Introduction
Bevel gears are crucial components in gear transmission systems and are widely used in various fields such as automobiles, precision machine tools, aerospace, etc. Time-varying meshing stiffness is an important basis for evaluating the transmission performance of bevel gears, and accurately calculating its time-varying meshing stiffness is a prerequisite for ensuring the stability of the transmission performance of bevel gears. Therefore, it is of great significance to calculate the time-varying meshing stiffness of bevel gears efficiently and accurately.
Calculation Model of Meshing Stiffness of Spur Bevel Gears
- Spur Bevel Gear Slice Model
Considering the three-dimensional spatial structure and spatial meshing characteristics of the spur bevel gear, the gear teeth of the bevel gear are discretized along the tooth width direction with the back cone, and the circular plane of the gear body along the axis direction is discretized to form a series of thin slice bevel gears with the same tooth width. Based on the back cone equivalence principle, the large end back cone of each thin slice bevel gear is expanded. When the width of the thin slice is small enough, the bevel gear can be approximated as a series of spur gears with the same number of teeth (but different sizes). Figure 1 shows the slice model of the spur bevel gear.
In Figure 1, the gear teeth of the bevel gear are divided into a series of tooth slices with a small enough width along the tooth width direction, and is the width of the thin slice gear teeth; , , and (where represent the driving gear and the driven gear, respectively) represent the pitch circle radius, addendum circle radius, and dedendum circle radius of the bevel gear; , B, R, and represent the cone angle, tooth width, outer cone distance, and shaft hole radius of the bevel gear, respectively.
Based on the back cone equivalence principle, the large end back cone of the thin slice gear teeth is expanded, and the equivalent number of teeth , equivalent pitch circle radius , equivalent addendum circle radius , and equivalent dedendum circle radius of the -th thin slice can be expressed as:
where is the thin slice number, ; is the number of teeth; and are the tooth top angle and tooth root angle of the bevel gear, respectively.
In addition, the gear body part of the thin slice bevel gear is divided into a series of thin slice gear bodies with a small enough width along the vertical axis direction of the circular plane. The relationship between the width of the thin slice gear body, the width of the gear teeth, the tooth width , and the number of thin slices can be expressed as: - Calculation of Slice Meshing Stiffness
Each thin slice can be approximated as a spur gear, and the spur bevel gear can be approximated as a number of spur gears connected in parallel. The stiffness of the thin slices participating in the meshing at each instant is obtained, and finally the total meshing stiffness at each meshing position can be obtained by accumulation. Under the action of external loads, the equivalent meshing stiffness of the gear caused by the deformation of the gear teeth includes Hertz contact stiffness, bending stiffness, shear stiffness, and radial compression stiffness; in addition, there is also the equivalent meshing stiffness of the gear caused by the deformation of the gear body, namely the gear body stiffness. Therefore, the single-tooth linear meshing stiffness corresponding to the -th thin slice can be expressed as:
where , , , , and are the contact stiffness, bending stiffness, shear stiffness, radial compression stiffness, and gear body stiffness, respectively. The Hertz contact stiffness can be calculated by Equation (10) in Reference [9], the gear body stiffness can be calculated by Equation (17) in Reference [10], and the bending stiffness, shear stiffness, and radial compression stiffness can be calculated by Equations (2.26), (2.30), and (2.32) in Reference [11], respectively; the superscripts 1 and 2 represent the driving gear and the driven gear, respectively.
The traditional analytical method calculates the multi-tooth meshing stiffness by adding the single-tooth meshing stiffness of the tooth pairs, resulting in a large calculation error. This is because the traditional analytical method only considers the single-tooth meshing situation when calculating the gear body stiffness, ignoring the coupling effect between the tooth pairs. To this end, in the calculation of the double-tooth meshing stiffness, a correction coefficient of the gear body stiffness is introduced in this paper, and the double-tooth linear meshing stiffness is expressed as:
where represents the meshing tooth pair; and are the correction coefficients of the driving wheel and the driven wheel gear body stiffness, respectively, and this coefficient will be determined in Section 1.3.
