30Cr2Ni4MoV is a heavy quenched and tempered steel, which generally has a carbon content of 0 3% to 0 Between 6%, it belongs to medium carbon steel. This type of steel, when used to make components, has excellent comprehensive material properties, excellent strength, and excellent plasticity and toughness. In engineering construction and production manufacturing, the commonly used heat treatment method is quenching and tempering. Quenching and tempering treatment enables the steel to achieve good mechanical comprehensive properties, so this type of steel is commonly referred to as quenched and tempered steel. Quenched and tempered steel is often used in large components and structural components.
Quenched and tempered steel is generally a structural steel that has undergone quenching to form martensite, and has undergone tempering and heat treatment between 500 and 650 ℃. After quenching and tempering heat treatment, the material obtained from steel has good properties, including good strength, plasticity, and toughness, indicating excellent overall performance. In manufacturing, the most widely used quenching and tempering steels are chromium manganese quenching and tempering steels (including 42CrMo and 40CrMn), chromium quenching and tempering steels (including 40CrSi and 40Cr), chromium nickel quenching and tempering steels (including 40CrNiMo and 37CrNi3A) and boron containing quenching and tempering steels.
The characteristic of quenched and tempered steel is that its carbon content is approximately 0 3% to 0 5% range, including one or more alloy metals. The alloying elements of quenched and tempered steel are mainly used to improve the hardenability of the steel and enable the components made of quenched and tempered steel to achieve good mechanical properties after high-temperature tempering. The heat treatment process of quenched and tempered steel involves heating and quenching the material within a certain temperature range beyond the critical point to obtain martensite, and completing tempering within the temperature range of 500 ℃ to 650 ℃. The microstructure obtained after heat treatment is tempered martensite, which has good strength, plasticity, and toughness.
Alloy quenched and tempered steel is widely used in various manufacturing industries, especially in vehicle manufacturing, including automobiles and tractors. In addition, on machines that use equipment such as machine tools and parts, such as bolts, fasteners, gears, connecting rods, bearings, etc. The mechanical properties of quenched and tempered steel can withstand various working load requirements, and the stress effect is relatively complex. Different components have different stress requirements, and their hardenability requirements are also different.
Among quenched and tempered steels, there are various types of carbon steel, including 30 # steel, 35 # steel, 40 # steel, 45 # steel, ML30 # steel, ML35 # steel, ML40 # steel, ML45 # steel. Under room temperature conditions, the mechanical properties of the steel are stable, and it is mostly used for small and medium-sized structural steel parts, gears, fasteners, shafts, etc. The steel types of manganese steel include 40Mn2 steel and 50Mn2 steel. The material characteristics of manganese steel are high temperature tempering brittleness, thermal sensitivity, easy cracking after water quenching, and higher hardenability than carbon steel. Silicon manganese steel generally uses two types of materials, 35SiMn and 42SiMn. This type of steel has obvious tempering brittleness, decarburization, thermal sensitivity, and a very high emphasis on fatigue. More suitable for manufacturing medium speed products with less impact, such as bearings, connecting rods, rotating shafts, etc. In addition, this material can manufacture components such as bolts with temperatures below 400 ℃.
There are several types of boron steel, including 40B, 45B, 50BA, and ML35B. This type of steel has good hardenability and comprehensive mechanical properties, and its comprehensive mechanical properties are superior to carbon steel. Similar to 40Cr, this type of steel is used in the manufacturing of small components and fasteners, such as nuts and bolts. The steel grade of manganese boron steel is 40MnB, and the hardenability of 40MnB material is higher than that of 40Cr material, which has low-temperature impact toughness and temper brittleness. The steel types of manganese vanadium boron steel include 20MnVB steel and 40MnVB steel. Its characteristics are that compared with 40Cr, it has good quenching and tempering characteristics and hardenability, and has a small tendency to overheat. In addition, it has a certain degree of tempering brittleness. The steel grade of manganese tungsten boron steel used for manufacturing and processing important quenched and tempered parts is 40MnWB, which has good impact performance at low temperatures and no tempering brittleness. This steel has properties similar to those of 35CrMo and 40CrNi, and is generally used in the manufacturing of parts not exceeding 65mm. There are various types of silicon manganese molybdenum tungsten steel, including 35SiMn2MoW, which has high hardenability, low tempering brittleness, and extremely low quenching cracking ability; High strength and toughness. Used for rotating shafts, rods, and fasteners with relatively large load-bearing and cross-sectional areas.
