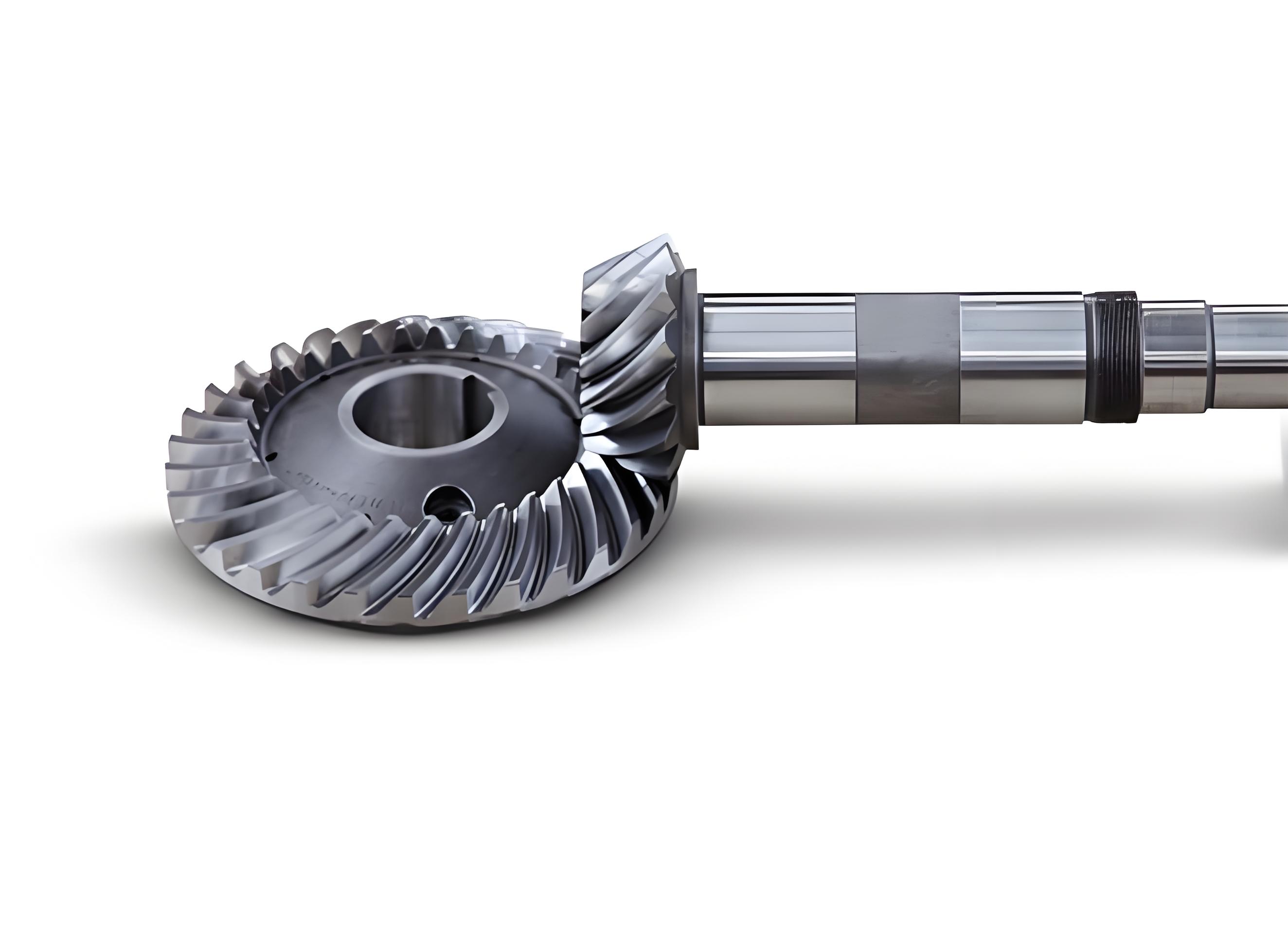
Abstract
Tooth profile design is a critical factor in the performance of spiral bevel gear, influencing their load-carrying capacity, efficiency, noise, and wear characteristics. This review explores advanced techniques and methodologies for optimizing tooth profile design to enhance the overall performance of spiral bevel gear.
