Face gear transmission is an advanced new type of angular transmission that meshes cylindrical gears with bevel gears. It can be applied in situations where the axes of two wheels intersect or are offset. Common face gear tooth shapes include straight teeth, helical teeth, and spiral teeth. Compared with bevel gears that belong to the same category of angular transmission, face gear transmission has unique advantages such as greater overlap, higher load-bearing capacity, more stable transmission, high single-stage transmission ratio, and very compact structure. Face gear transmission is more suitable for application in branch transmission systems, especially for aviation transmission systems with strict volume and quality requirements. In recent years, major equipment such as aerospace has become a strategic demand for various countries. Given the unique advantages of face gear transmission in helicopter branch transmission systems, research on new tooth profiles and tooth surface modification of face gear transmission has attracted much attention. Exploring the new tooth profile of face gear transmission, conducting tooth surface design and tooth surface modification design, is extremely necessary for further exploring and improving the comprehensive performance of face gear transmission. toothDuring the meshing process of the wheel, due to unavoidable manufacturing and installation errors, as well as various forces and deformations, the meshing performance will be reduced, resulting in impact and noise. After research, it was found that using tooth surfaces for gearsAfter modification, the above shortcomings can be effectively improved and the gear life can be increased. This article provides an overview of the research on the traditional tooth profile of face gear transmission, and further summarizes the important achievements made in the research on new tooth profiles and tooth surface modification of face gear transmission both domestically and internationally. On this basis, the future research work on new tooth profile and tooth surface modification of face gear transmission is prospected, providing reference for the next stage of research direction.
1 New tooth profile for 1-sided gear transmission
1.1 Overview of Traditional Tooth Profile of 1-sided Gear Transmission
The traditional tooth profile of face gear transmission mainly includes two types: straight tooth face gear transmission and helical tooth face gear transmission, as shown in Figure 1.
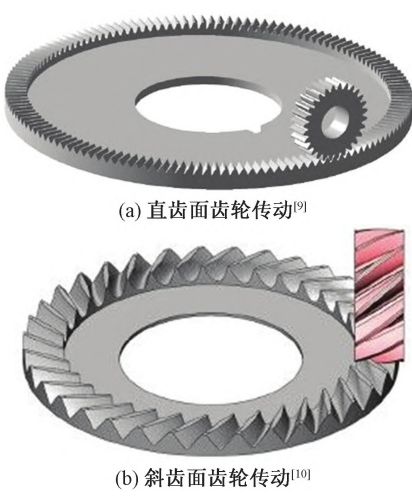
Figure 1 Face gear drive
The research on traditional tooth surface gear transmission has made great contributions to the development of surface gear transmission, involving meshing theory, tooth profile, meshing simulation, contact characteristics, and stress analysis.Firstly, the meshing principle of surface gears was systematically studied, and the conditions for undercutting and tipping of the tooth profile of straight tooth surface gears were obtained by applying the principle of meshing geometry. The minimum inner radius and maximum outer radius of straight tooth surface gears under non-undercutting and non-tipping conditions were derived, and it was pointed out that due to the influence of undercutting and tipping of the tooth profile, the tooth width of surface gears cannot be designed too large.Secondly, point contact surface gears were developed based on the localization theory of contact area.
