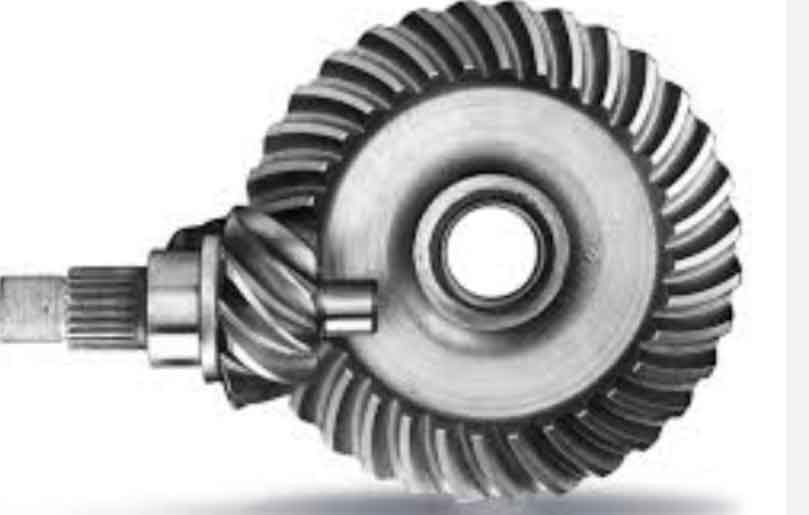
Abstract: Hypoid gear is widely used in various fields due to their excellent transmission characteristics. However, the traditional machining methods have some limitations in achieving ideal meshing performance. This paper focuses on the hypoid gear pair manufactured by the duplex helical method. By establishing mathematical models and using numerical analysis methods, the influence of installation errors and helical motion coefficients on the meshing performance of hypoid gear is studied in detail. The research results provide a theoretical basis and practical guidance for improving the manufacturing quality and meshing performance of hypoid gear.
1. Introduction
1.1 Application and Significance of Hypoid Gear
Hypoid gear is type of bevel gear with unique geometric characteristics and transmission properties. They have a wide range of applications in automotive differentials, helicopter transmissions, and industrial machinery. The main advantages of hypoid gear include high transmission ratio, large contact ratio, strong load-carrying capacity, smooth transmission, and high efficiency. These characteristics make them an ideal choice for power transmission systems that require high performance and reliability.
1.2 Research Status of Hypoid Gear Meshing Performance
In recent years, scholars at home and abroad have conducted extensive research on the meshing performance of hypoid gear. The research mainly focuses on the following aspects: gear tooth contact analysis, the influence of machining parameters on meshing performance, and the improvement of meshing performance through tooth surface modification. However, there are still some problems that need to be further studied, such as the influence of installation errors on meshing performance and the optimization of helical motion coefficients in the duplex helical method.
1.3 Research Objectives and Contents of This Paper
The objective of this paper is to study the meshing performance of hypoid gear manufactured by the duplex helical method. The main research contents include: establishing the mathematical model of the hypoid gear cutting process, analyzing the influence of helical motion coefficients on the tooth surface contact characteristics and geometric morphology, studying the influence of installation errors on the meshing performance of the gear pair, and verifying the correctness of the analysis model through experiments.
2. Mathematical Model of Hypoid Gear with Duplex Helical Method
2.1 Mathematical Model of the Generating Surface of the Pinion with Straight Cutter Profile
The generating surface of the pinion with a straight cutter profile is an important part of the hypoid gear machining process. Tthe cutter profile is mainly composed of two parts: a straight line (part a) and an arc (part b). The straight line is the main working part of the cutter profile, and the arc is used to form the tooth root fillet. The mathematical model of the generating surface can be established by using vector methods, and the position vector and unit normal vector of the generating surface can be expressed in the cutter coordinate system.
2.2 Tooth Surface Equation of the Pinion
The tooth surface of the pinion is formed by the relative movement between the cutter and the workpiece. In the machining process, the cutter rotates around its own axis and moves along the machine tool axis, while the workpiece rotates around its own axis. By using the coordinate transformation method, the tooth surface equation of the pinion can be obtained in the machine tool coordinate system. The tooth surface equation is an important basis for analyzing the meshing performance of the hypoid gear.
2.3 Establishment of the Gear Pair Model
In order to study the meshing performance of the hypoid gear pair, it is necessary to establish a gear pair model. The gear pair model includes the geometric parameters and machining parameters of the gear pair. The geometric parameters mainly include the number of teeth, module, tooth width, offset distance, shaft angle, and spiral angle. The machining parameters mainly include the cutter diameter, cutter tooth profile angle, cutter tip distance, radial cutter position, cutter tilt angle, cutter rotation angle, vertical and horizontal cutter positions, bed position, roll ratio, and center rolling position. By using the gear pair model, the tooth surface contact characteristics and meshing performance of the hypoid gear pair can be analyzed.
3. Analysis of Meshing Performance
3.1 Influence of Helical Motion Coefficient on Tooth Surface Contact Characteristics and Geometric Shape
3.1.1 Tooth Surface Contact Characteristics
The helical motion coefficient is an important parameter in the duplex helical method. By changing the helical motion coefficient, the tooth surface contact characteristics of the hypoid gear can be adjusted. When the helical motion coefficient changes, the position and shape of the tooth surface contact area also change. With the increase of the helical motion coefficient, the contact length along the tooth length direction becomes longer, and the contact trajectory direction angle increases. Conversely, the contact length becomes shorter, and the contact trajectory direction angle decreases.
3.1.2 Geometric Shape of the Tooth Surface
The helical motion also has an impact on the geometric shape of the tooth surface. The helical motion can perform diagonal modification on the tooth surface. For the working surface of the pinion, the modification is from the root of the large end to the top of the small end, while for the non-working surface, the modification is from the top of the large end to the root of the small end. The modification amount at different positions of the tooth surface is also different, which is related to the helical motion coefficient.
