This article focuses on a new type of plane helical cylindrical gear and its machining method. It begins with an introduction to the background and significance of the research, highlighting the limitations of existing cylindrical gear machining methods and the need for improvement. The main body of the article elaborates on the machining principle of the plane helical cylindrical gear, including the formation principle of the plane helical tooth line, the gear machining cutter head design, and the generating motion principle. It also describes the machining and simulation process, presenting the models of the machining cutter head and the simulation results. The geometric parameters and meshing characteristics of the plane helical cylindrical gear are analyzed in detail, demonstrating its advantages in reducing meshing load and improving bearing capacity. Finally, the article concludes with a summary of the research findings and prospects for future research.
1. Introduction
Cylindrical gear transmission is widely used in power transmission mechanisms. The meshing characteristics of gear pairs directly affect the transmission performance of mechanical equipment, and the geometry of gear teeth is crucial for the performance of gear pairs. Currently, there are several types of cylindrical gears, such as spur gears, helical gears, herringbone gears, and circular arc tooth line cylindrical gears. However, existing machining methods like hobbing and shaping have limitations in achieving continuous full-tooth-width gear machining, resulting in restricted machining efficiency. Additionally, gear pairs are prone to meshing load due to machining, installation errors, and elastic deformation, which affects the service life of gears. In recent years, many scholars have studied circular arc tooth line cylindrical gears and their machining methods, but these methods often involve single-tooth cutting, leading to low machining efficiency. To address these issues, this article proposes a new type of plane helical cylindrical gear and its rapid prototyping method.
2. Machining Principle of Plane Helical Cylindrical Gear
2.1 Plane Helical Tooth Line Formation Principle
The hobbing and shaping methods commonly used for machining cylindrical gears cannot achieve continuous full-tooth-width machining. To improve machining efficiency, a tool is installed on a large cutter head. When machining a rack as an example, if the cutter head rotates at a high speed while the rack is stationary in the radial direction of the cutter head, the machined tooth groove will be circular arc-shaped. This method requires indexing after each tooth groove is machined, limiting the efficiency. To overcome this, the rack is made to move linearly in the radial direction of the cutter head while the cutter head rotates. When the speed relationship satisfies that the cutter head rotates one circle and the rack moves one tooth pitch, a plane helical tooth line (Archimedes spiral line) is formed, enabling continuous full-tooth-width machining. For cylindrical gear machining, there are differences compared to rack machining. It involves deep-cutting and generating machining. In deep-cutting, the speed of the rack movement is converted to the angular velocity of the cylindrical workpiece, and the workpiece needs to make a feed motion along the axial direction of the cutter head. In generating machining, additional rotational speed and linear motion in the radial direction are required for the gear blank.
2.2 Gear Machining Cutter Head
Since a single tool may result in large cutting amounts and difficulty in ensuring machining efficiency and accuracy, multiple tools are evenly arranged on the large cutter head according to a plane helical line, with the pitch of the helical line being the same as the gear pitch. The tools are divided into main cutting tools and auxiliary cutting tools. The main cutting tool is installed at a certain height, and the auxiliary cutting tools are installed lower to pre-cut the tooth grooves of the workpiece, reducing the cutting amount and force of the main cutting tool. The polar coordinate equation of the tool arrangement helical line is given, and the distance of each tool from the center of the cutter head can be calculated. The main and auxiliary cutting tools have the same shape, consisting of an outer cutting edge and an inner cutting edge, which generate the concave and convex surfaces of the gear tooth, respectively.
2.3 Generating Motion Principle
During machining, the cutter head rotates at an angular velocity ωD around the YD axis as the main motion, and the gear blank rotates at an angular velocity ωC around the zC axis. To ensure accurate machining of the tooth grooves, the relationship between ωC and ωD is determined. For deep-cutting of the tooth grooves, the gear blank also makes a continuous feed motion along the YC direction. For generating the involute tooth profile, the gear blank makes a generating motion relative to the machining tool, with specific rotational and linear motions as described. The left and right tooth surfaces are machined in a similar manner with some differences in the direction of motion.
3. Machining and Simulation of Plane Helical Cylindrical Gear
3.1 Machining Cutter Head Model
Based on the machining principle, the models of the machining cutter head and the gear blank are established using SOLIDWORKS software. The cutter head and tools are then imported into the VERICUT tool management library. The gear machining tool has a 90° angle with the cutter head plane, and the cutting edge rotates to form a theoretical cutting edge cylindrical surface.
3.2 Machining Simulation
After setting appropriate milling parameters and importing the NC program, the gear simulation machining is carried out. The simulation shows that there is no interference or collision during the process, and a plane helical cylindrical gear is obtained. The machined gear tooth surface has concave and convex surfaces, with the radius of the concave tooth line being slightly larger than that of the convex tooth line, forming a slightly drum-shaped tooth.
3.3 Actual Machining
Based on the machining method and the simulation verification results, a plane helical cylindrical gear machining machine is developed. The cutter head of the machine has 6 front-to-back through-type tool slots for installing tools. The machine uses special tools made of hard alloy steel and can achieve continuous full-tooth-width cutting of gears, with higher machining efficiency than existing hobbing methods.
