In addition to the commonly used hot precision forging, there are warm precision forging, cold precision forging and powder sintering forging processes. The heating temperature of hot precision forging is 1000 ° c-1150 ° C, the heating temperature of warm precision forging is 700 ° c-800 ° C, and the cold forging is carried out at room temperature. Due to the advanced technology in Japan and Germany, different precision forging processes can be adopted according to the conditions of spur bevel gear products. Warm forging and cold forging processes are widely used. In China, the hot precision forging technology is more common. The straight bevel gear with high precision requirements will be subject to cold finishing or warm precision pressing after hot precision forging, and the simple warm forging is rarely used.
1). Hot precision forging process
China started the development and application of hot precision forging gear technology in the late 1960s, and the technology began to mature in the middle and late 1980s. Its technology was independently developed by China. In 1970, Shanghai first carried out the hot precision forging process forming test on the differential planetary gear of American Daqi t234 automobile, which was successful in 1972. The following year, it began mass production. Therefore, Shanghai Automobile Gear General Factory has gained a lot of successful manufacturing experience, which has laid a foundation for the application and development of forging technology. In 1974, Shandong University of technology first applied the precision forging process to the mass production of tractor differential bevel gears. From the late 1970s to the mid 1980s, China has successfully researched the precision forging process of spiral bevel gears for automobiles and motorcycles, which has been basically popularized in China.
The hot forging process of spur bevel gear is shown in Figure 1.
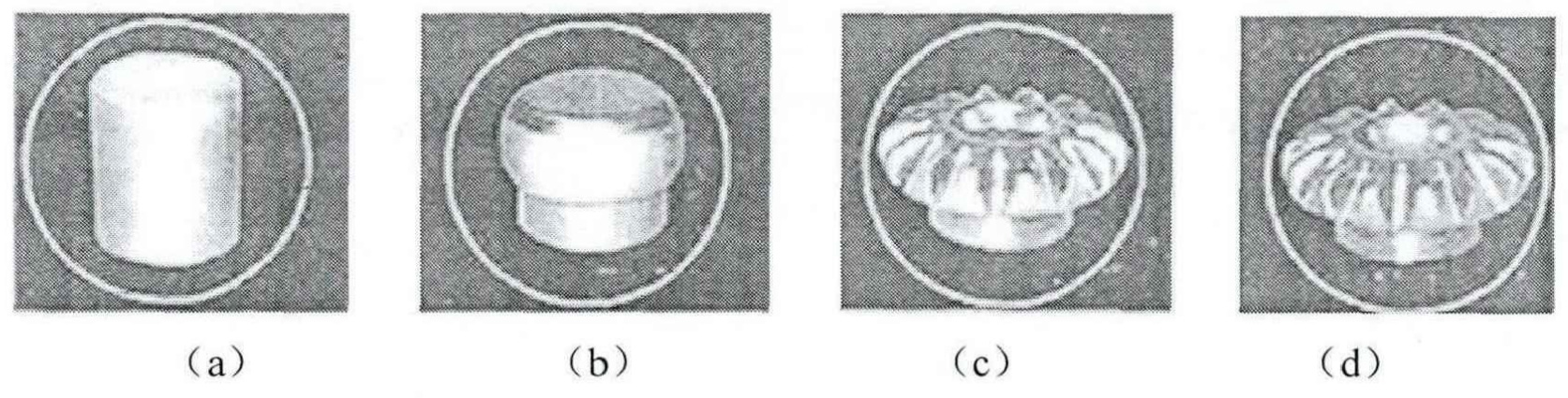
The earliest hot forging process of spur bevel gear is called “two fires and two forgings”. Due to twice heating, there is an additional heating process, resulting in higher production costs; In addition, efficient and controllable heating equipment cannot be used for secondary heating. Therefore, the former Shandong University of technology developed the “one fire two forging” process. The “one fire two forging” process only needs one heating. Compared with the “two fire two forging” process, it shortens the process flow, saves energy, improves production efficiency and reduces production costs. It is widely used in China.
2). Cold precision forging process
Cold precision forging at room temperature is a near net shape forming process. The cold precision forging of spur bevel gear can avoid the error caused by high temperature. The spur bevel gear has high strength and precision and good surface quality. However, in the forming process, the deformation resistance of the workpiece is large, the filling effect is poor, and the requirements for the mold and equipment are high. In order to overcome the problems of cold precision forging process, new process methods including block forging, floating four die forging and prefabricated split flow forging have been developed.
3). Warm precision forging process
Warm precision forging is a forging process carried out at a suitable temperature below the recrystallization temperature. It is generally considered that forging within the temperature range of 700-850 ° C belongs to warm forging. This process has the advantages of low load of hot precision forging and high precision of cold precision forging, and overcomes the shortcomings of both. However, the warm precision forging process has a narrow forging temperature range and high requirements for its forging range, equipment, die structure and die materials. It is only suitable for mass production.
