1. Macro-examination
The fracture morphology of the failed large helical gear teeth is analyzed. As shown in Figure 1, it can be seen that all the failed teeth break from the root of the teeth, and there is a residual section not broken at the large end of the gear. The fracture is concave.The magnetic particle test on the failed large helical gear shows that, as shown in Figure 2, there are cracks parallel to the root of the tooth convex surface at the root of some unbroken teeth, and the shape of the cracks is the same as that of the fracture line in the broken tooth section in Figure 2.
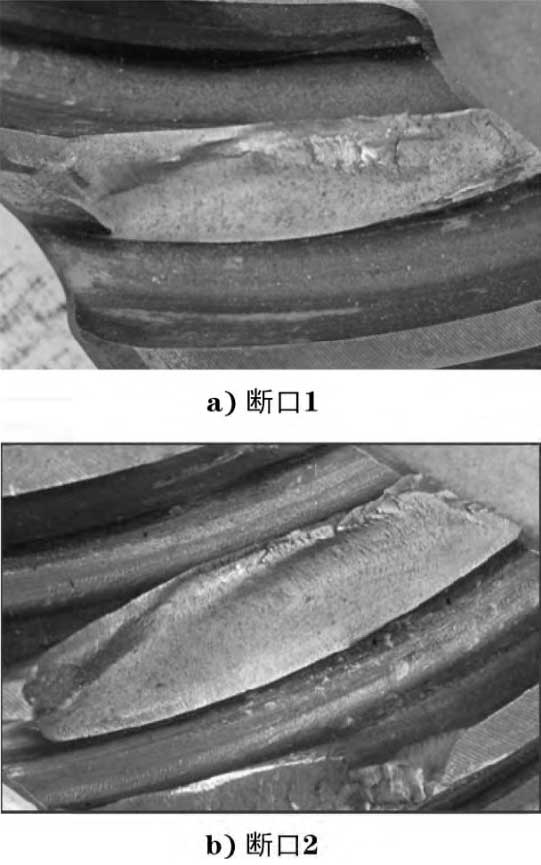
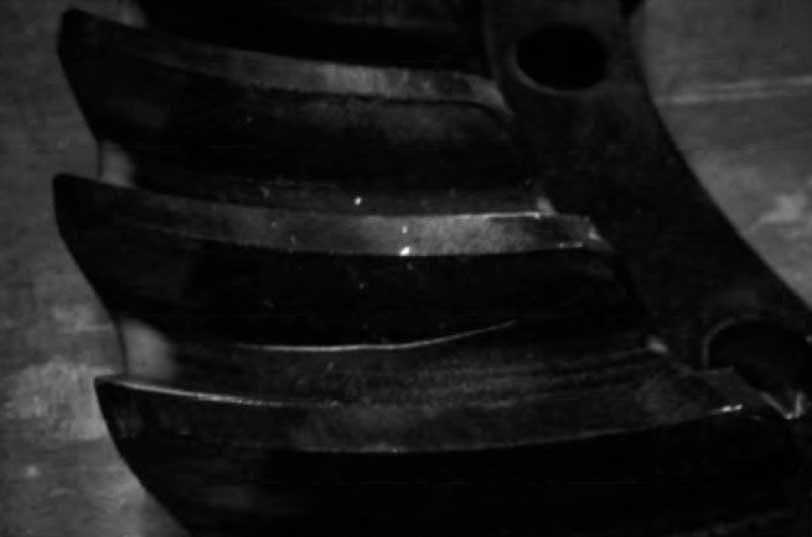
The cracks are slightly higher at the small end and slightly lower at the large end, which again indicates that the cracks originate at the root of the tooth.In order to obtain a more exact crack initiation position, the failed large helical gear is split perpendicular to the crack length. It can be seen from the observation after grinding and polishing that the crack originates at the transition position between the fillet of the root and the tooth surface, as shown in Figure 3.
