his article focuses on the topology modification of herringbone gears. It begins with an introduction to the importance of herringbone gears in various industries and the challenges they face, such as vibration and stress concentration. The methods of Monte Carlo and genetic algorithms for topology modification are then described in detail. The article also presents the modeling of herringbone gear transmission systems and the analysis of tooth surface loading. Through a comparison of the results of different modification methods under various working conditions, it is demonstrated that gear modification can effectively reduce transmission error and contact stress. Finally, the advantages of genetic algorithm modification are emphasized, and the future research directions and potential applications of herringbone gear topology modification are discussed.
1. Introduction
Herringbone gears have been widely used in many fields such as aerospace and large ships due to their advantages of large transmission torque, compact structure, no additional axial force, and stable operation. However, the large transmission torque and high rotational speed of herringbone gears can lead to increased contact deformation of the gear teeth, resulting in vibration and fatigue damage to the gear transmission system. Therefore, it is crucial to adopt appropriate methods for gear design and processing to improve the meshing state of the gear teeth. Gear modification is one of the common measures to enhance the meshing state of the gear teeth. By modifying the gear teeth, the contact stress distribution of the gear teeth can be improved, the transmission error of the gear can be reduced, and vibration and noise can be decreased, thereby reducing the occurrence of fatigue damage.
1.1 Background and Motivation
In recent years, with the development of modern industry, the requirements for the performance of gear transmission systems have become increasingly high. Herringbone gears, as an important part of many mechanical transmission systems, play a crucial role in ensuring the stable operation of the entire system. However, the traditional standard tooth surface herringbone gears often face problems such as vibration and noise during the transmission process, which seriously affect the performance and service life of the gear transmission system. Therefore, it is necessary to study the modification methods of herringbone gears to improve their transmission performance.
1.2 Objectives of the Study
The main objective of this study is to explore effective topology modification methods for standard tooth surface herringbone gears to reduce vibration and noise during the transmission process and improve the stability of the transmission system. Specifically, the study aims to:
- Use Monte Carlo method and genetic algorithm to modify the topology of standard tooth pinion.
- Analyze the transmission error and contact stress of the modified gears under different working conditions.
- Compare the modification effects of the two algorithms and determine the more effective method.
2. Herringbone Gear Basics
2.1 Structure and Characteristics
Herringbone gears are composed of two helical gears with opposite helix angles. This unique structure endows them with several notable characteristics. Firstly, they can transmit large torque due to the multiple teeth in contact simultaneously. Secondly, the opposing helix angles cancel out the axial forces, resulting in a more stable transmission without the need for additional axial thrust bearings. The compact structure of herringbone gears also makes them suitable for applications where space is limited.
2.2 Applications in Different Industries
In the aerospace industry, herringbone gears are used in aircraft engines and flight control systems to ensure reliable power transmission and precise control. In large ships, they are employed in the main propulsion systems and auxiliary equipment to handle the high torque requirements. Additionally, herringbone gears can be found in heavy machinery, such as mining equipment and construction machinery, where they are required to withstand heavy loads and continuous operation.
3. Gear Modification Methods
3.1 Overview of Gear Modification
Gear modification involves altering the shape of the gear teeth to improve their meshing characteristics. This can be achieved through various methods, such as profile modification, lead modification, and topological modification. Profile modification changes the shape of the tooth profile, while lead modification affects the helix angle or lead of the gear teeth. Topological modification, on the other hand, focuses on changing the overall geometry of the gear teeth in a more comprehensive manner.
3.2 Monte Carlo Method
3.2.1 Principles and Algorithms
The Monte Carlo method is a stochastic simulation technique based on random sampling. In the context of gear topology modification, it involves generating a large number of random samples within a defined parameter space. These samples represent possible modifications to the gear teeth. The algorithm then evaluates each sample based on certain criteria, such as the reduction of transmission error or contact stress. Through repeated sampling and evaluation, an optimal or near-optimal modification solution can be obtained.
3.2.2 Advantages and Limitations
The advantages of the Monte Carlo method include its ability to handle complex problems with multiple variables and its flexibility in exploring a wide range of possible solutions. It does not require a priori knowledge of the exact functional relationship between the variables and the objective function. However, it can be computationally expensive, especially when a large number of samples are required to achieve accurate results. Additionally, the random nature of the method may lead to some variability in the results, and it may not always guarantee the global optimum.
