Bevel gears play a crucial role in the transmission system of automobiles. They are responsible for reducing the speed, increasing the torque, and changing the direction of torque rotation. In this article, we will focus on the analysis of the abnormal failure fracture of the active bevel gear, which is an important transmission component in the system.
1. Introduction
The main reducer in the automotive transmission system serves to lower the rotational speed, increase the torque, and simultaneously change the direction of torque rotation. It consists of one or several pairs of reduction gear pairs. The reduction is achieved by the gear with fewer teeth driving the gear with more teeth. The conical gear transmission is used to change the direction of torque rotation. The active bevel gear is an essential transmission component in this part of the system. It inputs power and transmits it to the driven gear to control the steering system of the automobile, adjust the linear speed of the inner and outer wheels, and thus achieve smooth turning of the automobile wheels.
The processing technology of the bevel gear is as follows: blanking -> hot forging -> normalizing (pre-heat treatment) -> rough machining -> finish machining -> carburizing and quenching -> tempering -> fine grinding to form [1]. The pre-heat treatment can eliminate the uneven distribution of the austenite structure, eliminate the stress generated during the forging process, reduce the chance of cracks, improve the cutting performance, and prepare for the final quenching and tempering heat treatment [2 – 3].
The automotive main reducer gear studied in this article experienced abnormal fracture before reaching the normal service life. The design standard of this component requires a surface effective hardening layer depth of 0.8 – 1.1 mm and a surface hardness of 32 – 48HRC for the matrix hardness. Therefore, a comprehensive analysis and detection were conducted to provide some theoretical guidance for later production.
2. Analysis and Detection
2.1 Macroscopic Observation
Most of the teeth of the active bevel gear were fractured, and macroscopic cracks had also appeared at the root of the unbroken teeth. By observing the fracture surface, obvious crack propagation traces of the Bellini lines could be found on two of the broken teeth, indicating low-cycle fatigue [4] fracture. Figure 1 shows the physical image of the active bevel gear.
Figure | Description |
---|---|
1 | Physical image of the broken gear. |
2.2 Chemical Composition
The chemical composition of the tooth surface layer was determined using a direct reading spectrometer. The material of the gear was 20CrMnTiH steel, and the results of the chemical element analysis are shown in Table 1, which meets the requirements for the content of each element in the GB / T 3077 – 2015 “Alloy Structural Steel Standard”.
Table | Composition | Content (mass fraction) |
---|---|---|
1 | Chemical composition of the bevel gear | C: 0.22, Mn: 0.65, P: 0.015, Cr: 1.06, Ti: 0.056, Cu: 0.058, Ni: 0.029, Si: 0.33 |
2.3 Hardness Test
Samples were taken from the residual tooth surface and the interior of the matrix, and the Rockwell hardness of each part was measured respectively. The test results are shown in Table 2. The detected value of the matrix is close to the lower limit of the design requirement. The average hardness value of the gear surface is lower than the design requirement, and the hardness is uneven. The gradient of the hardness difference value on the surface is large, indicating the presence of abnormal tissue on the surface, and the inhomogeneity of the tissue causes the difference in hardness.
Table | Hardness | Values |
---|---|---|
2 | Hardness test of the bevel gear (HRC) | Surface: 53.3, 58.9, 59.2, 54.1, Mean: 56.4; Matrix: 32.7, 32.3, 33.2, 32.1, Mean: 32.6 |
2.4 Determination of the Depth of the Surface Effective Carburizing Hardening Layer
Samples were taken at three positions on the surface layer, and the average depth of the surface effective hardening layer of the gear was measured using a micro Vickers hardness tester to be 0.86 mm (required: 0.8 – 1.1 mm. The hardness limit value is based on the standard (GB / T 9450 – 2005 “Determination and Verification of the Depth of the Carburizing and Quenching Hardening Layer of Steel Parts”)). The measurement result exceeds the required minimum value and meets the design requirements.
2.5 Metallographic Analysis
Metallographic samples were prepared at the broken teeth, and after rough grinding, fine grinding, polishing, and observation under a metallographic microscope, no obvious non-metallic inclusions were found in the vicinity of the fracture and the matrix, only a small amount of spherical oxides were present, all below grade 1, as shown in Figure 2. Therefore, it is not the main reason for the gear fracture.
