Hypoid gears have important applications in the field of mechanical engineering and automobile. However, at present, its machining process is relatively complex and manufacturing is relatively difficult. Therefore, some experts and scholars at home and abroad have been committed to studying hypoid gears.
The research on the design and machining of hypoid gears by experts from foreign countries and Taiwan, China is earlier than that in China, and the research is more in-depth at present. Bevel gears and hypoid gears have the same tooth system, mainly including: 1) Gleason system, from the United States; 2) Oerlikon system, from Switzerland; 3) The cyclo palloid system comes from Germany. In 1913, Gleason company designed a spiral bevel gear end face cutting machine, as shown in the figure. By 1919, Gleason had obtained the invention patent from Paul Bottcher and carried out in-depth research on single tooth indexing processing. E.wildhaber of the United States has published many related articles in the American Machinist magazine, including a complete description of the geometry and kinematics of hypoid gears. Litvin and Gutman developed a method for machining hypoid gears,
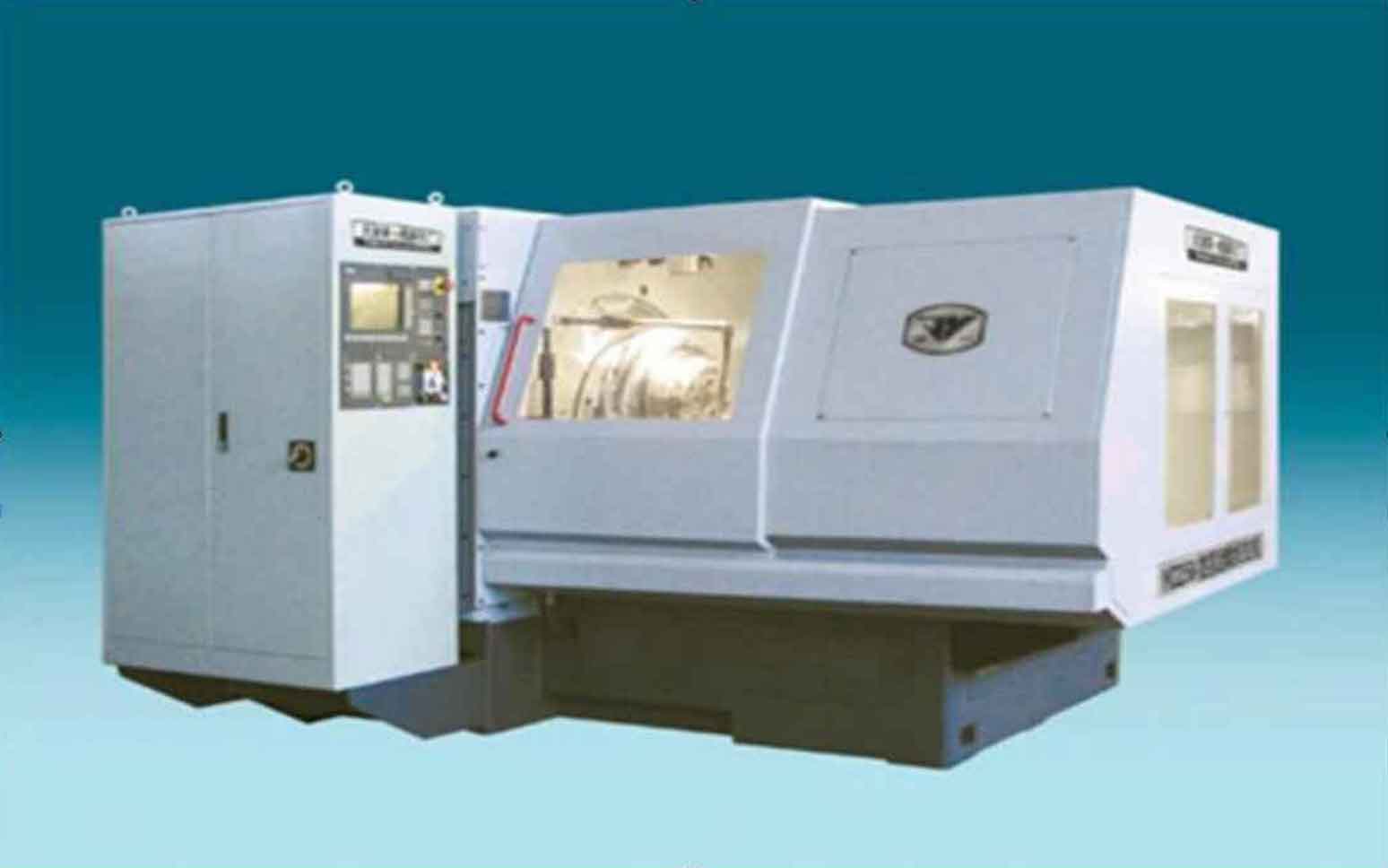
They are ‘forming method’ and ‘spiral forming method’ respectively, and a train of thought is determined: making the pinion tooth surface conjugate with the gear tooth surface. Then the relevant mathematical model is established. The method used is face milling method, and the tooth contact analysis and local synthesis method are proposed. Hypoid gears can be conjugate in theory, that is, the contact between the big wheel and the small wheel is linear contact, but there are assembly errors and tooth surface errors in the actual transmission process. Therefore, the point contact of tooth surface must be used to replace the theoretical line contact, which needs to be realized by tooth surface modification. A lot of related research has been done in this regard.
M. The theoretical basis put forward by l.baxter in the design of machining methods for hypoid gears is very detailed. M. According to the ‘local conjugate principle’, l.baxter proposed the design of tooth cutting method by modifying the normal curvature of the small gear tooth surface at the reference point. According to the calculation reference points on the big tooth surface of hypoid gear, and let the small wheel make line contact with it, the corresponding normal vector and normal curvature at these points can be obtained. The curvature is used to modify the tooth surface of the small gear, and the machining parameters of the small gear are obtained. Finally, the position relationship between the small wheel and the production wheel is set to meet the requirements of the small wheel normal vector. At the same time, fan et al. Put forward the basic principle of machining hypoid gear by