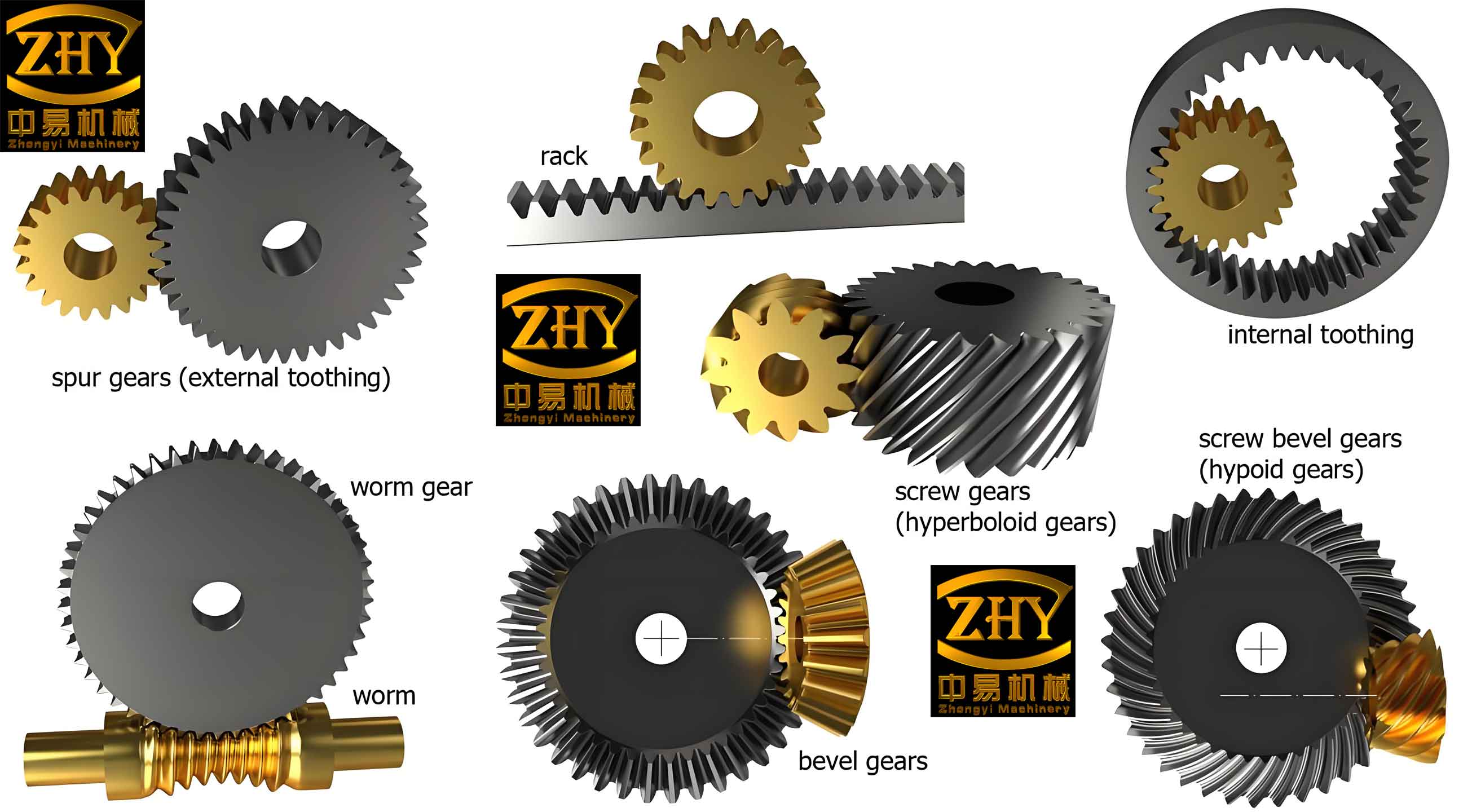
Introduction
Noise in spur gear mechanisms is a significant concern in high-performance applications, where the demand for smooth and quiet operation is paramount. Excessive noise not only reduces the efficiency and lifespan of gear systems but also contributes to acoustic pollution. This article explores various strategies for reducing noise in high-performance spur gear mechanisms, including design modifications, material selection, lubrication techniques, and advanced manufacturing processes.
Sources of Noise in Spur Gear Mechanisms
Understanding the primary sources of noise in spur gear mechanisms is essential for effective noise reduction. Noise in spur gear is primarily generated due to spur gear mesh vibration, misalignment, and surface roughness.
Gear Mesh Vibration
Gear mesh vibration occurs due to the dynamic forces generated during spur gear tooth engagement and disengagement. Variations in spur gear tooth stiffness and manufacturing inaccuracies contribute to this vibration.
Misalignment
Misalignment between spur gear shafts leads to uneven load distribution across spur gear teeth, causing noise and vibration. This can result from improper installation, bearing wear, or thermal expansion.
Surface Roughness
Surface roughness of spur gear teeth increases friction during spur gear operation, leading to noise. Manufacturing processes and wear can contribute to increased surface roughness.
