1. Introduction
In the aerospace industry, the efficient operation of components is crucial for the overall performance and safety of aircraft. The circular arc oscillating internal gear pump is a vital part in many aerospace systems, especially in the lubrication and fuel delivery processes. However, the presence of gas – liquid two – phase flow in these pumps, due to factors such as gas release from lubricating oil after it has fulfilled its cooling and lubricating functions in the engine, often leads to a decrease in the pump’s volumetric efficiency. This reduction in efficiency not only affects the performance of the pump itself but also has implications for the entire aircraft system’s energy consumption and reliability.
Previous studies on the volumetric efficiency of gear pumps can be divided into two main categories: those focused on circular arc oscillating internal gear pumps and those on external gear pumps. For circular arc oscillating internal gear pumps, researchers have explored aspects such as flow characteristics and the impact of different structural parameters on volumetric efficiency under single – phase conditions. For example, Zhang et al. studied the flow characteristics and volumetric efficiency variation within a certain speed range through numerical calculations. Shen Dongping used dynamic grid technology to obtain the flow rate and volumetric efficiency change curves of a vehicle – used circular arc oscillating internal gear pump under different working conditions. However, the research on the influence of different working conditions and structures on the volumetric efficiency under gas – liquid two – phase conditions is relatively limited.
Regarding external gear pumps, scholars have carried out in – depth research on issues such as flow pulsation and the influence of leakage on volumetric efficiency. Campo Sud analyzed the transient flow change process in external gear pumps and the influencing factors of volumetric efficiency through numerical simulation. Kong Fanyu et al. derived the calculation formula for the flow pulsation coefficient of external gear pumps and studied the impact of gear parameters on flow pulsation.
This paper aims to fill the gap in the research on circular arc oscillating internal gear pumps under gas – liquid two – phase conditions. By using the computational fluid dynamics software Pumplinx, it comprehensively analyzes the influence of various factors such as different rotational speeds, end clearances, rotor stages, and rotor thicknesses on the volumetric efficiency of the pump. The research results can provide a theoretical basis for the design and optimization of circular arc oscillating internal gear pumps in aerospace applications, helping to improve their performance and reliability.
2. Numerical Calculation Method
2.1 Control Equations
The gas – liquid two – phase flow in the circular arc oscillating internal gear pump is treated as a homogeneous medium, assuming no relative velocity between the phases and the same velocity and pressure for each component. The control equations for the oil – liquid flow inside the pump are as follows:
- Continuity Equation: \(\frac{\partial \rho_{m}}{\partial t}+\nabla \cdot\left(\rho_{m} \vec{V}\right)=0\)
- Momentum Conservation Equation: \(\frac{\partial\left(\rho_{m} u_{i}\right)}{\partial t}+\frac{\partial\left(\rho_{m} u_{i} u_{j}\right)}{\partial x_{j}}=-\frac{\partial p}{\partial x_{i}}+\frac{\partial}{\partial x_{j}}\left(\mu_{m} \frac{\partial u_{i}}{\partial x_{j}}\right)\) where \(u_{i}\) represents the velocity in the \(i(i = 1,2,3)\) direction, p is the pressure, \(\rho_{m}\) is the mixed density, and \(\mu_{m}\) is the dynamic viscosity coefficient of the mixed phase. The mixed density \(\rho_{m}\) and dynamic viscosity coefficient \(\mu_{m}\) are calculated as follows: \(\rho_{m}=\rho_{p} \alpha_{p}+\rho_{q} \alpha_{q}\) \(\mu_{m}=\mu_{p} \alpha_{p}+\mu_{q} \alpha_{q}\) Here, \(\alpha\) is the volume fraction, and the subscripts p and q represent the gas phase and liquid phase respectively.