The small gear with 1-3 teeth meshes with the face gear, which can achieve the localization of the tooth surface contact area, and change the face gear pair from linear contact to point contact, improving the sensitivity of the tooth surface load distribution to the installation error. On the other hand, in order to improve the bending strength of the straight tooth surface gear root, Litin et al. proposed replacing the tooth tip angle with the tooth tip fillet of the gear shaper to process the face gear The transition surface part of the wheel, with a larger curvature radius of the root transition surface, reduces the bending stress of the root of the face gear by up to 12%. In order to further improve the bending strength of the root on the working tooth side, Litvin et al. designed a face gear with asymmetric tooth profile with double pressure angles, taking the pressure angle at the pitch circle on the working tooth side to be greater than that on the non-working tooth side, thereby reducing the bending stress of the root on the working tooth side by 10%. Based on the consideration of improving the smoothness and coincidence of the face gear transmission, Litvin et al. proposed a transmission method using helical cylindrical gears meshing with face gears, and analyzed its meshing performance. Guingand et al. proposed a simple and easy-to-use formula for calculating the tooth width of face gears based on mathematical statistics experimental design methods, and proposed an optimal design method for geometric parameters based on the comparison results of the formula and software. Ram et al. proposed a design strategy for loading face gear optimization, using genetic algorithms to conduct a large amount of work, and obtained the global optimal solution for face gear design. This method has been widely applied in subsequent research. Schippan et al. conducted simulation research on the forming process of face gears, determined suitable process parameters such as radial feed and rotational feed, and contributed to the rapid and stable manufacturing of face gears. Domestic scholars have also conducted research on the traditional tooth profile face gear transmission, and proposed a new design method based on the optimization of the tooth profile.
The research on the meshing theory of face gears has made a lot of progress, and the influence of shaft angle, tooth ratio and tool tooth number on the tooth width of face gears has been discussed. The research results have laid a theoretical foundation for avoiding undercutting and tooth tipping in the design of face gears. Guo Hui et al. have done a lot of research on the processing and numerical simulation of face gears, and proposed a “grid screening method” for finite element models. This method can correct the distortion of the finite element mesh cell shape of face gears, providing a method for domestic finite element analysis of face gears. He Peng et al. have studied the numerical tooth surface of face gears based on processing simulation, and proposed a method to search for points on the tooth surface by numerically calculating the intersection point of the tool surface and a straight line to form a numerical tooth surface. This method has the characteristics of simpler solving process and higher solving accuracy. Peng Xianlong et al. have solved the face gear transmission strength and load-carrying performance parameters using finite element analysis method based on the tooth surface contact analysis, and proved that the influence of the installation error of face gear transmission on the load-carrying performance parameters is related to the direction of the installation error. Lu Rui et al. have established a simulation analysis model of face gears after performing rounding and top cutting optimization design using finite element software, and conducted quasi-static contact analysis. It was found that the tooth tip rounding can reduce the edge contact stress of the face gear system, and the tooth tip cutting can reduce the mass of the face gear system. Zhao Xinhui et al. have demonstrated that the maximum bending stress position of orthogonal face gears is located in the upper half of the tooth surface along the tooth height direction rather than at the root based on the analysis of the inscribed paraboloid theory. Fu Xuezhong et al. have used a small wheel shaping curve to analyze the meshing theory of face gears, and proposed a method to improve the meshing efficiency of face gears by optimizing the tooth profile.
Dong et al. established a lumped parameter model of six degrees of freedom gear vibration, input shaft torsion, gear pair meshing, and bearing support coupling for a face gear torque split transmission system, and studied the inherent characteristics and other properties of dynamic load sharing. The results showed that factors such as torsional stiffness, gear backlash, and time-varying meshing stiffness have a significant impact on dynamic load sharing performance.
In summary, many foreign scholars have done a lot of research on the theoretical research of traditional face gears and have achieved a series of results, which have made great contributions to the development of face gear transmission. After more than 20 years of hard work, China’s research on face gear transmission has also made great progress in the research of traditional face gears. However, there is still a certain gap between China and foreign countries in terms of the generation, design methods, meshing characteristics, and other aspects of traditional tooth profiles.