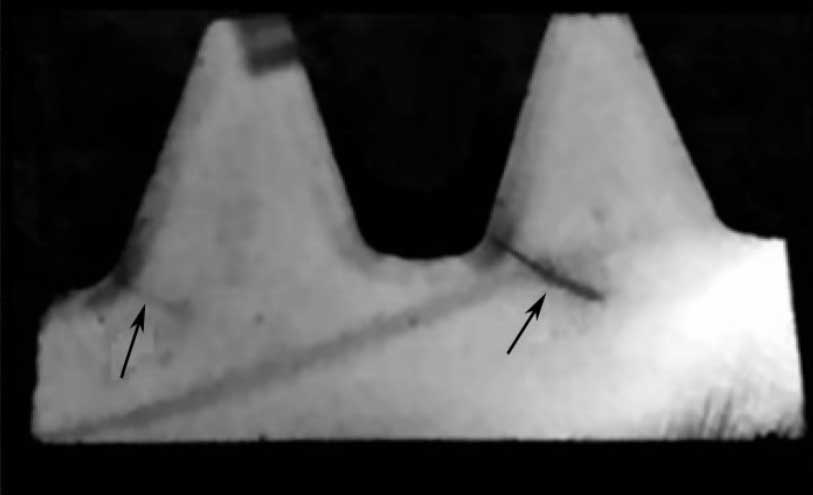
2. Fracture analysis
Samples were cut from the broken teeth and the fracture morphology was observed by SEM. The results are shown in Fig. 5.You can see that there are many fatigue arcs on the fracture.Fatigue arc is the most basic feature of fatigue fracture, so it can be determined that the failure mode of large helical gear is bending fatigue fracture.It can also be seen by SEM that the direction of fatigue arc is basically perpendicular to the direction of tooth width on the side close to the tooth root, while in the middle of the teeth, the direction of fatigue arc is basically parallel to the direction of tooth width.It is generally believed that the normal direction of the fatigue arc is the propagation direction of the fatigue crack at this point.Therefore, it can be judged that fatigue crack extends along the tooth width at the root and along the tooth thickness inside the gear teeth.
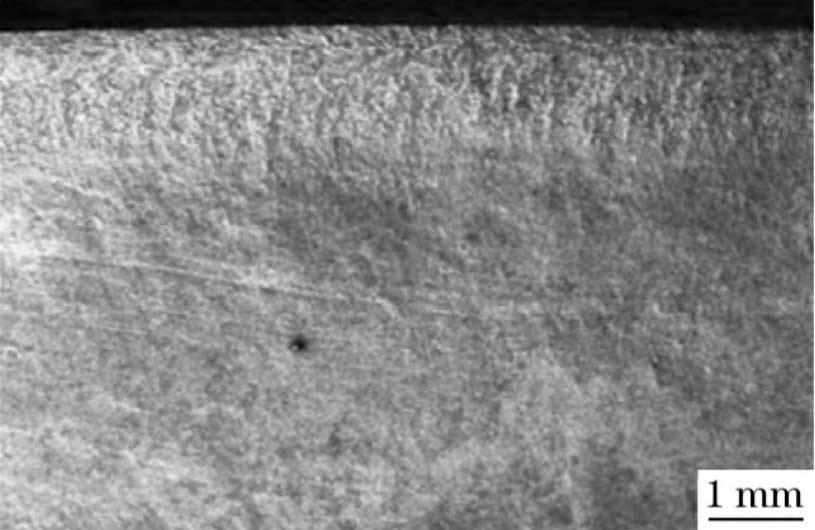
3. Chemical Composition Analysis
Three failed large helical gears were randomly selected for chemical composition analysis.It can be seen that the chemical composition of each failed gear meets the technical requirements of 20CrMnTi steel in GB/T 3077-1999 Alloy Structural Steel.
4. Hardness and metallographic examination
The surface hardness and core hardness of the above three randomly selected failed large helical gears were tested.It can be seen that the surface hardness of the failed large helical gears meets the technical requirements of JB/T 6041-2013, while the core hardness is low or just meets the lower limit of the standard requirements.Carbide grade, martensite + residual austenite grade and core ferrite grade in the microstructure of the failed gear were graded respectively.It can be seen that the grade of carbide, martensite + residual austenite and ferrite in the core in the microstructures meet the technical requirements of GB/T 8539-2000 General Provisions for Quality Inspection of Gear Materials and Heat Treatment.