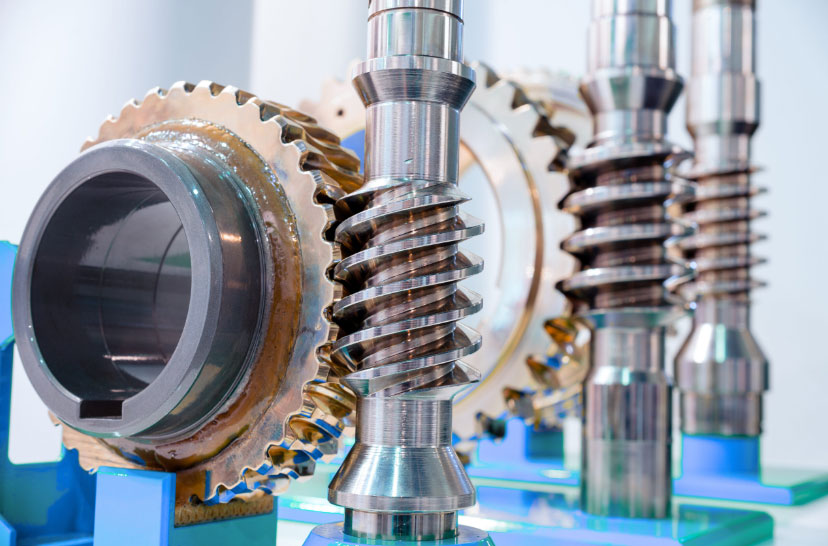
Reducing noise and vibration in high-performance worm gear systems is crucial for improving performance, extending lifespan, and ensuring smooth operation. Here are several strategies that can be employed:
1. Material Selection and Coatings
Materials:
- Advanced Composites: Utilizing advanced composite materials can help in dampening vibrations and reducing noise.
- Alloy Steels: High-quality alloy steels with excellent mechanical properties and wear resistance can also contribute to quieter operation.
Coatings:
- Diamond-Like Carbon (DLC) Coatings: These coatings provide a hard, smooth surface that reduces friction and wear, which can lead to lower noise levels.
- Molybdenum Disulfide (MoS₂) Coatings: These coatings can reduce friction and enhance lubrication properties, thereby minimizing noise and vibration.
2. Design Optimization
Tooth Geometry:
- Modified Tooth Profiles: Optimizing the tooth profile, such as using a slightly modified involute shape, can help in reducing meshing noise.
- Helical Teeth: Using helical teeth instead of straight teeth can provide a smoother engagement and lower noise levels.
Load Distribution:
- Even Load Distribution: Ensuring even load distribution across worm gear teeth can reduce localized stress and vibration.
- Contact Ratio: Increasing the contact ratio (the number of teeth in contact) can lead to smoother power transmission and reduced noise.
3. Lubrication
Lubricants:
- High-Performance Synthetic Oils: These oils can provide better lubrication and reduce friction, leading to quieter operation.
- Solid Lubricants: Incorporating solid lubricants such as graphite or PTFE in worm gear material can enhance lubrication and reduce noise.
4. Precision Manufacturing
Gear Accuracy:
- High Precision Machining: Utilizing high precision machining techniques to ensure tight tolerances and accurate worm gear profiles can minimize deviations that cause noise.
- Surface Finish: Achieving a high-quality surface finish on worm gear teeth can reduce friction and vibration.
5. Dynamic Balancing
Balancing:
- Dynamic Balancing of Components: Ensuring that all rotating components are dynamically balanced can minimize vibrations.
- Vibration Damping Materials: Using vibration damping materials in the housing or mounting structures can absorb vibrations.
6. Structural Design
Housing Design:
- Stiff Housing: A rigid and well-designed housing can prevent resonance and reduce noise.
- Isolation Mounts: Using vibration isolation mounts can decouple worm gear system from the structure, reducing transmitted noise.
7. Advanced Technologies
Active Vibration Control:
- Active Vibration Control Systems: Implementing active vibration control systems that use sensors and actuators to counteract vibrations in real-time can be very effective.
- Condition Monitoring: Utilizing condition monitoring systems to detect and address any anomalies before they lead to significant noise issues.
Research and Development
Staying abreast of the latest research in noise and vibration reduction technologies for worm gear systems can also provide new insights and methods. This includes exploring new materials, manufacturing techniques, and computational methods for simulating and optimizing worm gear performance.
Conclusion
Implementing a combination of these strategies can significantly reduce noise and vibration in high-performance worm gear systems, leading to smoother, quieter, and more efficient operation. Each application may require a tailored approach depending on specific requirements and operating conditions.