Helical gears have indeed brought about a silent revolution in the field of gear technology, offering significant advantages in terms of noise reduction and efficiency compared to other gear types. Let’s explore how helical gears achieve these improvements:
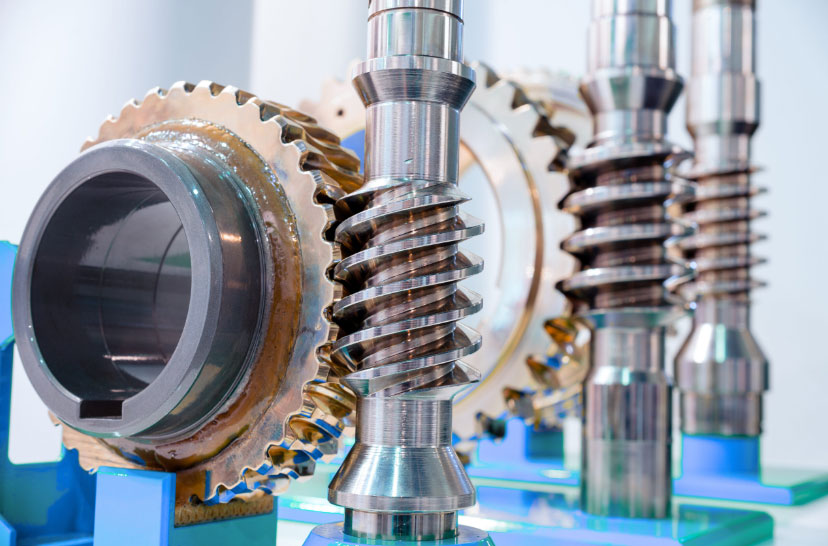
- Gradual Tooth Engagement: One of the key features of helical gears is their helical tooth profile, which allows for gradual tooth engagement during meshing. Unlike spur gears, which produce an abrupt impact when their teeth come into contact, helical gears exhibit a smoother meshing action. This gradual engagement significantly reduces noise and vibration, making them an excellent choice for applications where quiet operation is essential, such as in precision machinery, consumer appliances, and automotive transmissions.
- Reduced Vibration: The smoother meshing action of helical gears also leads to reduced vibration. This reduction in vibration not only contributes to lower noise levels but also helps enhance the overall stability and performance of the machinery.
- Load Distribution: Helical gears distribute the load across multiple teeth due to their angled tooth profile. This feature results in higher contact ratios compared to spur gears, which enhances the load-carrying capacity and allows for more efficient power transmission.
- Efficiency in High-Speed Applications: The gradual meshing and increased contact area of helical gears also result in reduced sliding friction between teeth during operation. As a result, helical gears are more efficient at higher speeds, making them ideal for applications where rotational speeds are significant, such as in gearboxes, turbines, and high-speed machinery.
- Energy Efficiency: Due to their smoother operation and reduced friction, helical gears are more energy-efficient than other gear types, such as bevel gears or worm gears. The improved efficiency can lead to energy savings in industrial processes and result in lower operating costs.
- Backlash Reduction: Helical gears exhibit lower backlash compared to spur gears, which is essential for precise motion control and positioning applications. The reduced backlash contributes to the accuracy and repeatability of the machinery.
- Durability and Longevity: The load distribution and reduced sliding friction in helical gears lead to less wear and longer gear life. Properly lubricated helical gears can operate with minimal maintenance and offer excellent durability in industrial applications.
- Versatility and Adaptability: Helical gears can be used in various configurations and gear arrangements, making them versatile for different industrial applications. They can be applied in both parallel and crossed shaft arrangements, as well as in multiple-stage gearboxes to achieve the desired speed and torque requirements.
Due to these advantages, helical gears have found extensive use in industries such as automotive, aerospace, manufacturing, and robotics. Their ability to provide quieter operation, improved efficiency, and reliability has made them a preferred choice for gear applications, contributing to the “silent revolution” in the gear technology domain.