In addition, the time-varying meshing stiffness can also be evaluated by the torsional meshing stiffness. According to the relationship between the linear meshing stiffness and the torsional meshing stiffness [12]331, the torsional meshing stiffness of the bevel gear can be expressed as:
where is the base circle radius corresponding to the -th thin slice. - Calculation of Gear Body Stiffness Correction Coefficient
Considering the three-dimensional spatial structure of the bevel gear, a three-dimensional finite element model of each thin slice bevel gear is established in the finite element software Ansys. Figure 2 shows the finite element model of the thin slice of the bevel gear.
In order to calculate the displacement along the action line induced by the gear body at the meshing point, the elastic modulus of the thin slice gear teeth of the bevel gear is set to 10,000 times that of the gear body. At this time, compared with the gear body, the gear teeth can be regarded as a relatively rigid region, so the displacement caused by the local Hertz contact and the elastic deformation of the gear teeth can be ignored [12]337. A mass21 element is established at the midpoint of the tooth width of the axis of the thin slice, coupled with the inner ring nodes and subjected to full constraints. In the figure, , are the local coordinate systems of the meshing point; the axes and are along the direction of the action line, respectively. At the double-tooth meshing position , a force is applied along the axis , and at the meshing position , a force (where ) is applied along the axis , and the displacement generated at (where ; ) along the action line direction is measured. To make the calculation method in this paper easier to understand, the definitions of each symbol are shown in Table 1. According to the finite element results, we can obtain:
The load distribution coefficients and can be expressed as:
Table 1: Symbol Definition
Symbol | Definition |
---|---|
Fo | The resultant force applied at 0 |
ky | The gear body stiffness when the force F is applied at 0 |
Kg | The gear body stiffness when the forces F are applied at 0 and 0 |
The displacement along the action line at 0 when the force F is applied | |
The displacement along the action line at 0 when the force F is applied at 0 | |
The displacement along the action line at 0 when the forces F are applied at 0 and 0 |
Based on the linear superposition assumption, and can be expressed as:
By combining Equations (7) and (8), the gear body correction coefficients and can be obtained as:
By calculating the gear body correction coefficient and corresponding to each thin slice and substituting them into Equation (5), the double-tooth meshing stiffness of the bevel gear can be obtained. Compared with the finite element model of the bevel gear pair, the thin slice finite element model is very simple and does not require the setting of contact pairs, normal penalty stiffness coefficients, solution methods, etc., therefore, most of the calculation time can be saved.
Calculation Model of Meshing Stiffness of Error Tooth Profile Bevel Gears
- Deviation of Each Thin Slice Tooth Profile Caused by Assembly Error of Bevel Gears
There are many factors that affect the meshing stiffness of spur bevel gears. In addition to design deviations and manufacturing errors, the installation error has a greater impact on the meshing stiffness of spur bevel gears. Therefore, in this paper, only the deviation of the tooth profile position (thin slice back cone error tooth profile) caused by the installation error is considered, and its meshing stiffness model is established. According to national standards, the installation error can be divided into shaft intersection angle error and shaft intersection point error [13]5. Figure 3 shows the relationship diagram of the assembly error coordinate system. In Figure 3, and are the shaft intersection angle error and the shaft intersection point error, respectively; the coordinate systems and are fixed to the main and driven gears, respectively, where and coincide with the axes of the main and driven gears, respectively; and are the auxiliary coordinate systems at the -th thin slice, where the angles between , and , are and , respectively.
From Figure (a), under the shaft intersection angle error, the coordinate system rotates clockwise around the axis by an angle to the position shown in the figure . From Figure (b), under the shaft intersection point error, the coordinate system translates along the axis by to the position shown in the figure . Therefore, the tooth profile deviation and caused by the shaft intersection angle and the shaft intersection point of the -th thin slice are:
where (where ) is the cone angle of the main and driven wheels; is the outer cone distance of the thin slice . When the driving gear rotates clockwise, can be expressed as:
where is the pressure angle; is the angle between the centerline connection of the gear tooth slices of the main and driven gears and the direction of the of the driving gear slice.
