Precision engineering plays a crucial role in the design and manufacturing of hypoid gears, especially when dealing with challenging gear meshing configurations. The offset nature of hypoid gears presents unique challenges that require precise engineering solutions to ensure smooth and efficient gear performance. Here are some key aspects of precision engineering with hypoid gears:
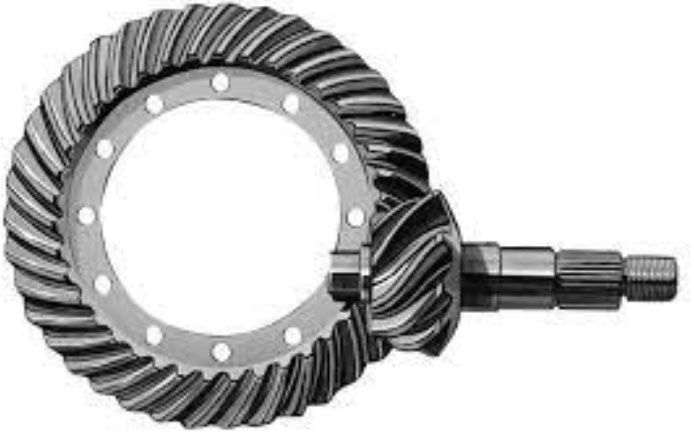
- Gear Design and Modeling: Precision engineering begins with the accurate design and modeling of hypoid gears. Advanced computer-aided design (CAD) software is used to create 3D models of the gear geometry, taking into account the specific offset and spiral characteristics. These models help in simulating gear meshing, analyzing contact patterns, and predicting potential issues.
- Tooth Profile Optimization: Achieving the correct tooth profile is critical in hypoid gears. Precision engineering involves optimizing the tooth geometry to ensure proper tooth contact and minimize stress concentration. This process requires careful consideration of factors such as pressure angle, helix angle, and tooth thickness to achieve the desired performance and durability.
- Manufacturing Process Selection: Choosing the appropriate manufacturing process is vital in precision engineering for hypoid gears. Methods such as face milling, face hobbing, and face grinding are commonly employed. Each method has its advantages and limitations, and selecting the most suitable process depends on factors like production volume, gear size, and accuracy requirements.
- Quality Control and Inspection: Rigorous quality control measures are essential to maintain precision in hypoid gear manufacturing. Advanced inspection techniques, such as coordinate measuring machines (CMMs) and gear analyzers, are used to verify gear dimensions, tooth profile, and tooth contact pattern. This helps ensure that the gears meet the required specifications and tolerances.
- Material Selection: Choosing the right material for hypoid gears is crucial for achieving precision and durability. High-quality steel alloys with excellent mechanical properties, such as heat-treated carburized steel, are commonly used in precision hypoid gears.
- Surface Finish and Gear Finishing: Achieving the desired surface finish is vital for reducing friction and wear. Precision engineering involves using specialized gear finishing techniques, such as honing and superfinishing, to achieve the required surface quality.
- Collaborative Engineering Approach: Precision engineering for hypoid gears often involves a collaborative approach between gear designers, manufacturers, and end-users. Engineers work closely to optimize gear designs, ensure manufacturability, and address any issues that may arise during production or use.
- Continuous Improvement: Precision engineering is an iterative process that involves continuous improvement. Data gathered from gear testing and real-world performance is used to refine gear designs and manufacturing processes, leading to even higher levels of precision and performance.
By incorporating these precision engineering practices, manufacturers can produce high-quality hypoid gears capable of handling challenging gear meshing configurations. The result is a more efficient, quieter, and durable gear solution that meets the demanding requirements of modern engineering applications.