The steel grade of silicon manganese molybdenum tungsten vanadium steel is 37SiMn2MoWVA, which has good low-temperature impact toughness and tempering stability, high high-temperature strength, and low tempering brittleness. The most common types of chromium steel are 40Cr and ML40Cr, which have good hardenability. Water quenching is around 30-55 mm, while oil quenching is between 20-40 mm. Their mechanical properties are relatively good, and in addition, they have good low-temperature impact toughness. Commonly used in the manufacturing of gears, shafts, rods, and fasteners. The steel grade of chromium silicon steel is 38CrSi, which has a higher hardenability than 40Cr. Chromium molybdenum steel is generally 30CrMoA, 42CrMo, ML30CrMo, and ML42CrMo, with excellent strength and mechanical properties. This material has good low-temperature impact resistance and no tempering brittleness.
Chromium nickel molybdenum steel is generally 40CrNiMoA, with good comprehensive mechanical properties, high low-temperature impact toughness, low notch sensitivity, and no tempering brittleness. It is commonly used in the manufacturing of large crankshafts, gears, and fasteners. Chromium nickel molybdenum vanadium steel is generally 45CrNiMoVA. The material has good strength and tempering stability, and is commonly used in the manufacturing of heavy-duty vehicle axles.
30Cr2Ni4MoV is one of the commonly used alloy quenched and tempered steels in the mechanical industry. The steel has a moderate carbon content and contains various alloying elements, including Cr, Ni, Mo, V and other alloys. It has good hardenability and high mechanical strength. After quenching, tempering, and tempering, 30Cr2Ni4MoV steel has a microstructure composed of tempered martensite with high hardenability and good comprehensive mechanical properties. It is widely used in the entire manufacturing industry at present, mainly for the production of gears, various shafts, rotors, and other components, especially for manufacturing gear forgings with large cross-sections, high loads, load-bearing and impact loads. The article mainly studies the optimization of chemical elements in 30Cr2Ni4MoV forgings, the influence of forging manufacturing methods and quenching and tempering heat treatment methods on the microstructure and mechanical properties of 30Cr2Ni4MoV gear forgings.
1. Manufacturing process of gear forgings
1.1 Melting of Steel Ingots
The selection of gear forgings for steel ingots is VOD refined 6T ingot type. Due to the fact that the alloy elements of this alloy quenched and tempered steel include various alloy elements such as Cr, Ni, Mo, etc., its elemental composition is relatively complex. Moreover, as a power transmission device, the mechanical properties required for strength and toughness of gear forgings are very important. Therefore, during the smelting of steel ingots, the composition optimization ratio should be carried out, and the chemical element percentage of the steel ingot should be adjusted reasonably. Due to the high required strength, the alloy element content in the material should be increased, and the upper limit of the composition requirements for Cr and V should be selected. The working environment is relatively harsh, and the Ni and Mo element content of the material should be increased to improve its corrosion resistance, By increasing the content of alloying elements, the mechanical properties and usability of the product can be improved. The detailed chemical element composition analysis of VOD refined 6T steel ingots after composition optimization is shown in Table 1. The selected steel ingots are hot opened and forged by a 5000T hydraulic press, with an initial forging temperature controlled within the range of 1185 ℃± 15 ℃. After being opened into billets by a 3000 ton hydraulic press, they are forged. The gear forgings are pre treated with 900 ℃× 6H normalizing after forging.
