small – batch, low – precision gears | Low | General – purpose milling machines like X62W |
3.2 Why Choose the Form – Milling Method on X62W Milling Machine
Given the low – precision requirement (Grade 9) of our example gear, the form – milling method using the X62W milling machine is a practical choice. The X62W milling machine is widely available in many workshops, and the form – milling method is relatively simple to implement. It can meet the production needs of small – batch, low – cost gears, such as those used in agricultural machinery.
4. Selection of Gear Milling Cutter and Cutting Fluid
4.1 Selection of Gear Milling Cutter
The selection of the gear milling cutter is based on the normal module (\(m_{n}\)), normal pressure angle (\(\alpha_{n}\)), and equivalent number of teeth (\(z_{v}\)) of the gear.
- Calculation of Equivalent Number of Teeth (\(z_{v}\)): The equivalent number of teeth is calculated using the formula \(z_{v}=\frac{z}{\cos^{3}\beta}\) or \(z_{v}=Kz\) (by looking up the coefficient K in the equivalent gear coefficient table). For our example gear (\(z = 21\), \(\beta=9^{\circ}\)), using \(z_{v}=\frac{z}{\cos^{3}\beta}=\frac{21}{(\cos9^{\circ})^{3}}\approx21.798\).
- Selection of Milling Cutter: Based on the equivalent number of teeth (\(z_{v}\approx21.798\)), referring to the standard disc – type gear milling cutter number table, when the number of teeth is in the range of 21 – 25, a set of 8 – piece, \(m = 2.5\) No. 4 standard disc – type gear milling cutter is selected.
4.2 Selection of Cutting Fluid
The cutting fluid plays important roles in cooling and flushing during the gear milling process. For the X62W milling machine, considering its relatively old design and the need to prevent internal gears from rusting, oil – based lubrication is preferred. Among various cutting oils, No. 0 diesel is chosen due to its cost – effectiveness and safety. The following table summarizes the functions and selection criteria of cutting fluids:
Function | Importance | Selection Considerations for X62W Milling Machine |
---|---|---|
Cooling | High | Helps to reduce the temperature of the cutting zone, preventing overheating of the tool and workpiece. |
Flushing | Moderate | Removes chips from the cutting area, ensuring smooth cutting. |
Anti – rust | High | Protects the machine’s internal gears from rusting. |
Cost – effectiveness | High | No. 0 diesel is selected as it offers a good balance between performance and cost. |
Safety | High | Avoids the use of potentially hazardous fluids like kerosene. |
5. Preparation Work Before Milling
5.1 (Calibration of the Milling Machine)
The rotation direction of the worktable needs to be determined according to the helix direction of the gear. For a left – hand helix gear, the worktable is rotated clockwise by the helix angle (\(9^{\circ}\) in our example). This step is crucial as it ensures that the milling cutter can cut the helical teeth at the correct angle.
5.2 (Installation of the Dividing Head and Tailstock)
The dividing head and tailstock should be installed in an appropriate position to ensure sufficient space for workpiece clamping and unclamping. They need to be accurately aligned to ensure the concentricity of the workpiece during machining.
5.3 (Preparation of the Mandrel)
A suitable mandrel is selected based on the inner hole of the gear blank. The mandrel should firmly hold the gear blank without interfering with the milling process. It serves as a key component to ensure the stability and accuracy of the workpiece during machining.
5.4 (Inspection, Installation, and Calibration of the Gear Blank)
The outer diameter, inner hole size, coaxiality between the outer diameter and inner hole, and the runout of the gear end face relative to the inner hole axis of the gear blank are inspected. After passing the inspection, the gear blank is fixed on the mandrel, and then the mandrel with the gear blank is installed between the dividing head spindle and the tailstock center. The coaxiality of the gear blank outer diameter is checked using a dial indicator to ensure machining accuracy.
5.5 (Installation of the Milling Cutter and Centering)
The selected milling cutter is installed on the milling machine, and the centering is carried out using the scribing and trial – cutting method. This ensures that the milling cutter is accurately positioned relative to the gear blank, which is essential for cutting the teeth evenly.
