Reducing noise in spur gear systems is crucial for improving overall system performance, especially in applications like automotive transmissions and industrial machinery. Several strategies can be employed to address this issue:
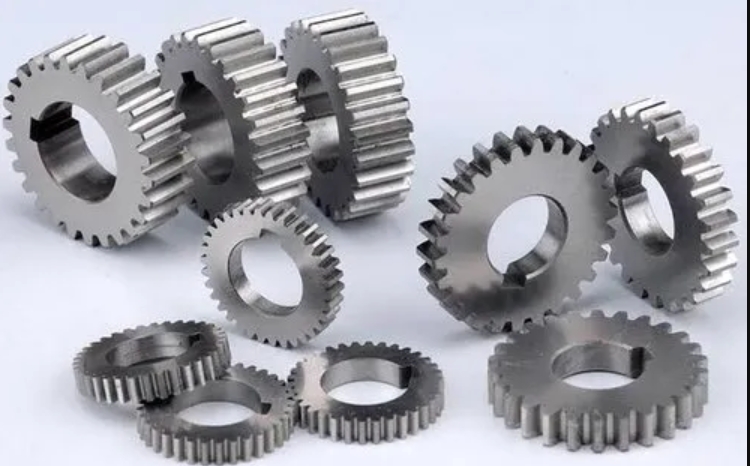
- Precision Manufacturing: Ensuring high precision in the manufacturing process reduces spur gear meshing inaccuracies, which are a common cause of noise. This includes maintaining tight tolerances on tooth geometry, pitch, and surface finish.
- Material Selection and Treatment: Using materials with good damping properties can reduce noise. Materials like polymers, composites, or metals with specific heat treatments can absorb vibrations better than conventional spur gear materials.
- Gear Tooth Profile Modification: Modifying the tooth profile can significantly reduce noise. Techniques like crowning or helical gear design allow for a more gradual engagement of spur gear teeth, which reduces impact and the resultant noise.
- Proper Lubrication: Adequate lubrication reduces friction between gear teeth, which can minimize noise. The use of specially formulated gear oils can also dampen sound and reduce wear.
- Dynamic Balancing: Ensuring that spur gears and associated rotating parts are dynamically balanced minimizes vibration, which is a key contributor to noise.
- Damping Techniques: Incorporating damping materials or mechanisms within spur gear system can absorb vibrations. This can include the use of vibration dampers, sound-absorbing materials around spur gear casing, or even integrating damping elements into spur gear structure.
- Isolation and Enclosure: Isolating spur gear system from other parts of the machinery and using enclosures can prevent the transmission of sound. Enclosures can be designed with sound-absorbing materials to further enhance noise reduction.
- Optimized Gear Meshing: Ensuring optimal alignment and spacing of spur gear reduces the likelihood of misalignment and uneven load distribution, both of which can cause excessive noise.
- Use of Helical Gears: While not spur gear, helical gear offer a smoother and quieter operation due to the angled teeth and continuous contact during gear rotation. They can sometimes be used as an alternative to spur gear in noise-sensitive applications.
- Controlled Load Distribution: Evenly distributing the load across spur gear face can prevent localized stress and the associated noise. This can be achieved through careful design and alignment of spur gear system.
- Noise Analysis Tools: Utilizing advanced software and noise analysis tools to simulate and analyze gear noise can help in identifying and mitigating potential noise issues during the design phase.
By implementing these strategies, engineers can significantly reduce noise levels in spur gear systems, leading to quieter operation, increased lifespan of spur gear system, and greater overall efficiency. Each approach has its own set of considerations and costs, and the optimal solution often involves a combination of several techniques, tailored to the specific requirements of the application.