Element | C | Si | Mn | S | P | Cr | Ni | Mo | V |
Composition requirement | ≤ 0 35 | 0 18-0 35 | 0 20-0 40 | ≤0. 020 | ≤ 0 015 | 1 55-2 05 | 3 25-3 75 | 0 30-0 60 | 0 07~0 16 |
Finished product analysis | 0. 32 | 0. 21 | 0. 38 | 0. 007 | 0. 008 | 2. 01 | 3. 69 | 0. 57 | 0. 14 |
1.2 Forging process of gear forgings
Gear forgings are subjected to relevant hot forming forging on a 3000 ton hydraulic press. Due to the large size of gear forgings, necessary forging process control should be taken during the opening, forming, and forging process. The starting and final forging temperatures of the forgings (starting forging temperature: 1185 ℃, final forging temperature: 800 ℃) and the forging ratio for each heat should be controlled. The steel ingot is heated to 1185 ℃ in an electric heating furnace, with a holding time of 6-7 hours. After appropriate preheating, the steel ingot is subjected to subsequent high-temperature heating before being cast out for forging. The specific heating process is shown in Figure 1.
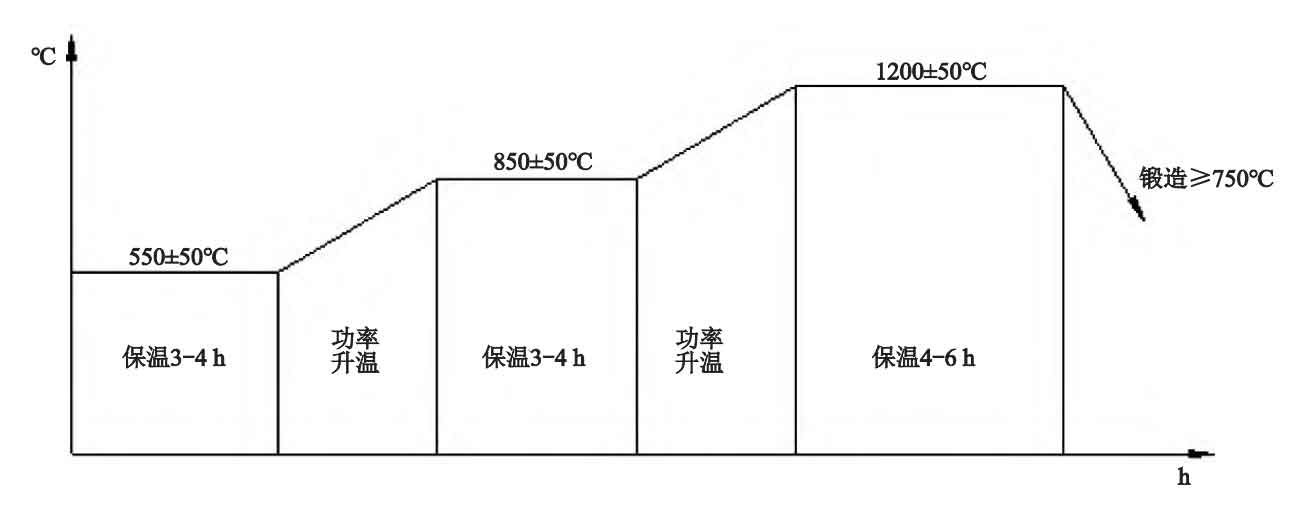
Open the billet on a 3000 ton hydraulic press, with a capacity of 650 square meters x 1520 x 2 pieces. As shown in Figure 2, then proceed with forming and finishing.