6. Processing – Related Calculations and Installation of Change Gears
6.1 (Lead Calculation)
The lead (\(p_{h}\)) is the distance the cutter travels along the workpiece during one complete rotation of the dividing head. It is calculated using the formula \(p_{h}=\frac{\pi m_{n}z}{\sin\beta}\). For our example gear (\(m_{n}=2.5\), \(z = 21\), \(\beta = 9^{\circ}\)), \(p_{h}=\frac{3.14\times2.5\times21}{\sin9^{\circ}}\approx1508\).
6.2 (Calculation of Change Gears)
The calculation of change gears is to determine the speed ratio, ensuring that when the dividing head rotates \(360^{\circ}\), the cutter travels the correct distance along the workpiece. The speed ratio (i) is calculated based on the pitch of the longitudinal feed screw of the worktable (\(P_{r}\)) and the lead (\(p_{h}\)). For the X62W milling machine, \(P_{r}=6mm\), and \(i=\frac{z_{1}z_{3}}{z_{2}z_{4}}=\frac{40P_{r}}{p_{h}}\). Substituting the values, \(i=\frac{40\times6}{1508}\approx0.2268\). After approximation, the change gears are selected as \(z_{1}=30\), \(z_{2}=60\), \(z_{3}=40\), \(z_{4}=90\).
6.3 (Installation of Change Gears)
The side – shaft gear – hanging method is used to connect the longitudinal feed screw of the worktable and the side – shaft of the dividing head with change gears. Since the gear to be processed has a left – hand helix, an intermediate gear is used to adjust the rotation direction of the gear blank. During installation, the fixing screws of the dividing plate are loosened first. Then, the driven gear \(z_{4}\) is installed on the side – shaft at the rear end of the dividing head spindle, the driving gear \(z_{1}\) is installed at the end of the longitudinal feed screw of the worktable, and \(z_{2}\) and \(z_{3}\) are connected together with a key and installed between \(z_{1}\) and \(z_{4}\). It should be noted that the clearance between each pair of gears should be appropriate to ensure smooth transmission.
6.4 (Indexing Calculation)
The indexing calculation is to determine the number of turns of the dividing head handle for each tooth machining. The formula is \(n=\frac{40}{z}\). For our example gear (\(z = 21\)), \(n=\frac{40}{21}=1\frac{19}{21}\). In the common hole plate, a hole circle with a multiple of 21 is selected. To ensure higher machining accuracy, a hole circle with more holes is preferred. In this case, a 42 – hole circle is selected, and \(n = 1\frac{38}{42}\). The dividing fork is adjusted according to 38 hole pitches.
7. Gear Milling Process
7.1 (Inspection of the Rotation Direction of the Dividing Head Spindle and the Lead)
Before starting the milling process, it is necessary to check whether the rotation direction of the dividing head spindle is correct and whether the lead is accurate. This can be done by making a trial cut on a scrap piece or by performing a dry – run of the machine. Only when both are correct can the formal milling process begin.
7.2 (Selection of Milling Method)
There are two main milling methods: up – milling and down – milling. The following table compares the characteristics of these two methods:
Milling Method | Cutting Thickness Change | Workpiece 受力情况 (Force Condition of the Workpiece) | Impact on Machining Quality | Applicability |
---|---|---|---|---|
Up – milling | From zero to maximum. The cutting edge may cause surface hardening and increase tool wear. | The milling force is opposite to the feed direction, which may cause the workpiece to vibrate and is not conducive to clamping. | May result in a relatively rough surface finish. | Suitable for general – purpose milling when the machine has large backlash. |
Down – milling | From maximum to zero. Can obtain a better surface finish and improve tool durability. | The feed force makes the screw and nut contact tightly on one side, but may cause the worktable to move suddenly if the backlash is large. | Can improve the surface quality and tool life. | Suitable for finishing and machines with small backlash. |
For the X62W milling machine, due to its relatively large gear backlash and low – precision lead screw, up – milling is more suitable for rough machining, and down – milling is more suitable for finishing.
