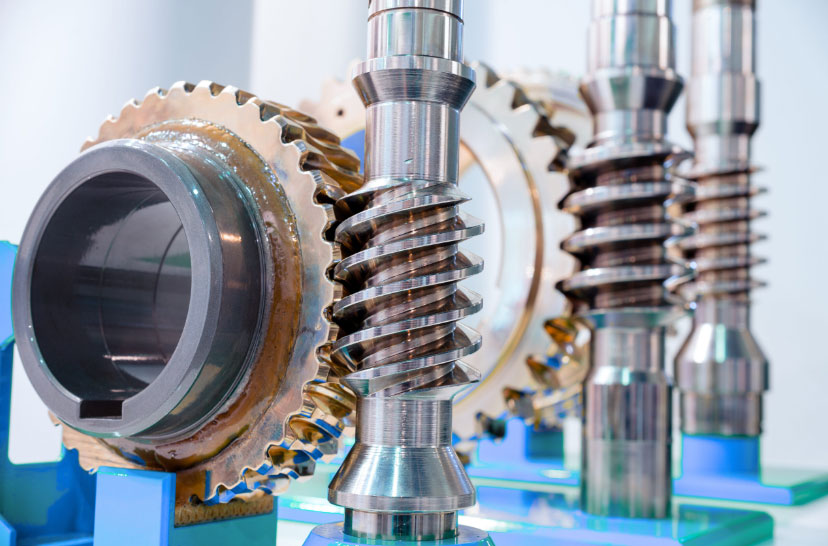
Helical gears offer several advantages that make them well-suited for various industrial applications. Here are some of the key benefits:
- Smooth and Quiet Operation: The helical tooth profile allows for gradual tooth engagement, resulting in smoother and quieter operation compared to spur gears. The continuous contact between teeth reduces vibration and noise, making helical gears ideal for applications where noise reduction is essential, such as in precision machinery and high-speed gearboxes.
- High Load-Carrying Capacity: The helical gear design spreads the load across several teeth, leading to a larger contact area. This increased contact ratio enhances the gear’s load-carrying capacity and makes helical gears more suitable for heavy-duty applications in industrial machinery, construction equipment, and heavy transport systems.
- Efficiency: Helical gears have higher efficiency compared to other gear types, such as worm gears. The gradual tooth engagement reduces sliding friction and allows for more power to be transmitted from the input shaft to the output shaft, making helical gears an energy-efficient choice.
- Ability to Transmit Large Torque: The design of helical gears allows them to transmit higher torque loads, making them suitable for applications that require substantial power transmission, such as in industrial drives and gearboxes.
- Compact Design: Helical gears offer a compact and space-saving design, especially when compared to other gear types like bevel gears. Their ability to transmit motion between non-parallel shafts while maintaining a compact profile makes them suitable for a wide range of industrial machinery.
- Versatility: Helical gears can be used in a variety of configurations, including parallel shaft arrangements, crossed helical gear sets, and multiple stage gearboxes. This flexibility makes them adaptable to different industrial applications and gear arrangements.
- Less Heat Generation: The gradual meshing of helical gears results in reduced sliding friction, leading to lower heat generation during operation. This can be advantageous in applications where temperature control is critical or in high-speed machinery.
- Reduced Backlash: Helical gears have lower backlash compared to spur gears, which means there is less play between meshing teeth. Reduced backlash is essential for precision motion control applications and helps improve the overall accuracy of the system.
- Longer Gear Life: The load distribution and reduced sliding friction in helical gears result in less wear and longer gear life compared to other gear types. When properly lubricated and maintained, helical gears can offer excellent durability and reliability.
Due to their numerous advantages, helical gears are widely used in various industrial applications, including conveyors, pumps, compressors, machine tools, robotics, and automotive transmissions. They strike a balance between efficiency, smooth operation, and load-carrying capacity, making them an essential component in many industrial systems.