The research on the new tooth profile and its processing method of face gears is an important way to explore and improve the comprehensive performance of face gear pairs. A series of achievements have been made in the new tooth surface gear transmission meshing theory. The research on the new tooth profile has effectively promoted the prosperity and development of face gear transmission. Japanese scholar Gunaara proposed a face gear with an arc tooth profile on the pinion, and clarified the influence of the arc tooth profile radius on the contact surface structure and tooth surface contact mode. The research found that the meshing performance of this face gear is similar to that of the Wildhaber-Novikov gear (also known as the circular arc gear), and its contact strength is more than twice that of ordinary gears. Fang Zongde et al. proposed a transmission form of the meshing of an arc tooth cylindrical gear and an arc tooth surface gear, as shown in Figure 2. Due to the point contact of the convex and concave meshing tooth surfaces of the large and small gears, and the small curvature difference of the tooth surfaces, the transmission is stable, the noise is small, and the coincidence degree is high. The contact imprint and transmission error can be easily adjusted according to the local conjugate theory. Feng Zhanrong et al. conducted a lot of research on the tooth profile modification of the arc tooth surface gear. The research showed that the tooth profile modification can increase the single tooth thickness of the face gear and improve the transmission strength of the face gear. It provides a theoretical basis for the subsequent research on the arc tooth surface gear. Meng Fanjing proposed a double circular arc tooth profile face gear transmission, as shown in Figure 3. The tooth surface equation of the double circular arc tooth profile face gear was derived, and a three-dimensional solid model of the double circular arc tooth profile face gear was established using the Pro/E software. Illes et al. proposed a new type of geometric worm gear transmission with an arch-shaped tooth profile in the axial section. Using the knowledge of the double parameter vector-scalar function of the conical spiral surface with an arch-shaped tooth profile in the axial section, the tooth surface of the spiral worm gear was determined, and a general modeling process was formulated. It can generate any face gear tooth surface that meshes with the spiral worm gear. The CAD model of the spiral worm gear transmission pair was fabricated using rapid prototyping technology, as shown in Figure 4. Li et al. [37] and Peng et al. [38] proposed a method to generate the gear tooth surface and contact line equations of cylindrical worm cutters and curved tooth surface gears are derived. The contact conditions and transmission characteristics under different contact positions, pressure angles, and tooth number differences are analyzed using ANSYS software. In order to minimize the space and mass occupied by non-circular gear transmission systems, Liu et al. proposed a face gear pair consisting of a cylindrical spur gear and a non-circular face gear for integrated speed reduction and speed change, as shown in Figure 5. This transmission mechanism combines the transmission characteristics of face gears and non-circular face gears, and has the advantages of high transmission efficiency, short transmission chain, low requirement for closed gear pitch curve, and the ability to achieve any continuous variable speed ratio. The research on integrated speed reduction and speed change face gears currently remains at the theoretical stage, which limits the application of integrated speed reduction and speed change face gears. Lin Chao et al. proposed an eccentric end curved face gear transmission that can simultaneously transmit rotation and movement based on the gear meshing principle, as shown in Figure 6.
As shown in Figure 1, the pitch curve, meshing equation, and tooth surface equation of the eccentric end curved surface gear pair are derived, and the variation law of the pressure angle of the eccentric end curved surface gear pair is studied. Based on the secondary development of SolidWorks software, a three-dimensional modeling of the eccentric end curved surface gear pair is realized. The analysis results show that the eccentric end curved surface gear transmission can achieve a larger pressure angle and transmission ratio. Wang Shuang [42] conducted research on the tooth profile modification design of the end curved surface gear, and found that appropriate modification can effectively improve the load-bearing capacity of the gear. This has important theoretical significance for the research of the eccentric end curved surface gear transmission. Peng Xianlong et al. [43] combined the characteristics of face gear transmission and herringbone gear transmission, and proposed a herringbone tooth surface gear transmission without a backlash groove, as shown in Figure 7. The tooth surface mathematical model and geometric contact analysis model of the herringbone tooth surface gear were established. The simulation results show that the meshing performance of the herringbone tooth surface gear transmission is good, and it can meet specific meshing performance requirements. Peng [44] also proposed a developable ruled surface face gear transmission. Compared with traditional tooth profiles, the machining of the developable ruled surface face gear is simpler, but there may be situations where contact and bending stresses are large when the transmission ratio is small. The developable ruled surface face gear can be used instead of traditional face gears when the transmission ratio is large.
