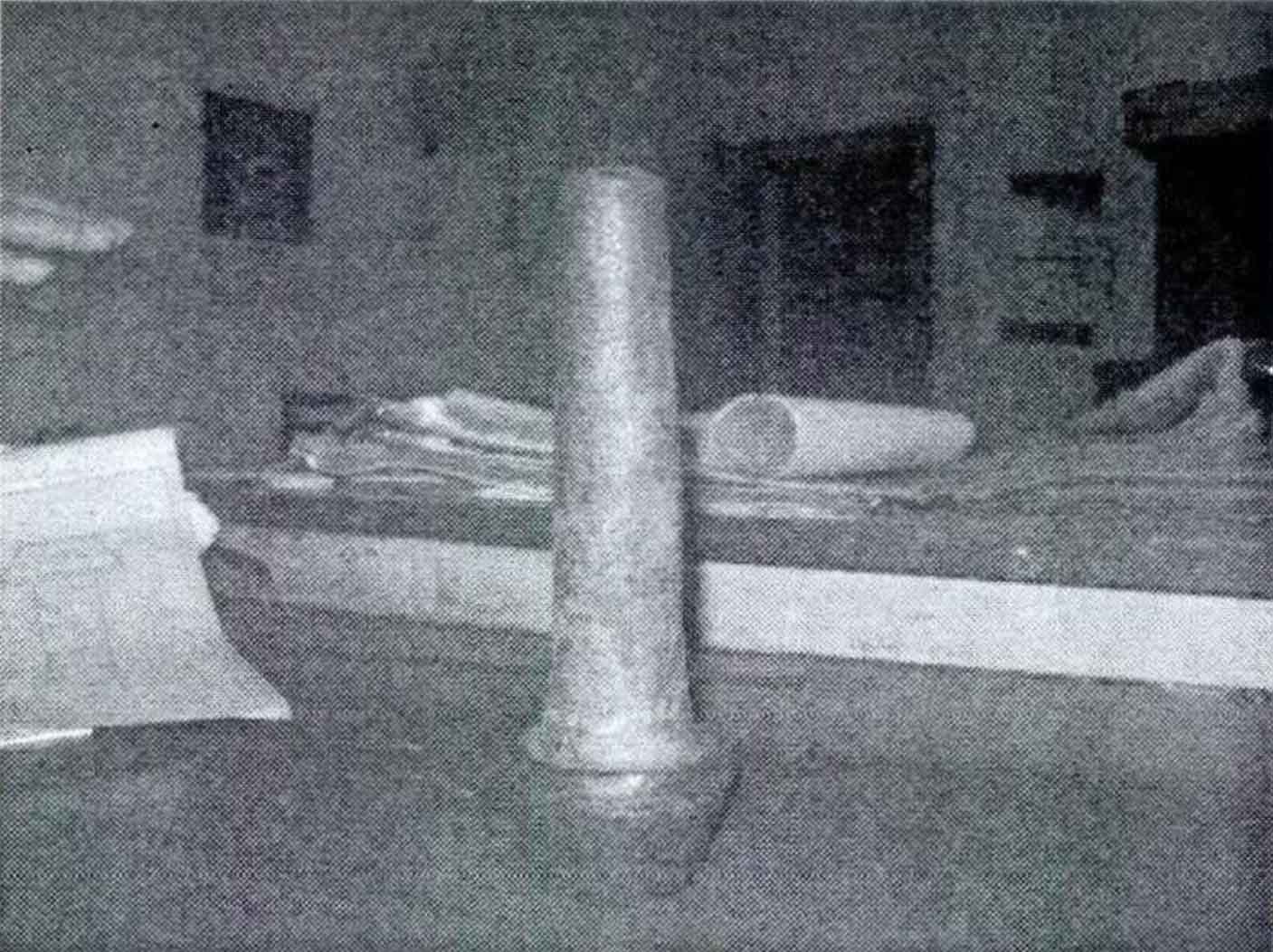
Due to the problems in the free forging process of the cutting block, other forming methods are considered to replace the free forging of the cutting block to achieve the purpose of drawing. The following two forming methods are considered to replace the free forging of cutting block to realize the drawing of spiral bevel gear blank.
Extrusion forming
Extrusion is a plastic forming processing method that applies pressure to the metal blank of spiral bevel gear in the die cavity through the punch fixed on the press to produce plastic deformation, so as to obtain the required shape, size and parts with certain mechanical properties. Extrusion can be used to lengthen the bar. Extrusion has the following advantages:
- improve metal deformation capacity. In the process of extrusion, the metal can give full play to its plasticity and obtain large deformation due to the strong triaxial compressive stress.
- high comprehensive quality of extruded products. Extrusion deformation can improve the microstructure and mechanical properties of metal materials.
- great production flexibility. Products with different shapes, sizes and varieties can be produced on the same equipment only by changing the mold.
Spinning forming
Spinning forming is a kind of metal pressure processing method which makes use of tools such as spinning wheel to make feeding motion, pressurize the rotating metal slab or rotary body blank, and make it produce continuous local plastic deformation to obtain the workpiece. Spinning is generally used to form thin-walled hollow rotary workpiece. But we can also use the spinning method to realize the bar drawing. Spinning has the following advantages:
- the spinning pressure required for spinning forming is small, the requirements for equipment tonnage are small, and the forming energy consumption is small.
- high material utilization, saving man hours and reducing costs.
- high quality spiral bevel gear. After spinning, the structure of the workpiece is compact, the fiber is continuous, the grain is refined, and the comprehensive properties of the spiral bevel gear are improved.
The extrusion forming method is proposed to be used to stretch the spiral bevel gear blank, the extrusion forming process is numerically simulated by using Defrom-3D, and the extrusion process and die forging process are analyzed in multiple steps.