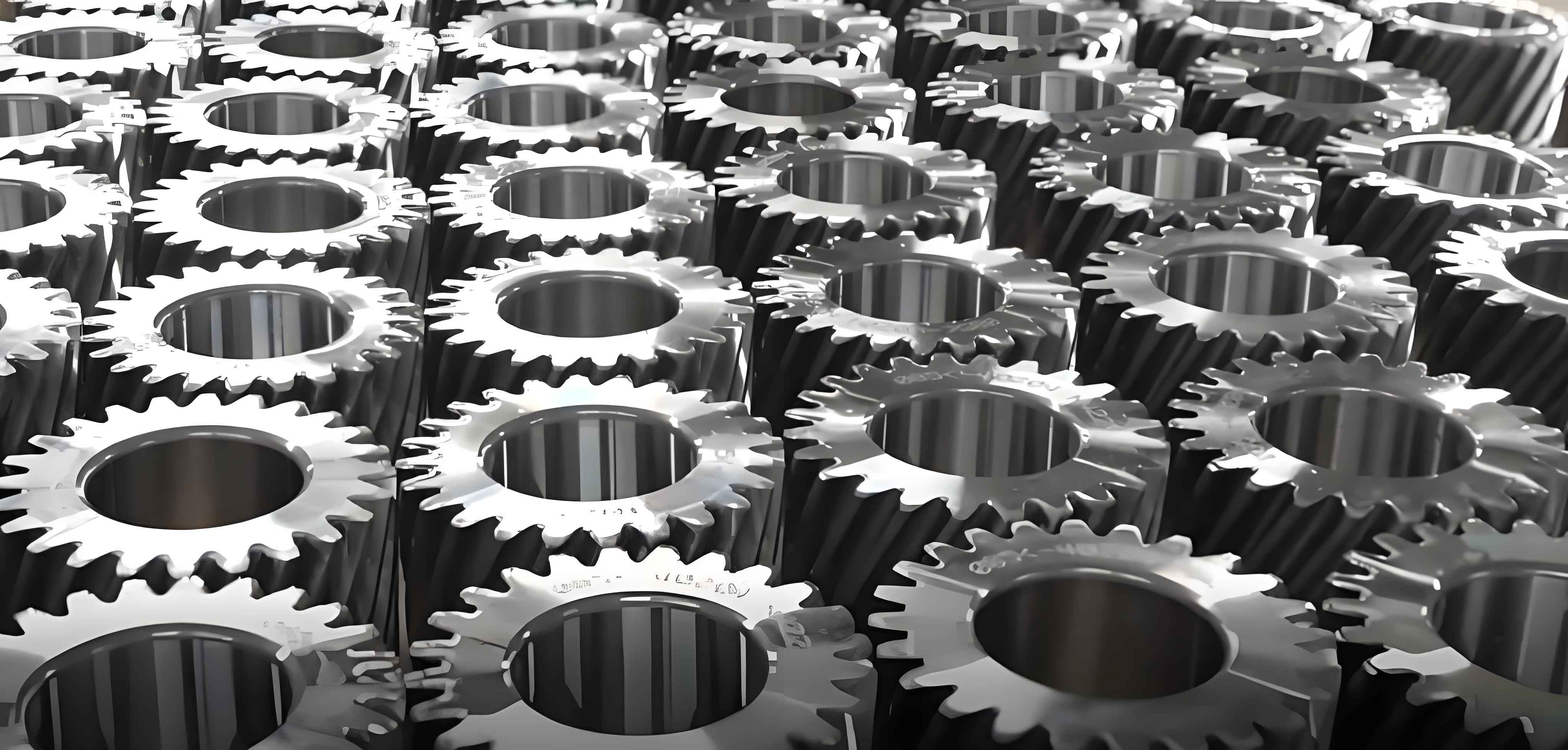
Introduction
Spur gear is widely used in high-performance applications due to their simplicity, efficiency, and reliability. Understanding the load distribution in high-performance spur gear is crucial for optimizing their design, enhancing their durability, and ensuring efficient power transmission. This article delves into the intricacies of load distribution in spur gear and explores methods to optimize it for high-performance applications.
What is Load Distribution in Spur Gear?
Load distribution in spur gear refers to the way in which the forces are shared among the gear teeth during operation. Uniform load distribution is essential for the longevity and performance of spur gear, as uneven loads can lead to premature wear, increased noise, and potential gear failure.
