Abstract:
This study investigates the impact of high linear velocity on the oil injection lubrication flow field and temperature field in spiral bevel gears commonly used in aeronautical applications. A thermal-fluid coupling analysis model is developed to explore the behavior of spiral bevel gears operating at velocities up to 160 m/s. Results indicate a significant reduction in lubrication effectiveness as velocity increases, leading to excessive temperature rise and potential gear failure. The study highlights the key challenges and provides insights into the design and optimization of lubrication systems for high-speed spiral bevel gears.
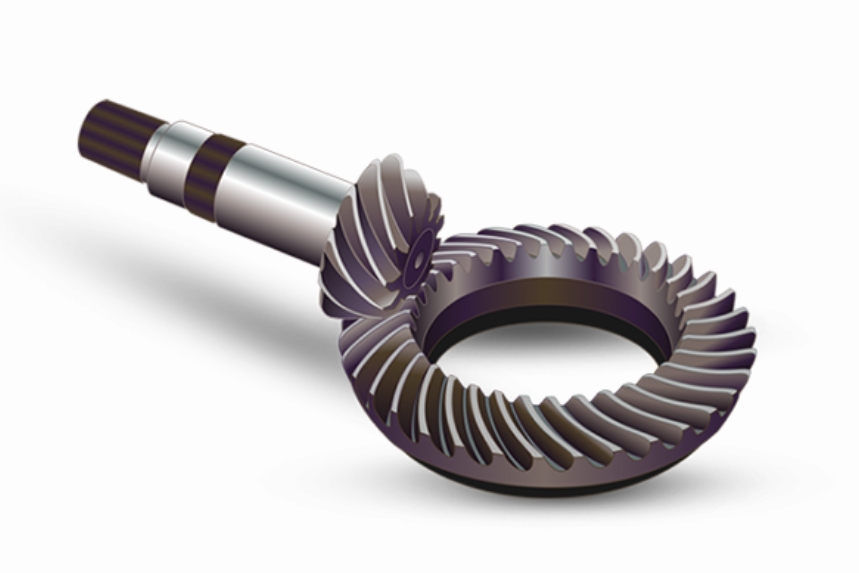
1. Introduction
Spiral bevel gears are widely used in aeronautical applications due to their high load-carrying capacity and transmission stability. However, under high-speed conditions, where linear velocities can exceed 100 m/s, the lubrication of these gears becomes increasingly challenging. Reliable lubrication is crucial to prevent gear scuffing, pitting, and excessive wear, which can significantly reduce gear life and impact aircraft performance.
Traditional methods for estimating oil requirements in spiral bevel gears rely on empirical formulas that do not fully account for the complex interplay between gear speed, oil spray velocity, and spray angle. This study aims to address this gap by developing a thermal-fluid coupling model to analyze the flow field and temperature field of spiral bevel gears operating at high velocities.
2. Literature Review
Spiral bevel gears are subject to high contact pressures and rotational speeds, leading to increased risks of gear scuffing and pitting. Previous studies have primarily focused on cylindrical gears due to their simpler geometry and lower velocities. For example, Liu et al. [1] utilized CFD to analyze the lubrication flow field in FZG gearboxes and validated their results with high-speed camera imagery. Similarly, Hildebrand et al. [2] studied the influence of baffles on the oil flow in a gear stage under splash lubrication conditions.
However, these studies do not fully capture the complexities of spiral bevel gear lubrication at high velocities. High-speed operation of spiral bevel gears results in phenomena such as jet breakup, windage losses, and abnormal temperature distributions, which have not been comprehensively investigated. This study aims to bridge this gap by analyzing the lubrication flow field and temperature field in spiral bevel gears up to 160 m/s.
3. Methodology
3.1 Model Development
A thermal-fluid coupling model was developed using the finite volume method (FVM) in ANSYS Fluent. The model consists of two main components: a flow field simulation module and a temperature field simulation module. The flow field module calculates parameters such as oil volume fraction, wall heat transfer coefficient, and windage loss, while the temperature field module determines the steady-state temperature distribution based on the heat sources and dissipation channels identified in the flow field analysis.