3.3 Genetic Algorithm
3.3.1 Principles and Algorithms
The genetic algorithm is an optimization algorithm inspired by the process of natural selection and genetics. It starts with an initial population of candidate solutions (in this case, different gear modification designs). These solutions are encoded as chromosomes, and genetic operators such as selection, crossover, and mutation are applied to the population over successive generations. The fitness of each solution is evaluated based on a predefined objective function (e.g., minimizing transmission error or contact stress). Through this iterative process, the population evolves towards better solutions, and eventually, an optimal or near-optimal modification design can be found.
3.3.2 Advantages and Limitations
The genetic algorithm has several advantages. It is capable of handling complex optimization problems with non-linear and discontinuous objective functions. It can explore a large search space efficiently and has a good ability to avoid getting trapped in local optima. However, it also has some limitations. The performance of the algorithm depends on the proper design of the genetic operators and the choice of parameters. If not configured correctly, it may converge slowly or produce suboptimal results. Additionally, the interpretation of the results in terms of real-world gear design can be somewhat challenging as the genetic representation may not be directly intuitive.
4. Modeling of Herringbone Gear Transmission System
4.1 System Parameters
The parameters of the herringbone gear transmission system play a crucial role in determining its performance. These parameters include the number of teeth, module, pressure angle, spiral angle, and tooth width of the gears. For example, the number of teeth affects the gear ratio and the distribution of load on the teeth. The module determines the size of the gear teeth, while the pressure angle and spiral angle influence the meshing characteristics and the direction of the axial force. The tooth width is related to the contact area between the teeth and the load-carrying capacity of the gear.
Parameter | Unit | Small Gear | Large Gear |
---|---|---|---|
Number of Teeth | 17 | 44 | |
Module | mm | 6 | 6 |
Pressure Angle | 20 | 20 | |
Spiral Angle | 24.43 | -24.43 | |
Tooth Width | mm | 55 | 55 |
4.2 Modeling Approach
Since herringbone gears are composed of two symmetric helical gears, and considering the high manufacturing precision and symmetric load distribution of the standard tooth surface herringbone gears studied in this research, the modeling can be simplified by only modeling the corresponding helical gears (with the tooth width being half of the herringbone gear tooth width and the helical gears being left-handed and right-handed respectively) and applying half of the torque. The gear transmission system model is shown in Figure 1.
[Insert Figure 1 here: Gear transmission system model]
5. Tooth Surface Loading Analysis
5.1 Selection of Modification Curve
For the convenience of processing, all modification results are accumulated on the small gear. Considering the good tolerance of the quadratic parabola, the modification curve is chosen as the quadratic parabola.
5.2 Topology Modification Results
Using the Monte Carlo method and the genetic algorithm, the topology modification results of the small gear are obtained as shown in Figure 2.
[Insert Figure 2 here: Topology modification results of the small gear]
5.3 Transmission Error Analysis
The modification results are respectively superimposed on the standard tooth surface to obtain the transmission error curve as shown in Figure 3. The peak-to-peak values of the transmission error are listed in Table 3.
Working Condition | Peak-to-Peak Value (μm) Before Modification | Peak-to-Peak Value (μm) After Monte Carlo Modification | Peak-to-Peak Value (μm) After Genetic Algorithm Modification |
---|---|---|---|
Condition 1 | 0.255 | 0.094 | 0.078 |
Condition 2 | 0.400 | 0.141 | 0.112 |
Condition 3 | 0.545 | 0.290 | 0.239 |
Condition 4 | 0.689 | 0.402 | 0.345 |
Condition 5 | 0.832 | 0.445 | 0.421 |
From Figure 3 and Table 3, it can be seen that both the Monte Carlo method and the genetic algorithm can reduce the peak-to-peak value of the gear transmission error. The Monte Carlo method can reduce the maximum value by 64.75% (under Condition 2), and the genetic algorithm can reduce the maximum value by 72% (under Condition 2). The genetic algorithm shows a more significant modification effect.
5.4 Contact Stress Analysis
The contact stress distribution is shown in Figures 4 – 8. The maximum values of the contact stress are listed in Table 4.
