The CAD two-dimensional drawing of the upper and lower molds is shown in Figure 1.
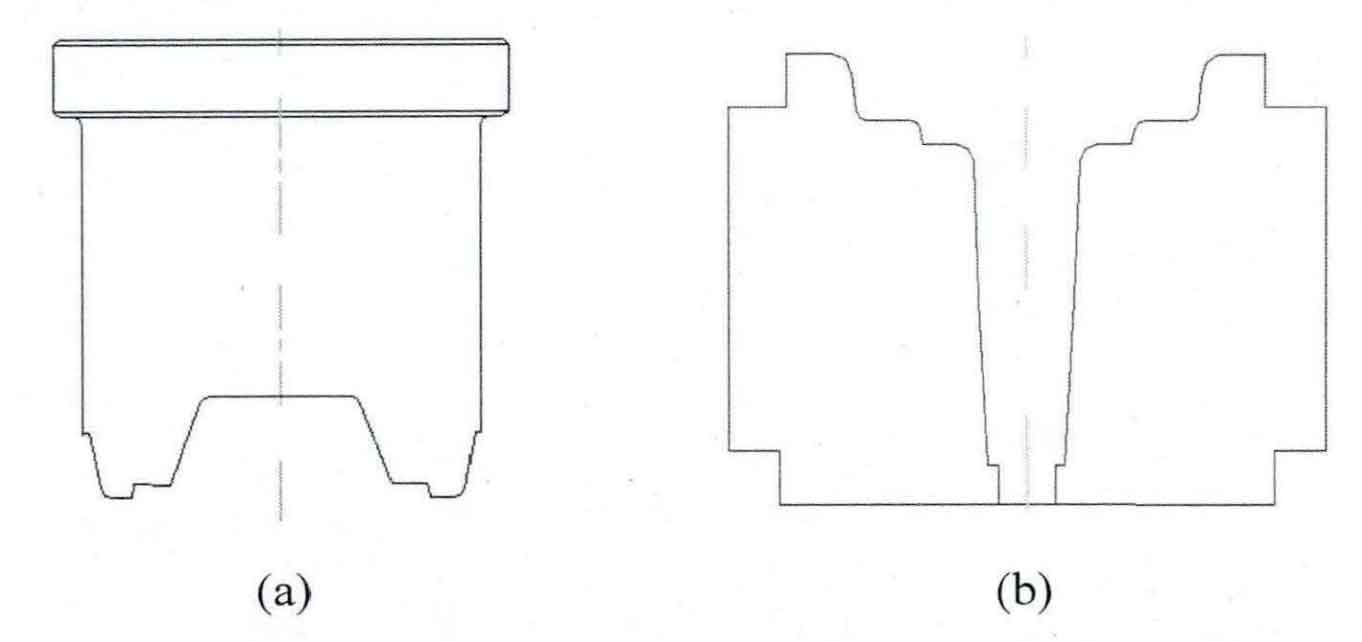
1.Mold geometric model establishment
According to the two-dimensional drawings of the upper and lower molds, the 1/4 geometric model of the upper and lower molds is established, as shown in Figure 2.
