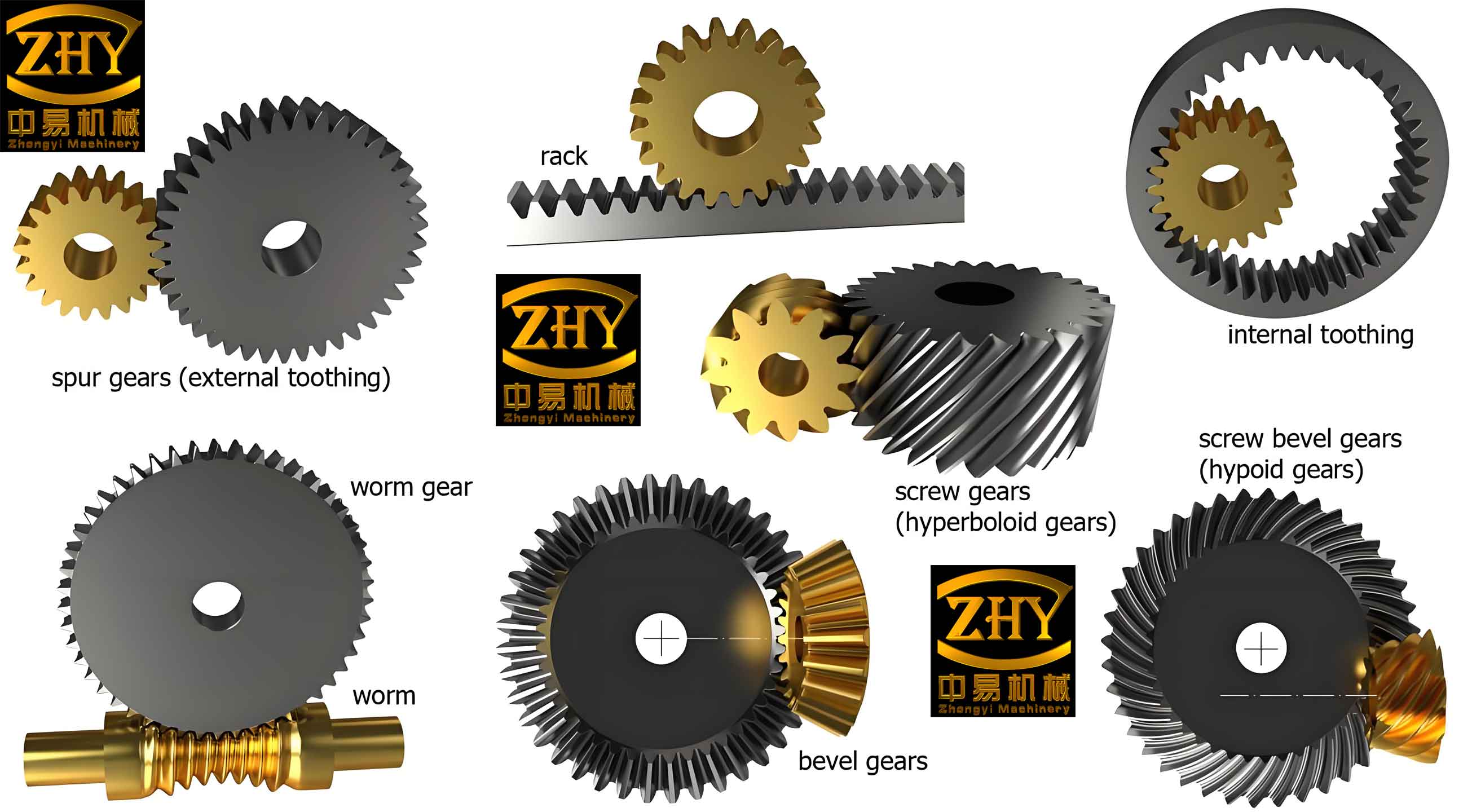
Introduction
Screw gear is integral components in various mechanical systems, known for their ability to transmit motion and power efficiently. Optimizing the geometry of screw gear is crucial for enhancing their load capacity, which directly impacts the performance, reliability, and longevity of mechanical systems. This article explores the key aspects of screw gear geometry, the factors influencing load capacity, and the methods to optimize gear design for improved performance.
Importance of Screw Gear Geometry
The geometry of screw gear, including parameters such as tooth profile, helix angle, pitch, and module, plays a significant role in determining their load capacity. Properly optimized geometry ensures efficient power transmission, minimizes stress concentrations, and enhances the overall durability of the gear system.
Key Geometric Parameters
- Tooth Profile: The shape of screw gear teeth, typically involute or trochoidal, affects the contact pattern and load distribution.
- Helix Angle: The angle between screw gear axis and the teeth, influencing the smoothness of operation and load capacity.
- Pitch: The distance between corresponding points on adjacent teeth, impacting screw gear’s strength and durability.
- Module: A measure of the size of screw gear teeth, related to the pitch diameter and number of teeth.
Table 1: Key Geometric Parameters of Screw Gears
Parameter | Description | Influence on Load Capacity |
---|---|---|
Tooth Profile | Shape of the gear teeth | Contact pattern, load distribution |
Helix Angle | Angle between gear axis and teeth | Smoothness of operation, load capacity |
Pitch | Distance between adjacent teeth | Strength, durability |
Module | Size of the gear teeth | Gear size, load handling capability |
Factors Influencing Load Capacity
Several factors influence the load capacity of screw gear, including material properties, lubrication, operating conditions, and manufacturing precision. However, the geometry of the gear remains a primary determinant.