Figure | Description |
---|---|
2 | Spherical oxides. |
After the polished sample was etched with 4% nitric acid alcohol, washed, dried, and microscopically observed, the microstructure of the surface carburizing hardening layer of the unbroken gear was fine needle martensite + a small amount of residual austenite [5], as shown in Figure 3. Its microstructure belongs to the normal product after quenching; the microstructure of the core is lath-shaped bainite + sorbite, as shown in Figure 4. This structure will lead to a reduction in the bending strength of the gear [6 – 7]. However, considering its location at the core and not the main stress-bearing part, it has little impact on the gear fracture.
Figure | Description |
---|---|
3 | Surface microstructure. |
4 | Matrixic phase. |
There is a network-like non-martensitic structure on the surface of the broken gear root, and the depth of the test is about 0.04 mm. After carburizing and carbonitriding, the ideal structure on the surface of the quenched part should be fine needle-like high-carbon martensite. However, due to many uncontrollable factors in the heat treatment process and processing technology, some non-martensitic mixed structures such as bainite and troostite (pearlitic type) are formed on the gear surface, resulting in serious quality defects. If the depth of the non-martensitic structure exceeds the standard seriously, the surface hardness of the part will be low in mechanical properties, affecting the hardness gradient and resulting in uneven test hardness.
Figure | Description |
---|---|
5 | Superficial non-equine microstructure (shallow etching). |
The presence of non-martensitic structure at the root of the gear tooth is regulated by the national automotive industry standard QC / T 262 – 1999 “Metallographic Inspection of Automotive Carburized Gears”, which stipulates that the deepest non-martensitic structure on the gear surface shall not exceed 0.02 mm. The surface non-martensitic depth of this gear is 0.04 mm and penetrates along the original austenite grain boundary in a network-like manner [8]. The deeper non-martensitic structure seriously reduces the surface hardness and wear resistance of the gear, as well as the fatigue limit [9]. Fine cracks are initiated from the grain boundary or the stress concentration area of the oxide, forming a crack source, causing the gear to fracture due to insufficient bending strength during later service meshing.
3. Discussion of the Detection Results
The gear surface has a deeper non-martensitic structure that penetrates along the original austenite grain boundary in a network-like manner. This structure severely weakens the strength of the gear surface and grain boundary, reduces the wear resistance and fatigue life of the gear (under the same applied force, the early initiation of the crack source or the accumulated degree of crack damage will mostly reduce the fatigue coefficient of the gear, thereby reducing the fatigue limit life). The presence of the non-martensitic structure first causes uneven surface hardness of the gear, making it prone to stress concentration during service, resulting in the emergence of fatigue crack sources. The continued expansion of multiple crack sources eventually leads to gear fracture, greatly shortening the fatigue life of the gear, which is the main reason for the gear failure and fracture [10].
4. Improvement Measures and Effects
There are two main ways to address the source of the non-martensitic structure: one is to minimize the elements that are preferentially selectively oxidized during material selection. The order of preferential oxidation of different elements is C > Ce > Ba > Mg > Al > Ti > Si > B > V > Nb > Mn > Cr > Cd > Fe > P > Mo > Sn > Ni > As > Cu). The second is to reduce the oxidizing components of the carburizing atmosphere (such as reducing the oxygen partial pressure, etc.). To address the current issues with domestic gears, the second option is more readily accepted by manufacturers.
Specific measures are as follows: (1) The presence of the non-martensitic structure indicates the presence of an oxidizing atmosphere in the heat treatment furnace. The cleanliness of the carburizing atmosphere in the furnace should be improved, and the sealing of the heat treatment furnace should be strictly controlled. The exhaust time of the heat treatment furnace can be appropriately extended to make the carburizing atmosphere in the furnace purer. (2) The overall hardness of the surface layer of this failed gear is relatively low. Appropriately increasing the surface hardness can improve the contact fatigue strength of the tooth surface. Ensure the cleanliness of the workpiece surface before carburizing to improve the surface hardness and uniformity. (3) During the carburizing process, due to the higher carbon potential at the tooth root and the slower cooling rate compared to other parts, non-martensitic structure is prone to form at the tooth root. It is necessary to appropriately increase the quenching cooling rate of the gear to achieve the goal of reducing or eliminating this defect.