In addition, the angle deviation and of the -th thin slice caused by the shaft intersection angle and the shaft intersection point are:
where is the base circle radius corresponding to the thin slice . - Meshing Stiffness Model of Error Tooth Profile Bevel Gears
Under the installation error condition, the axis of the bevel gear will shift and tilt, resulting in different meshing situations for each thin slice tooth pair, often leading to edge contact, which seriously affects the transmission performance of the gear. Therefore, the calculation of the meshing stiffness under the error condition needs to judge whether each。
- Meshing Stiffness Model of Error Tooth Profile Bevel Gears
Under the installation error condition, the axis of the bevel gear will shift and tilt, resulting in different meshing situations for each thin slice tooth pair, often leading to edge contact, which seriously affects the transmission performance of the gear. Therefore, the calculation of the meshing stiffness under the error condition needs to judge whether each thin slice participates in the meshing. Figure 4 shows the load-bearing contact process of the bevel gear thin slice under the error condition. In the figure, (where and so on) is the tooth profile deviation of the thin slice ; is the sum of the deformation amount and the tooth profile deviation of the thin slice under load; is the angle deviation of the thin slice; is the sum of the angular displacement and the angle deviation of the thin slice under load; is the applied external torque. Under the action of the load, as the driving wheel rotates, the thin slice with the smallest angle deviation among all the thin slices will definitely be the first to come into contact. Suppose the angle deviation of the thin slice is the smallest among all the thin slices, that is, the thin slice starts to contact first. As the driving wheel continues to rotate, the thin slice starts to undergo elastic deformation, causing the center point to produce an angular displacement . When the sum of and is greater than the angle deviation of the thin slice , the thin slice starts to contact and deform, bearing the load; if the load capacity at this time does not reach the load capacity of the bevel gear, will continue to increase until the sum of and is greater than the angle deviation of the tooth pair , the tooth pair starts to participate in the meshing. And so on, until the load capacity of all the thin slice tooth pairs participating in the meshing is equal to the external torque received by the bevel gear, the gear is in a force balance state, and the deformation ends.
After loading, the angular displacement of the bevel gear can be expressed as:
From Equation (14), when the center point angular displacement of the thin slice tooth pair is known, the center point angular displacement of the thin slice tooth pair is:
According to the principle of force balance, the load-bearing torque generated by the bevel gear as a whole should be the sum of the load-bearing capacities of the thin slice tooth pairs in the meshing state, that is:
where is the applied external torque; is the number of thin slices participating in the meshing under ideal conditions; is the judgment factor, which takes 1 when the thin slice participates in the meshing, and 0 otherwise; is the torsional meshing stiffness of the thin slice ; is the center point angular displacement of the thin slice .
Figure 5 shows the calculation process of the angular displacement of the thin slice under the error condition. Input , , and by judging whether is greater than a certain value, the thin slices participating in the meshing are obtained. If the relative error between the load-bearing capacity of the thin slice tooth pairs participating in the meshing and the external torque is greater than the acceptable value , increase the step size of , and continue the loop calculation; otherwise, output , , and the loop ends. In this paper, the initial value of is set to 0, , , and .
When the bevel gear pair is regarded as a whole, under the action of an external load, the angular displacement of the center point of the bevel gear is the same as that of the thin slice tooth pair that first comes into contact, that is, the center angular displacement of the thin slice tooth pair . Therefore, the comprehensive torsional meshing stiffness of the bevel gear pair under the error condition can be expressed as:
In addition, according to the deformation amount of each thin slice, the load borne by each thin slice can be obtained as:
Example Analysis
Take a pair of spur bevel gears as an example (parameters are shown in Table 2) for finite element analysis, and compare the finite element calculation results with the method in this paper and the traditional analytical method to verify the accuracy of the method in this paper.