7.3 (Selection of Milling Cutter Speed)
The milling cutter speed is selected based on the material of the gear and the machining stage (rough or finish machining). For 45 steel, the rough – milling speed (\(v_{c}\)) is about 32m/min, and the finish – milling speed is about 40m/min. The spindle speed (n) of the milling machine can be calculated using the formula \(n=\frac{1000v_{c}}{\pi D}\), where D is the diameter of the milling cutter. Given a milling cutter diameter of about 70mm, the spindle speed for rough machining is \(n = 90r/min\), and for finish machining is \(n = 130r/min\).
7.4 (Rough Milling of Gear Tooth Profile)
The rough – milling width (\(a_{e}\)) is calculated as \(a_{e}=2.25m_{n}-0.3\). For \(m_{n}=2.5\), \(a_{e}=2.25\times2.5 – 0.3 = 49.5mm\). Since the depth is relatively low, the worktable can be raised to 49.5mm at one time, and the teeth are machined one by one.
7.5 (Finish Milling of Gears)
Based on the equivalent number of teeth (\(z_{v}=21.798\)), the values of \(\bar{s}\) and \(\overline{h_{m}}\) are obtained through table – lookup and interpolation calculation. After rounding the equivalent number of teeth and looking up the table, and using the proportional interpolation method, we get \(\overline{s_{n}}=1.5695\), \(\overline{h_{a n}}=1.0820\). Then, the chordal tooth thickness (\(S_{n}\)) and chordal tooth height (\(\bar{h}_{an}\)) at the pitch circle are calculated as \(S_{n}=m_{n}\overline{S_{n}}=2.5\times1.5695 = 3.92375\) and \(\bar{h}_{an}=m_{n}\bar{h}_{an}=2.5\times1.0820 = 2.705\) respectively. The chordal tooth thickness at the pitch circle is measured using a gear tooth vernier caliper, and the additional feed amount for finish milling is calculated according to \(\Delta a_{e}=1.37(s_{s}^{-}实 -\overline{s_{s}})\), where \(s_{s}^{-}实\) is the actual measured value of the chordal tooth thickness at the pitch circle after rough milling. The gear is then finish – milled according to the \(\Delta a_{e}\) value.
8. Precautions
8.1 (Trial – Cutting Inspection)
Before mass production, a trial – cutting must be carried out to check whether the change gears, lead, and worktable rotation direction are adjusted correctly. This can prevent the production of a large number of defective products.
8.2 (Loosening the Locking Handle of the Dividing Head Spindle and the Fixing Screws of the Dividing Plate)
Before milling, the locking handle of the dividing head spindle and the fixing screws of the dividing plate should be loosened to ensure the normal rotation of the dividing head during the machining process.
8.3 (Inserting the Pin of the Indexing Handle into the Corresponding Hole)
During the milling process, the pin of the indexing handle must be inserted into the corresponding hole on the dividing plate to ensure accurate indexing and prevent errors in the number of teeth.
8.4 (Selecting the Nut for Clamping the Workpiece According to the Helix Direction)
When clamping the workpiece, a nut with the same helix direction as the gear should be selected. For a left – hand helix gear, a left – hand nut is chosen, and a fine – pitch left – hand nut is preferred for better fastening.
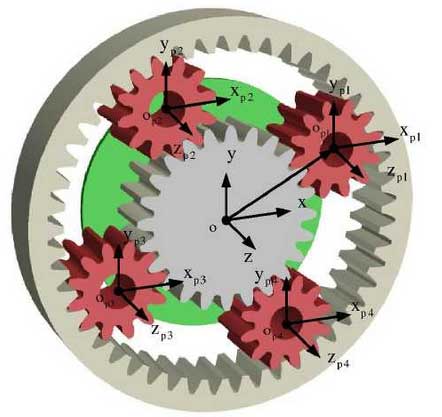