4. Geometric Parameters and Meshing Analysis of Plane Helical Cylindrical Gear
4.1 Main Geometric Parameters and Characteristics
The plane helical cylindrical gear obtained by the above machining method has concave and convex tooth surfaces. The radius of the concave tooth line is slightly larger than that of the convex tooth line, and the difference between them at the same helical line expansion angle is related to the gear modulus. The gear has five main parameters: modulus m, number of teeth Z, pressure angle α, tooth width B, and spiral line curvature radius RT at the tooth width midline. By analyzing the plane helical tooth line rack according to the meshing relationship between the gear and the rack, the characteristics of the gear can be understood. The pitch of the helical tooth line is equal to the gear pitch, and the tooth thickness at the tooth width midline is equal to the tooth groove width, which is half of the circumferential tooth pitch. This feature can ensure that the contact force of the gear pair is mainly distributed in the middle of the tooth surface, reducing stress concentration at the tooth roots of both ends of the gear teeth and effectively reducing meshing load caused by machining and installation errors.
4.2 Meshing Characteristics Analysis
Using two plane helical cylindrical gear models with the same parameters but opposite rotation directions, the meshing characteristics of the gear pair are analyzed. By accurately assembling the gear pair in SOLIDWORKS software and using the interference check tool for analysis, it is found that the theoretical contact interval is mainly distributed in 80% – 90% of the middle area of the contact tooth surface of the gear pair, and the force on both ends of the gear teeth is small. This can effectively reduce the bending stress at the tooth roots of both ends of the gear teeth and improve the bearing capacity of the gear pair.
5. Conclusion
This article proposes a method of continuous full-tooth-width cutting of cylindrical gears using a large cutter head and verifies its feasibility through VERICUT software simulation. The geometric characteristics of the plane helical cylindrical gear are analyzed. The gear has a standard involute tooth profile in the middle section, and the tooth line is a plane helical line. The theoretical tooth surface contact characteristics of the gear pair show that the contact interval is mainly distributed in the middle part of the contact tooth surface, reducing the bending stress at the tooth roots of the gear teeth and improving the bearing capacity. Future research directions include calculating the tooth surface equation, analyzing the stress distribution on the tooth surface and at the tooth roots, and building a gear transmission experimental device to study the transmission characteristics.
6. Tables for Summary
Table 1: Gear and Machining Tool Parameters
Parameter | Value |
---|---|
Number of teeth | 30 |
Modulus (mm) | 5 |
Pressure angle (°) | 20 |
Tooth width (mm) | 40 |
Shaft hole diameter (mm) | 40 |
Cutter head radius (mm) | 200 |
Number of blades | 4 |
Table 2: Comparison of Machining Methods
Machining Method | Continuous Full – Tooth – Width Machining | Machining Efficiency | Meshing Load |
---|---|---|---|
Hobbing | No | Limited | Prone to occur |
Shaping | No | Limited | Prone to occur |
Plane Helical Cylindrical Gear Machining | Yes | High | Reduced |
7. Images for Illustration
[Insert images of the gear machining process, including the cutter head, tools, and the machined gear. Also include images of the simulation results and the actual machined gear.]
The development of this new type of plane helical cylindrical gear and its machining method provides a new approach for improving the machining efficiency and performance of cylindrical gears, with potential applications in various mechanical transmission systems.
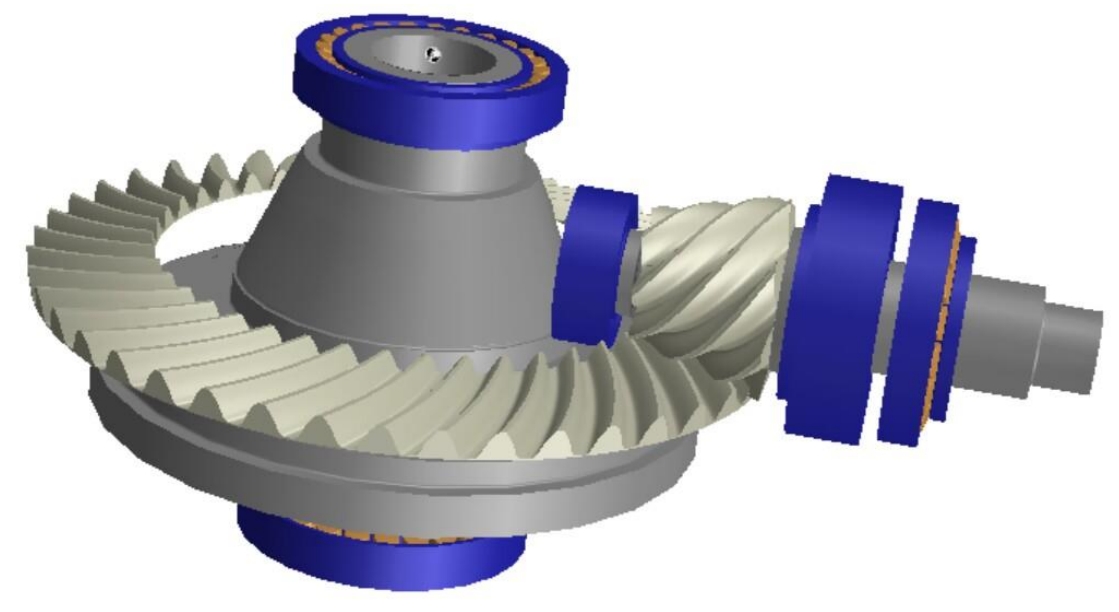