Table 2: Spur Bevel Gear Parameters
Parameter | Value | Parameter | Value |
---|---|---|---|
Module/mm | 1.75 | Addendum Coefficient | 1 |
Number of Teeth of Driving Gear | 35 | Clearance Coefficient | 0.25 |
Number of Teeth of Driven Gear | 35 | Hole Radius | 15 |
Tooth Width | 10 | Poisson’s Ratio | 0.3 |
Pressure Angle | 20 | Elastic Modulus/CPa | 206 |
- Finite Element Model of Spur Bevel Gear
Figure 6 shows the finite element model of the spur bevel gear. A mass21 element is established at the midpoint of the tooth width of the axis of the main and driven gears, coupled with the nodes on the inner surface of the gear wheel; the axial rotation degree of freedom is retained for the driving gear and a torque is applied; full freedom constraints are applied to the driven gear. The normal penalty stiffness coefficient is set to 1, the penetration coefficient is set to 0.1, and the augmented Lagrangian method is used for the solution.
In this model, by calculating 10 meshing positions within one meshing cycle, the torsional meshing stiffness of the spur bevel gear can be obtained, that is:
where is the torque applied to the driving wheel; is the angular displacement of the center point of the coupling of the driving wheel.
- Verification of Spur Bevel Gear Meshing Stiffness
During the meshing cycle, taking the meshing stiffness when the rolling angle is , that is, when the spur bevel gear just enters the double-tooth meshing, as the benchmark for mesh independence verification, as shown in Figure 7. It can be seen from Figure 7 that the convergence of this method is good, and when the number of thin slices is greater than 60, the meshing stiffness value tends to be stable.
When the number of thin slices is selected to be 60, the calculation results of the meshing stiffness of the spur bevel gear by the method in this paper, the traditional analytical method, and the finite element method are compared in Figure 8. It can be seen from Figure 8 that the error of the double-tooth meshing stiffness of the spur bevel gear obtained by the analytical method is relatively large, about 40%; the single and double-tooth meshing regions of the bevel gear meshing calculated by the method in this paper are basically the same as those of the finite element method, and the calculated results are also relatively close, with the error of the double-tooth meshing stiffness being about 2% and the error of the single-tooth meshing stiffness being about 3%. This shows that the method in this paper can accurately calculate the meshing stiffness of the bevel gear pair.
The comparison of the calculation time between the method in this paper, the analytical method, and the finite element calculation is shown in Table 3. It can be seen from Table 3 that, under the condition of similar calculation accuracy, the calculation time of the method in this paper (including the time for calculating the correction coefficient of the gear body stiffness) is much less than that of the finite element method, about 0.3% of the calculation time of the finite element method; in addition, the accuracy of the double-tooth meshing stiffness calculated by the method in this paper is much higher than that of the analytical method, about 95% higher. In summary, it shows that the method in this paper can calculate the meshing stiffness of the bevel gear quickly and accurately.
- Analysis of Meshing Stiffness and Load Distribution Considering Assembly Error
To verify the accuracy of the calculation method in this paper under the condition of assembly error, take the shaft intersection point error as , and the calculation results of the meshing stiffness of the bevel gear by the method in this paper and the finite element method are shown in Figure 9. It can be seen from Figure 9 that the calculation error of the double-tooth meshing stiffness is about 3%, and the calculation error of the single-tooth meshing stiffness is about 2%, indicating that this method is also accurate in calculating the meshing stiffness when considering the assembly error.
According to the requirements for the installation accuracy of bevel gears in the national standard GB/T 11365 – 2019, take the shaft intersection angle error as , , , and , and the shaft intersection point error as , , , and , respectively. The meshing stiffness calculation results of the corresponding spur bevel gear pairs are shown in Figures 10 and 11, respectively. It can be seen from Figures 10 and 11 that as the shaft intersection angle error and the shaft intersection point error of the gear increase, the meshing stiffness of the bevel gear decreases. With the decrease of the meshing stiffness of the bevel gear, the meshing deformation and transmission error of the bevel gear will increase, thus affecting the transmission performance and service life of the bevel gear.
