Accurate three-dimensional geometric model of cylindrical helical gear is the precondition of establishing heat transfer-deformation coupling finite element model.The basic parameters of cylindrical helical gear studied in this paper are: mn=2 mm, number of teeth Z=18, pressure angle a=20 degrees, helical angle beta=16 degrees and tooth width B=20mm.A three-dimensional model of the cylindrical helical gear created by the three-dimensional modeling software Pro/Engineer Wildefire is shown in Figure 1(a).
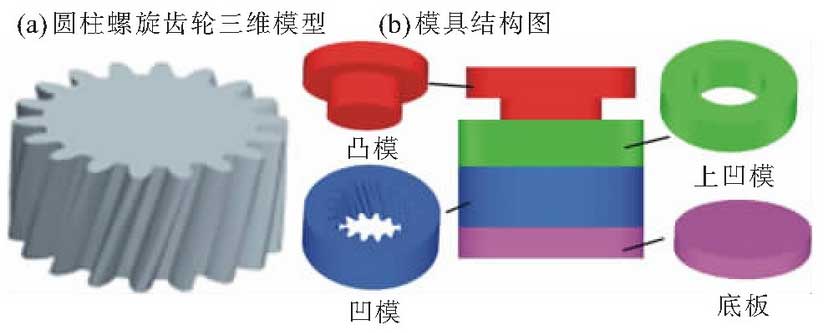
In the deformation-heat transfer coupling finite element model established in this paper, the billet metal is 20CrMnTiH, and the material constitutive equation [11] is obtained by thermal compression experiment by Feng et al.In order to reduce the upsetting deformation of the blank during the forming process, the diameter of the blank is as close as possible to the top circle of the concave die teeth and is designed to be accurate 32mm.According to the principle of volume invariance, the blank size is quasi-32 mm x 26.8 mm, which is defined as plastic body, and the die material is H13 steel, which is defined as rigid body.The ambient temperature, mold preheating temperature and initial billet temperature are 20, 250 and 1000 C respectively. The convection heat transfer coefficient between the free surface of billet or mold and the external environment is 0.02N/(s.mm.C) and that between the billet and the contact surface of the mold is 11N/(s.mm.C).A constant shear friction model is used between the blank and the die with a friction coefficient of 0.25 and a downward speed of 10 mm/s for the punch.The specific die structure used for the model is shown in Figure 1(b).