5. Conclusion
Based on the improvement suggestions, the heat treatment process was adjusted (including the oxidizing atmosphere and quenching cooling process), and sampling and observation were conducted on the new batch of gears. No obvious network-like surface non-martensitic structure was found. Completely eliminating this structure requires high requirements for the material and heat treatment process. The adjustment of the process has greatly improved the organizational defects on the surface layer of the gear. From the final analysis results and the improved effect, it can be seen that the analysis method in this article is highly effective and can provide certain guidance for the processing technology of the gear.
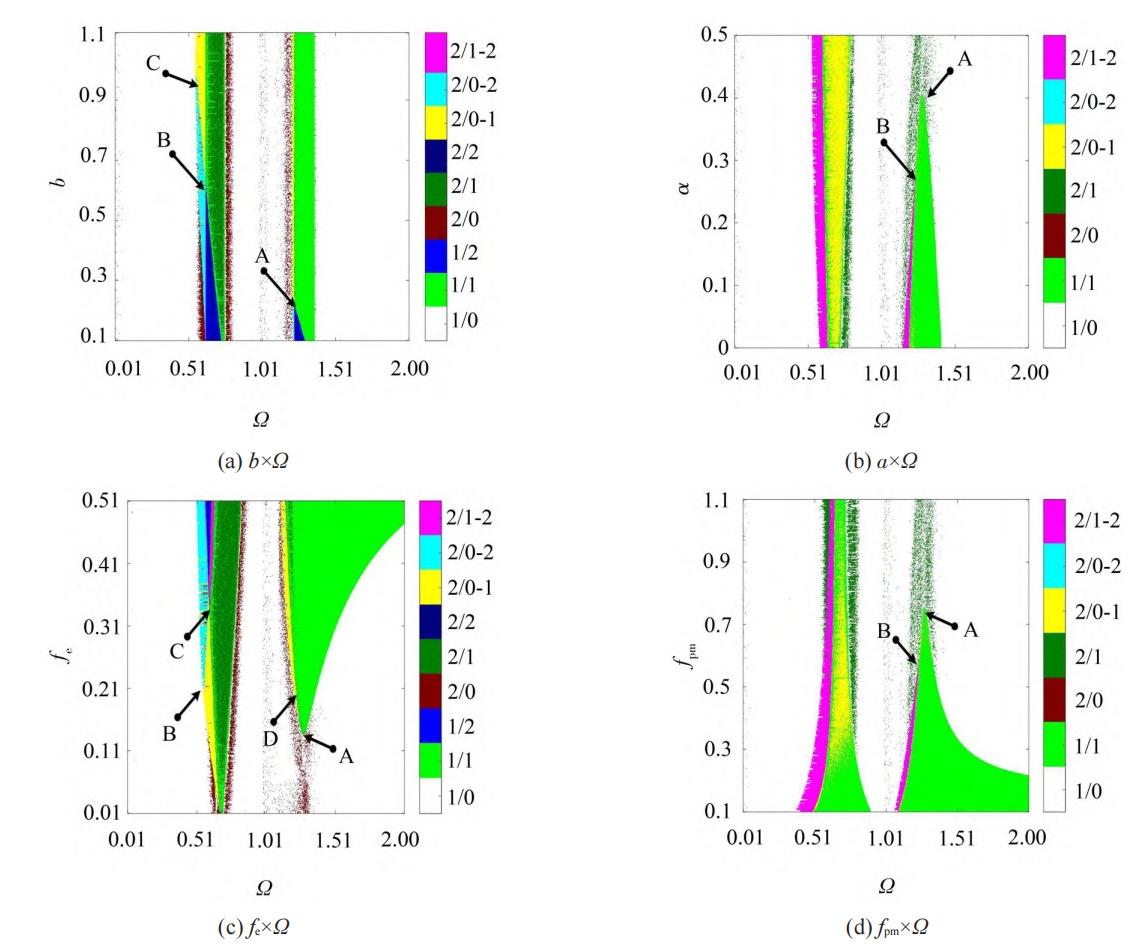