The research on spiral bevel gears and hypoid gears in foreign countries is early, develops rapidly, and is also very advanced in technology. It is in the leading position in the world in terms of manufacturing accuracy, fatigue strength and wear resistance, such as Germany, the United States, Japan and other industrial developed countries.
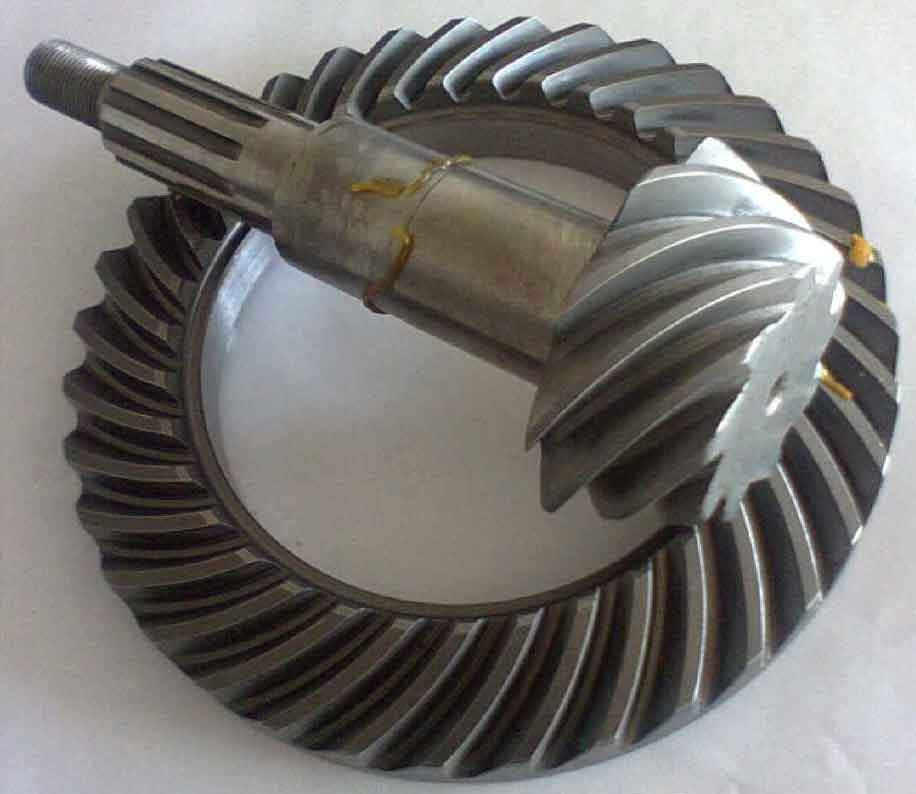
In the 1980s, Dana company and Battelle Research Institute of the United States developed the precision forging technology of spiral bevel gear driven gear, and effectively tried the flangeless die forging process. In the 1990s, Japan forged steel samples of spiral bevel gears with small cone angles. Ravikiran duggirala used numerical simulation to explore the flow law of metal forming in the forging process of driven spiral bevel gear, analyzed the stress and stress distribution of the die in the forging process, and optimized the die.
Compared with other industrial developed countries, the manufacturing of spiral bevel gears in China is still relatively backward, and has not been well promoted and applied in production. Zheng Jianshe successfully completed the precision die forging of spiral bevel gear of Fiat front axle by applying the near net shape technology of precision die forging of spiral bevel gear; Zhang Meng and others conducted experimental research on the plastic forming process of the driving spiral bevel gear of the automobile differential, designed and processed the mold for the test, carried out the plastic forming experiment relying on the universal tensile testing machine, and used the method of grid experimental analysis to study the metal flow on the section and the tooth filling process in the gear forming process, The trend and distribution of the internal metal fibers are revealed, and the stroke pressure curve of the plastic forming spiral bevel gear lead specimen is obtained, which provides a reliable experimental basis for the structural design of the forming die and the calculation of force and energy parameters; Tian Fuxiang et al. Proposed a new closed die forging process and a new die structure of spiral bevel gear without flash, which can complete rough forging and fine pressing with only one heating; Wang Huajun et al. Simulated the precision forging process of driven spiral bevel gear by using three-dimensional rigid plastic finite element method. The metal deformation law in the process was verified by experiments, and the precision forging process and tooth shape deformation law of driven spiral bevel gear were revealed.