2.2 Two – Phase Flow VOF Model
Accurately representing the two – phase interface is essential for simulating gas – liquid two – phase flow. The Volume of Fluid (VOF) model is selected in this study. This model is based on a fixed Eulerian grid system and tracks the two – phase interface by using the phase volume fraction in the grid cells. In each grid cell, the sum of the volume fractions of all phases is 1, that is \(\sum_{i = 1}^{n} \alpha_{q i}=1\), where q represents the gas phase and \(\alpha_{q i}\) is the volume fraction of the gas phase. If \(\alpha_{q i}=0\), the grid cell is completely filled with the liquid phase; if \(\alpha_{q i}=1\), it is completely filled with the gas phase; if \(0<\alpha_{q i}<1\), the grid cell is in a two – phase mixing position, and the interface between the two phases can be determined accordingly.
2.3 Turbulence Model
The internal flow of the circular arc oscillating internal gear pump is usually in a turbulent state. The \(k – \varepsilon\) turbulence model based on the Reynolds – averaged method is widely used in engineering fluid calculations due to its simple structure, stable convergence, high accuracy, and excellent universality. The equations for the turbulent kinetic energy k and the dissipation rate \(\varepsilon\) are as follows:
- Turbulent Kinetic Energy Equation k: \(\frac{\partial(\rho k)}{\partial t}+\frac{\partial\left(\rho k \overline{u_{j}}\right)}{\partial x_{j}}=\frac{\partial}{\partial x_{j}}\left[\left(\mu_{m}+\frac{\mu_{t}}{\sigma_{k}}\right) \frac{\partial k}{\partial x_{j}}\right]+P_{t}-\rho \varepsilon\)
- Diffusion Equation \(\varepsilon\): \(\begin{aligned}\frac{\partial(\rho \varepsilon)}{\partial t}+\frac{\partial\left(\rho \varepsilon \overline{u_{j}}\right)}{\partial x_{j}}=\frac{\partial}{\partial x_{j}}\left[\left(\mu_{m}+\frac{\mu_{t}}{\sigma_{k}}\right) \frac{\partial \varepsilon}{\partial x_{j}}\right]+C_{\varepsilon 1} P_{t} \frac{\varepsilon}{k}-C_{\varepsilon 2} \rho \frac{\varepsilon^{2}}{k}\end{aligned}\) where \(\mu_{m}\) is the viscosity of the gas – liquid mixed phase, \(\mu_{t}=\rho C_{\mu} \frac{k^{2}}{\varepsilon}\) is the turbulent eddy viscosity, and \(P_{t}\) is the turbulent kinetic energy generation term.
2.4 Calculation Model and Boundary Conditions
A certain type of circular arc oscillating internal gear pump used in aircraft lubricating oil return pumps is selected as the research object. The pump mainly consists of internal and external rotors, front and rear end covers, an eccentric sleeve, and a pump housing. The number of teeth of the internal and external rotors is 4 and 5 respectively, the rotor thickness is 13 mm, the diameter of the inlet port is 48 mm, and the diameter of the outlet port is 40 mm.
The three – dimensional model of the flow channel calculation domain of the circular arc oscillating internal gear pump is obtained through Boolean operations. The calculation domain model retains the geometric details of the flow channel of the pump to the greatest extent. The inlet and outlet section flow channels are stationary domains, and the flow channel between the internal and external teeth is a rotating domain, as shown in Figure 1.
Figure 1 | Computational domain 3D model |
---|---|
[Insert a clear image of the computational domain 3D model here, showing the inlet, outlet, and the rotating part clearly] | The inlet and outlet section flow channels are stationary, and the internal – external tooth – gap flow channel is rotating. This structure is crucial for understanding the flow behavior inside the pump. |
2.5 Computational Grid and Calculation Conditions
The software Pumplinx is used to divide the computational grid of the gear pump. The stationary domain is divided by the general grid division module, and the rotating domain is divided by the RTM (roter template mesher) grid division module for dynamic grid division. Considering the non – contact operation between the internal and external rotors and the cavity wall during the pump’s operation, as well as the process and working conditions, the radial clearance is set to 0.07 mm, and the end clearance is set to 0.06 mm.
