Compared with cutting gear, precision forging gear has many advantages. Therefore, using precision forging technology to produce gear is the development trend of gear manufacturing industry. Because of its structural characteristics, the precision forging technology of spur bevel gear is the first to be used in production. At present, the precision forging technology of straight bevel gear is mature, and the reasonable precision forging technology and forging equipment can be selected according to the module, size and material of straight bevel gear.
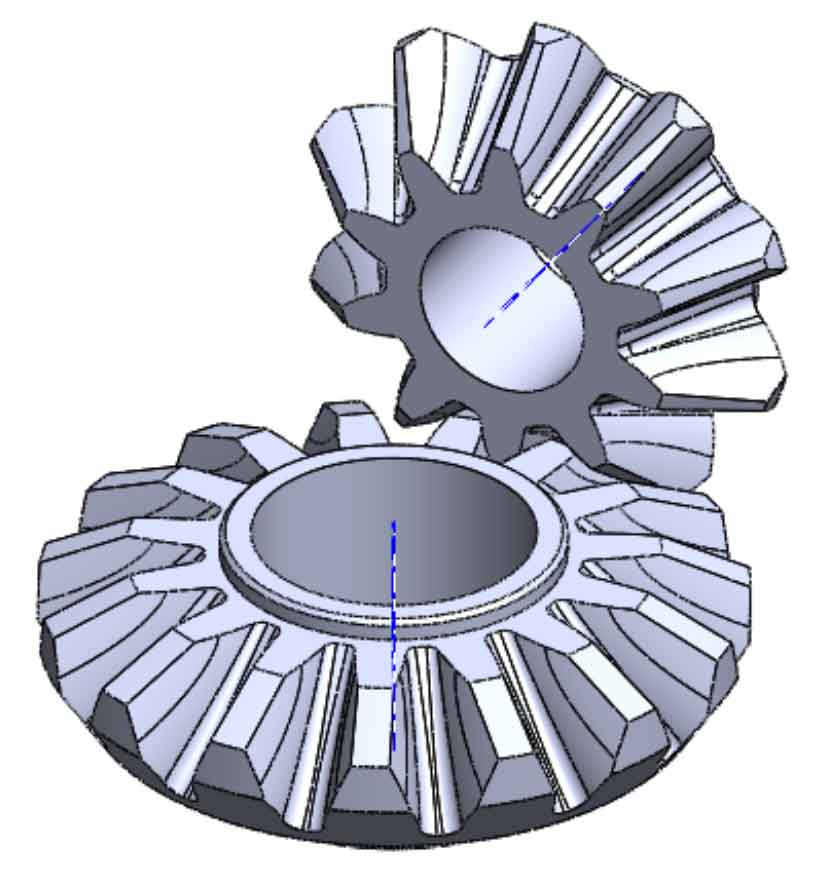
In production, “one fire two forging” process is generally used to form large modulus or large modulus straight bevel gear. Generally speaking, this process is relatively mature. However, due to the large deformation of the part of the gear teeth, problems such as insufficient filling at the top of the teeth, excessive forming load and premature failure of the straight bevel gear dies often occur during the forming process. After precision forging of straight bevel gear, its tooth surface can be directly used without machining, so it is required that the gear teeth of precision forging have high dimensional accuracy. There are many factors that affect the accuracy of straight bevel gears produced by “one heat two forging” process. It is necessary to consider not only the elastic recovery after forging, but also the cold shrinkage of hot forging and the influence of secondary oxidation on the size during forging. How to design tooth profile conveniently and accurately is also an urgent problem to be solved.
In view of the problems existing in forming large modulus straight bevel gears by “one heat two forging” process, two typical straight bevel gears are studied, and the main research contents are as follows:
1) Design the forging process of “one heat two forging” forming straight bevel gear, design the shape and size of forgings, pre forgings and preforms, and analyze the key technologies in precision forging.
2) This paper analyzes the relationship between the tooth shape of the finished product, the tooth shape of the forging, the tooth shape of the die cavity and the tooth shape of the electrode when forming the straight bevel gear with “one heat and two forgings”, establishes the accurate mathematical relationship between them, so as to realize the design from the tooth shape of the finished product straight bevel gear to the tooth shape of the electrode conveniently and accurately, and studies the tooth shape design of the non linear expansion heat forging, A new design model of tooth profile of non-linear expansion hot forging is proposed.
3) In this paper, the deformation law of straight bevel gear in precision forging process is studied. The dynamic simulation of forging process is carried out by using the finite element software one, and the stress distribution, strain distribution, strain rate distribution and load stroke curve of each deformation stage are obtained. The metal flow law and tooth filling form are analyzed to study the influence of pre forging shape on tooth filling and metal flow law, The metal flow can be controlled by the reasonable design of the die cavity size to ensure the lowest load when the cavity is full.
4) According to the process design and numerical simulation results, two die structures of pre forging and final forging are designed.