Double gear is widely used in gear boxes. In general transmission, it is not required to align the teeth.However, this example is a double planetary gear drive with high speed and heavy load. The specific structure is shown in Figure 1.
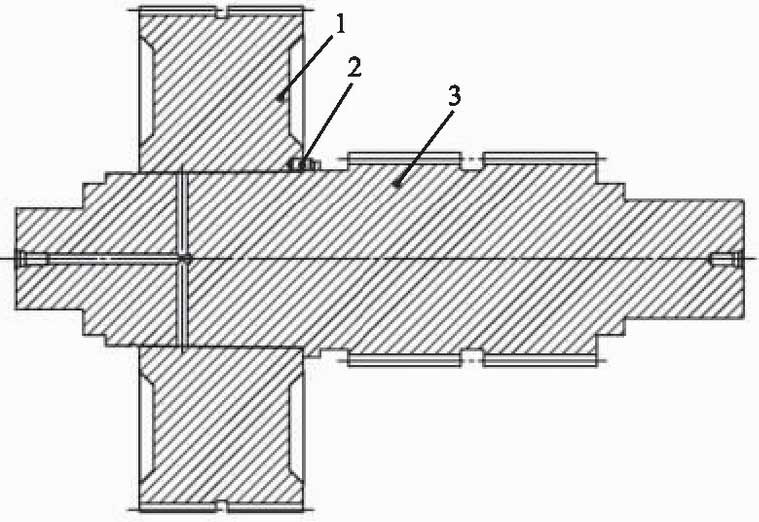
Technical Requirements
(1) Big gear parameters: number of teeth 147, modulus 6, pressure angle 20 degrees, gear accuracy GB/T 10095-4;
Gear shaft parameters: number of teeth 45, modulus 8, pressure angle 20 degrees, gear accuracy GB/T10095-4.
(2) Carburizing and hardening of tooth surface and root of gear. The depth of carburizing layer is 1.8-2.3 mm and the hardness of tooth surface is HRC58-62.
(3) The angular position deviation between the large gear and the reference teeth of the gear shaft is not more than 0.003 degrees.
Analysis of processing difficulties
(1) High gear accuracy is required. Machining accuracy of large gear and gear shaft is GB/T10095-4.
(2) Carburizing heat treatment is required for the teeth. Gear material is 18CrNiMo7-6. After carburizing heat treatment, the deformation is large and tooth grinding is difficult to achieve.
(3) The gear shaft must grind the teeth before the combination, otherwise the large gear will interfere with the grinding wheel during the grinding process.
(4) It is necessary to design the positioning device of the combination of double gears to ensure the angular positioning accuracy of the gears in assembly.
(5) How to ensure the angular position during grinding.