The meshing process of helical gear is affected not only by the distribution of tooth profile load, but also by the distribution of tooth direction load. In the process of helical gear processing, the grinding process is often used to compensate the helix deviation caused by manufacturing and installation errors, so as to ensure the uniform contact of helical gear along the tooth width direction under normal temperature and no-load environment. However, the transmission of power during the meshing process of helical gears will cause various deformations of helical gears, such as bending deformation and contact deformation of gear teeth under the action of load, bending, torsion and shear deformation of helical gear shaft under the action of external torque, eccentricity of high-speed helical gears under the action of centripetal force and eccentric mass, and thermal deformation of gear teeth under the action of friction heat, The load distribution of the tooth direction will be affected by the unequal load of the left and right bearings, the skew caused by the asymmetric configuration of the helical gear, and the uneven clearance between the original tooth direction and the tooth side caused by the manufacturing error of the tooth direction. These factors will skew the helix of the helical gear.
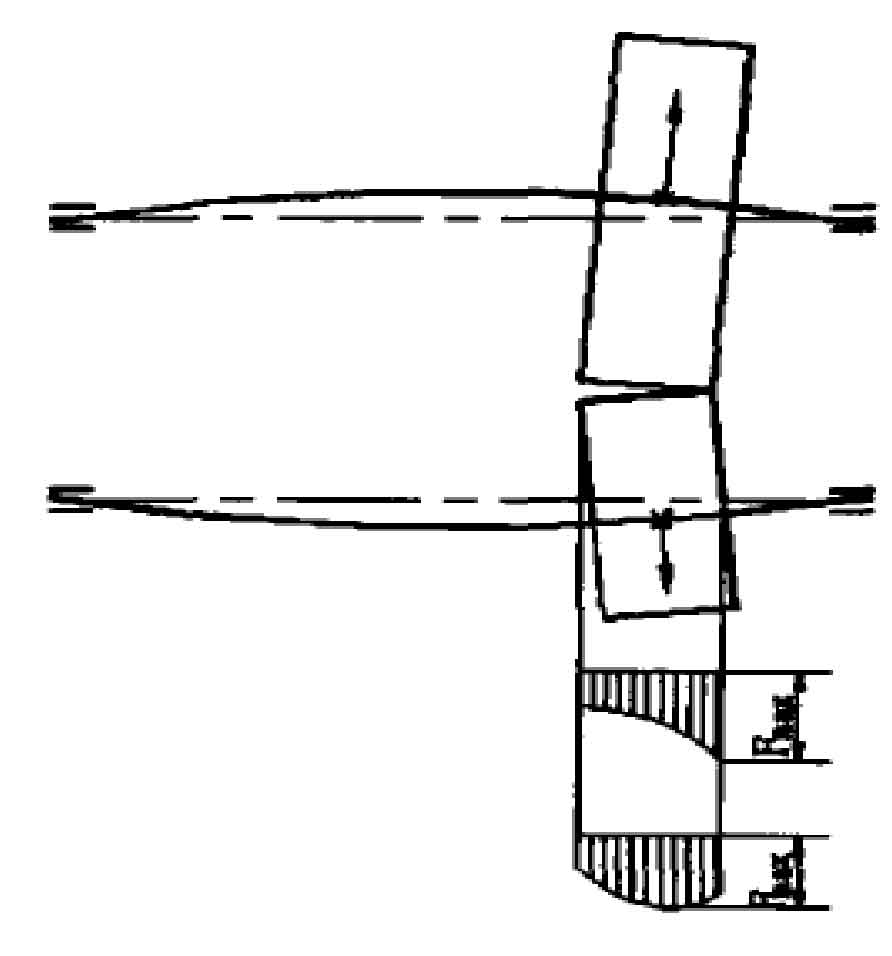
Figure 1 shows the meshing condition of helical gear under no-load, with uniform load distribution and stable meshing. Fig. 2 shows the meshing condition of the helical gear after being loaded. The helical gear shaft is bent and deformed under the action of load, and the contact along the tooth direction is uneven, causing the tooth to deviate to one end contact, affecting the normal meshing of the helical gear.