In summary, the research on the new tooth profile of face gears focuses on transmission stability, transmission meshing performance, and transmission efficiency. Although most of the research on the new tooth profile is at the theoretical stage and there are few practical engineering applications, the research on the new tooth profile of face gears enriches the application scope of face gear transmission. Studies have shown that the new tooth profile has better transmission meshing performance and wider working adaptability than traditional tooth profiles. Therefore, the research on the new tooth profile of face gears is necessary and has broad prospects.However, there is still a long way to go in the research of the design and processing methods of the new tooth shape.
The contact quality and meshing performance of gear transmission are related to many parameters, among which tooth surface modification is an important means to improve the contact quality and meshing performance of gears. Tooth surface modification refers to a process of slightly modifying the standard tooth surface of gear teeth to make it deviate from the theoretical tooth surface, which can effectively compensate for elastic deformation, installation errors, and manufacturing errors. It is a main measure to reduce gear noise and uneven load distribution in the tooth direction, and has become a key technology for the design and manufacture of high-performance gear transmissions [45-46]. The tooth surface modification methods [47-50] are divided into three categories: tooth profile modification, tooth direction modification, and topology modification.
(1) Tooth profile modification. The theoretical tooth profile of the gear tooth is slightly modified along the tooth height direction. The three main modification methods for tooth profile modification are edge modification, root modification, and root cutting, as shown in Figure 8. Edge modification is the modification of the tooth profile near the tooth tip; root modification is the modification of the tooth profile near the tooth root; and root cutting is the modification of the transition surface of the tooth root. Through tooth profile modification, the impact generated during gear meshing, as well as the noise caused by vibration, can be improved, and the bonding failure of the gear tooth can be alleviated.
(2) Tooth profile modification. Tooth profile modification involves trimming the tooth surface slightly along the tooth length direction, mainly including tooth end thinning, helical angle modification, drum modification, and curved surface modification, as shown in Figure 9. Tooth end thinning refers to gradually thinning the tooth thickness towards the end on one or both ends of the gear tooth over a
small section of the tooth width. Helical angle modification involves slightly changing the size of the helical angle, but due to the small change in angle, it cannot have a significant effect on the tooth profile everywhere. Drum modification involves making the gear tooth protrude outward in the center of the tooth width, usually symmetrically on both sides. Curved surface modification involves modifying the tooth profile according to the actual offset error. The modification effects of tooth end thinning and helical angle modification are relatively poor, while the modification effects of drum modification and curved surface modification are better, but curved surface modification is more computationally cumbersome than other tooth surface modification methods, and has more complex processing techniques during the forming process of the tooth surface. Through tooth profile modification, it is possible to improve the uneven distribution of load in the tooth profile and reduce the occurrence of offset loading.
(3) Topological shaping, also known as bidirectional shaping, refers to simultaneously shaping the tooth profile and tooth direction. Through topological shaping, both the tooth profile and tooth direction can be improved.The topology modification is an effective means to improve the performance of gear transmission, which can improve the lubrication state of the tooth surface, ensure smooth transition of gear meshing, solve the problem of uneven load distribution in the tooth direction, reduce the sensitivity of installation errors, and alleviate the impact, vibration, and noise generated during gear meshing. Therefore, it has attracted more and more attention.