Working Condition | Maximum Contact Stress (MPa) Before Modification | Maximum Contact Stress (MPa) After Monte Carlo Modification | Maximum Contact Stress (MPa) After Genetic Algorithm Modification |
---|---|---|---|
Condition 1 | 339 | 345 | 320 |
Condition 2 | 428 | 410 | 382 |
Condition 3 | 502 | 459 | 434 |
Condition 4 | 567 | 500 | 479 |
Condition 5 | 626 | 537 | 520 |
From Figures 4 – 8 and Table 4, it can be seen that the contact stress of the standard tooth surface gear is concentrated near the end face of the gear teeth. After modification by the Monte Carlo method and the genetic algorithm, the contact stress is concentrated in the interior of the tooth surface. The maximum values of the contact stress are also decreased. The Monte Carlo method can reduce the maximum value by 16.57% (under Condition 5), and the genetic algorithm can reduce the maximum value by 20.38% (under Condition 5). The genetic algorithm shows a more significant modification effect on contact stress as well.
6. Comparison and Discussion
6.1 Comparison of Modification Effects
By comparing the transmission error and contact stress of the standard tooth surface gear and the modified gears under different working conditions, it can be seen that gear modification can effectively reduce the peak-to-peak value of the transmission error and the maximum value of the contact stress, and move the contact stress to the middle of the tooth surface, thereby reducing the edge stress concentration and improving the contact stress distribution.
6.2 Advantages of Genetic Algorithm
Under the same working conditions, the genetic algorithm can more effectively reduce the peak-to-peak value of the transmission error and the maximum value of the contact stress compared to the Monte Carlo method. Therefore, the genetic algorithm has a better modification effect than the Monte Carlo method.
7. Conclusion
7.1 Summary of Research Findings
- Gear modification using both Monte Carlo method and genetic algorithm can improve the performance of herringbone gears by reducing transmission error and contact stress.
- The genetic algorithm shows a more significant modification effect in terms of reducing transmission error and contact stress compared to the Monte Carlo method.
7.2 Implications for Gear Design and Manufacturing
The research findings have important implications for gear design and manufacturing. The use of appropriate modification methods can help designers to optimize the performance of herringbone gears, reduce vibration and noise, and improve the service life of the gears. This can lead to more reliable and efficient gear transmission systems in various industries.
7.3 Future Research Directions
Future research could focus on further exploring the potential of genetic algorithms in gear modification, such as optimizing the genetic operators and parameters for better performance. Additionally, research could be extended to three-dimensional modification of herringbone gears and the study of the dynamic characteristics of modified gears under different operating conditions.
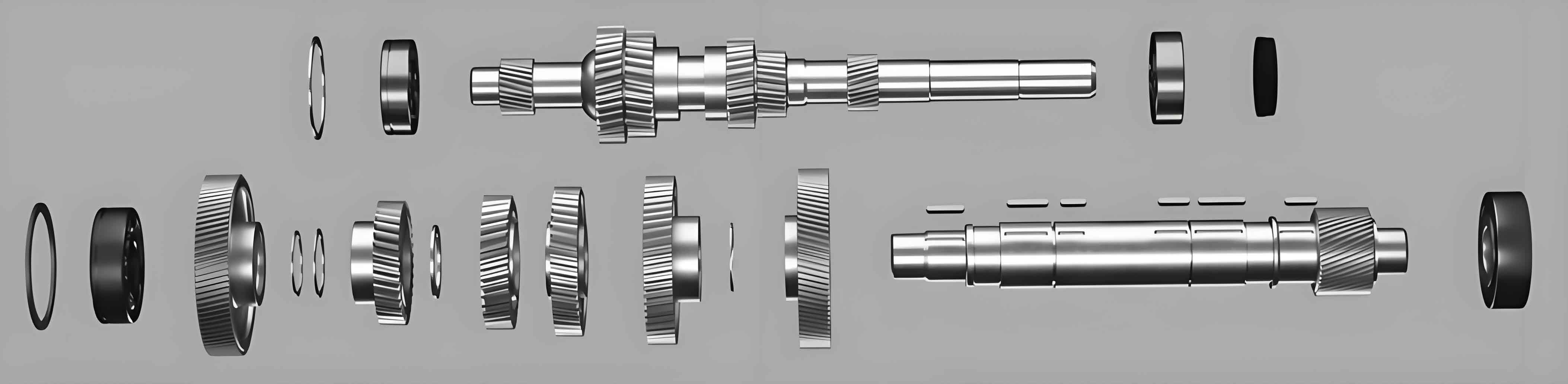