Figure 12 shows the distribution of the center point angular displacement and the tooth surface load of the bevel gear center point in the ideal state. It can be seen from Figure 12(a) that under the condition of no error, the center point angular displacement of each thin slice of the bevel gear first increases and then decreases from the tooth root to the tooth top. This is because only one pair of tooth pairs bears the load during single-tooth meshing, while two pairs of tooth pairs bear the load during double-tooth meshing, resulting in a larger angular displacement during single-tooth meshing; it can be seen from Figure 12(b) that the place with the largest load is the large end during the single-tooth meshing of the bevel gear, because the meshing stiffness of the large end thin slice is greater than that of the small end, resulting in a larger torque borne by the large end.
Figure 13 shows the distribution of the center point angular displacement and the tooth surface load of the bevel gear center point when the shaft intersection angle error . It can be seen from Figure 13(a) that the angular displacement of the center point of the small end thin slice of the bevel gear under load is the largest, because the angle deviation of the small end is the smallest under the shaft intersection angle error state, and it is the first to participate in the meshing during the meshing process, resulting in the largest angular displacement of its center point among all the participating thin slices; it can be seen from Figure 13(b) that the maximum load borne by the bevel gear is the small end during the single-tooth meshing.
Figure 14 shows the distribution of the center point angular displacement and the tooth surface load of the bevel gear center point when the shaft intersection point error . It can be seen from Figure 14(a) that the angular displacement of the center point of the large end thin slice of the bevel gear under load is the largest, because the angle deviation of the large end is the smallest under the shaft intersection point error state, and it is the first to participate in the meshing during the meshing process, resulting in the largest angular displacement of its center point among all the participating thin slices; it can be seen from Figure 14(b) that the place with the largest load borne by the bevel gear is the large end during the single-tooth meshing.
In summary, the assembly error of the bevel gear causes serious unbalanced loading during the transmission process of the gear, resulting in increased meshing deformation and transmission error, which will reduce the load-bearing capacity of the spur bevel gear pair and seriously affect its service life. Therefore, in actual engineering, the installation accuracy of the bevel gear pair should be improved as much as possible to ensure its service life.
Conclusions
In this paper, the following research is carried out to address the issue of efficient calculation of the time-varying meshing stiffness of spur bevel gears:
- Based on the back cone equivalence principle, the bevel gear is equivalent to a series of spur gears, and the energy method is used to calculate the meshing stiffness of each thin slice. In the calculation of the double-tooth meshing stiffness, the coupling effect between the tooth pairs during multi-tooth meshing is considered, and the finite element method is used to introduce the correction coefficient of the gear body stiffness to reduce the calculation error of the double-tooth meshing stiffness.
- By comparing the calculation results of the method in this paper, the analytical method, and the finite element calculation, it is shown that the error of the single-tooth meshing stiffness calculated by the method in this paper is about 3%, and the error of the double-tooth meshing stiffness is about 2%, and the calculation time is much less than the finite element calculation time, verifying the accuracy and efficiency of the method in this paper.
- By solving the angular displacement at the center point of each thin slice tooth pair of the spur bevel gear after loading, the meshing stiffness, the center point angular displacement of each thin slice, and the load distribution on the tooth surface under the error condition are calculated; compared with the finite element method, the accuracy of the meshing stiffness calculation under the error condition is verified.
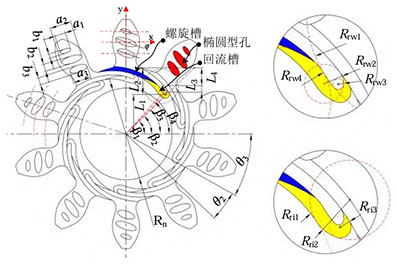