For face gear transmission, although a point contact face gear pair can be obtained by using a small gear and a generating cutter with a different number of teeth, the contact path is perpendicular to the root cone of the face gear, which can easily lead to edge contact or even tooth surface separation. Therefore, Litvin et al. proposed using a rack cutter with a parabolic tooth profile to machine the small gear, achieving a profile modification of the small gear. The analysis results showed that after the profile modification of the small gear, the contact path is no longer perpendicular to the root cone of the face gear, effectively reducing the contact stress on the tooth surface and the possibility of edge contact on the tooth. However, the phenomenon of uneven load distribution on the tooth surface was not resolved. Therefore, Litvin et al. proposed using a butterfly-shaped grinding wheel cutter to modify the tooth profile of the small gear in a directional parabolic way, achieving a topological modification of the tooth surface, obtaining a pre-determined parabolic transmission error and a tilted contact path, solving the problem of uneven load distribution on the tooth surface. However, the long axis of the contact ellipse on the tooth surface was uneven and the bending stress increased. Spanish scholars Zanzie et al. improved the modification method proposed by Litvin et al., proposing to tilt the plane of the tooth profile modification parabola and the plane of the rotating trajectory of the butterfly-shaped grinding wheel by a certain angle during the modification process. This method avoids the uneven long axis of the contact ellipse on the tooth surface. Italian scholars Barone et al. established a finite element three-tooth contact model of face gear transmission containing small gear modification in ANSYS, and analyzed the impact of small gear modification on the contact pattern, load transmission error, load distribution coefficient, tooth surface contact stress, and tooth root bending stress. Japanese scholars Inoue et al. proposed a method for modifying the tooth profile of the small gear by using a high-speed milling machine with a helical cutting tool, achieving a three-dimensional tooth profile modification of the small gear.The use characteristics of the face gear of the fishing reel are analyzed, and a method for optimizing the modified tooth surface of the face gear based on the minimum geometric transmission error is proposed. The results show that the method reduces the sensitivity of installation errors and effectively improves the performance of the fishing reel face gear.
Many scholars in China have also explored the technology of face gear pair tooth surface modification. Wei Bingyang et al. proposed a method of double drum modification of the small wheel, and conducted double drum modification grinding on a forming wheel grinding machine. The results of rolling inspection tests and noise tests proved the feasibility and effectiveness of the double drum modification method. Peng Xianlong et al. proposed an active design method for face gear transmission based on the topological modification of the small wheel, which significantly improved the meshing performance of face gear transmission. Fu Xuezhong et al. conducted extensive research on the topological modification of the small wheel of face gear transmission, mainly focusing on the analysis of tooth contact, meshing performance analysis, multi-objective optimization, anti-adhesion optimization, and vibration reduction optimization of the small wheel after the topological modification of the tooth surface of face gear transmission. They designed the topological modified tooth surface of the small wheel; established the calculation model of the topological modified tooth surface contact analysis and load-bearing contact analysis of the face gear pair; realized the visualization of the tooth surface; calculated the modification parameters for different optimization objectives; and analyzed the impact of the topological modification of the small wheel on the face gear transmission. These studies have contributed to the further research on the tooth surface modification technology of face gear transmission in China.
In summary, in view of the characteristics of face gear transmission, domestic and foreign scholars have proposed A variety of theories and methods for modifying the shape of small wheels suitable for face gear transmission have been developed. The optimization design of modification improves the contact pattern, geometric transmission error, load transmission error, and adhesive load capacity of face gear transmission, and promotes the production and use of face gears. Although the research on tooth surface modification technology in China started relatively late, it has also achieved considerable research results, especially in the study of topological modification, which combines the advantages of tooth profile modification and tooth direction modification, effectively improving the performance of face gear transmission. It will be the focus of future research.
The tooth surface modification technology is proposed for cylindrical gears, but it is also applicable to face gear tooth surface modification. Compared with the modification of small wheels, there are fewer relevant literature on the modification of face gears. Sandro et al. evaluated the influence of misalignment and tooth profile modification in face gear transmission through finite element meshing simulation, and provided the establishment process of the three-dimensional model of the face gear after tooth profile modification. The results of finite element analysis were discussed, and the differences between unmodified, modified, and misaligned were explained. Tetsuo et al. aimed at the minimum transmission error of face gear transmission, modified the tooth profile of the face gear, and then derived the transmission contact trajectory of the face gear after tooth surface modification, and studied its robustness to alignment errors. This method can improve the assembly operation in high-volume production lines. Zhao Ning et al. proposed a method of using a parabolic tooth profile to achieve the tooth profile modification of a straight face gear, and analyzed the meshing characteristics of the face gear after tooth profile modification. For the parabolic tooth profile modified face gear, Dong Jianxiong et al. based on the tooth contact analysis, analyzed the meshing characteristics of the modified face gear, and proposed a method to improve the accuracy of the tooth profile modification.
