1、 Establishment of geometric model
Using pro/e4.0, the geometric model of extrusion process is established, including the geometric model of upper and lower dies and the geometric model of spiral bevel gear blank. According to the drawings provided by the enterprise, the blank of spiral bevel gear is Φ 40mmx196mm bar stock. Since the upper and lower dies and the blanks of spiral bevel gear are symmetrical, only 1/4 model is taken for research. The established assembly drawing is shown in Figure 1.
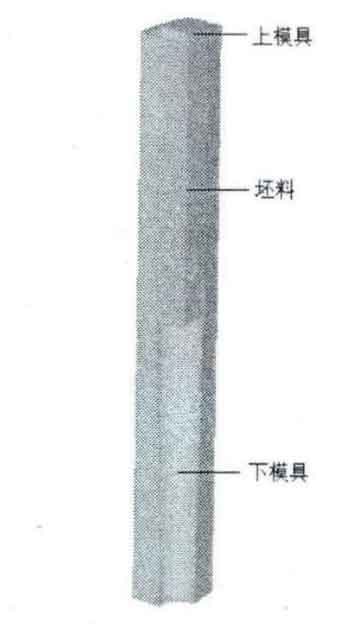
2、 Establishment of finite element model
The geometric model is imported into the Defrom-3D preprocessor in STL format to establish the finite element model.
(1) Meshing
The mesh is divided according to the method introduced. After division, the mesh number of the upper die is 8135, the mesh number of the spiral bevel gear blank is 109021, and the mesh number of the lower die is 110174.
(2) Basic attribute settings of blank and upper and lower dies
The spiral bevel gear blank is set as a plastic body, the initial forging temperature is 1050 ° C, and the material is 20CrMnTiH. Set the upper and lower molds as rigid bodies, with the initial temperature of 250 ° C and the material of 4Cr5MoSiV1.
3、 Analog control parameter setting
The Lagrangian incremental model is selected as the simulation method, and the deformation+heat transformer is selected as the type. The simulation step length is set to 0.28mm, and the simulation step number is set to 600. The conjugate gradient method is used as the solution algorithm, and the direct iteration method is used as the iteration method.
4、 The friction coefficient is taken as 0.3, and the downward speed of the upper die is taken as 5mm/s
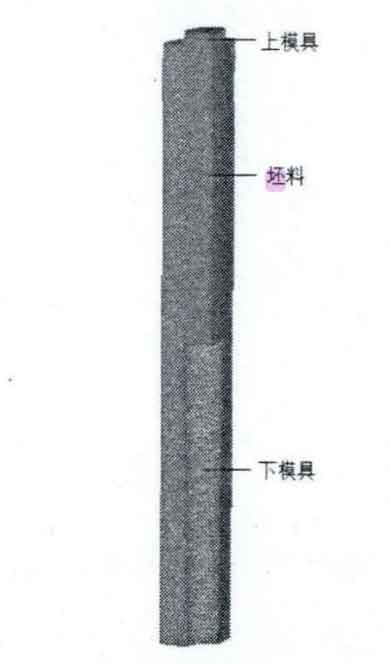
The final finite element model is shown in Figure 2.