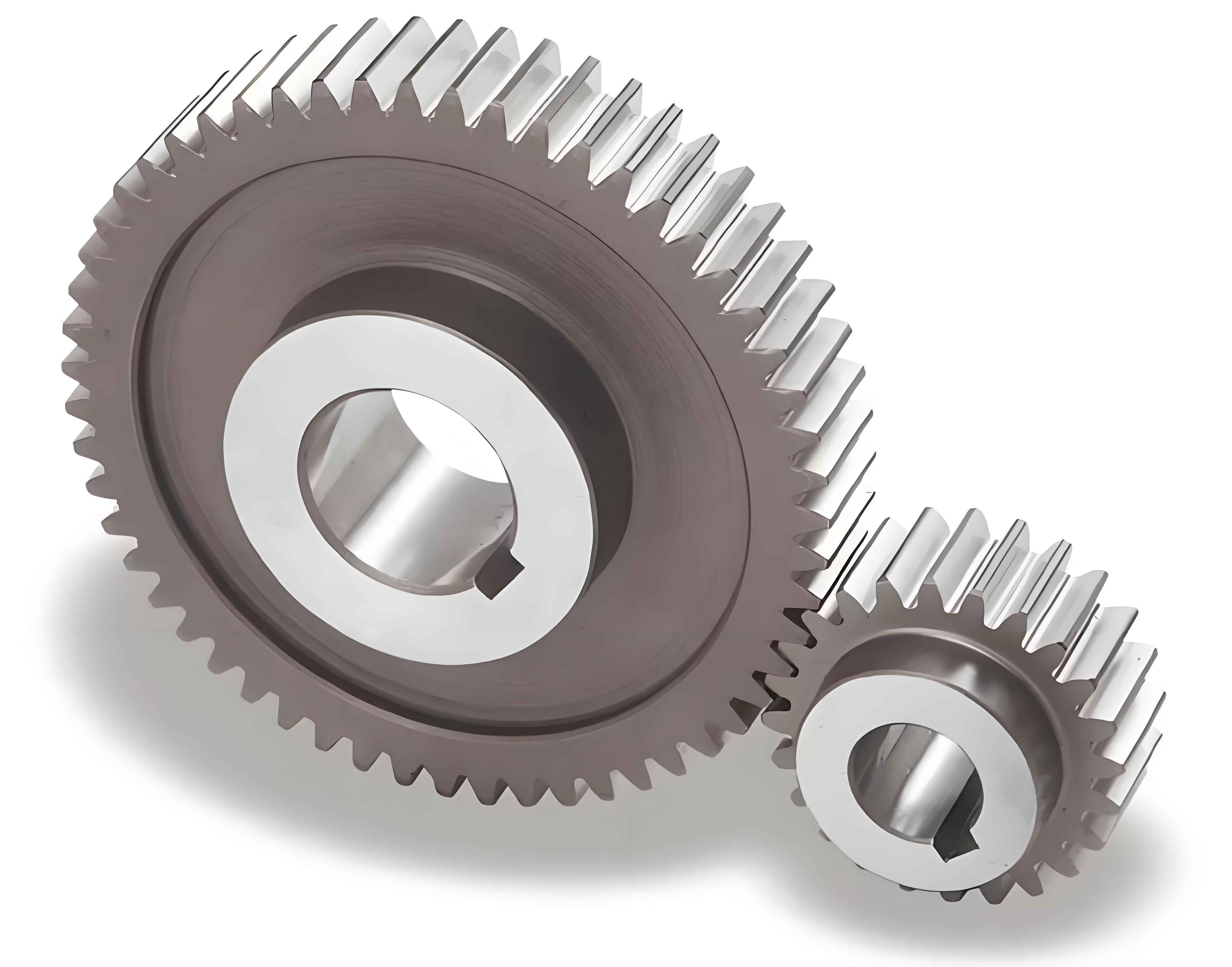
Introduction
Spur gear is widely used in various mechanical systems due to their simplicity, reliability, and efficiency. However, the increasing demand for higher performance and durability necessitates the optimization of spur gear design. This optimization involves several factors including material selection, geometric configuration, and manufacturing processes. This article explores the strategies and methodologies to optimize spur gear design for enhanced performance and durability.
