Introduction
In the use of hobs, it was found that there was a significant difference in processing quality and life between imported and domestic hobs. After several comparisons, it was known that The service life of the mouth hob can reach more than twice that of the domestic hob, and the service life of the imported hob after returning to the original factory for grinding is about 90% of the new tool, but the same After being ground by domestic manufacturers, the actual grinding accuracy of the tool is not lower than the original tool, and some accuracy is even better than the original tool, but the processing quality and The lifespan of the tool is significantly reduced. After microscopic observation of the tool, it was found that there are significant differences in the edge treatment between imported and domestic tools. The imported hob has obvious passivation marks on the edge, with uniform size of the passivation fillet, consistent edge quality, and few microscopic defects and grinding burrs, and its coating has good adhesion. When used, the tool cuts quickly and is wear-resistant, and its performance is significantly better than domestic tools. Most of the production hobs have not undergone passivation treatment or have only been manually polished with oilstones; most of the regrinding gear hobs have not undergone passivation treatment, and even have not undergone manual blunt treatment. Through electron microscopy observation, it was found that there are defects such as grinding burrs and microcracks at the edge, which not only affect the adhesion of the coating, but also cause increased wear and chipping of the tool during the hobbing process. The domestic emphasis on passivation of the hob edge is generally low, which will seriously restrict the improvement of tool quality. In order to improve tool durability and fundamentally reduce the cost of hobbing, the author conducted a large number of hob edge passivation and cutting experiments through theoretical research, deepening the research and understanding of hob edge passivation, improving the durability of the hob, fundamentally reducing the cost of tool procurement, and providing a basis for hob passivation research.
Confirmation of passivation method
The external dimensions of hob are large, and the material and structure are complex and diverse. According to statistics, the outer diameter range of gear hob is about ϕ50-ϕ400mm, and the length range is about 50-500mm. The tool structure includes whole, insert, welding, etc. The tool material includes high-speed steel, high-performance high-speed steel, powder metallurgy high-speed steel, etc. Therefore, a passivation method with strong inclusiveness and high cost performance must be selected for the passivation of gear hob. Technical communication with passivation equipment manufacturers, investigation and research with relevant tool manufacturers and coating manufacturers, and finally confirmation of using dry sandblasting Dry sandblasting uses compressed air to form a power that allows abrasives to enter the sandblasting tube through a sand outlet valve, and then the abrasives are sprayed onto the processed surface through a nozzle to achieve sandblasting. Compressed air is both the power supply and the acceleration power of the jet. Dry sandblasting machines can control the passivation effect by adjusting pressure values, changing the material and particle size of the sand, and changing the sandblasting time. Compared to other passivation methods, sandblasting is the most thorough, versatile, and efficient passivation method, and dry sandblasting is easier to operate, with recyclable sand particles and lower costs.
Passivation medium
There are many kinds of commonly used sandblasting sand: carborundum, alumina, white corundum, brown corundum, etc. White corundum has strong cutting force and can be used for Remove metal burrs and have grinding and polishing effects on the surface. Considering that the tool needs to be coated after passivation, white corundum is selected as the passivation material Through sandblasting tests on scrapped tools, it was found that if larger particles of sand are used, there is a high risk of over-passivation of the tool, which will result in loss of cutting performance. If the particle size is too small, the passivation time will be too long, and the passivation effect may not be achieved at all. Through a series of tests, The selected passivation medium for the hob has a mesh count of 400#. The sandblasting pressure and duration of the sandblasting machine can directly affect the size of the passivation fillet; the sandblasting pressure of the dry sandblasting machine selected is set at 2.5-3MPa. Repeated tests were conducted on scrapped tools to investigate the relationship between sandblasting time and fillet size under a certain spray distance.
Gear hob edge form
There are several types of cutting tool edges: sharp edges, chamfered edges, rounded edges, and other major categories. Among them, sharp edges refer to the sharp edges naturally formed by the intersection of the front and rear cutting surfaces of the tool. Cutting tool edges generally have a front and rear angle, and a schematic diagram of the cutting edge section. The shaded area refers to the part of the cutting edge with microscopic defects and burrs. The purpose of passivation is to eliminate microscopic defects at the cutting edge, that is, to smooth out the shaded area to achieve consistency, defect-free or reduced defects at the cutting edge.
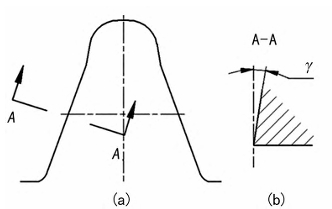
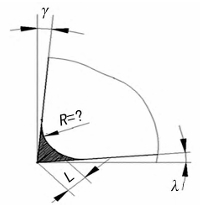
In order to understand the actual condition of the edge of the gear hob after grinding and obtain the size of the passivation fillet, it is necessary to conduct
Detection.
The inspection results of the hob edge show that the edge is generally serrated, and the distance between the peaks and valleys of the serration is called the microscopic defect size, which is generally between 0.005 and 0.015 mm.
(2) Theoretical calculation of the blunt fillet of the hob
Theoretical calculation of the blunt rounded corner of the top edge of the hob: The back angle of the top edge of the hob is generally taken as 10° to 12°, and the rake angle is 0°.
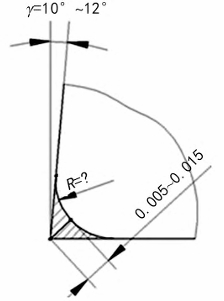
In summary, the theoretical value of the passivation fillet for the top edge of the hob is between 0.085 and 0.02mm, and the theoretical value of the passivation fillet for the side edge is between 0.01 and 0.03mm. Since the top and side edges of the hob are passivated together, considering comprehensively, when the microscopic detection value of the hob’s edge defects is between 0.005 and 0.015mm, the theoretical range of the passivation fillet is between 0.085 and 0.02mm. Through theoretical analysis and calculation of the tool’s cutting edge, technical communication with tool manufacturers, and testing of purchased tools and outsourced grinding and coating tools, as well as reference to the passivation fillet of imported tool cutting edges, the passivation fillet implementation was initially confirmed.
Results of tool trial
To verify the effectiveness of tool passivation, cutting tests were conducted on different modulus hobs. Taking the cutting of a 14-modulus hob as an example, the parameters of the test parts are listed in Table 7. With consistent cutting parameters, the test results of the passivated hob were obtained. From the test results, it can be seen that the cutting performance and durability of the passivated hob have been greatly improved.
Data statistics from tool tests show that most tools are durable degrees have been significantly improved, and the life expectancy has increased by more than 30%; some small The modulus tool has achieved a more than 50% improvement.
Conclusion
The technology of tool edge passivation is one of the effective measures to improve tool life, reduce tool consumption, and increase processing efficiency. This article focuses on the hob Theoretical analysis of the passivation of the cutting edge of the hob has been conducted, and tool tests have demonstrated that the passivation of the cutting edge of the hob can effectively improve the durability and lifespan of the tool Previously, the passivation of hob was still in the exploratory stage, and it was found in the experiment that there was a significant difference in the passivation effect between different tools. Therefore, increasing research on the passivation technology of hob is of great significance for improving the processing performance of domestic hobs and shortening the gap with foreign tools.