Factors Affecting Load Distribution in Spur Gear
- Tooth Profile: The shape and precision of spur gear teeth influence how the load is distributed.
- Gear Alignment: Proper alignment of spur gear ensures even load distribution across the teeth.
- Material Properties: The strength and flexibility of spur gear material affect load distribution.
- Manufacturing Tolerances: Precision in manufacturing reduces deviations that can lead to uneven load distribution.
- Lubrication: Adequate lubrication minimizes friction and ensures smooth load transfer.
- Operating Conditions: Variations in speed, torque, and temperature can impact load distribution.
Importance of Uniform Load Distribution
Uniform load distribution in spur gear is vital for several reasons:
- Increased Durability: Even load distribution reduces stress concentrations, extending the life of spur gear.
- Efficient Power Transmission: Uniform load distribution ensures efficient transfer of power, reducing energy losses.
- Reduced Noise and Vibration: Evenly distributed loads minimize noise and vibration, enhancing operational comfort.
- Preventive Maintenance: Understanding load distribution helps in predictive maintenance, preventing unexpected failures.
Methods to Optimize Load Distribution in Spur Gear
- Improved Tooth Profile Design
- Involute Profile: Using an involute tooth profile ensures a constant contact ratio, providing smooth and even load distribution.
- Profile Modifications: Implementing profile modifications like crowning or tip relief can reduce edge loading and improve load distribution.
- Precision Manufacturing
- High-Precision Machining: Utilizing high-precision machining techniques reduces manufacturing errors and ensures uniform tooth geometry.
- Quality Control: Rigorous quality control processes help in identifying and correcting deviations that affect load distribution.
- Proper Gear Alignment
- Accurate Assembly: Ensuring accurate assembly and alignment of spur gear minimizes misalignment issues.
- Alignment Adjustments: Regular alignment checks and adjustments help maintain optimal load distribution.
- Material Selection
- High-Strength Materials: Using high-strength materials with good fatigue resistance enhances load-carrying capacity.
- Composite Materials: Incorporating composite materials can improve flexibility and load distribution characteristics.
- Lubrication Management
- Adequate Lubrication: Using appropriate lubricants reduces friction and wear, ensuring smooth load transfer.
- Regular Lubrication Maintenance: Regularly checking and maintaining lubrication levels helps in maintaining uniform load distribution.
Comparative Analysis: Methods for Optimizing Load Distribution
Method | Effectiveness | Cost | Complexity |
---|---|---|---|
Improved Tooth Profile Design | High | Moderate | High |
Precision Manufacturing | High | High | High |
Proper Gear Alignment | High | Low | Low |
Material Selection | Moderate | Moderate | Moderate |
Lubrication Management | Moderate | Low | Low |
Best Practices for Ensuring Uniform Load Distribution
To achieve optimal load distribution in high-performance spur gear, consider the following best practices:
- Holistic Design Approach: Integrate considerations of tooth profile, material selection, and manufacturing processes during the design phase.
- Regular Maintenance: Implement a maintenance schedule that includes alignment checks, lubrication management, and inspection of gear teeth.
- Continuous Monitoring: Use condition monitoring tools to track the performance and load distribution of spur gear in real-time.
- Employee Training: Train personnel on the importance of load distribution and proper maintenance techniques.
- Invest in Quality: Use high-quality materials and precision manufacturing processes to ensure optimal gear performance and load distribution.
Summary Table: Key Factors in Load Distribution Optimization
Key Factor | Description |
---|---|
Tooth Profile Design | Use involute profiles and profile modifications for even load distribution |
Precision Manufacturing | High-precision machining and quality control ensure uniform tooth geometry |
Proper Gear Alignment | Accurate assembly and regular alignment checks prevent misalignment |
Material Selection | High-strength and composite materials improve load-carrying capacity |
Lubrication Management | Adequate and regular lubrication maintenance ensures smooth load transfer |
Conclusion
Understanding and optimizing load distribution in high-performance spur gear is essential for ensuring their efficiency, durability, and reliability. By focusing on improved tooth profile design, precision manufacturing, proper gear alignment, material selection, and effective lubrication management, industries can achieve uniform load distribution. This not only enhances the performance of spur gear but also extends their lifespan, reduces maintenance costs, and ensures efficient power transmission.
In conclusion, a comprehensive approach to load distribution in spur gear is vital for maximizing their potential in high-performance applications. By prioritizing these strategies and best practices, industries can enjoy the benefits of reliable, efficient, and long-lasting spur gear systems.