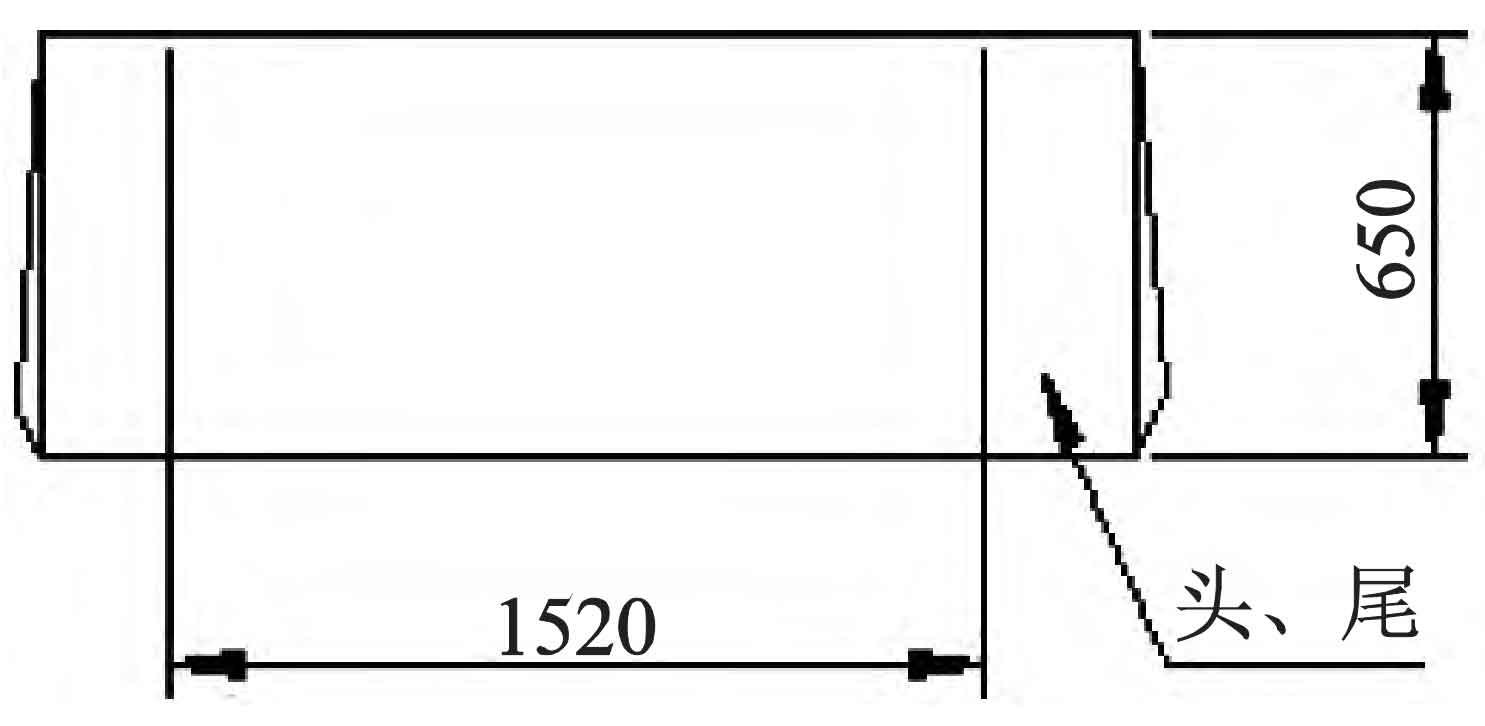
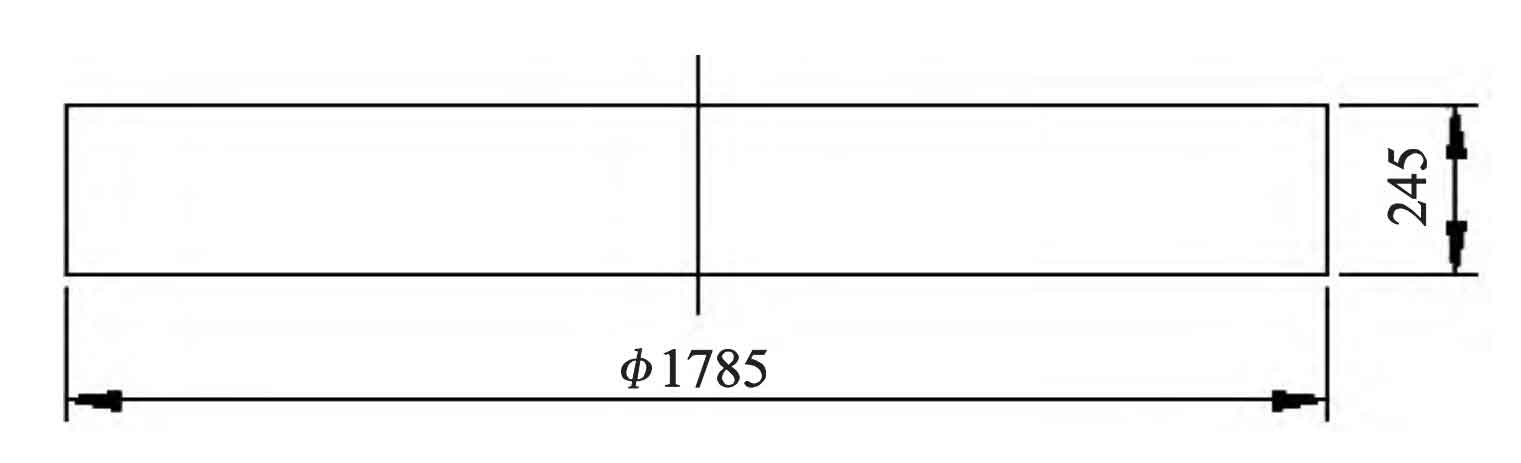
Due to the high alloy content of the steel, it should be subjected to rough machining and then subjected to quenching and tempering heat treatment. After rough turning, the dimensions of the shaft are shown in Figure 4.