4). Compound forming technology of hot forging and cold forging
The combined forming technology of hot forging and cold forging began to appear in the 1980s and has been more and more widely used since the 1990s. It discards the shortcomings of cold, warm and hot forging and gives full play to the advantages of cold, warm and hot forging. It is a precision metal forging process combining hot forging and cold forging.
The process flow of hot forging and cold forging compound forming of spur bevel gear is as follows:
Blanking – heating (850 ± 10 ° C) – hot forging all flash and punching skin – annealing – Cleaning – phosphating saponification – cold forging – hot forging cold forging.
5). Block forging process
Block forging process is also known as compound forming technology. It uses compound punch to apply different pressures in one or more directions to make the blank produce multi-directional flow, so that large deformation and complex surface can be obtained in one deformation process to complete the plastic forming of complex parts. Block forging requires accurate blanking and good lubrication during forming.
6). Forging process of floating die
When traditional extrusion forming is adopted, as shown in Fig. 2 (a), the lower punch and die are fixed, and the upper punch moves downward at speed v. The main flow direction of the blank is downward, and the female die is transported upward relative to the blank
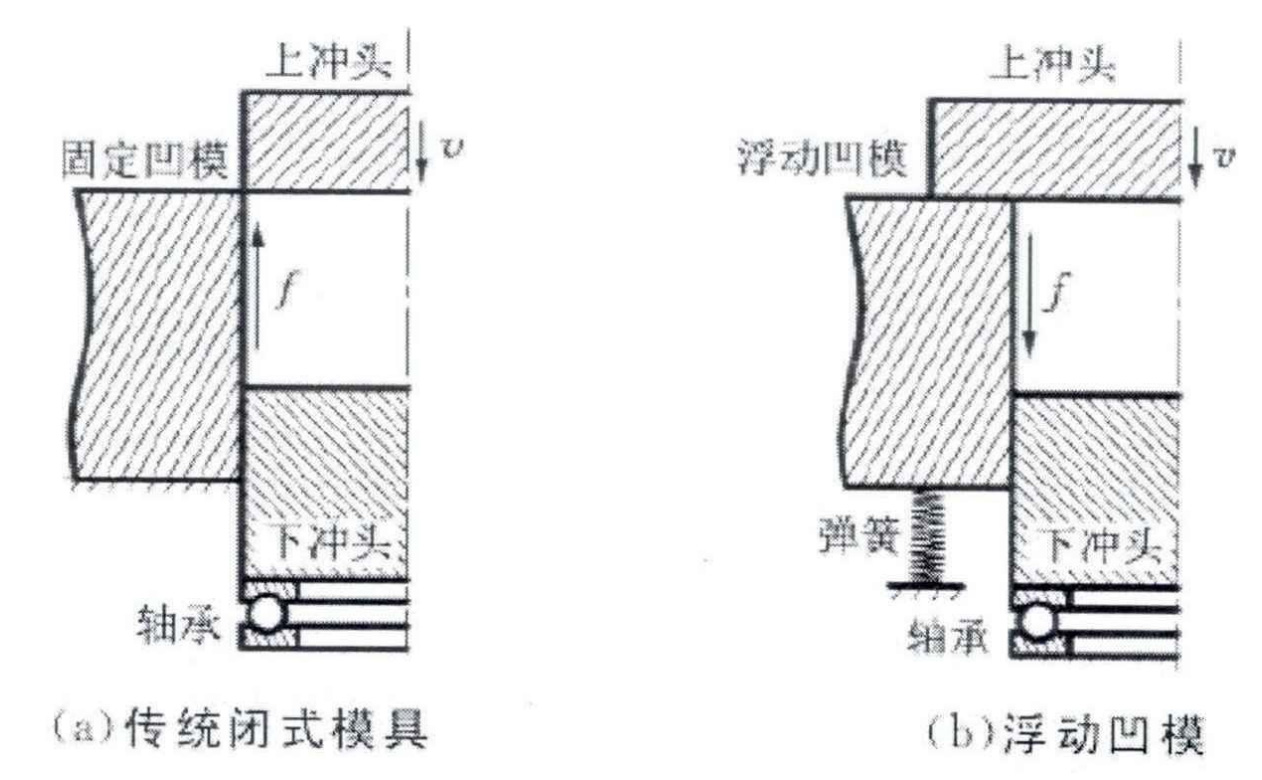
During the extrusion process, the blank is subjected to the friction force exerted by the die. The direction of the friction force is opposite to the direction of metal movement. With the extrusion process, the friction force will become larger and larger, and finally it will be difficult to fill the upper and lower corners of the spur bevel gear. If the four dies are changed to be floating, as shown in Fig. 2 (b), at the beginning of extrusion deformation, the four dies descend with the same speed V under the pressure of the upper punch. During the whole deformation process, the female die generates friction against the blank, but the direction of the force is downward along the axial direction, which is the same as the direction of metal movement. Finally, it can promote the filling of the tooth corners.
