The traditional closed die forging of internal gear is shown in figure (a). In the process of pressing the blank with punch, the side surface of the blank will be subject to the upward friction f τ between the concave die and the side surface of the mandrel. As more materials are filled into the space between the die and the mandrel, the free flow range of the metal becomes smaller and smaller, and the friction f τ becomes larger, that is, the forming force will increase sharply. At the same time, the corner filling of the die becomes more difficult due to the increasing friction. The traditional closed die forging of internal gear is not ideal due to the limitation of its process characteristics and the damage of the die and parts.
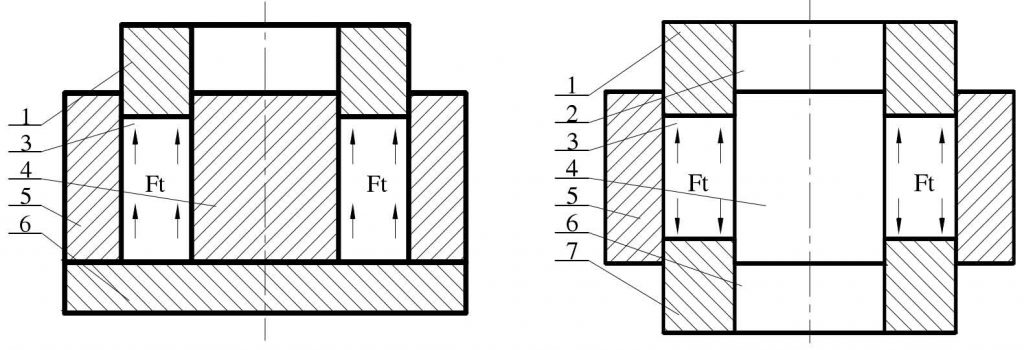
1.(upper) punch; 2. Upper base plate; 3. Blank; 4. Mandrel; 5. Female die; 6. Lower base plate; 7. Lower punch
Different from the traditional forming process, the two-way upsetting extrusion precision forming process device is shown in figure (b). Due to the effect of two-way force, the direction of friction between the die and the mandrel on the side surface of the billet is opposite, which can effectively reduce the friction. Due to the reduction of forming force, it is easier for the die to achieve full state, and the quality of machined parts will be effectively guaranteed.
Based on the above analysis, it can be seen that the difference of forming force and filling fullness of corner between single and double upsetting extrusion is mainly due to the different friction distribution on the side surface during the forming process. According to this phenomenon, it can be judged that the new process design of two-way upsetting extrusion is obviously better than that of one-way upsetting extrusion.