To determine the appropriate number of grids to meet the calculation accuracy, grid – dependency analysis is carried out with grid numbers of 145181, 200853, 304353, 415537, and 554795. The maximum difference in the numerical simulation results of the lubricating oil flow rate is within 0.5%, and as the total number of grids increases, the numerical simulation results tend to be stable. Considering the simulation duration and the reliability of the results, a grid with a total number of 304353 is selected for subsequent numerical simulations. The computational domain grid is shown in Figure 2.
Figure 2 | Computational domain grid diagram |
---|---|
[Insert an image showing the grid details of the inlet – outlet and internal – external tooth – gap flow channels] | The grid distribution affects the accuracy of the simulation results. A proper grid division can better capture the flow characteristics. |
The SIMPLC algorithm is used to couple the pressure and velocity. The Multiphase model is called, and the gas phase and liquid phase are added. Based on the rotational speed of the internal rotor of the circular arc oscillating internal gear pump, each 1° rotation of the internal rotor is set as one time step. To ensure the accuracy of the analysis, the rotor of the circular arc oscillating internal gear pump is set to rotate for 8 cycles, and the average flow rate at the pump outlet in the last cycle is selected for analysis.
2.6 Definition of Volumetric Efficiency
The displacement of the circular arc oscillating internal gear pump is determined by the change in the working volume formed by the internal and external rotors. When the rotor thickness is constant, the working volume depends on the area enclosed by the internal and external rotors. The theoretical average flow rate expression is defined as: \(Q_{L}=S b z_{1} n_{1}×10^{-3}(L/min)\) where b is the rotor thickness in mm, \(z_{1}\) is the number of teeth of the internal rotor, \(n_{1}\) is the rotational speed of the internal rotor in r/min, and \(S=\pi e(R – r_{w})\) is the maximum area formed by the internal and external rotors in \(mm^{2}\), with e being the eccentricity in mm, R being the generating radius in mm, and \(r_{w}\) being the radius of the external rotor tooth – shaped circle in mm.
The volumetric efficiency is the ratio of the actual flow rate to the theoretical flow rate of the gear pump, which has a significant impact on the volume size of the lubricating oil pump and the energy consumption of the entire engine. In this paper, the volumetric efficiency is used as the performance index of the gear pump. The volumetric efficiency of the circular arc oscillating internal gear pump transporting gas – liquid mixed media under gas – liquid two – phase conditions is defined as: \(\eta_{vm}=\frac{Q_{1}+Q_{g}}{Q_{L}}×100\%\) where \(Q_{1}\) is the calculated flow rate of the liquid in L/min, and \(Q_{g}\) is the calculated flow rate of the gas at the inlet in L/min.
3. Calculation Results and Analysis
3.1 Influence of Rotational Speed on Volumetric Efficiency
Figure 3 shows the change curves of the lubricating oil flow rate \(Q_{1}\) of the circular arc oscillating internal gear pump with the rotor rotational speed under different inlet section oil – volume – fraction (IOVF) conditions. It can be seen that under the same operating conditions, the lubricating oil flow rate of the circular arc oscillating internal gear pump increases with the increase of the rotor rotational speed at different inlet section oil – volume – fractions. However, as the rotational speed increases, the increase in the lubricating oil flow rate caused by the same rotational speed increment becomes less and less obvious. Especially when the oil – volume – fraction is 70%, when the rotational speed increases from 9000 r/min to 10000 r/min, the lubricating oil flow rate hardly increases. This is because when the rotational speed is low, the lubricating oil does not fully fill the cavity between the internal and external rotors. At this time, the increase in the rotational speed leads to an increase in the centrifugal force of the lubricating oil, allowing the oil to better fill the cavity. At the same time, due to the compressibility of the gas, the lubricating oil flow rate increases significantly. When the rotational speed increases, the filling time of the lubricating oil is shortened, and the increase trend of the lubricating oil flow rate gradually becomes less obvious. Especially when the inlet section oil – volume – fraction is high, the volume of the compressible gas is small. When the rotational speed increases to a certain value, the lubricating oil flow rate will reach a threshold. Under the condition that other operating conditions remain unchanged, the ability to pump lubricating oil is limited, and the lubricating oil flow rate of the pump cannot be increased simply by increasing the rotational speed.
