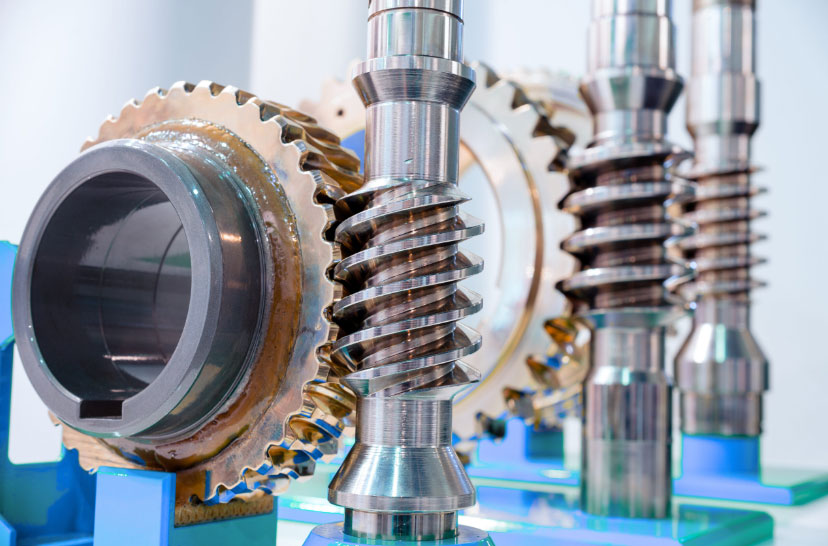
Predictive maintenance (PdM) techniques for worm gear in industrial applications aim to foresee potential failures and reduce unplanned downtime by monitoring and analyzing various indicators of gear health. Here are some key techniques used:
- Vibration Analysis:
- Principle: Vibration analysis monitors the vibrations produced by the worm gear during operation. Changes in vibration patterns can indicate wear, misalignment, imbalance, or other issues.
- Tools: Accelerometers and vibration sensors are commonly used to collect data, which is then analyzed using specialized software.
- Oil Analysis:
- Principle: Analyzing the lubricant oil can provide insights into the condition of the worm gear. The presence of metal particles, contaminants, or changes in viscosity can indicate wear or impending failure.
- Tools: Spectrometric analysis, particle counters, and viscosity tests are used to analyze oil samples.
- Acoustic Emission Monitoring:
- Principle: This technique involves monitoring the high-frequency sound waves produced by the worm gear. Acoustic emissions can detect cracks, pitting, and other forms of wear at an early stage.
- Tools: Acoustic sensors and signal processing equipment are used to detect and analyze the emissions.
- Thermography:
- Principle: Thermography involves monitoring the temperature of the worm gear using infrared cameras. Abnormal temperature rises can indicate friction, lubrication issues, or other mechanical problems.
- Tools: Infrared cameras and thermal imaging software are used for real-time monitoring.
- Ultrasonic Testing:
- Principle: Ultrasonic testing detects flaws and wear by sending high-frequency sound waves through the worm gear. Changes in the reflected sound waves can indicate internal defects or surface degradation.
- Tools: Ultrasonic transducers and analysis software are employed to perform these tests.
- Electrical Signature Analysis (ESA):
- Principle: ESA monitors the electrical signals of motors and other electrical components connected to the worm gear. Variations in current and voltage can indicate mechanical issues within worm gear system.
- Tools: Current and voltage sensors along with ESA software are used to capture and analyze the electrical signals.
- Machine Learning and AI:
- Principle: Advanced algorithms and machine learning models can analyze large datasets from various sensors to predict gear failures. These models can identify patterns and anomalies that are not easily detectable by traditional methods.
- Tools: Data acquisition systems, machine learning frameworks, and predictive maintenance platforms.
- Wear Debris Analysis:
- Principle: Examining the debris collected from the worm gear’s lubrication system can provide insights into the type and extent of wear.
- Tools: Microscopy and analytical ferrography are used to study wear particles.
Integrating Predictive Maintenance in Industrial Applications
To effectively implement predictive maintenance for worm gear in industrial settings, consider the following steps:
- Baseline Data Collection: Gather initial data on the worm gear’s performance under normal operating conditions to establish baseline measurements.
- Sensor Installation: Equip the worm gear system with appropriate sensors for continuous monitoring of vibration, temperature, oil condition, and other relevant parameters.
- Data Analysis: Use specialized software and algorithms to analyze the collected data, identifying trends and potential issues.
- Threshold Setting: Establish acceptable ranges for monitored parameters based on baseline data and manufacturer specifications.
- Regular Inspections: Conduct regular inspections and maintenance based on the predictive insights provided by the monitoring systems.
- Integration with Maintenance Management Systems: Connect the PdM system with your existing maintenance management software to automate alerts, schedule maintenance activities, and keep records of gear health.
Implementing these predictive maintenance techniques can significantly enhance the reliability and lifespan of worm gear in industrial applications, leading to improved operational efficiency and reduced maintenance costs.