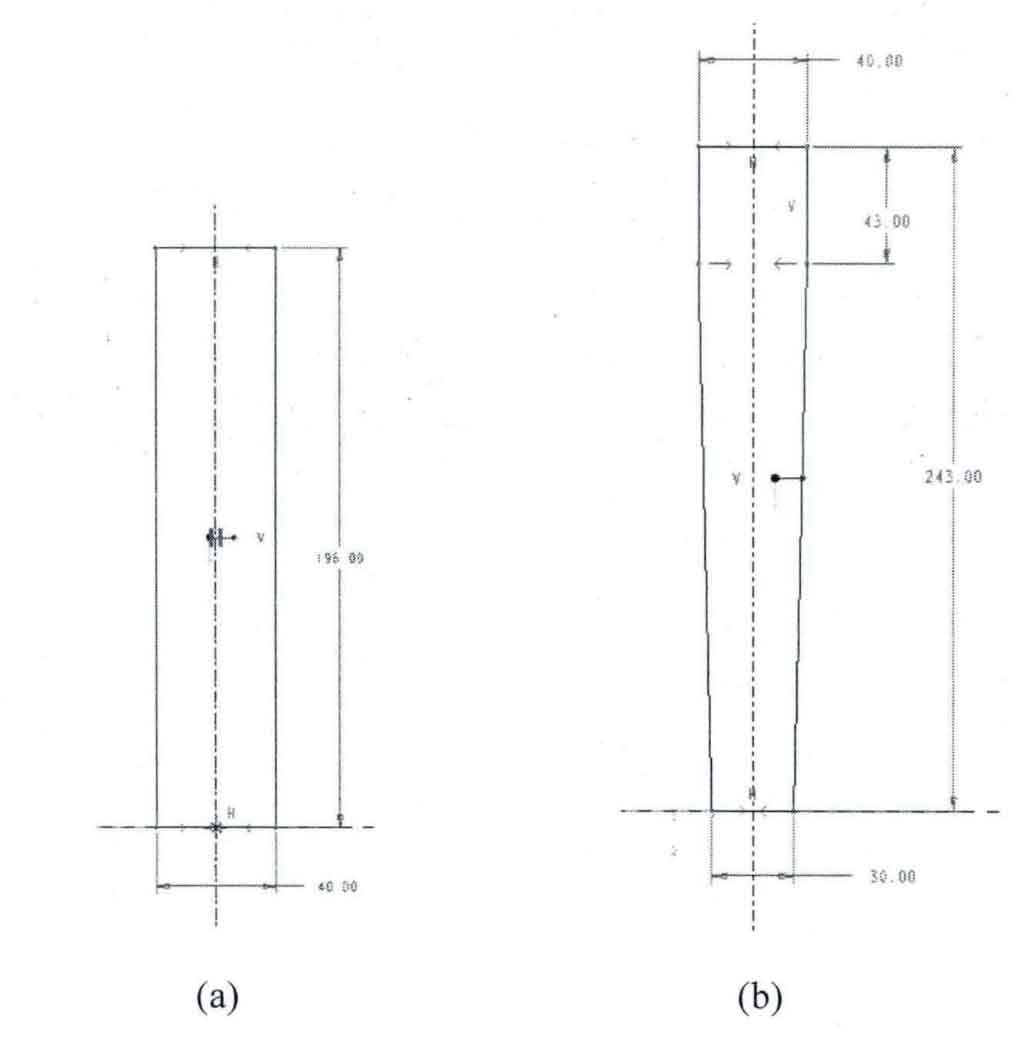
The forging process of driving spiral bevel gear blank also includes four steps: heating, drawing, die forging and trimming. That is, before die forging, the blank shall be drawn into a certain taper, as shown in Figure 1. The existing process of ZHY gear is to lengthen the billet by means of free forging on the cutting board, but the material distribution around the spiral bevel gear billet is uneven after lengthening by means of free forging on the cutting board, The uneven distribution of materials around the drawn spiral bevel gear blank is easy to cause bending of forgings after die forging, as shown in Figure 2
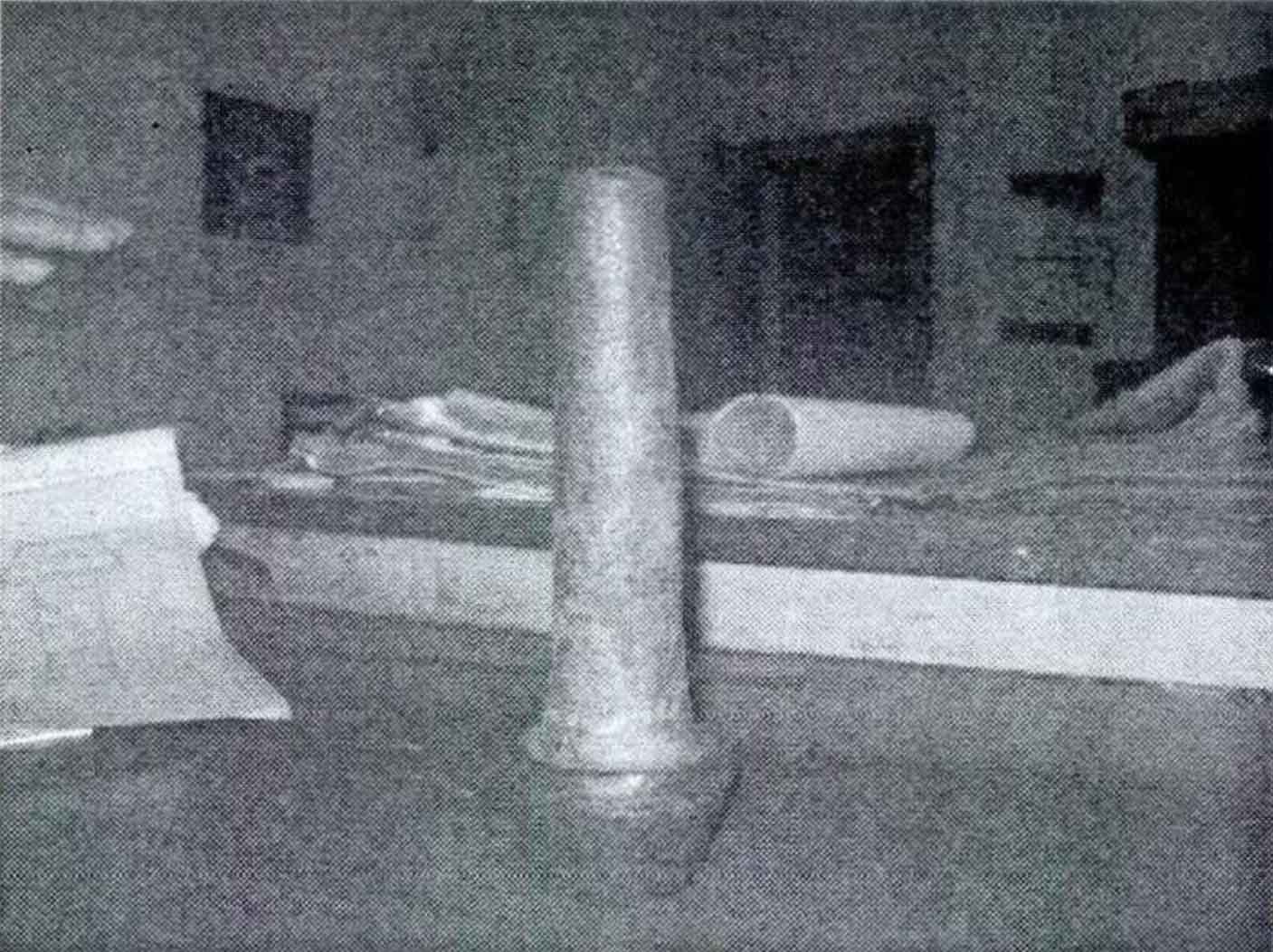
- The extrusion forming and drawing method is put forward to solve the problem of forging bending caused by free forging and drawing of cutting block.
- The extrusion forming process is numerically simulated, and the multi-step analysis is carried out in combination with the die forging process. The metal flow laws in the extrusion process and the die forging process are obtained, and the curves of equivalent stress, strain and temperature with time in the forging process are obtained. The equivalent stress The load curve and energy consumption curve of the spiral bevel gear forging process were obtained.
- The lower die structure of the spiral bevel gear driving wheel was improved, and the forging process of the spiral bevel gear with the improved die was numerically simulated. The stress, strain, temperature distribution and forming load of gear blank before and after die improvement were compared, and the influence of die structure on forming effect was analyzed.
- The influence of different initial forging temperature and friction on the forging effect of the driving gear blank of spiral bevel gear is studied.