Guo Hui et al. proposed an active design method for face gear transmission based on the topological modification of the face gear tooth profile. The meshing performance of the modified face gear was significantly improved. Wang et al. proposed a honing method for face gear tooth profile modification based on the principle of honing, and analyzed the influence of various machining errors on the accuracy of the face gear tooth surface. The results of face gear honing and tooth surface measurement showed that this method can produce high-precision face gears and improve the production efficiency of face gears. In order to solve the problem of excessive complexity and low operating efficiency in the process of face gear tooth profile modification, the feasibility and operating efficiency of tooth profile modification and tooth profile modification were compared, and the tooth surface contact analysis of the two modification methods was conducted using Abacus. Wang et al. also proposed a two-directional modification method for hobbing straight-tooth face gears, which modifies the contact trace and contact line of the face gear tooth surface, and then hobbles the face gear after two-directional modification. This modification and processing method can improve the production efficiency and meshing performance of face gears. Mo et al. proposed a design and modeling method for modifying parabolic face gears by introducing a parabola into the rack tooth profile to complete the modification design and processing of the face gear tooth. Peng et al. studied the surface active modification method for face gears, and reduced the vibration of the face gear transmission through modification. This research provides a theoretical basis for the vibration reduction design of face gear pairs.
In summary, although the modification of the face gear is more complex than that of the small wheel, it still has its unique advantages. The modification of the face gear can reduce the difficulty of machining the face gear to a certain extent, reduce production costs and improve production efficiency of the face gear. Its technical research has broad prospects in large-scale production lines.
Through the analysis of the research status quo, it can be seen that although many achievements have been made in the research on the new tooth profile and tooth surface modification of face gear transmission, there are still many areas that can be studied. The new tooth profile of face gear transmission still needs to be further studied, and the design and analysis of face gear tooth surface modification are also key research issues in the future. The future research directions and priorities mainly include the following aspects.
(1) Research on the processing method of new tooth profiles for face gears. Although there are already a variety of new tooth profiles for face gears, most of them have only achieved results in the field of transmission meshing theory. In the future, we should focus on the research of the processing and experimental analysis of new tooth profiles. The experimental results are an important indicator for testing the load-bearing capacity and transmission performance of the new tooth profiles, which can verify the correctness of theoretical analysis. The exploration of new tooth profiles cannot be separated from the combination of theory and practice.
(2) Meshing analysis of modified tooth surfaces. In face gear transmission, the modification process parameters such as tooth surface modification amount and modification length have a significant impact on the bending strength and contact strength of the face gear. Moreover, the face gear generates a high temperature rise during high-speed operation, causing the face gear to experience thermal deformation.
Deformation and even tooth surface bonding significantly reduce the tooth surface contact condition. At the same time, factors affecting the tooth surface contact condition include elastic deformation, dimensional errors, and positional errors of the gear and support systems. Therefore, in the future, it is necessary to consider the comprehensive modification of tooth surface meshing analysis including macro parameters, micro parameters, errors, and working conditions, and further explore which comprehensive parameters can be controlled to effectively optimize the modification design of face gear transmission and improve the quality of modification optimization design.
(3) Analysis of the load-bearing capacity of the modified tooth surface. The load-bearing capacity analysis mainly includes three aspects: contact stress analysis, bending stress analysis, and tooth surface bonding analysis. It is necessary to establish a mechanical analysis model that includes contact stress and bending stress for the modified tooth surface, and then perform stress analysis. The mechanical model and stress analysis results are verified through finite element simulation analysis. For the tooth surface bonding analysis, it is necessary to study the calculation method based on three-dimensional heat conduction analysis.