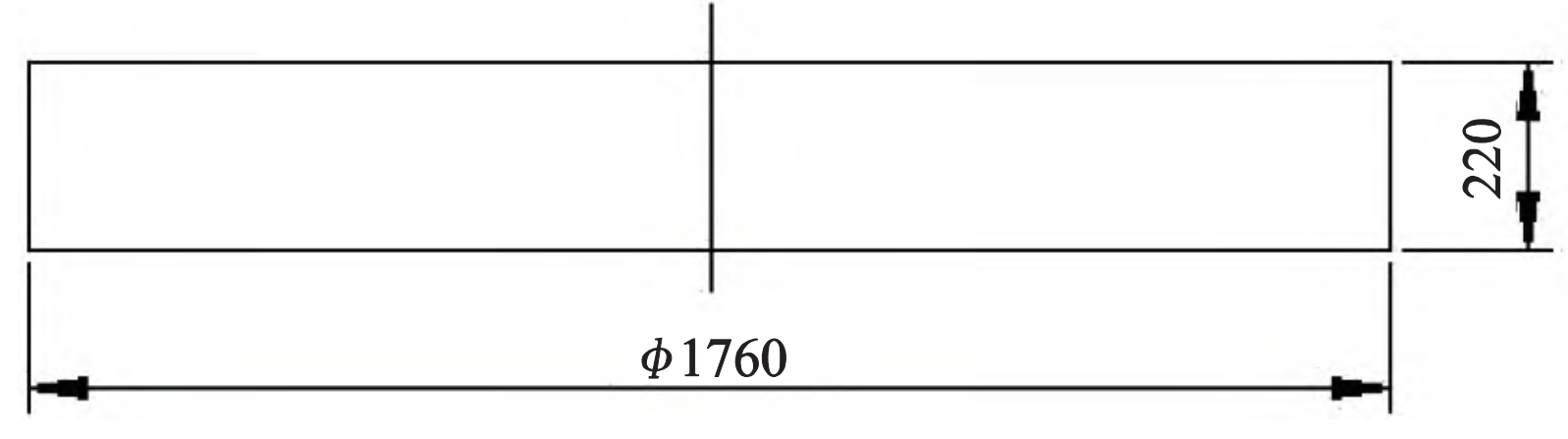
1.3 Quenching and tempering heat treatment of gear forgings
The performance heat treatment of gear forgings adopts the heat treatment process shown in Figure 5.