surface hobbing method, established the mathematical model of tooth surface, and deepened and enhanced the tooth contact analysis method of Gleason company. TCA refers to the tooth cutting correction and tooth surface calculation for the calculation points set on the tooth surface. Finally, the universal tooth surface generation model of free form NC hypoid gear machine tool based on (UMC) is established. Its tooth surface processing methods are face milling method and face hobbing method. Lim et al. Studied the vibration model of hypoid gear system, and analyzed the meshing characteristics of hypoid gears. Gosselin et al. Proposed and verified the transmission error simulation model of gear under certain load.
Due to the late development of China’s machinery industry, the corresponding gear manufacturing level is relatively backward. However, due to the redoubled efforts of Chinese scholars and the strong support of national policies, our country has made great progress in the field of gears recently. After so many years of hard work, China has made fruitful achievements in the field of hypoid gear research and processing. At present, there are many enterprises with bevel gear production capacity in China.
In the early stage of reform and opening up, Chinese scholars carried out research on the machining of hypoid gears through the Oricon gear machine equipment introduced by the state. At the same time, due to the technical blockade imposed by the United States on China, Chinese scholars and experts mainly focus on the key cutting technology and subsequent gear analysis technology of Gleason gear. Lihuamin, a professor of Harbin Institute of technology, wrote the gear manual, which contains the basic gear theory and gear cutting methods, and has a profound guiding effect on the subsequent research of various gears. Zhengchangqi and zhanghongbiao of Chongqing University first studied the gear machining technology of Gleason, including its gear design method and cutting calculation principle. In zhengchangqi’s book, two methods of gear processing by Gleason are discussed, and the calculation formula is derived. Professor wuxutang elaborated the meshing principle of gears in great detail, and deduced the relevant parameters of hypoid gears in Chapter 6 of his book gear meshing principle, which laid a solid foundation for the follow-up research of hypoid gears. Fangzongde, a professor of Northwestern Polytechnic University, deduced the tooth contact analysis method based on the ‘local synthesis method’, and established a method to check the interference and undercutting in the machining process.
There are also many Chinese scholars who have made contributions to the development of gears, but they are basically based on Gleason gears. The gear processing technology blocked by foreign countries has hindered the development of China’s gear industry to a certain extent.