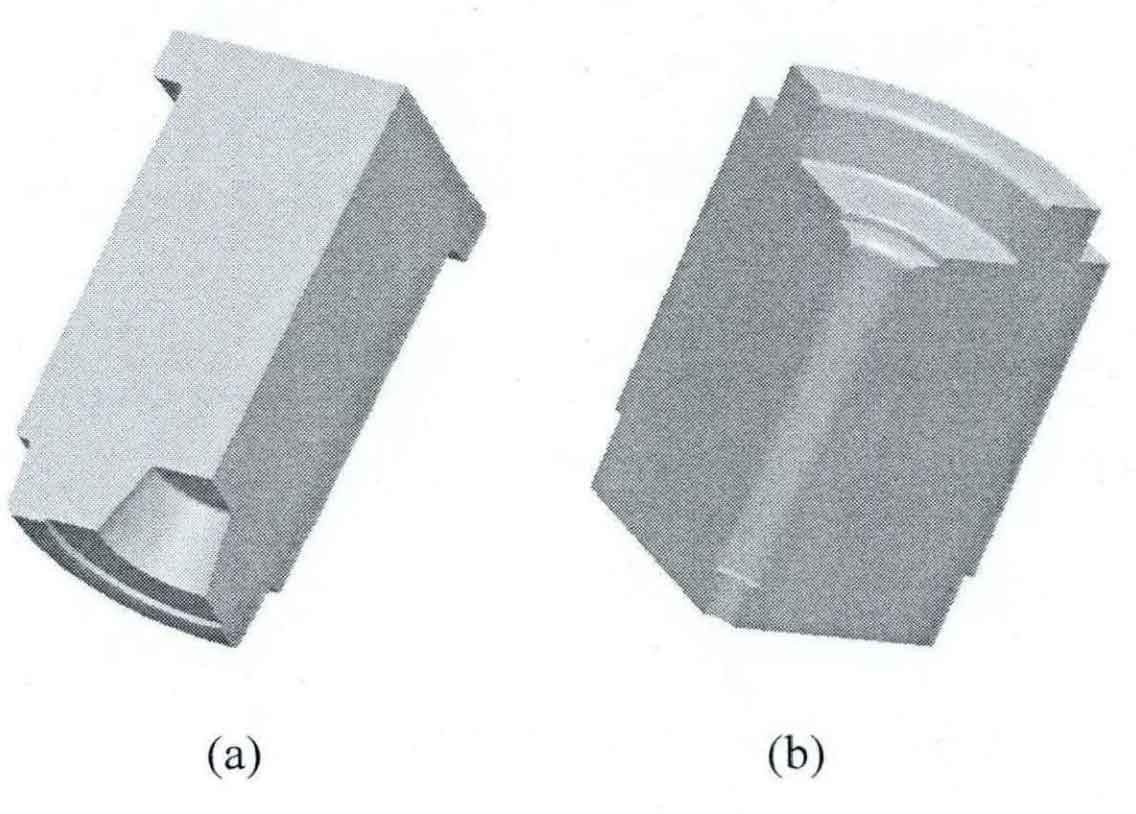
2.Establishment of finite element model for die forging process
After the extrusion process is completed, enter the pre-processing module of Defrom-3D, delete the grids and geometric models of the upper and lower dies in the extrusion process, and import the geometric models of the upper and lower dies in the die forging process, so as to establish the finite element model of the die forging process. The establishment of finite element model for die forging process includes the following contents:
(1) Mesh the upper and lower dies. After division, the number of upper mold grids is 60883 and the number of lower mold grids is 137789.
(2) Set the upper and lower molds as rigid bodies, with the initial temperature of 250 ° C and the material of 4Cr5MoSiV1.
(3) The simulation step size is set to 0.15mm and the simulation steps are set to 500. The conjugate gradient method is used as the solution algorithm and the direct iteration method is used as the iteration method.
(4) The friction coefficient is taken as 0.3, and the screw press sample is selected as the forging equipment.
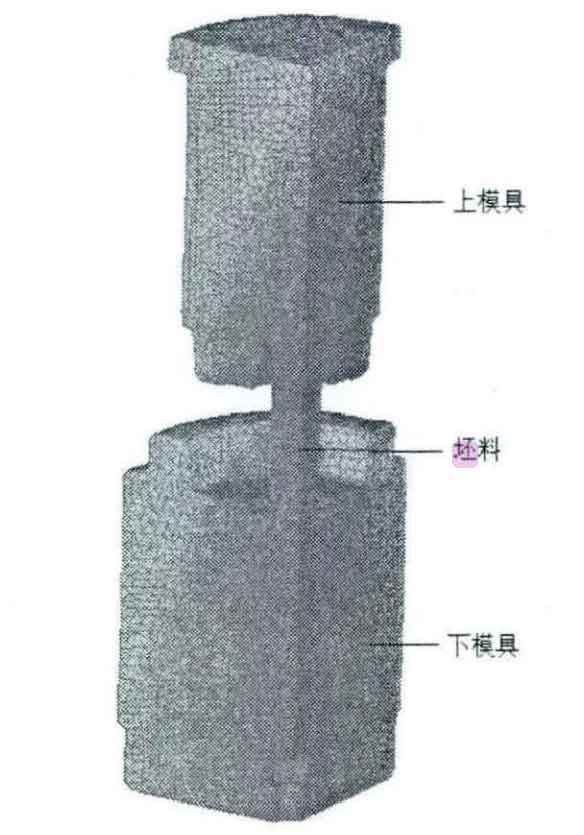
The final finite element model is shown in Figure 3.
