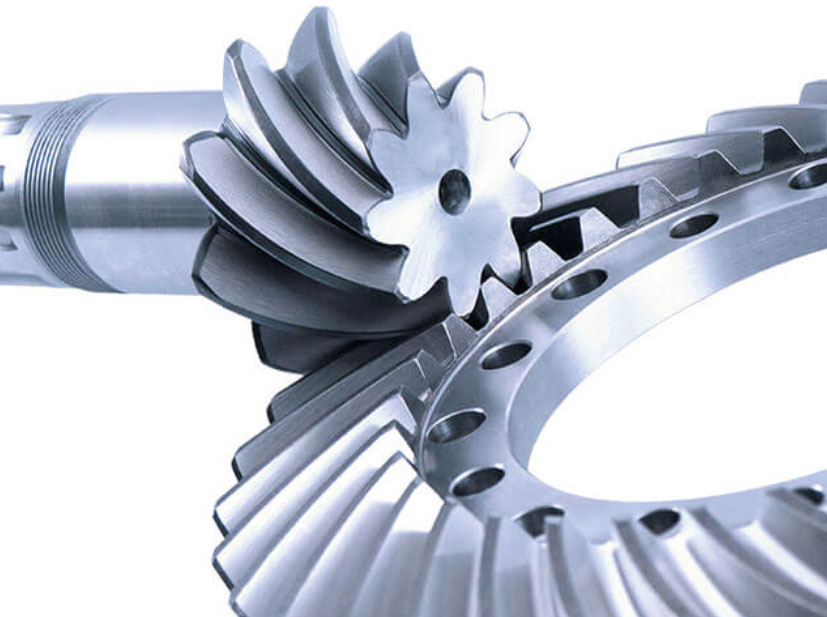
Spiral bevel gears excel in power transfer applications due to their unique design features and performance advantages. They are widely used in various industries where efficient and reliable power transmission is essential. Let’s explore how spiral bevel gears achieve optimal gear transmission:
- Smooth Meshing Action: The rolling/sliding meshing action of spiral bevel gears ensures smoother and gradual tooth engagement. This reduces impact and vibration during gear meshing, leading to quieter operation and improved efficiency. The smooth meshing action also helps in distributing the load more evenly across the gear teeth, minimizing wear and increasing gear life.
- Higher Contact Ratio: Spiral bevel gears typically have a higher contact ratio compared to other gear types. This means that multiple teeth are in contact at any given moment during operation. The increased contact ratio allows for better load distribution, resulting in higher load-carrying capacity and improved power transmission efficiency.
- Optimized Tooth Geometry: Engineers can optimize the tooth geometry of spiral bevel gears to match specific application requirements. This optimization includes factors like tooth profile, spiral angle, and pitch diameter. The customized gear design ensures that power transfer is efficient and tailored to the system’s needs.
- Durability and Load-Carrying Capacity: Spiral bevel gears are designed to handle high loads and provide reliable performance. The gradual tooth engagement, reduced tooth impact, and larger contact area contribute to their exceptional durability, making them suitable for heavy-duty power transmission applications.
- Versatility in Shaft Arrangements: Spiral bevel gears can connect intersecting shafts at various angles. This versatility allows them to be used in systems with complex spatial configurations, making them suitable for applications where non-parallel shafts are required.
- Low Noise and Vibration: The smooth meshing action and optimized tooth profile of spiral bevel gears contribute to reduced noise and vibration during gear operation. This is particularly beneficial in applications where noise reduction is important, such as in automotive differentials or precision machinery.
- High Efficiency: The combination of smooth meshing, high contact ratio, and optimized tooth geometry results in higher gear efficiency. Reduced friction and better load distribution contribute to less power loss during gear transmission, leading to improved overall system efficiency.
- Reliable Power Transmission in Precision Machinery: Spiral bevel gears find extensive use in precision machinery and robotic systems due to their ability to provide accurate motion control and reliable power transmission. The low backlash and high precision of these gears make them ideal for applications requiring tight control and repeatability.
Spiral bevel gears excel in power transfer applications due to their smooth meshing action, higher contact ratio, optimized tooth geometry, durability, low noise, and versatility. Their ability to handle heavy loads, provide reliable and efficient power transmission, and perform well in precision applications makes them a preferred choice in various industries, ranging from automotive and aerospace to robotics and industrial machinery.