Table 1: Sources of Noise in Spur Gear Mechanisms
Source | Description | Impact on Noise Level |
---|---|---|
Gear Mesh Vibration | Dynamic forces during tooth engagement/disengagement | High |
Misalignment | Uneven load distribution due to shaft misalignment | Moderate |
Surface Roughness | Increased friction from rough gear tooth surfaces | Moderate |
Design Modifications
Design modifications are a primary strategy for reducing noise in spur gear mechanisms. These include optimizing gear geometry, using helical gears, and employing profile modifications.
Optimizing Gear Geometry
Optimizing spur gear geometry involves selecting the appropriate module, pressure angle, and face width. These parameters influence the load distribution and contact ratio, affecting noise generation.
Using Helical Gears
Helical gears, with their angled teeth, provide smoother and quieter operation compared to spur gears. The gradual engagement of teeth in helical gears reduces vibration and noise.
Profile Modifications
Profile modifications such as tip relief and crowning can reduce gear noise by minimizing the effects of manufacturing errors and load concentrations. These modifications help achieve a more uniform load distribution across the gear teeth.
Table 2: Design Modifications for Noise Reduction
Modification | Description | Noise Reduction Effectiveness |
---|---|---|
Optimizing Geometry | Adjusting module, pressure angle, face width | High |
Using Helical Gears | Employing gears with angled teeth | Very High |
Profile Modifications | Applying tip relief, crowning | Moderate |
Material Selection
Selecting the appropriate material for gears can significantly impact noise levels. Materials with high damping properties absorb vibrations, reducing noise.
High-Damping Materials
Materials such as composite polymers and certain alloys exhibit high damping properties. These materials absorb vibrations more effectively than traditional steel gears, leading to quieter operation.
Surface Treatments
Surface treatments such as shot peening and nitriding can enhance the surface properties of gears, reducing noise. Shot peening introduces compressive stresses that improve surface smoothness, while nitriding increases surface hardness and reduces friction.
Table 3: Material Selection and Treatments for Noise Reduction
Material/Treatment | Description | Noise Reduction Effectiveness |
---|---|---|
High-Damping Materials | Composite polymers, specific alloys | High |
Shot Peening | Introducing compressive stresses | Moderate |
Nitriding | Increasing surface hardness, reducing friction | Moderate |
Lubrication Techniques
Effective lubrication reduces friction and noise in spur gear mechanisms. Lubricants with high viscosity and good film-forming properties are particularly effective in noise reduction.
High-Viscosity Lubricants
High-viscosity lubricants provide a thicker film between gear teeth, reducing direct metal-to-metal contact and subsequent noise.
Additives
Lubricants with additives such as extreme pressure (EP) and anti-wear (AW) agents improve film strength and reduce friction, leading to quieter gear operation.
Table 4: Lubrication Techniques for Noise Reduction
Lubrication Technique | Description | Noise Reduction Effectiveness |
---|---|---|
High-Viscosity Lubricants | Thicker lubricant film reduces metal-to-metal contact | High |
Additives | EP and AW agents enhance lubricant performance | Moderate |
Advanced Manufacturing Processes
Advanced manufacturing processes can produce spur gear with higher precision and smoother surfaces, reducing noise generation.
Precision Grinding
Precision grinding is a finishing process that produces spur gear with high dimensional accuracy and surface smoothness. This reduces the noise generated by surface roughness and manufacturing errors.
Gear Honing
Gear honing is a process that improves gear tooth surface finish and accuracy. It reduces the amplitude of surface roughness, leading to quieter gear operation.
Table 5: Advanced Manufacturing Processes for Noise Reduction
Manufacturing Process | Description | Noise Reduction Effectiveness |
---|---|---|
Precision Grinding | High dimensional accuracy, smooth surfaces | High |
Gear Honing | Improved surface finish and accuracy | Moderate |
Case Studies
Case Study 1: Automotive Gearbox
An automotive gearbox manufacturer implemented helical gears and precision grinding to reduce noise. The result was a significant reduction in gear noise, improving overall vehicle comfort.
Case Study 2: Industrial Machinery
An industrial machinery company used high-viscosity lubricants with EP additives to reduce noise in their gear systems. The improved lubrication led to quieter operation and increased gear life.
Table 6: Case Study Results
Case Study | Strategy Implemented | Key Improvements |
---|---|---|
Automotive Gearbox | Helical gears, precision grinding | Reduced noise, improved comfort |
Industrial Machinery | High-viscosity lubricants with EP additives | Quieter operation, increased gear life |
Conclusion
Reducing noise in high-performance spur gear mechanisms requires a comprehensive approach, including design modifications, material selection, effective lubrication, and advanced manufacturing processes. By addressing the primary sources of noise and implementing these strategies, engineers can significantly improve the performance and longevity of spur gear systems. The case studies demonstrate the practical application of these strategies, leading to quieter and more efficient spur gear mechanisms.