Introduction
Spiral bevel gear is essential components in various high-performance applications due to their ability to transmit torque between intersecting shafts with high efficiency and minimal noise. The tooth profile design significantly affects spiral bevel gear’s performance, including its load distribution, stress concentration, and wear behavior. Optimizing this design is crucial for achieving superior gear performance.
Traditional Tooth Profile Design
- Standard Tooth Profiles: Involves using conventional geometric shapes based on industry standards (e.g., AGMA, ISO).
- Limitations: Often results in suboptimal load distribution and higher stress concentrations, leading to increased wear and potential failure.
Advanced Optimization Techniques
- Finite Element Analysis (FEA)
- Stress Analysis: Using FEA to analyze stress distribution across spiral bevel gear teeth and identify areas of high stress concentration.
- Optimization: Iteratively modifying the tooth profile to achieve uniform stress distribution and reduce peak stresses.
- Computer-Aided Design (CAD) and Computer-Aided Manufacturing (CAM)
- Precision Modeling: Leveraging CAD software to create precise 3D models of optimized tooth profiles.
- CAM Integration: Ensuring that the optimized designs are manufacturable with available CAM technologies, maintaining high accuracy and repeatability.
- Genetic Algorithms (GA)
- Optimization Process: Utilizing GA to explore a wide range of tooth profile variations, selecting and refining designs based on performance criteria.
- Multivariable Optimization: Considering multiple factors such as load distribution, stress concentration, and manufacturing constraints simultaneously.
- Topology Optimization
- Material Distribution: Optimizing the distribution of material within spiral bevel gear tooth to achieve desired performance characteristics.
- Innovative Designs: Producing non-conventional tooth profiles that offer improved performance compared to traditional designs.
- Surface Engineering Techniques
- Micro-Geometry Modifications: Implementing micro-geometry modifications such as crowning and end relief to enhance load distribution and reduce edge loading.
- Surface Finishing: Applying advanced surface finishing techniques to achieve smoother tooth surfaces, reducing friction and wear.
Case Studies and Applications
- Automotive Gears
- Load Capacity: Optimized tooth profiles have led to significant improvements in load capacity and durability in automotive differential spiral bevel gear.
- Noise Reduction: Enhanced tooth profiles contribute to quieter operation, a critical factor in passenger vehicles.
- Aerospace Gears
- Weight Reduction: Optimization techniques have enabled the design of lighter spiral bevel gear without compromising strength, essential for aerospace applications.
- High Reliability: Ensuring high reliability and performance under extreme operational conditions.
- Industrial Machinery
- Efficiency Improvements: Optimized spiral bevel gear in industrial machinery have shown marked improvements in efficiency and lifespan, reducing maintenance costs.
- Stress Reduction: Effective stress distribution has minimized the risk of spiral bevel gear failure in heavy-duty applications.
Challenges and Future Directions
- Computational Complexity
- Resource Intensive: Advanced optimization techniques, especially those involving FEA and GA, require significant computational resources.
- Solution: Development of more efficient algorithms and increased computational power.
- Manufacturing Precision
- Tolerance Management: Ensuring that optimized tooth profiles can be manufactured within tight tolerances.
- Solution: Advances in CNC machining and additive manufacturing techniques.
- Integration with Digital Twins
- Real-Time Monitoring: Incorporating real-time data from operational spiral bevel gear systems into the optimization process.
- Predictive Maintenance: Using digital twin technology to predict wear and optimize tooth profiles dynamically.
Conclusion
Optimizing tooth profile design is essential for enhancing the performance of spiral bevel gear. Advanced techniques such as FEA, genetic algorithms, and topology optimization have revolutionized the design process, leading to spiral bevel gear that are more efficient, durable, and reliable. Continued innovation in this field promises further improvements, contributing to the development of high-performance spiral bevel gear system for a wide range of applications.
References
- Journal of Mechanical Design: Articles on finite element analysis and genetic algorithms for spiral bevel gear optimization.
- International Journal of Advanced Manufacturing Technology: Studies on CAD/CAM integration and surface engineering techniques.
- Tribology Transactions: Research on micro-geometry modifications and their impact on spiral bevel gear performance.
- Journal of Aerospace Engineering: Papers on optimized spiral bevel gear designs for aerospace applications.
This review provides a comprehensive overview of the methodologies and advancements in optimizing tooth profile design for spiral bevel gear, serving as a valuable resource for researchers, engineers, and industry professionals.