Figure 3 | Variation curve of oil flow with rotation speed under different oil content |
---|---|
[Insert a line – graph with rotational speed on the x – axis and lubricating oil flow rate on the y – axis, showing curves for different IOVF values] | The curves clearly show the relationship between rotational speed and lubricating oil flow rate at different IOVF values. |
Figure 4 shows the curves of the volumetric efficiency of the circular arc oscillating internal gear pump transporting lubricating oil with the rotational speed under different inlet section oil – volume – fraction conditions. When the rotational speed is 5000 r/min, the volumetric efficiency of the circular arc oscillating internal gear pump gradually increases with the increase of the inlet section oil – volume – fraction, increasing from 73.83% when the oil – volume – fraction is 30% to 75.76% when the oil – volume – fraction is 70%, and the increase amplitude gradually decreases. When the rotational speed increases, the volumetric efficiency gradually decreases with the increase of the oil – volume – fraction. Moreover, the higher the rotational speed, the more obvious the decrease in the volumetric efficiency when the oil – volume – fraction increases from 30% to 70%, increasing from 5.96% at a rotational speed of 6000 r/min to 27.79% at 10000 r/min.
Figure 4 | Variation curve of volumetric efficiency with rotation speed under different oil content |
---|---|
[Insert a line – graph with rotational speed on the x – axis and volumetric efficiency on the y – axis, showing curves for different IOVF values] | These curves help to understand how rotational speed and IOVF interact to affect volumetric efficiency. |
When the inlet section oil – volume – fraction is small and the rotational speed is low, the increase in the lubricating oil flow rate is greater than the increase in the theoretical flow rate as the rotational speed increases. Therefore, the volumetric efficiency of the circular arc oscillating internal gear pump increases with the increase of the rotational speed. As the rotational speed continues to increase, the difference between the increase in the lubricating oil flow rate and the increase in the theoretical flow rate gradually decreases, and even becomes negative. Thus, when the oil – volume – fraction is low, the volumetric efficiency of the circular arc oscillating internal gear pump first increases and then decreases with the increase of the rotational speed. When the inlet section oil – volume – fraction increases, within the existing rotational speed range, the increase in the lubricating oil flow rate with the increase of the rotational speed is less than the increase in the theoretical flow rate. Therefore, when the oil – volume – fraction is high, the volumetric efficiency of the circular arc oscillating internal gear pump decreases directly with the increase of the rotational speed. For the working conditions with a high inlet section oil – volume – fraction, when the lubricating oil flow rate meets the working requirements, the lower the rotor rotational speed, the more conducive it is to the operation of the entire lubricating oil system.
Table 1 summarizes the volumetric efficiency changes at different rotational speeds and oil – volume – fractions.
Rotational Speed (r/min) | Oil – Volume – Fraction 30% | Oil – Volume – Fraction 40% | Oil – Volume – Fraction 50% | Oil – Volume – Fraction 60% | Oil – Volume – Fraction 70% |
---|---|---|---|---|---|
5000 | 73.83% | – | – | – | 75.76% |
6000 | – | – | – | – | – (5.96% decrease compared to 30% oil – volume – fraction) |
10000 | – | – | – | – | – (27.79% decrease compared to 30% oil – volume – fraction) |
4. Conclusion
This paper takes the high – speed circular arc oscillating internal gear pump for aviation as the research object and uses the valve – pump simulation analysis software Pumplinx to conduct gas – liquid two – phase performance simulation analysis under multiple – structure and multiple – working – condition conditions. The following influence laws of the structure and working – condition parameters of the circular arc oscillating internal gear pump on the pump’s volumetric efficiency under gas – liquid two – phase conditions are obtained:
- Under different inlet section oil – volume – fractions, the lubricating oil flow rate of the circular arc oscillating internal gear pump all increases with the increase of the rotor rotational speed. As the rotational speed increases, the increase in the lubricating oil flow rate caused by the same rotational speed increment becomes less and less obvious. When the inlet section oil – volume – fraction is low, the volumetric efficiency of the circular arc oscillating internal gear pump first increases and then decreases with the increase of the rotor rotational speed. When the inlet section oil – volume – fraction increases, the volumetric efficiency decreases with the increase of the rotor rotational speed. When the oil – volume – fraction is 70%, the maximum decrease in the volumetric efficiency is 27.79%.