Material Properties
The choice of material affects the strength, hardness, and wear resistance of screw gear. High-quality materials such as alloy steels and hardened bronze are preferred for their superior mechanical properties.
Lubrication
Proper lubrication reduces friction and wear, enhancing the load capacity and lifespan of screw gear. Advanced lubricants with additives can further improve performance under high-load conditions.
Operating Conditions
The load capacity of screw gear is also influenced by operating conditions such as speed, temperature, and load variations. Optimizing gear geometry helps mitigate the adverse effects of these conditions.
Manufacturing Precision
Precision in manufacturing ensures accurate tooth profiles and minimal deviations, which are critical for achieving optimal load capacity. Advanced manufacturing techniques such as CNC machining and additive manufacturing enable high precision and customization.
Methods for Optimizing Gear Geometry
Optimizing screw gear geometry involves several steps, including analytical calculations, finite element analysis (FEA), and experimental testing. The goal is to achieve a balance between load capacity, efficiency, and durability.
Analytical Calculations
Analytical methods involve mathematical calculations based on screw gear geometry and material properties. These calculations help estimate the load capacity and identify potential areas for improvement.
Finite Element Analysis (FEA)
FEA is a powerful tool for optimizing gear geometry. It allows for detailed analysis of stress distribution, deformation, and contact patterns under various loading conditions. By simulating different geometric configurations, FEA helps identify the optimal design parameters.
Experimental Testing
Experimental testing involves physical testing of prototype gears under controlled conditions. This provides valuable data on actual performance and helps validate analytical and FEA models. Testing also helps identify unforeseen issues and areas for further optimization.
Table 2: Methods for Optimizing Gear Geometry
Method | Description | Benefits |
---|---|---|
Analytical Calculations | Mathematical estimation of load capacity | Quick initial assessment, identifies potential improvements |
Finite Element Analysis (FEA) | Detailed simulation of stress and deformation | Precise optimization, visualizes stress distribution |
Experimental Testing | Physical testing of prototypes | Validates models, identifies real-world issues |
Case Study: Optimization of a Helical Screw Gear
Initial Design Parameters
The initial design of a helical screw gear involved the following parameters:
- Tooth Profile: Involute
- Helix Angle: 20 degrees
- Pitch: 5 mm
- Module: 2 mm
- Material: Alloy Steel
Analytical Calculations
Analytical calculations indicated a load capacity of 500 N, with stress concentrations observed at the tooth root and flank.
Finite Element Analysis
FEA was conducted to simulate screw gear under load. The analysis revealed high stress concentrations at specific points, suggesting the need for geometric modifications.
Optimization Process
- Adjusting Helix Angle: Increasing the helix angle to 25 degrees reduced stress concentrations and improved load distribution.
- Modifying Tooth Profile: Refining the tooth profile to a more curved shape further reduced stress at the tooth root.
- Increasing Module: Increasing the module to 2.5 mm enhanced the overall strength and load capacity.
Experimental Testing
Prototypes of the optimized gear were tested under controlled conditions. The results confirmed an improved load capacity of 650 N, with reduced stress concentrations and smoother operation.
Table 3: Comparison of Initial and Optimized Gear Parameters
Parameter | Initial Design | Optimized Design |
---|---|---|
Tooth Profile | Involute | Curved Involute |
Helix Angle | 20 degrees | 25 degrees |
Pitch | 5 mm | 5 mm |
Module | 2 mm | 2.5 mm |
Material | Alloy Steel | Alloy Steel |
Load Capacity | 500 N | 650 N |
Stress Concentration | High at tooth root | Reduced |
Future Trends in Gear Geometry Optimization
Advanced Computational Tools
The use of advanced computational tools such as artificial intelligence (AI) and machine learning (ML) is emerging in screw gear geometry optimization. These technologies can analyze vast amounts of data and identify optimal design parameters more efficiently than traditional methods.
Additive Manufacturing
Additive manufacturing, or 3D printing, enables the creation of complex gear geometries that were previously impossible to manufacture. This technology allows for greater design flexibility and the production of highly customized screw gear with enhanced performance characteristics.
Smart Materials
The development of smart materials that can adapt to changing loads and conditions holds promise for the future of screw gears. These materials can self-heal, change their properties, or provide real-time feedback on gear performance, further enhancing load capacity and reliability.
Table 4: Future Trends in Gear Geometry Optimization
Trend | Description | Potential Benefits |
---|---|---|
Advanced Computational Tools | AI and ML for design optimization | Efficient, data-driven optimization |
Additive Manufacturing | 3D printing of complex geometries | Greater design flexibility, customization |
Smart Materials | Materials that adapt to loads and conditions | Self-healing, real-time performance feedback |
Conclusion
Optimizing the geometry of screw gear is essential for enhancing their load capacity and overall performance. By focusing on key geometric parameters, leveraging advanced analytical and computational tools, and employing precise manufacturing techniques, engineers can design screw gear that meet the demanding requirements of modern machinery. Future trends such as AI-driven optimization, additive manufacturing, and smart materials promise to further revolutionize gear design, offering unprecedented levels of performance and reliability.