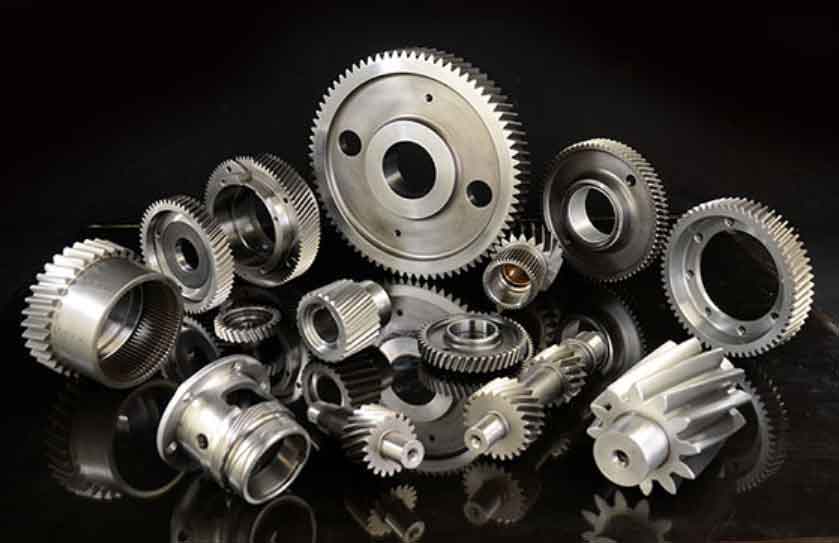
The manufacturing process of spiral bevel gears involves several steps to achieve the desired tooth geometry and ensure the gears’ precise operation. The process typically includes gear design, blank preparation, gear cutting, heat treatment, and final finishing. Here’s a step-by-step overview of the manufacturing process:
1. Gear Design:
The first step in manufacturing spiral bevel gears is to create a detailed gear design. This involves determining the gear specifications, such as pitch diameter, number of teeth, helix angle, and tooth profile. Computer-aided design (CAD) software is commonly used to generate the gear geometry and tooth profiles.
2. Blank Preparation:
The gear blank is prepared from a suitable material, typically steel or alloy steel. The gear blank is a cylindrical or conical shape that serves as the starting material for the gear cutting process. The blank’s size and shape depend on the gear design and the application requirements.
3. Gear Cutting:
The gear cutting process involves machining the gear teeth into the blank. There are several methods to cut the teeth of spiral bevel gears, including:
a. Milling:
In gear milling, a specialized milling machine with a rotating cutter is used to cut the gear teeth. This process is suitable for low to medium production volumes.
b. Hobbing: Gear hobbing is a common method for high-volume production. A gear hob, a cutting tool with helical teeth, is used to generate the gear teeth by rotating the gear blank and hob simultaneously.
c. Gear Shaping: In gear shaping, a gear shaping machine is used to cut the gear teeth by reciprocating the cutting tool across the gear blank.
4. Heat Treatment:
After the gear cutting process, the gears undergo heat treatment to improve their mechanical properties and ensure uniform hardness. Heat treatment processes, such as carburizing, quenching, and tempering, are used to achieve the desired hardness and durability of the gears.
5. Final Finishing:
After heat treatment, the gears undergo final finishing operations to achieve the required surface smoothness and dimensional accuracy. Grinding is often used to finish the gear teeth and ensure precise gear meshing.
6. Quality Control:
Throughout the manufacturing process, quality control measures are essential to ensure the gears meet the required specifications. Gear measurements and inspections are performed to check tooth profile accuracy, tooth contact pattern, and gear runout.
7. Assembly and Testing (If Required):
In some cases, the spiral bevel gears may need to be assembled into gearboxes or other components for testing and verification of their performance.
8. Surface Treatment (Optional):
Depending on the application and requirements, the gears may undergo surface treatments such as coating or plating to enhance their corrosion resistance and durability.
In conclusion, the manufacturing process of spiral bevel gears involves precision machining, heat treatment, and finishing steps to create high-quality gears capable of transmitting power efficiently and reliably in various engineering applications.