- Under different inlet section oil – volume – fractions, the volumetric efficiency of the circular arc oscillating internal gear pump all decreases with the increase of the end clearance. As the oil – volume – fraction increases from 30% to 70%, the volumetric efficiency decreases from 20.42% when the end clearance is 0.06 mm to 15.72% when the end clearance is 0.12 mm.
- When the inlet section oil – volume – fraction is low, the volumetric efficiency of the circular arc oscillating internal gear pump decreases with the increase of the rotor stages. When the inlet section oil – volume – fraction is high, the volumetric efficiency of the circular arc oscillating internal gear pump increases with the increase of the rotor stages. As the oil – volume – fraction increases from 30% to 70%, the decrease in the volumetric efficiency changes from 12.59% when the rotor stage is 1 to 6.51% when the rotor stage is 3.
- Under different inlet section oil – volume – fractions, the volumetric efficiency of the circular arc oscillating internal gear pump all decreases with the increase of the rotor thickness. As the oil – volume – fraction increases from 30% to 70%, the maximum decrease in the volumetric efficiency increases from 12.59% when the rotor thickness is 6.5 mm to 35.51% when the rotor thickness is 19.5 mm.
These research results can provide important theoretical support for the design, optimization, and operation of circular arc oscillating internal gear pumps in the aerospace field, helping to improve the performance and reliability of aircraft lubrication and fuel – delivery systems. Future research can further explore more complex working conditions and multi – physical – field coupling effects to more comprehensively understand the performance of these pumps.
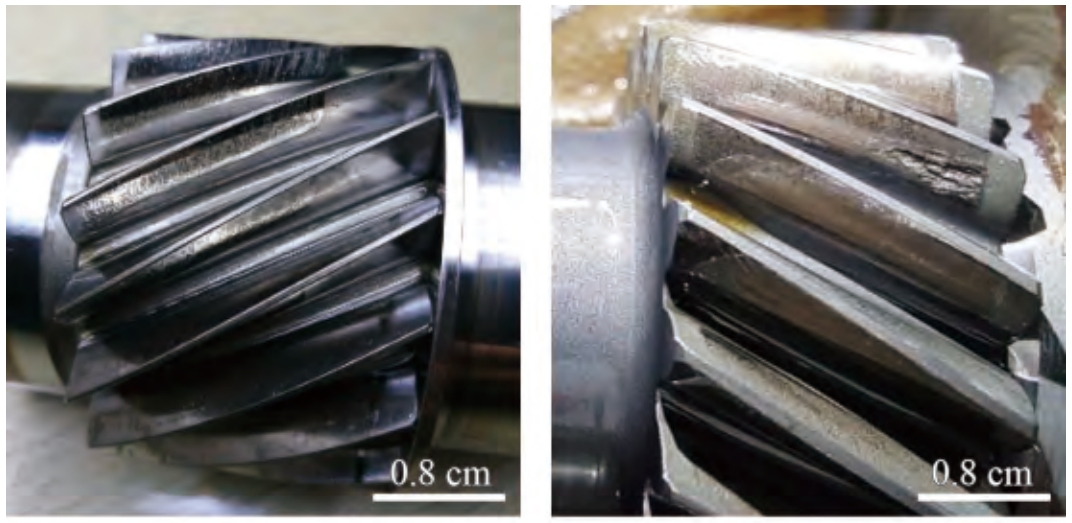