3.2 Influence of Helical Motion Coefficient on the Position of the Generating Line
The generating line is the cutting trajectory of the cutter on the tooth surface. The position of the generating line has an important influence on the microscopic morphology of the tooth surface and the meshing performance of hypoid gear pair. When the helical motion coefficient changes, the position of the generating line on the tooth surface also changes. For the working surface, with the increase of the helical motion coefficient, the generating line near the large end moves towards the tooth root direction, and vice versa. For the non-working surface, the situation is opposite.
3.3 Influence of Installation Errors on the Meshing Performance of hypoid Gear Pair
3.3.1 Influence of the Adjustment Amount of the Pinion Mounting Distance
The installation error of the pinion mounting distance will cause the contact area on the tooth surface to shift. Wwhen the pinion mounting distance increases, the contact trajectory of the working surface hypoid gear pair moves towards the small end and the tooth top. When the adjustment amount is large enough, it is easy to produce tooth top edge contact. Conversely, the contact trajectory moves towards the large end and the tooth root. For the non-working surface, the situation is opposite. At the same time, the transmission error of the working surface hypoid gear pair increases with the increase of the pinion mounting distance, while the transmission error of the non-working surface hypoid gear pair decreases.
3.3.2 Influence of the Adjustment Amount of the Pinion Offset Distance
The adjustment amount of the pinion offset distance also has an impact on the meshing performance of hypoid gear pair. When the pinion offset distance increases, the contact trajectory of the working surface gear pair moves towards the small end and the tooth top, and the contact trajectory of the non-working surface gear pair moves towards the large end and the tooth top. At the same time, the transmission error of the working surface gear pair decreases with the increase of the pinion offset distance, while the transmission error of the non-working surface gear pair increases.
3.3.3 Influence of the Adjustment Amount of hypoid Gear Mounting Distance
The adjustment amount of hypoid gear mounting distance affects the meshing performance of hypoid gear pair. When the gear mounting distance increases, the contact trajectory of the working surface gear pair moves towards the large end and the tooth root. Conversely, it moves towards the small end and the tooth top. The transmission error of both the working surface and the non-working surface gear pairs increases with the increase of hypoid gear mounting distance.
3.3.4 Influence of the Shaft Angle Adjustment Amount
The shaft angle adjustment amount has a certain influence on the meshing performance of hypoid gear pair. When the shaft angle changes, the contact length and contact trajectory direction angle of the working surface and the non-working surface change. The maximum transmission error of both the working surface and the non-working surface increases with the increase of the shaft angle.
4. Gear Pair Machining and Rolling Inspection Experiment
4.1 Experimental Equipment and Conditions
In order to verify the correctness of the theoretical analysis, a machining and rolling inspection experiment was carried out on the hypoid gear pair. The experimental equipment used in this experiment includes a CNC spiral bevel gear grinding machine and a rolling inspection machine. The grinding machine is used to machine the hypoid gear pair, and the rolling inspection machine is used to test the meshing performance of hypoid gear pair. The experimental conditions are set as follows: the rotational speed of the rolling inspection machine is 1440 r/min, and the load is 20 Nm.
4.2 Experimental Results and Analysis
The contact patterns on the tooth surfaces of hypoid gear pair obtained from the experiment are basically consistent with the tooth surface contact characteristics calculated by the numerical analysis method. This verifies the correctness of the established gear pair assembly mathematical model and the role of the helical motion in pre-controlling the diagonal contact and changing the contact trace length. The experimental results also show that the duplex helical method can effectively improve the meshing performance of the hypoid gear pair.
5. Conclusion
5.1 Summary of Research Results
- By establishing the tooth surface contact analysis mathematical model, the influence of installation errors such as the pinion mounting distance, pinion offset distance, gear mounting distance, and shaft angle on the tooth surface contact trajectory and maximum transmission error was studied.
- The influence of different helical motion coefficients on the tooth surface contact characteristics was analyzed through tooth surface contact analysis. The influence of different helical motion coefficients on the tooth surface geometric morphology was expounded by establishing the tooth surface mismatch mathematical model, and the different modification principles of the helical motion on the working surface and non-working surface during the machining process were obtained.
- The solution principle of the generating line was expounded by analyzing the geometric position relationship between the cutter and hypoid gear blank. The change rules of the positions of the tooth surface generating lines on the working surface and non-working surface under different helical motion coefficients and different cutter cutting lengths were analyzed and summarized.
- The correctness of the established hypoid gear pair assembly mathematical model was proved by the actual machining and rolling inspection experiment, and it was verified that the introduction of the helical motion can pre-control the diagonal contact of the tooth surface and change the contact trace length, providing a reference for pre-controlling the tooth surface contact characteristics.
5.2 Future Research Directions
Although this paper has achieved certain research results, there are still some problems that need to be further studied. In the future, the following research directions can be considered:
- Optimization of the helical motion coefficient: further study the optimization method of the helical motion coefficient to improve the meshing performance of the hypoid gear pair more effectively.
- Influence of other factors on meshing performance: study the influence of factors such as tooth surface roughness and lubrication conditions on the meshing performance of the hypoid gear pair.
- Application of new machining technologies: explore the application of new machining technologies in the manufacturing process of hypoid gear to improve the manufacturing accuracy and efficiency of hypoid gear.
In summary, this paper has conducted in-depth research on the meshing performance of hypoid gear with the duplex helical method. The research results have certain theoretical and practical significance for improving the manufacturing quality and meshing performance of hypoid gear. In the future, further research is needed to promote the development and application of hypoid gear.