(4) Shaping optimization design of face gear transmission. Mainly including: improving contact marks, improving geometric transmission errors, improving the load-bearing capacity of tooth surface bonding, etc. Face gear transmission has obvious advantages in helicopter power transmission, and its requirements for low vibration and noise and tooth surface bonding load-bearing capacity are particularly important. The domestic shaping optimization design technology for face gear transmission is not yet mature. In future research, it is necessary to synchronize the research on shaping optimization design in theory and practice. Starting from the application conditions of helicopters, it is necessary to carry out the optimization design of the shaping tooth surface according to different working conditions, so as to meet the more stringent technical specifications in specific applications, and achieve the synchronous development of high-quality, high-speed, high-reliability direction of face gear transmission.
(5) Software development. For the modeling and tooth surface modification design software of face gears, existing 3D modeling software does not have a face gear model library, requiring the operator to import the model. As for the tooth surface modification design software of face gears, there is currently no relevant report, and a 3D modeling and modification design software that can provide accurate geometric conditions of the modified face gear tooth surface is needed. For finite element analysis software, although existing large-scale commercial software can perform finite element analysis on modified face gear transmissions, it requires high-precision finite element models and assembly of modified face gear pairs, and has the disadvantages of long calculation time, low calculation efficiency, different calculation results for different people, cumbersome pre- and post-processing operations, etc., which is not conducive to embedding it in optimization design and other related programs. Therefore, it is difficult to widely promote it in practical engineering applications, and a finite element analysis software that can improve the above shortcomings is needed.