3.Metal flow law in die forging process
The metal velocity vector diagram of each stage of the die forging process is shown in Figure 4. Since the numerical simulation of die forging process is based on the numerical simulation of extrusion process, the numerical simulation of die forging process starts from step 549. Figure 4 (a) is the metal flow velocity vector diagram of step 550, figures (b) to (E) are the metal flow velocity vector diagram of the intermediate process, and figure (f) is the metal flow velocity vector diagram at the completion of die forging.

4.Equivalent stress analysis during final forging
The stress distribution of forgings during final forging is shown in Figure 5. The overall stress of the forging is between 86-656mpa, and the large stress occurs at the bottom, outer edge and flash of the forging. There is a sudden increase in stress at the step as shown in Figure 6.
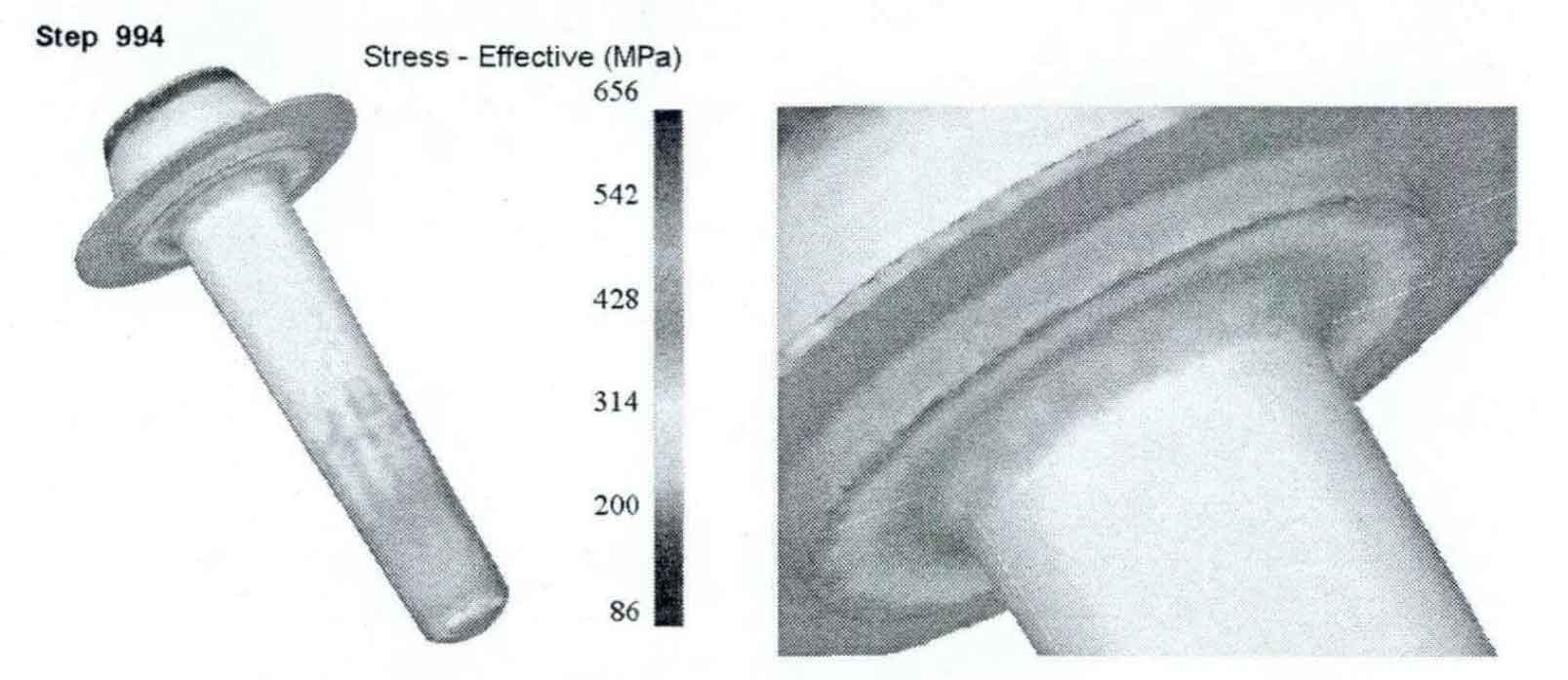
5.Equivalent strain analysis during final forging
The distribution of equivalent strain of forgings during final forging is shown in Figure 7. The overall strain of the forging is between 0.12 and 5.8, and the large strain occurs at the outer edge and flash. The strain increases abruptly at the step as shown in Figure 8.