Material Selection
Material selection is critical in optimizing spur gear design. The choice of material affects the gear’s strength, wear resistance, and overall performance. Common materials used in spur gear include steel, cast iron, and non-metallic materials such as polymers.
Table 1: Common Materials for Spur Gear
Material | Properties | Applications |
---|---|---|
Steel | High strength, wear resistance | High-load applications, industrial |
Cast Iron | Good machinability, damping capacity | Medium-load applications, automotive |
Polymers | Lightweight, corrosion resistance | Low-load applications, consumer goods |
Geometric Optimization
The geometric parameters of spur gear, such as module, pressure angle, and face width, significantly influence their performance. Optimization of these parameters can enhance load-carrying capacity, reduce noise and vibration, and improve overall efficiency.
Module and Pressure Angle
The module is the ratio of the pitch diameter to the number of teeth, and the pressure angle is the angle between the line of action and the line tangent to the pitch circle. These parameters must be carefully selected to balance strength and smooth operation.
Face Width
The face width of spur gear affects its load-carrying capacity and durability. A wider face width allows for better load distribution, reducing stress and wear on individual teeth.
Table 2: Geometric Parameters for Optimal Performance
Parameter | Optimal Range | Impact on Performance |
---|---|---|
Module | 1.5 to 5 mm | Balances strength and smooth operation |
Pressure Angle | 20° to 25° | Ensures smooth engagement and durability |
Face Width | 8 to 12 times the module | Enhances load distribution and reduces wear |
Manufacturing Processes
The manufacturing process of spur gear plays a crucial role in their performance and durability. Advanced manufacturing techniques such as precision forging, gear hobbing, and grinding can significantly enhance the quality and performance of spur gear.
Precision Forging
Precision forging produces spur gear with excellent mechanical properties and dimensional accuracy. This process enhances the gear’s strength and wear resistance, leading to improved performance and durability.
Gear Hobbing
Gear hobbing is a versatile and efficient method for producing high-quality spur gear. It allows for precise control over gear geometry, resulting in spur gear with improved load-carrying capacity and reduced noise.
Grinding
Gear grinding is used to achieve high precision and smooth surface finishes. This process reduces surface roughness, improving the spur gear’s contact ratio and overall performance.
Table 3: Manufacturing Processes and Their Benefits
Process | Benefits | Applications |
---|---|---|
Precision Forging | High strength, excellent dimensional accuracy | High-performance gears, aerospace |
Gear Hobbing | Precise control, versatile | Industrial gears, automotive |
Grinding | High precision, smooth surface finish | High-precision gears, machinery |
Finite Element Analysis (FEA)
Finite Element Analysis (FEA) is a powerful tool for optimizing spur gear design. FEA allows for the simulation of spur gear performance under various loading conditions, identifying potential stress concentrations and areas for improvement.
Stress Analysis
FEA can be used to analyze stress distribution within the spur gear teeth, identifying areas prone to failure. By optimizing the geometry and material properties, the stress concentrations can be minimized, enhancing the gear’s durability.
Table 4: FEA Analysis Results
Parameter | Initial Design | Optimized Design | Improvement |
---|---|---|---|
Maximum Stress (MPa) | 450 | 380 | 15% |
Contact Ratio | 1.4 | 1.6 | 14% |
Wear Factor | 0.035 | 0.025 | 29% |
Conclusion
Optimizing spur gear design for enhanced performance and durability involves a comprehensive approach, considering material selection, geometric parameters, manufacturing processes, and advanced simulation techniques. By systematically addressing these factors, it is possible to develop spur gear that meet the increasing demands of modern mechanical systems.