7) Prefabricated split flow forging
Since the 1980s, precision forging experts at home and abroad have begun to apply the split flow forging theory to the cold forging of spur gears and helical gears. The main principle of shunting forging is to establish a material shunting cavity or channel at the forming part of the mold, as shown in Figure 3. During the forging process, while the die cavity is filled with materials, some materials flow to the shunt cavity or shunt channel. The shunting chamber or channel can accommodate a small amount of materials with excessive volume, so that the forging stress will not increase sharply. In addition, through the reasonable design of the diversion path, the metal flow in the forging process is conducive to the filling at the sharp corners of the tooth shape, so as to reduce the forming stress and improve the filling effect. With the application of split flow forging technology, the less and no cutting processing of high precision spur bevel gears has rapidly reached the industrialization scale.
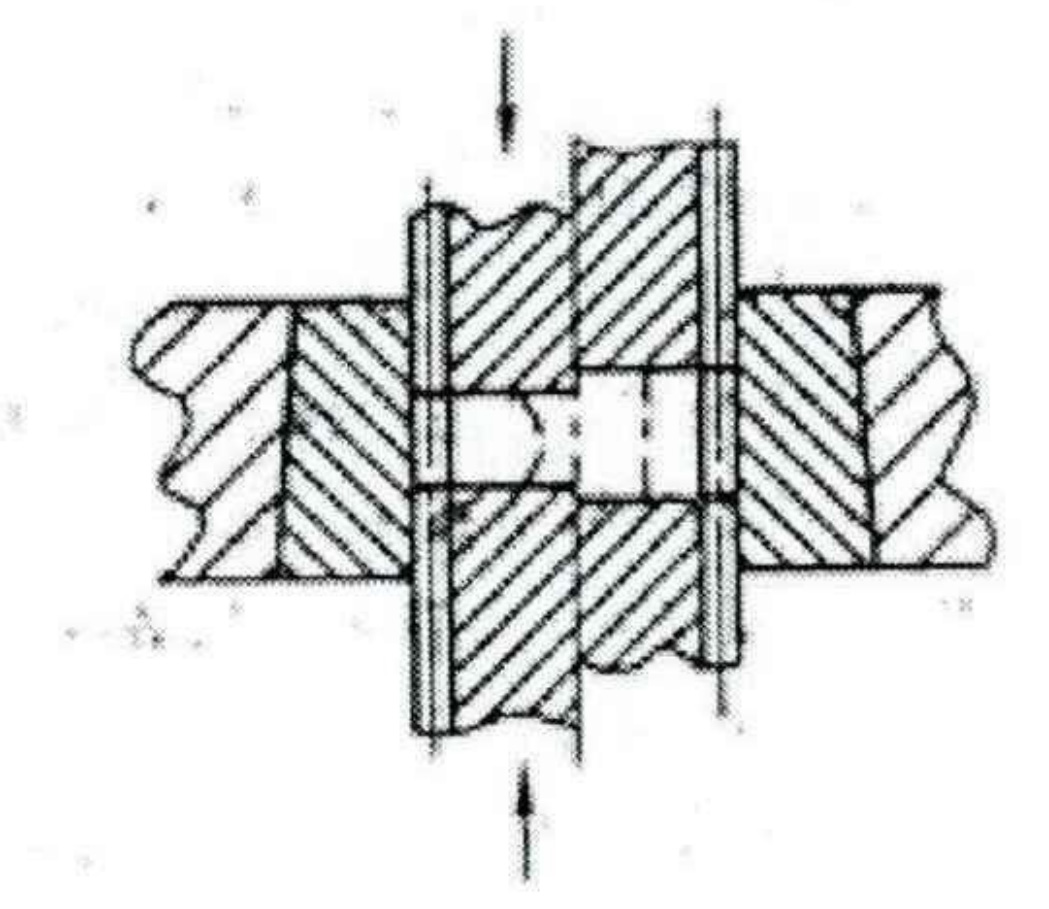
The design of shunting path is the key to the shunting forging of spur bevel gears. The basic principle is to make the material slide along the tooth direction as much as possible during forging, so as to obtain the full tooth shape under the minimum forming stress.
Split flow forging technology can realize the precision forming of spur gear or spiral spur gear and other parts with right angle shape, which is mainly used in automobile transmission gears. In addition to the reverse gear and planetary gear, the split flow forging technology can also be applied to the engagement ring and other ring gear parts.