(1) The research on the new tooth profile of face gears provides diverse possibilities for face gear transmission and is an important means to improve and optimize face gear transmission. However, there is still a long way to go in the research on the new tooth profile of face gears, and future research directions will mainly focus on the research of the tooth surface meshing theory and experiments of the new tooth profile, as well as the research of the processing and manufacturing technology of the new tooth profile.
(2) Tooth surface modification is an important means to improve the contact quality and meshing performance of gears. The research on tooth surface modification technology has strongly promoted the development of face gear transmission. The research on tooth surface modification of face gear transmission is still insufficient. In the future, it is necessary to consider the comprehensive parameter modification of tooth surface meshing analysis and load-bearing capacity analysis, as well as the optimization design of modification for helicopter application conditions. The face gear model library and tooth surface modification design software are still blank, which is the focus of future research.
(3) Face gear transmission has many unique advantages, and its application fields will become more extensive with the deepening of research. It is extremely necessary to explore the new tooth profile and tooth surface modification of face gear pairs to further tap into their comprehensive performance.
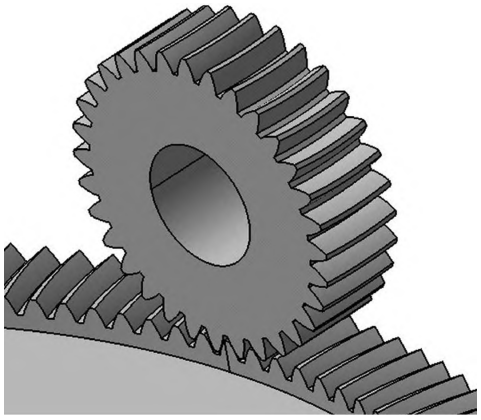
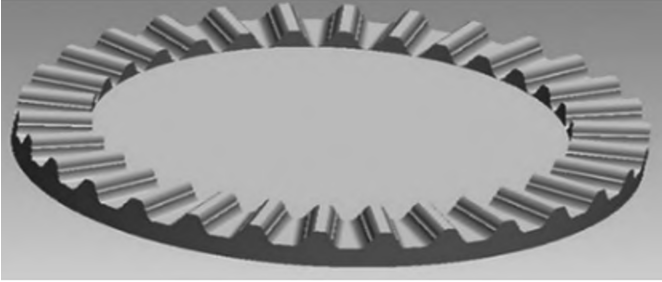
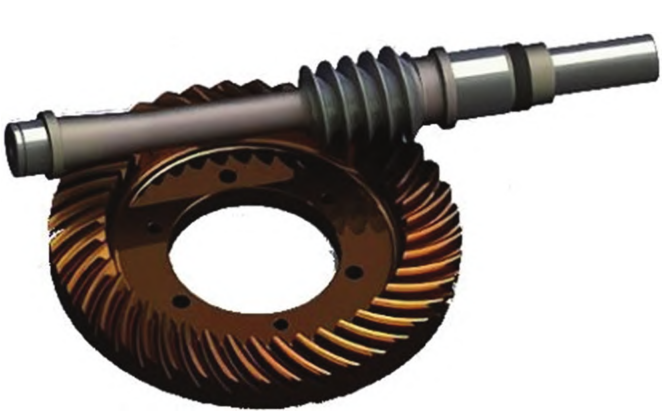
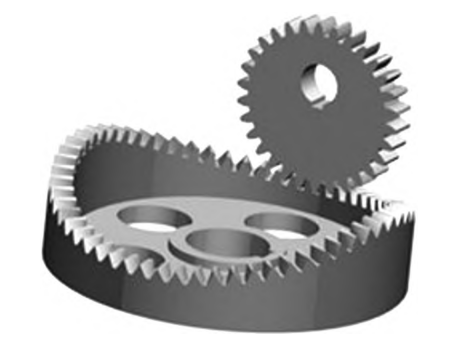

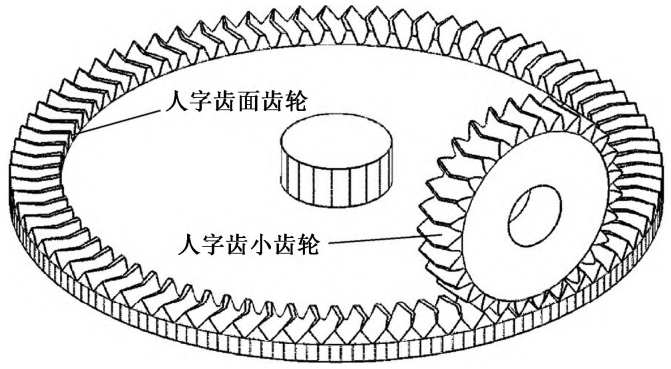
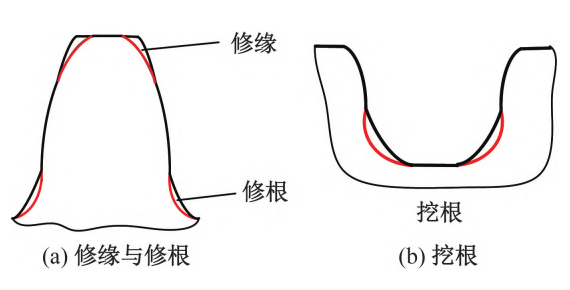
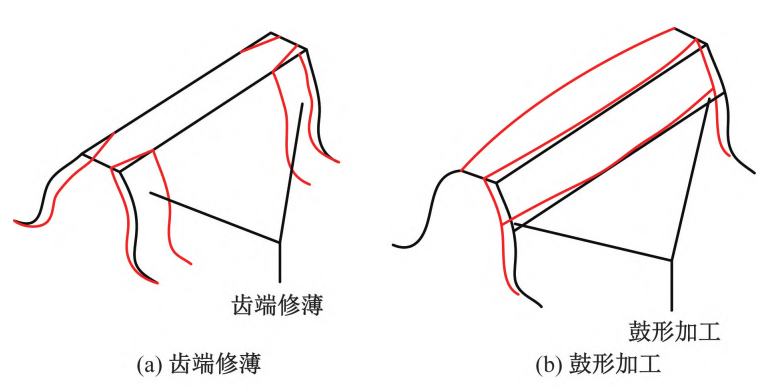