Noise and vibration in straight bevel gear can significantly impact the performance, reliability, and user experience of mechanical systems. These issues can lead to increased wear, reduced efficiency, and a shorter lifespan for straight bevel gear. Addressing noise and vibration is thus crucial for ensuring the optimal functionality of straight bevel gear in various applications. This article delves into the causes of noise and vibration in straight bevel gear and explores methods for reducing these issues through design, material selection, manufacturing processes, and maintenance practices.
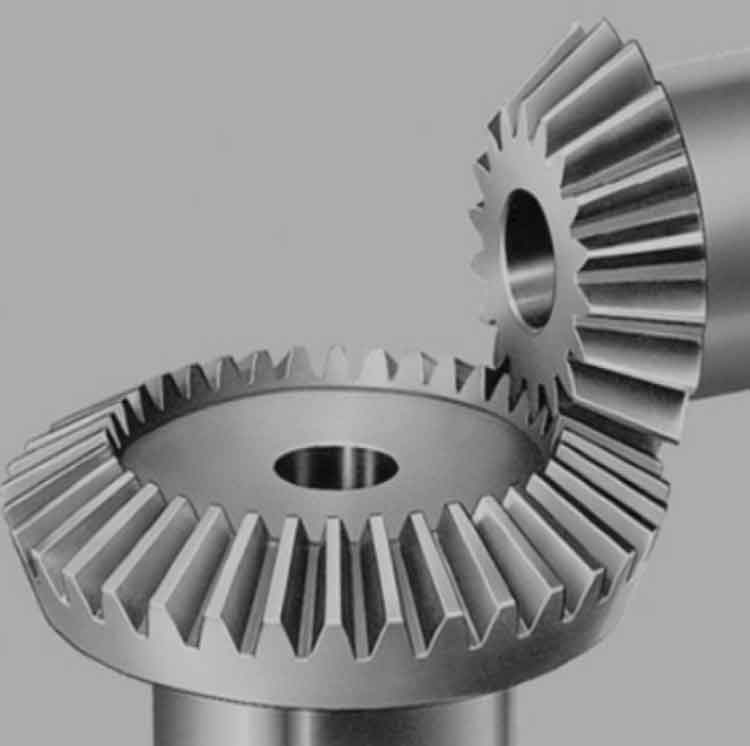
Introduction
Straight bevel gear is widely used in automotive, industrial, and aerospace applications due to their ability to efficiently transmit power between intersecting shafts. However, the meshing of straight bevel gear teeth can generate noise and vibration, which can lead to mechanical problems and discomfort in operation. Understanding the sources of these issues and implementing effective mitigation strategies is essential for enhancing gear performance and longevity.
Causes of Noise and Vibration
Noise and vibration in straight bevel gear can be attributed to several factors, including:
- Gear Design: Inadequate design can lead to poor meshing and increased noise.
- Manufacturing Errors: Imperfections in straight bevel gear teeth, such as surface roughness or misalignment, can cause vibration.
- Material Properties: The material of straight bevel gear can affect their vibration characteristics.
- Lubrication: Insufficient or improper lubrication can lead to increased friction and noise.
- Assembly and Installation: Incorrect assembly or installation can result in misalignment and increased vibration.
Table 1: Causes of Noise and Vibration in Straight Bevel Gear
Cause | Description |
---|---|
Gear Design | Poor tooth profile and geometry |
Manufacturing Errors | Surface roughness, misalignment, and inaccuracies |
Material Properties | Inherent vibration characteristics of the material |
Lubrication | Inadequate or improper lubrication |
Assembly and Installation | Misalignment and incorrect assembly practices |
Methods for Reducing Noise and Vibration
Several strategies can be employed to reduce noise and vibration in straight bevel gear, including optimizing gear design, improving manufacturing precision, selecting appropriate materials, ensuring proper lubrication, and following correct assembly procedures.
Optimizing Gear Design
Design optimization plays a critical role in reducing noise and vibration. Key design considerations include:
- Tooth Profile: Designing an optimal tooth profile can ensure smooth meshing and reduce noise.
- Gear Alignment: Proper alignment of straight bevel gear can minimize vibration.
- Load Distribution: Ensuring even load distribution across straight bevel gear teeth can prevent localized stress and vibration.
List of Design Optimization Techniques
- Designing optimal tooth profiles
- Ensuring proper gear alignment
- Achieving even load distribution
Improving Manufacturing Precision
High manufacturing precision is essential for reducing noise and vibration. Techniques to achieve this include:
- Advanced Machining: Using high-precision machining techniques to create accurate straight bevel gear teeth.
- Surface Finishing: Ensuring a smooth surface finish to reduce friction and noise.
- Quality Control: Implementing rigorous quality control measures to detect and correct manufacturing errors.
Table 2: Manufacturing Precision Techniques
Technique | Description |
---|---|
Advanced Machining | High-precision machining for accurate gear teeth |
Surface Finishing | Smooth surface finish to reduce friction |
Quality Control | Rigorous measures to detect and correct errors |
Selecting Appropriate Materials
The choice of material can significantly affect the noise and vibration characteristics of straight bevel gear. Considerations include:
- Material Damping: Materials with higher damping properties can absorb vibrations better.
- Strength and Hardness: Strong and hard materials can withstand stresses without deforming, reducing noise.
- Compatibility with Lubricants: Materials should be compatible with lubricants to ensure effective lubrication and noise reduction.
List of Material Selection Criteria
- High damping properties
- Adequate strength and hardness
- Compatibility with lubricants
Ensuring Proper Lubrication
Lubrication plays a vital role in reducing friction, noise, and vibration. Effective lubrication strategies include:
- Selecting Suitable Lubricants: Using lubricants that are specifically designed for straight bevel gear applications.
- Regular Maintenance: Ensuring regular lubrication maintenance to prevent degradation.
- Monitoring Lubricant Condition: Regularly checking the condition of lubricants to ensure their effectiveness.
Table 3: Lubrication Strategies
Strategy | Description |
---|---|
Selecting Suitable Lubricants | Using gear-specific lubricants |
Regular Maintenance | Regular lubrication maintenance |
Monitoring Condition | Regularly checking lubricant condition |
Following Correct Assembly Procedures
Correct assembly and installation are crucial for minimizing noise and vibration. Important practices include:
- Proper Alignment: Ensuring that straight bevel gear is properly aligned during installation.
- Torque Specifications: Adhering to recommended torque specifications to prevent misalignment.
- Verification and Testing: Performing verification and testing to ensure correct assembly.
List of Assembly Best Practices
- Ensuring proper gear alignment
- Adhering to torque specifications
- Performing verification and testing
Practical Applications and Case Studies
The implementation of these strategies can significantly reduce noise and vibration in various applications. For instance, in an automotive differential, optimizing straight bevel gear design and improving manufacturing precision resulted in a noticeable reduction in noise levels. Similarly, selecting a material with high damping properties for straight bevel gear used in industrial machinery helped minimize vibration and extend gear life.
Table 4: Case Studies and Results
Application | Strategy Implemented | Result |
---|---|---|
Automotive Differential | Design optimization, precise manufacturing | Reduced noise levels |
Industrial Machinery | High damping material | Minimized vibration, extended life |
Conclusion
Reducing noise and vibration in straight bevel gear is essential for ensuring their optimal performance and longevity. By addressing the root causes and implementing effective strategies such as optimizing gear design, improving manufacturing precision, selecting appropriate materials, ensuring proper lubrication, and following correct assembly procedures, manufacturers can significantly enhance gear performance. Continuous advancements in these areas will further contribute to the reduction of noise and vibration, leading to quieter and more efficient mechanical systems.