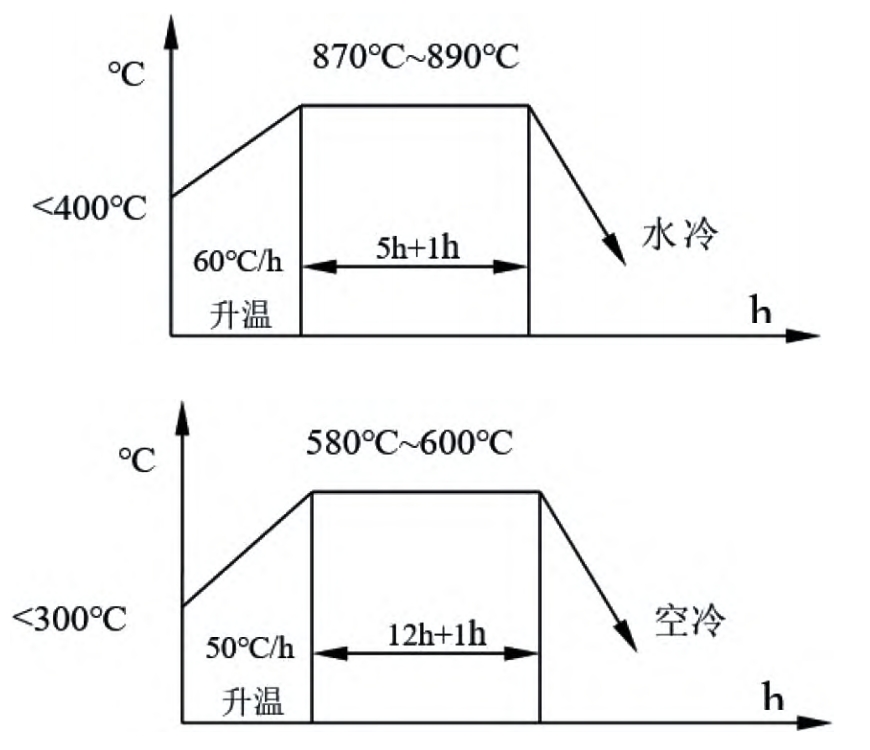
2.Physical and chemical inspection of gear forging products
After performance heat treatment, a test ring is taken from the gear forging at the outer circular end face of the pie gear forging, as shown in Figure 6. The specification of the metallographic specimen is 15 × 15 × 15, the tensile test specimen is a 10mm diameter specimen, the gauge distance is a 50mm standard specimen, and the impact test specimen is a Charpy V-notch specimen. The material structure is observed using a Nikon LV150N microscope. The mechanical properties of the tensile test machine used are WDW-100D and JB-300B, respectively, After the completion of mechanical performance testing and impact toughness testing, analyze the experimental results.
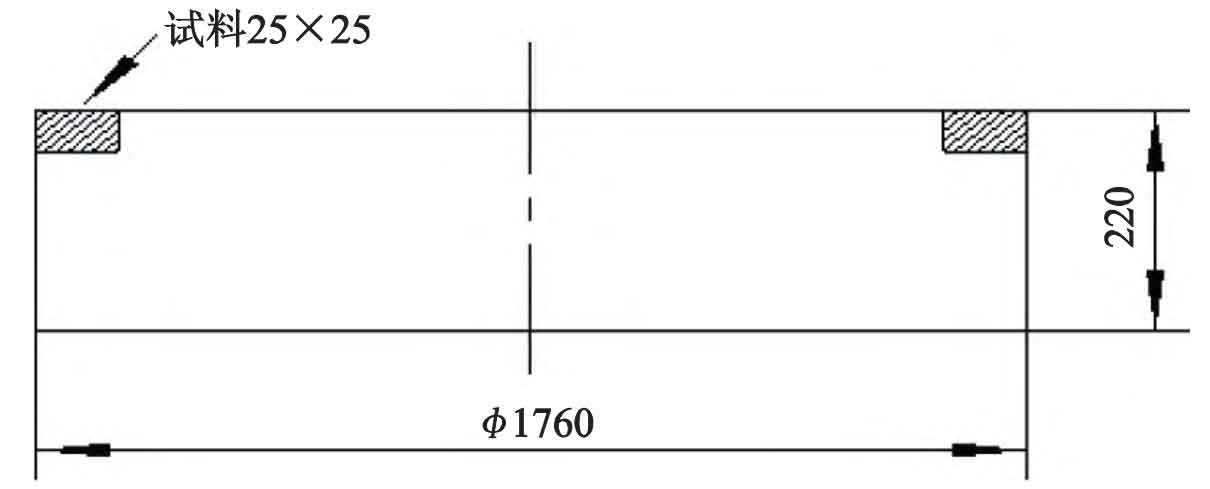
Figure 7 shows the microstructure of gear forgings after quenching and tempering heat treatment. It is easy to see from the microstructure in the photo that the microstructure of gear forgings after heat treatment is tempered martensite, which exhibits high strength and toughness, improving the performance of gear components.
