Hypoid gear, essential components in automotive differentials and various industrial applications, demand exceptional precision in their manufacturing due to their unique geometry and high-stress operational environment. Precision machining is crucial to ensure the optimal performance, longevity, and reliability of hypoid gear. This article explores the methods, advancements, and challenges in the precision machining of hypoid gear.
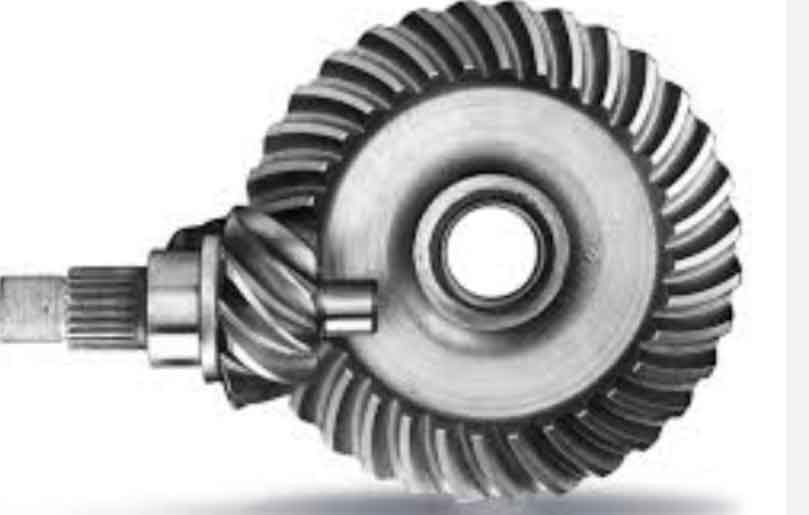
Introduction
Hypoid gear is type of bevel gear where the axes of the input and output shafts do not intersect, providing advantages in terms of torque transmission and noise reduction. The precision machining of these gears involves complex processes that must meet stringent tolerances and surface finish requirements. The evolution of machining techniques has significantly enhanced the quality and efficiency of hypoid gear production.
Key Machining Techniques for Hypoid Gear
- Gear Hobbing:
- Gear hobbing is a versatile and efficient method for rough and semi-finish machining of hypoid gear.
- It uses a rotating hob to generate hypoid gear teeth through continuous cutting.
- Gear Grinding:
- Gear grinding is employed for finishing operations to achieve high precision and surface quality.
- Types of gear grinding include form grinding, generating grinding, and profile grinding.
- Gear Shaping:
- Gear shaping involves the reciprocating motion of a cutter to produce hypoid gear teeth.
- It is particularly useful for internal gears and non-standard gear profiles.
- Five-Axis CNC Machining:
- Five-axis CNC machines allow for the precise machining of complex hypoid gear geometries.
- This technology ensures high accuracy and repeatability in hypoid gear production.
Comparative Analysis of Machining Techniques
Machining Technique | Advantages | Disadvantages |
---|---|---|
Gear Hobbing | High efficiency, versatility | Limited to rough and semi-finish machining |
Gear Grinding | Superior surface finish, high precision | High cost, slower process |
Gear Shaping | Suitable for internal gears, flexibility | Lower precision compared to grinding |
Five-Axis CNC Machining | High accuracy, complex geometries | Expensive equipment, complex programming |
Critical Factors in Precision Machining
- Tool Selection: Choosing the appropriate cutting tools and grinding wheels is crucial for achieving the desired surface finish and dimensional accuracy.
- Machine Accuracy: High-precision machines with advanced control systems are essential for maintaining tight tolerances.
- Coolant and Lubrication: Effective coolant and lubrication systems help reduce heat generation and tool wear, ensuring consistent quality.
- Process Control: Advanced process control systems, including real-time monitoring and feedback, are vital for maintaining precision throughout the machining process.
Advanced Techniques in Precision Machining
1. Computer-Aided Manufacturing (CAM)
CAM software enables the precise programming of machining operations, optimizing tool paths and cutting parameters for hypoid gear. This results in improved accuracy and reduced cycle times.
2. High-Speed Machining (HSM)
HSM techniques involve the use of high spindle speeds and feed rates to enhance productivity and surface quality. This approach minimizes heat generation and tool wear, leading to better dimensional control.
3. Adaptive Machining
Adaptive machining technologies utilize real-time data to adjust machining parameters dynamically. This ensures consistent quality, even when dealing with variations in material properties or machine conditions.
List of Challenges in Precision Machining
- Complex Geometry: The non-intersecting axes of hypoid gear require sophisticated machining strategies.
- Tight Tolerances: Maintaining tight tolerances and surface finishes demands high-precision equipment and meticulous process control.
- Tool Wear: The high-contact stresses involved in machining hypoid gear can lead to significant tool wear, necessitating frequent tool changes and maintenance.
- Heat Generation: High-speed machining processes can generate excessive heat, affecting the material properties and dimensional stability of the hypoid gear.
Future Directions in Hypoid Gear Machining
- Integration of Artificial Intelligence (AI):
- AI-driven systems can optimize machining parameters in real-time, improving precision and reducing cycle times.
- Predictive maintenance using AI can minimize downtime and enhance machine reliability.
- Hybrid Machining Processes:
- Combining additive and subtractive manufacturing techniques allows for the creation of complex geometries with minimal material waste.
- Hybrid processes can also improve the mechanical properties and surface finishes of hypoid gear.
- Sustainable Machining Practices:
- The focus on sustainability is driving the development of eco-friendly machining processes.
- The use of biodegradable coolants and energy-efficient machines is becoming increasingly important.
Conclusion
Precision machining is fundamental to the production of high-quality hypoid gear. The advancement of machining techniques, driven by innovations in material science and technology, has significantly improved the accuracy, efficiency, and reliability of hypoid gear manufacturing. As the industry continues to evolve, the integration of AI, hybrid machining processes, and sustainable practices will further enhance the precision and sustainability of hypoid gear production.