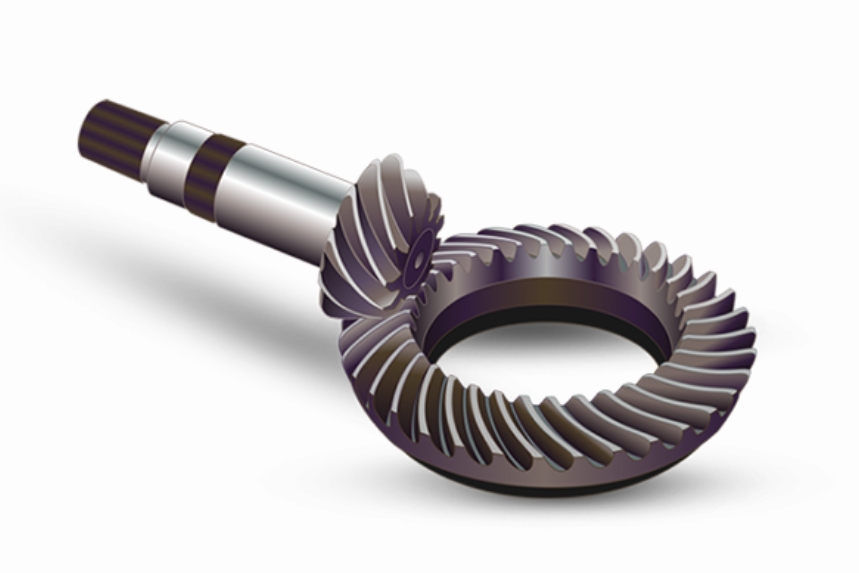
Optimizing spiral bevel gear designs for improved energy efficiency involves several key considerations, including gear geometry, materials, lubrication, and manufacturing processes. By focusing on these factors, gear manufacturers can develop gears that reduce energy losses and improve overall system efficiency. Here are some strategies for optimizing spiral bevel gear designs for energy efficiency:
1. Gear Geometry Optimization
- Profile Modification: Use profile modifications, such as tip relief and crowning, to improve tooth contact and reduce frictional losses.
- Optimized Tooth Profile: Design the tooth profile for smooth engagement and minimal sliding to reduce energy losses.
- Precision Machining: Use advanced machining techniques to ensure accurate spiral bevel gear tooth profiles and minimize surface roughness.
2. Material Selection
- High-Efficiency Materials: Select materials with low friction coefficients and high wear resistance to reduce energy losses.
- Lightweight Materials: Use lightweight materials to reduce inertia and improve overall system efficiency.
- Surface Treatments: Apply surface treatments, such as coatings and case hardening, to reduce friction and wear.
3. Lubrication
- High-Efficiency Lubricants: Use lubricants with low viscosity and high film strength to reduce frictional losses.
- Optimized Lubrication System: Design the lubrication system to ensure adequate lubrication while minimizing churning losses.
4. Manufacturing Processes
- High-Precision Manufacturing: Use advanced manufacturing processes, such as CNC machining and grinding, to ensure high gear accuracy and reduce losses.
- Quality Control: Implement stringent quality control measures to minimize manufacturing defects and ensure optimal spiral bevel gear performance.
5. Gear Pair Matching
- Precision Pairing: Match spiral bevel gear pairs with high precision to ensure optimal meshing and reduce energy losses.
- Optimized Contact Pattern: Adjust spiral bevel gear meshing contact pattern for optimal load distribution and reduced friction.
6. Noise and Vibration Reduction
- Noise-Optimized Design: Design spiral bevel gear to minimize noise generation, which can indicate energy losses.
- Vibration Damping: Use vibration-damping materials or structures to reduce energy losses due to vibration.
7. System Efficiency Analysis
- Simulation and Analysis: Use computer simulations and analysis tools to optimize spiral bevel gear designs for maximum efficiency.
- System Integration: Integrate spiral bevel gear into the overall system design to ensure compatibility and optimal performance.
By focusing on these strategies, gear manufacturers can optimize spiral bevel gear designs for improved energy efficiency, leading to reduced operating costs and environmental impact in various applications.