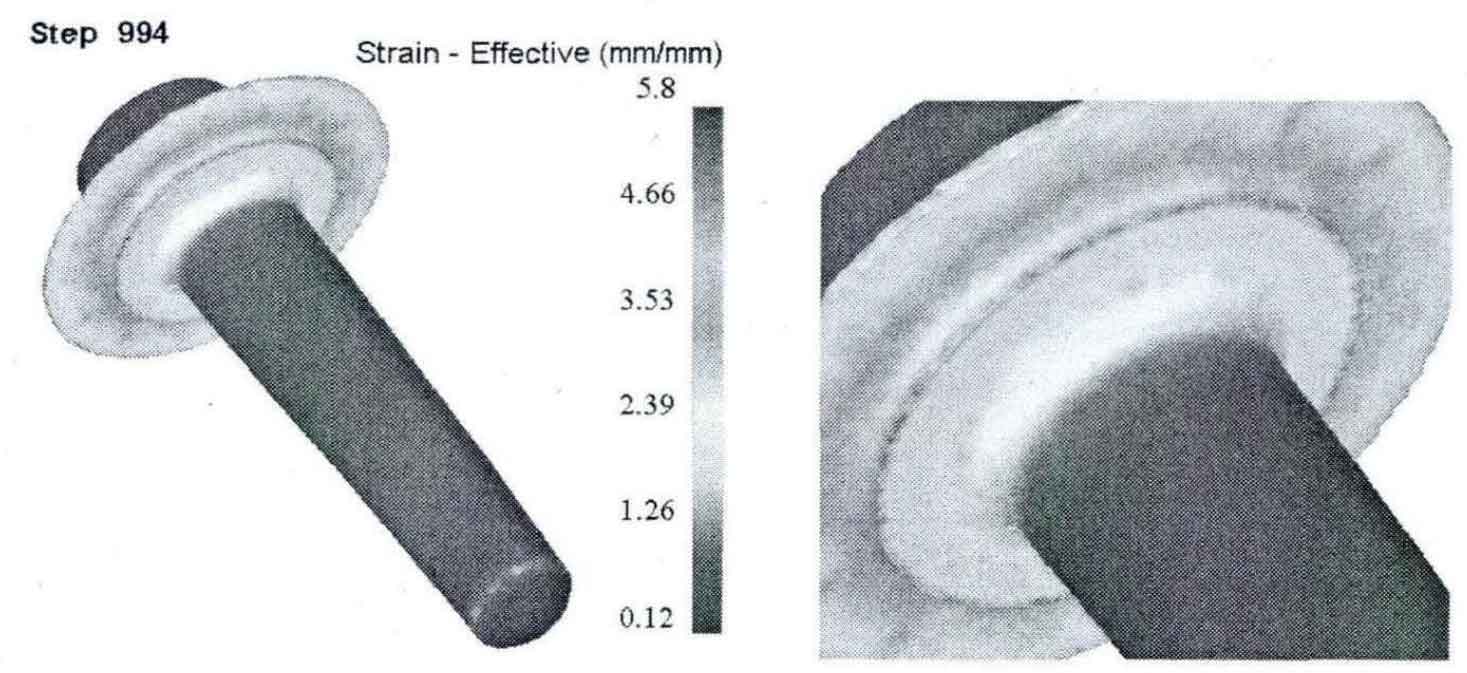
6.Temperature analysis during final forging
The temperature distribution of forgings during final forging is shown in Figure 9. The overall temperature of forgings is between 470-1601 ° C, and the high temperature occurs at the outer edge and flash. There is a sudden increase in temperature at the step as shown in Figure 10.