3.2 Geometric and Operating Conditions
The spiral bevel gear pair used in this study is from an aeroengine accessory gearbox, with a rated power of 223.5 kW and a pinion speed of up to 13800.85 r/min (equivalent to a linear velocity of 91.70 m/s at the pitch circle). The geometric parameters of the gear pair are summarized in Table 1.
Table 1: Geometric Parameters of the Spiral Bevel Gear Pair
Parameter | Pinion Gear | Gear |
---|---|---|
Number of teeth | 32 | 43 |
Normal module (mm) | 3.25 | 3.25 |
Face width (mm) | 17 | 17 |
Helix angle (°) | 35 (right) | 35 (left) |
Pressure angle (°) | 20 | 20 |
Pitch angle (°) | 36.7, 53.3 |
The oil spray system utilizes a 3 mm nozzle positioned 106.3 mm from the gear mesh plane, spraying oil at 20 m/s perpendicular to the gear faces. The oil used is 4106 aviation lubricant at 140°C, with physical properties detailed in Table 2.
Table 2: Physical Properties of 4106 Aviation Lubricant at 140°C
Property | Value |
---|---|
Viscosity (mm²/s) | 2.6 |
Density (kg/m³) | 682.79 |
Thermal conductivity (W/m·K) | 0.1331 |
Specific heat capacity (J/kg·K) | 2280 |
3.3 Meshing and Boundary Conditions
A multi-region grid was generated to ensure high resolution in critical areas such as the oil spray and gear mesh regions. The mesh was refined to ensure that cell sizes were smaller than 1.5 mm to prevent oil distribution distortions. A dynamic mesh was implemented to simulate gear rotation, with a time step of 1000 steps per gear revolution.
Boundary conditions included a pressure outlet with a pressure difference of 2 bar to simulate the oil extraction system. The VOF (Volume of Fluid) model was used to simulate the oil-air mixture, with air as the primary phase and oil as the secondary phase. The RNG k-ε turbulence model was employed to accurately capture flow dynamics under high rotational speeds.
4. Results and Discussion
4.1 Flow Field Analysis
At low velocities (40 m/s), the oil spray maintains its integrity and effectively lubricates the gear teeth. However, as velocity increases to 160 m/s, the oil jet breaks up and deflects away from the gear mesh, leading to insufficient lubrication .
- (a) 40 m/s
- (b) 160 m/s
The average oil volume fraction on the gear surface decreases significantly from 0.01275 at 40 m/s to 0.002085 at 160 m/s, a drop of 83.5%. This reduction in lubrication effectiveness is further evidenced by the decrease in the convective heat transfer coefficient in the meshing zone above 120 m/s.
4.2 Windage Loss Analysis
Windage loss increases exponentially with velocity, becoming the primary source of power loss above 80 m/s. At 160 m/s, windage loss accounts for over 80% of the total power loss, significantly impacting gear efficiency.
4.3 Temperature Field Analysis
The steady-state temperature distribution of the gear pair at 40 m/s and 160 m/s. The maximum gear temperature increases from 169.7°C at 40 m/s to 293.7°C at 160 m/s, indicating a significant risk of thermal failure at higher velocities.
- (a) 40 m/s
- (b) 160 m/s
The temperature difference between the hottest and coldest points on the gears also increases with velocity, leading to increased thermal stresses and potential deformation.
5. Conclusion
This study investigated the impact of high linear velocities on the oil injection lubrication flow field and temperature field in spiral bevel gears. Key findings include:
- As velocity increases from 40 m/s to 160 m/s, the oil jet breaks up and deflects, leading to an 83.5% decrease in the average oil volume fraction on the gear surface.
- Windage loss increases exponentially with velocity, becoming the primary source of power loss above 80 m/s.
- The maximum gear temperature increases from 169.7°C to 293.7°C as velocity increases, significantly increasing the risk of thermal failure.
- The temperature difference between the hottest and coldest points on the gears also increases with velocity, leading to increased thermal stresses and deformation.
These findings highlight the need for advanced lubrication systems and optimized gear geometries to ensure reliable operation of spiral bevel gears at high speeds. Future work will focus on developing adaptive lubrication strategies and optimizing gear designs to mitigate the challenges identified in this study.