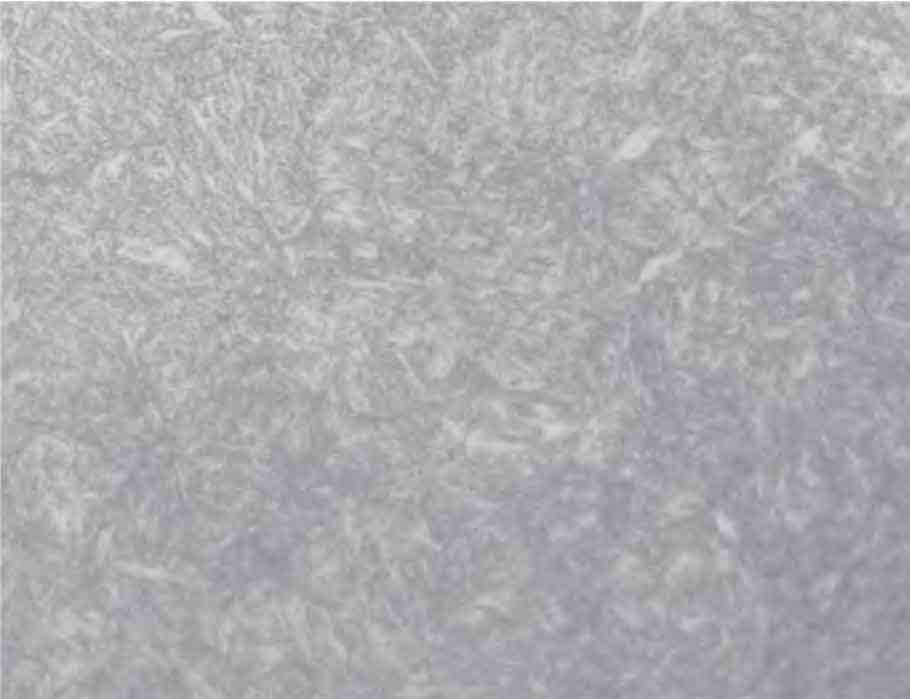
Table 2 shows the performance measurements of gear forgings after quenching and tempering. The results show that after quenching and tempering, the mechanical tensile and impact toughness of gear forgings at room temperature fully meet the technical specifications of the product, and the tensile and impact margins are relatively large. The impact values of the material are relatively uniform, indicating that the mechanical properties of the material matrix are relatively uniform and stable.
Sampling direction | Rm, MPa | Rp0 2, MPa | A,% | Z,% | Akv, J |
Tangential direction | 1020 | 960 | 18 | 63 | 97, 98, 98 |
Horizontal requirement value | ≥940 | ≥870 | ≥13 | ≥34 | ≥60 |
3. Conclusion
The 30Cr2Ni4MoV material has undergone optimization of the composition ratio in the early metallurgical process, control of the gear forging forging process in the forging process, and control of the overall forging ratio and final heat forming process, laying a solid foundation for the excellent quality of the later products. After the gear forging is completed, a reasonable heat treatment system is adopted in the later stage to optimize the mechanical properties and microstructure of the forging. The mechanical properties of the final manufactured gear forging product not only fully meet the technical requirements, but also have a large margin of mechanical strength and plastic toughness impact energy. The mechanical performance test results of the optimized gear forging show that the performance data of the gear forging is high, the toughness is good, and the microstructure is relatively uniform, Furthermore, the comprehensive mechanical performance of gear forgings has been improved, resulting in a certain degree of improvement in product safety and service life. At the same time, it also provides technical data reference for the manufacturing process of this type of material.