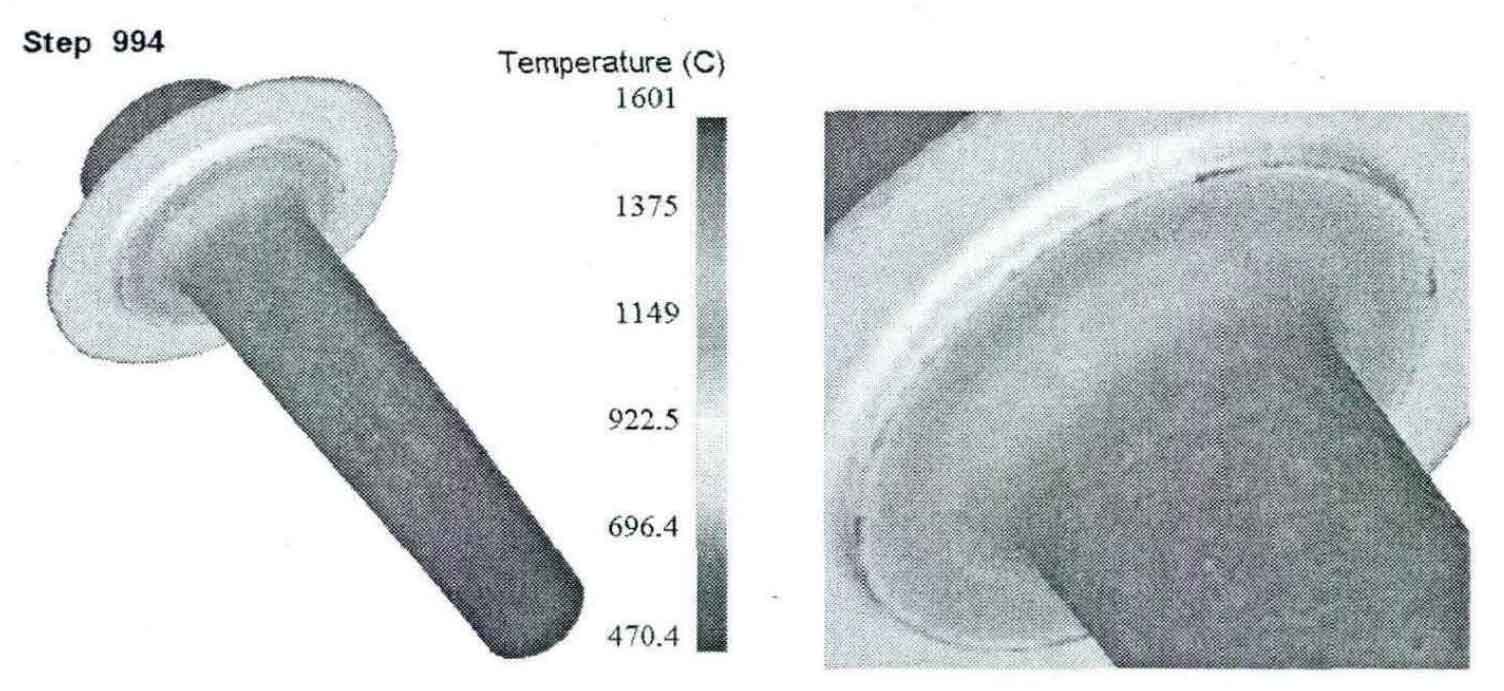