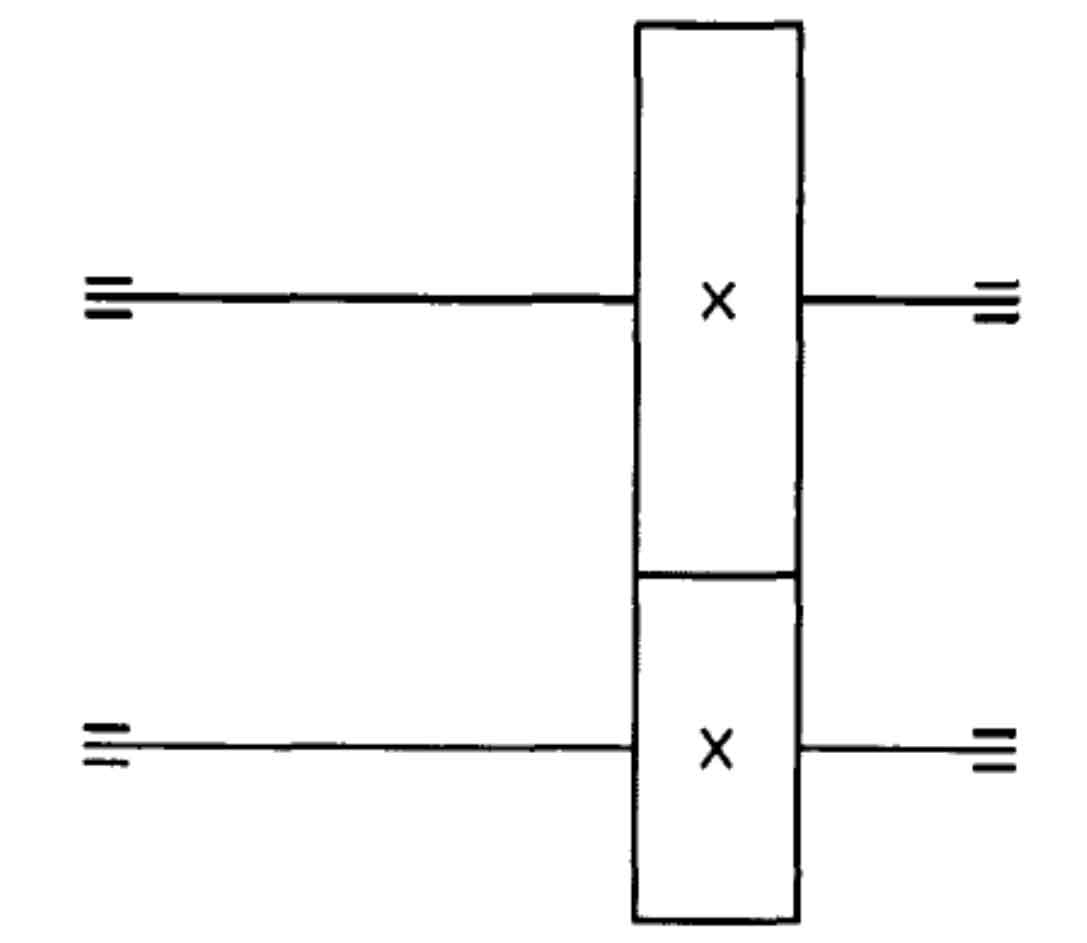
The tooth profile modification of helical gear is to trim the spiral line of the tooth profile according to the predetermined deformation law according to the load distribution law after the gear is loaded, and slightly trim the tooth surface in the tooth direction to make it deviate from the theoretical tooth surface. There are many factors to be considered in tooth profile modification, among which the elastic deformation caused by load is the most important. The traditional material mechanics method is based on the tooth profile modification theory of the assumption of uniform load, that is, the combined bending and torsion deformation curve of the helical gear shaft under the assumption of uniform load is obtained, and the symmetrical line of the deformation curve is the theoretical tooth profile modification curve.
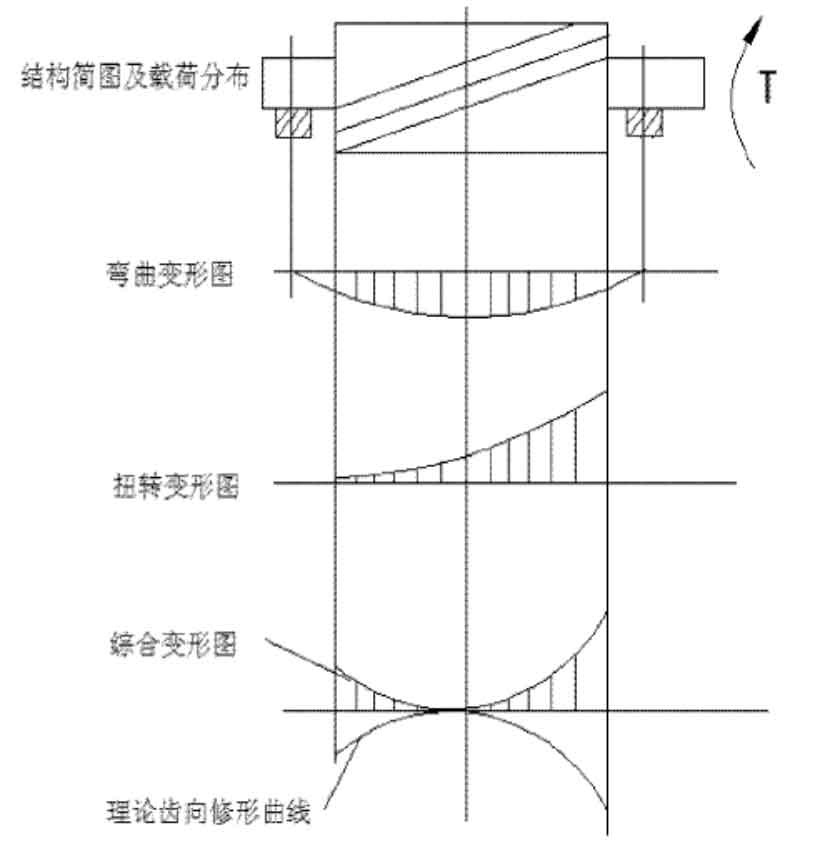
As shown in Figure 3, the bending deformation diagram shows the bending deformation curve generated when the shaft is subjected to the pressure of the meshing helical gear, the torsional deformation diagram shows the corresponding torsional deformation curve generated when the shaft is subjected to torque T, and the comprehensive deformation diagram shows the combined deformation curve of the shaft subjected to bending and torsional deformation. For determining the elastic deformation modification amount, it is to calculate the maximum relative value of the comprehensive deformation within the tooth width, that is, the total deformation. The comprehensive deformation curve of helical gear and the theoretical tooth direction modification curve are symmetrical to each other.